Биметаллы и их виды
Биметаллы — это вид композитного материала, состоящий из двух или нескольких разнородных металлов сцепленных между собой.
Они применяются для экономии дорогих цветных и ценных металлов, а также приданию материалам новых свойств. При этом слой более дешевого металла, который воспринимает силовую нагрузку, называют основным, а более дорогого, который обеспечивает специальный свойства, — плакирующим.
В качестве основного слоя используют сталь, а в качестве плакирующего специальные сплавы, цветные и благородные металлы.
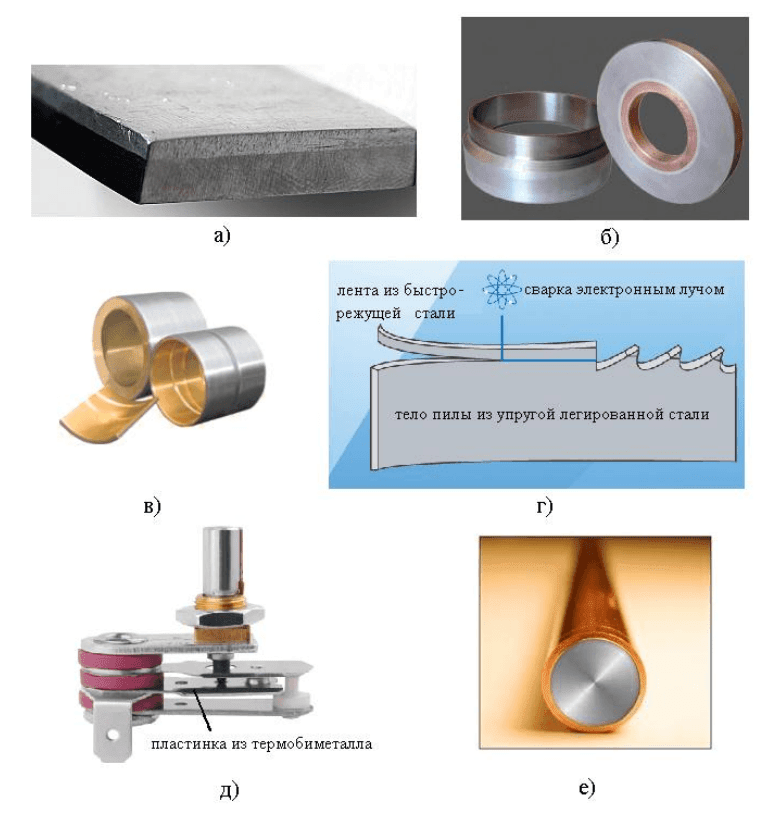
В зависимости от материала плакирующего слоя и назначения различают следующие виды биметаллов:
- Коррозионностойкие. Основной слой коррозионностойкого биметалла состоит из низкоуглеродистой или низколегированной стали, а плакирующий из нержавеющей стали (например 12Х18Н10Т, 08Х13), меди, никеля или их сплавов, алюминия. Такие биметаллы применяются в виде толстых и тонких листов (рис. 97, а) или труб (рис. 97, б) в химической, нефтеперерабатывающей, пищевой промышленности и судостроении.
- Антифрикционные. Антифрикционные биметаллы применяются в подшипниках скольжения (рис. 97, в). В качестве плакирующего слоя такого биметалла используются бронза или алюминий, которые обладают хорошими антифрикционными свойствами, но низкой прочностью, а в качестве основного слоя используется низкоуглеродистая сталь. Такие биметаллы выпускаются в виде лент, которые используются для изготовления вкладышей подшипников.
- Износостойкие и инструментальные биметаллы. Применяются для изготовления режущего инструмента (ножей, пил (рис. 97, г) и т.д.) В качестве основного слоя используется низкоуглеродистая сталь, а в качестве плакирующего слоя используют инструментальные легированные хромом стали (например Х12М, 9Х5Ф и т.д.) или твердые сплавы.
