Процесс профилирования принципиально отличается от процессов прокатки и гибки в штампах. Основные различия между этими процессами следующие:
1. При прокатке полоса за каждый проход обжимается валками. Толщина, высота и общая площадь поперечного сечения полосы уменьшаются, а длина в результате вытяжки значительно увеличивается. При профилировании толщина исходной заготовки и площадь ее поперечного сечения практически не изменяются. Форма поперечного сечения в процессе профилирования претерпевает постепенные изменения: высота сечения увеличивается, длина исходной заготовки практически не изменяется.
2. При прокатке с изменением размеров поперечного сечения полосы форма его может не изменяться; при профилировании изменение формы поперечного сечения обязательно.
3. Очаг деформации металла при прокатке в основном ограничен валками и незначительно выходит за пределы дуг захвата полосы валками. При профилировании деформация металла начинается перед валками значительно раньше, чем данный участок полосы придет с ними в соприкосновение.
4. При прокатке необходимая форма сечения придается полосе в результате обжатия и вытяжки главным образом горячего металла; при профилировании она получается в результате деформации пластического изгиба металла в холодном состоянии.
5. При гибке в штампах заготовка неподвижна и размер ее ограничен определенной длиной; при профилировании заготовка находится в непрерывном движении и теоретически может иметь бесконечную длину.
6. Рабочий инструмент, применяемый при холодной штамповке (матрицы, пуансоны), перемещается поступательно с одинаковыми линейными скоростями во всех точках; при профилировании он вращается, и поэтому в различных точках линейные скорости инструмента (валков) неодинаковы.
7. При штамповке контакт между рабочими инструментом и заготовкой происходит по всей ее длине; при профилировании площади контакта ограничены небольшими участками соприкосновения полосы с валками.
8. Количество расходуемой энергии, величина возникающих усилий и их направление при штамповке переменны во времени, тогда как при установившемся процессе профилирования они постоянным.
9. Гибка в штампах не сопровождается возникновением в полосе продольных деформаций, которые появляются при профилировании.
В процессе профилирования подгибка элементов заготовки в клетях стана осуществляется вверх и очень редко вниз, поэтому в большинстве случаев диаметры верхних и нижних валков профилегибочных станов неодинаковы. При изгибе и профилировании вверх увеличивается высота профиля, следовательно, верхние валки необходимо изготовлять с глубокими врезами, а диаметры этих валков принимать большими, чем диаметры нижних валков. При изгибе и профилировании вниз глубокие врезы делают в нижних валках, диаметры которых больше верхних.
Однако во всех случаях линейная скорость по основным (катающим) диаметрам валков должна быть одинаковой. Для этого на профилегибочных станах применяют шестеренные клети с определенным передаточным отношением, которое определяется отношением основных диаметров верхнего и нижнего валков. Обычно для всех клетей стана передаточное отношение выбирают одинаковым. Сохранение одинаковых линейных скоростей на верхних и нижних валках осуществляют уменьшением частоты вращения верхних валков в соответствии с увеличением их диаметров из-за использования в шестеренных клетях шестерен различного диаметра. Передаточное отношение зависит от сортамента профилей, для производства которых предназначен данный профилегибочный стан.
Профилегибочные агрегаты различают по характеру работы (непрерывное и поштучное профилирование), по назначению (общее и специальное), по конструкции рабочих клетей, по размерам исходных заготовок и диаметрам рабочих валков.