- Термо-биметаллы. Для таких производства таких биметаллов один слой состоит из металла с большим температурным коэффициентом линейного расширения (цветные металлы, сплавы 24НХ, Л90, 75ГДН), а второй слой из пассивных металлов, которые практически не расширяются (инвар — сплав железа и никеля). Полоса, изготовленная из такого материала изгибается под действием температуры из-за разного коэффициента линейного расширения двух металлов. Такие биметаллы используются для термометров, терморегуляторов (рис. 97, д), защитных реле.
- Электропроводные. В таких биметаллах более электропроводный материал располагается на поверхности, а основой является мене электропроводный металл или сталь. В качестве электропроводного слоя в основном используется медь, реже — алюминий. Такие биметаллы используются в линиях электропередач в северных районах (рис. 97, е) и в качестве контактного провода на железной дороге.
Способы получения биметаллов
Среди способов получения биметаллов, распространены следующие:
- одновременная прокатка;
- одновременное прессование или волочение;
- налив расплава одного металла на другой, более тугоплавкий;
- комбинированное литье;
- покрытие гальваническим способом;
- газотермическое напыление;
- наплавка;
- плакирование взрывом.
Рассмотрим основные способы получения биметаллов подробнее.
Комбинированное литье
Способ комбинированного литья (рис. 98) заключается в следующем: в изложницу для слитков закладывают перфорированные разделительные листы, отмечающие положение будущей плоскости соединения между металлами А и Б, затем заливают металлы А и Б одновременно из двух ковшей через две воронки, контролируя равенство высот зеркала жидкого металла в обеих частях изложницы.
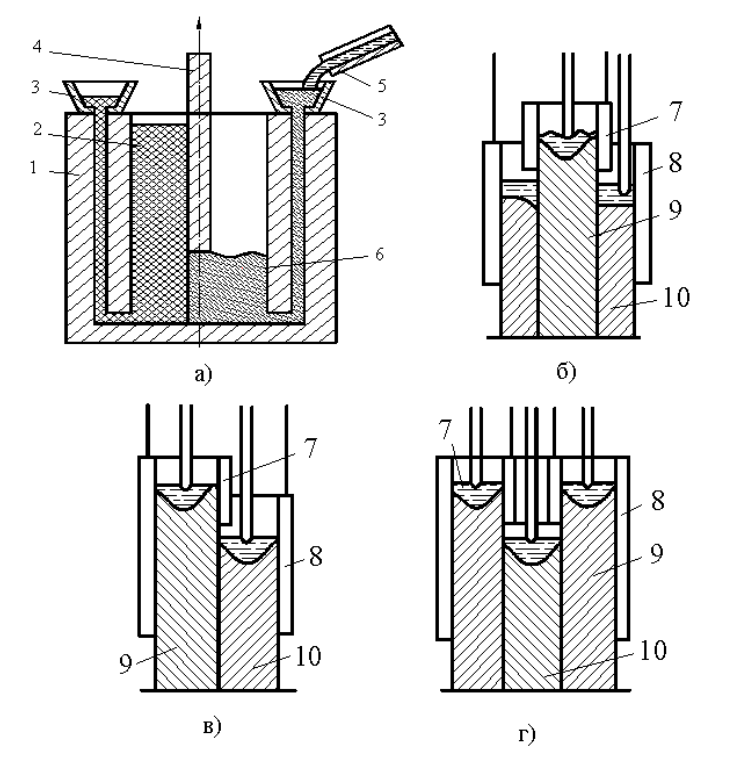
а) — способ последовательной отливки металлов с применением выдвижной перегородки;
б) — способ последовательной отливки металлов с применением схемы расположения кристаллизаторов при отливке трехслойной заготовки.
в) — способ последовательной отливки металлов с применением схемы расположения кристаллизаторов при отливке двухслойной заготовки.
г) — способ последовательной отливки металлов с применением схемы расположения кристаллизаторов при отливке двухслойной цилиндрической заготовки.
Затем биметаллический слиток прокатывают на плакированные листы или фасонные профили. Возможна заливка более двух металлов. Разновидностью способа является заливка одного жидкого металла на слой твердого, который предварительно помещен в изложницу (рис. 99).
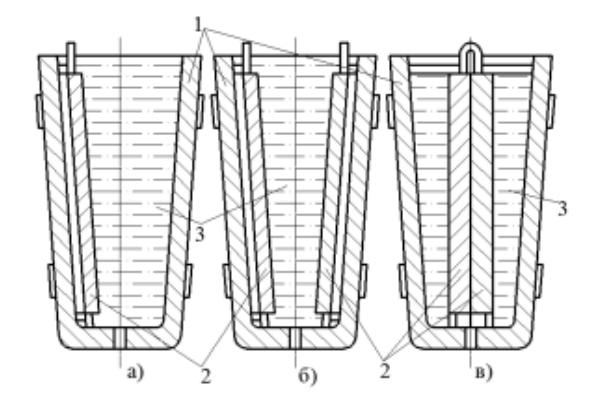
Пакетная прокатка
По способу пакетной прокатки плакированные листы получают путем прокатки собранных и сваренных многослойных пакетов (рис. 100).
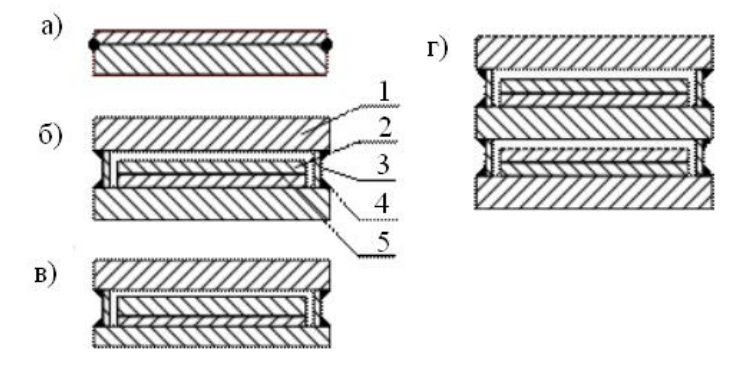
В зависимости от назначения, расположение и количество слоев может быть различным (двух-, трех- и четырехслойные пакеты). Листы могут быть с одно- и двухсторонним плакированием.
Сущность метода пакетной прокатки заключается в том, что основной и плакирующий металл собираются вместе в пакет, который обваривают герметичными швами и заполняют инертным газом.
Затем, пакет перед прокаткой нагревают до температур 1150…1250 °С, при который происходит растворение и восстановление окислов на всех поверхностях герметичного объема.
Последующая прокатка с величиной обжатия не менее 60% приводит к сварке основного металла с плакирующим слоем. Прокатывают такой пакет на обычных толстолистовых
станах.
Холодная сварка прокаткой
Холодную сварку прокаткой (рис. 101) применяют для получения двух- или трехслойных биметаллов, состоящих из стальной основы и плакирующих слоев из цветных металлов, например сталь + медь, сталь + латунь, медь + алюминий, алюминий + титан, алюминий + сталь + алюминий.
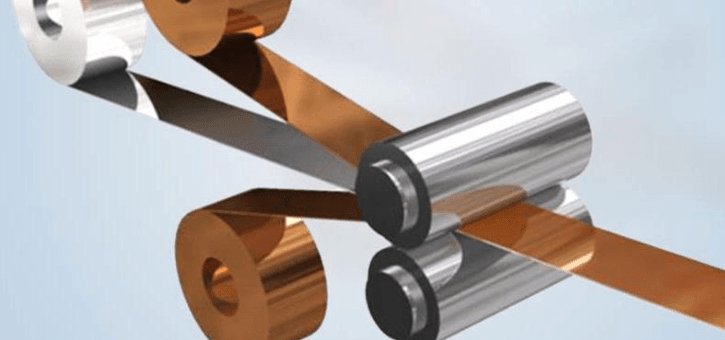
Для получения доброкачественного соединения слоев в биметалле требуется значительная деформация при сварке прокаткой и чистота соединяемых поверхностей, причем особенно важно отсутствие органических веществ.