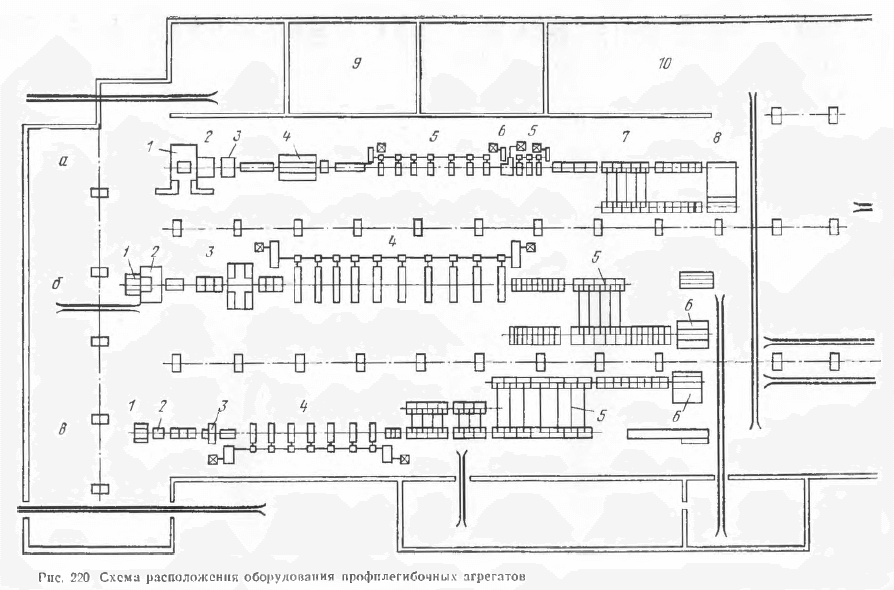
Для агрегатов непрерывного профилирования (рис. 220, а) характерно использование заготовки в виде рулона с порезкой готового профиля после стана. Эти агрегаты оборудованы машинами для стыковой сварки концов рулонов, цетлевыми накопителями и специальными ножницами для порезки готовых профилей.
На агрегатах поштучного профилирования (рис. 220, б, в) рулонную заготовку перед станом предварительно разрезают на летучих ножницах на определенные длины.
Профилегибочные агрегаты специального назначения используют для выпуска какого-либо одного типа гнутых профилей, например профилей для автомобилестроения и других отраслей народного хозяйства. Такие агрегаты оборудованы специальными приспособлениями, механизмами и трансформаторами для одношовной и двухшовной продольной сварки, поперечной сварки, механизмами для перфорации и завивки профилей.
На агрегатах с поштучным процессом профилирования (рис. 220, б, в) полосовую заготовку перед задачей в стан разрезают на мерные длины. Агрегат состоит из разматывателя рулонов 1, правильной машины 2, ножниц для резки заготовок на мерные листы 3, стана 4, участка набора рядов 5 и укладчика пакетов готовых профилей 6.
На агрегатах с непрерывным процессом профилирования (рис. 220, а) порезку профилей производят после профилирования. Такие агрегаты состоят из разматывателя рулонов 1, правильной машины 2, машины для сварки гонцов рулонов 3, петлевого накопителя 4, собственно стана 5, ножниц для резки готовых профилей 6, участка набора рядов 7, укладчика 8. К цеху примыкает вальцетокарная мастерская 9 и участок сборки и хранения валков 10.
Между агрегатами с поштучным и непрерывным процессами профилирования промежуточное место занимают профилегибочные станы с порулонным способом профилирования.
В состав оборудования такого стана входят разматыватель рулонов, правильная машина, собственно стан и механизм для порезки профилей на мерные длины после профилирования.
В зависимости от конструкции станины профилегибочные станы бывают открытого и закрытого типов. Рабочие валки станов открытого типа имеют подшипники с одной стороны, а рабочая часть валков, на которой набирают профильные элементы, является консольной. Такие станы иногда называют консольными. Их преимуществом является простота обслуживания при работе и перевалках. К недостаткам следует отнести малую жесткость валков консольного типа, что не дает возможности изготовлять на них профили из заготовок большой ширины и толщины. Для производства гофрированных и других профилей из заготовок толщиной до 20 мм и шириной до 2000 мм применяются также рабочие клети, имеющие станины закрытого типа. К станам закрытого типа относят станы, рабочие валки которых имеют опоры на обоих концах. Станины закрытого типа более жестки по конструкции. Если на станах открытого типа (со съемными крышками) перевалку производят (после снятия крышки) через верх станины, что на станах закрытого типа перевалку осуществляют через окно станины.
По размерам профилируемых исходных заготовок станы можно разделить на несколько типов (табл. 19).
Тип профилегибочного стана обозначают четырьмя цифрами. Например, стан 1÷4×400÷1500, где первые две цифры характеризуют толщину исходных заготовок, а две вторые — ширину исходных заготовок, мм.
Полная характеристика стана состоит из определения назначения стана, размеров профилируемых на нем заготовок, наибольшей высоты профиля (глубины вреза в валок), типа его конструкции, числа клетей, способа производства гнутых профилей, а также энергетических параметров профилирования (максимального крутящего момента на валках, максимально допустимого усилия деформации, скорости профилирования и установленной мощности).