При сварке прокаткой соединение образуется в условиях принудительного деформирования и малой длительности взаимодействия.
Холодная сварка прокаткой производится по следующей схеме:
- подготовка поверхности прокатываемых заготовок (травление, зачистка и т.д.);
- холодная прокатка на двухвалковом стане с обжатием 45…50% за один проход;
- промежуточный отжиг биметаллического проката в печах при температуре 320…330 ºС в течении 1 часа;
- холодная прокатка, калибровка и правка полос;
- окончательный отжиг биметалла при температуре 450…460 ºС в течении 3 часов.
Плакирование также производят накаткой порошка на полосу, а также путем прокатки порошковой ленты.
Прессование биметаллов
Самый простой способ прессования биметаллов заключается в горячем выдавливании через отверстие матрицы составной заготовки, имеющей круглое или трубное сечение с концентрическим расположением слоёв. Заготовка может быть изготовлена из различных комбинаций сталей, металлов или сплавов.
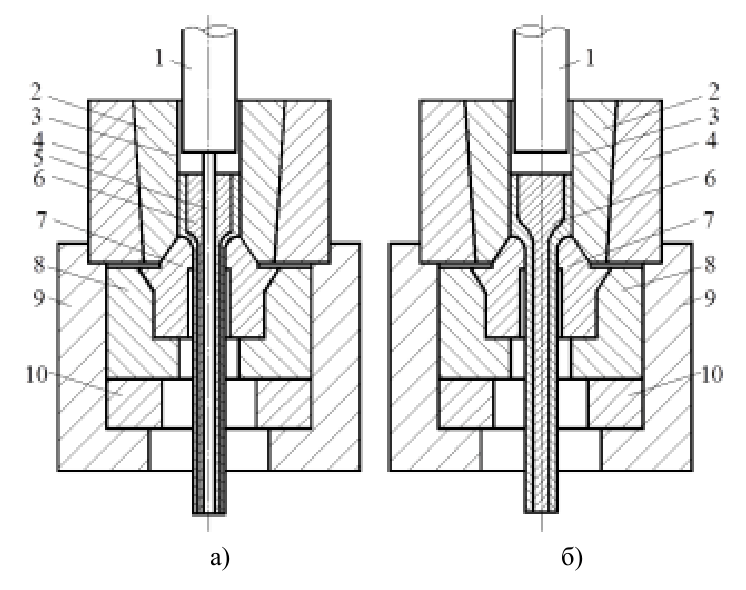
Для осуществления этого процесса можно использовать различные горизонтальные или вертикальные прессы, применяемые для прессования прутков, профилей или труб из цветных металлов и сталей. На рис. 102 приведена принципиальная схема процесса прессования биметаллического прутка и биметаллической трубы.
Волочение
Совместное холодное волочение является методом получения биметаллической проволоки сталь + алюминий или сталь + другие цветные металлы. На стальную проволоку (сердечник) со специально подготовленной поверхностью надевают рубашку в виде трубки, которая может быть бесшовной или в виде сформованной в трубку ленты. Если материал рубашки является высокопластичным, то при совместной пластической деформации в волоке происходит достаточно прочное соединение двух металлов.
Полученная таким образом биметаллическая проволока может быть использована в качестве проводника электрического тока или как коррозионностойкая проволока для различных целей.
Плакирование взрывом
Соединение двух металлов взрывом применяют для таких пар материалов, соединить которые другими способами плакирования трудно (из-за нерастворимости друг в друге, большом различии в сопротивлении деформации и т.д.) или же для изготовления изделий специального (часто военного) назначения. Для этого способа характерно применение основного металла и плакирующего материала в холодном состоянии. Плакирующий лист располагают под небольшим углом к основе, или просто накладывают один на другой. Затем устанавливают бортики и на поверхность плакирующего листа помещают взрывчатое вещество с детонатором (рис. 103).
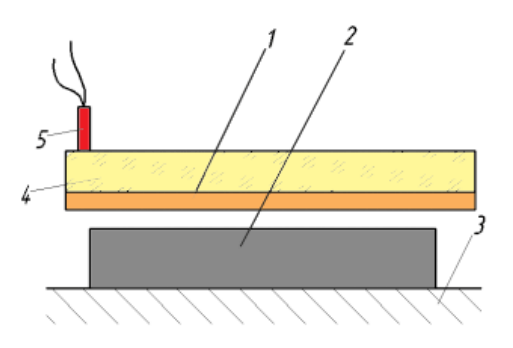
При взрыве, во время соударения пластин возникает струя металла, выходящая с поверхностных слоев основного и плакирующего материала. Вместе с ней удаляется и загрязнение, что способствует образованию очень чистых поверхностей при соединении материалов. Взрывы производят в специально отведенных для этого бункерах. После взрыва производится контроль соединения, обрезка краев и обработка поверхности готового биметалла.
Наплавка
Основные способы дуговой наплавки приведены на (рис. 104). Автоматическая наплавка под флюсом — наиболее распространенный и хорошо изученный процесс, весьма эффективный при изготовлении биметаллических деталей. При дуговой наплавке под флюсом сварочная дуга между электродом и изделием горит под слоем сухого гранулированного флюса, одновременно плавится сварочная проволока, основной металл и флюс.
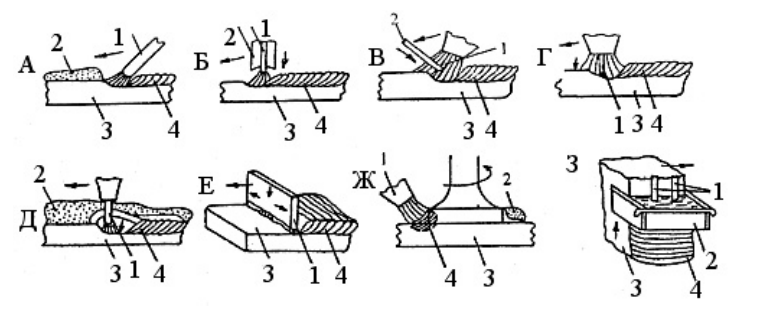
металл; 4 -наплавленный металл; а) графитовым электродом; б) ручной дуговой покрытым электродом с легирующим покрытием; в) неплавящимся вольфрамовым электродом в защитных инертных газах; г) плавящимся электродом в защитных газах; д) автоматическая дуговая плавящейся электродной проволокой под флюсом; е) плавящейся лентой; ж) расплавлением плазменной струей плазмотрона наплавочного материала; з) электрошлаковая наплавка
Металл наплавленного валика, полученного под флюсом, состоит из расплавленного присадочного металла и переплавленного основного. Использование флюса обеспечивает уменьшение разбрызгивания и угара металла. Для уменьшения проплавления основного металла используют многоэлектродную наплавку или ведут процесс с колебанием электрода поперек шва.
Газотермическое напыление
Это процесс получения покрытия из нагретых и ускоренных частиц материала с использованием высокотемпературного газового потока, при соударении которых с основой или напыленным материалом идет их соединение за счет сваривания, адгезии и механического сцепления. По энергетическим признакам методы газотермического нанесения покрытий подразделяются на газопламенный, детонационный, плазменный и электродуговой. Эти методы отличаются типом источника энергии, расходуемой на нагрев и ускорение материала, создающего покрытие.
Источник: Скляр В. О. Инновационные и ресурсосберегающие технологии в металлургии. Учебное пособие. – Донецк.: ДонНТУ, 2014. – 224 с.