Производство бандажей и колес для железнодорожного транспорта является комбинированным процессом обработки давлением, включающим ковку и прокатку.
Все принятые в железнодорожном транспорте колеса можно разделить на две группы: составные и цельные. В первом случае бандаж и центр колеса изготавливают отдельно. Колеса этой группы встречаются в виде колес с литым центром и колес с прокатанным стальным центром. Для цельных колес бандаж и центр составляют одно целое Колеса этой группы встречаются в виде цельнолитых и цельнокатаных. Материалом для изготовления цельнокатаных колес и бандажей служит углеродистая сталь химического состава; 0,50 — 0,80 % C; 0,60 — 0,90% Mn, 0,15 — 0,35 % Si и P. Наибольшее распространение в настоящее время получают цельнокатаные колеса.
Составные колеса имеют следующие недостатки: ненадежность работы бандажа в эксплуатации; сложность изготовления составного колеса, связанная с необходимостью обработки центра, обработки внутренней стороны бандажа и насадки бандажа на центр, что требует большого числа станков и значительно удорожает стоимость колес; несколько больший расход металла из-за необходимости делать припуск на обработку тех частей колеса, которые в цельнокатаных колесах не обрабатываются. Кроме того, установки для производства составных колес дают значительно меньшую производительность, чем современные установки для производства цельнокатаных колес.
Последовательность изготовления цельнокатаных колес следующая: резка слитков на заготовки; нагрев заготовки; обжим и прошивка заготовки на прессе; формовка колесной заготовки на прессе; прокатка на стане; выгибка и калибровка колес на прессе; термическая обработка колес.,
Исходным материалом служат так называемые комплектные слитки или прокатанная заготовка круглого или многогранного сечения, масса которых выбрана таким образом, чтобы из одного слитка можно было изготовить несколько колес.
Сначала слиток 1 на специальных отрезных многосупортных токарных станках разрезается несколькими резцами сразу (рис. 212) на части 2 соответственно массе прокатываемых колес. Полученную заготовку (рис. 213, а) нагревают и подвергают предварительной обработке на прессах или иногда на молотах. Эта обработка заключается в осаживании заготовки на прессе на торец, затем в прошивке отверстия (рис. 213,6) и в штамповке чернового колеса (рис. 213,в), которое поступает для дальнейшей обработки обода в специальный колесопрокатный стан.
На рис. 214 показан колесопрокатный стан, имеющий три вертикальных валка, из которых валок 1 является коренным, валки 2 и 3 — нажимными роликами. Эти три валка служат для обработки рабочей поверхности колеса. Для обработки внутренних и торцовых поверхностей обода имеются два наклонно расположенных валка 4 и 5. Валки 6 и 7 являются направляющими роликами. Валки 1, 4 и 5 приводные, а остальные холостые.
Ввиду того, что при прокатке диаметр колеса увеличивается, стационарно установлен лишь один валок 1, а остальные имеют возможность перемещаться. На рис. 214, а, б, в показано положение валков стана в начале и конце прокатки.
В прокатном стане колеса получают с прямым диском (см. рис. 213,г). Чтобы иметь коническую стенку (в целях большей устойчивости колеса), после прокатки колесо поступает на пресс, где производят небольшое выдавливание втулки и колесо приобретает форму, изображенную на рис. 213, д. Затем колеса поступают на холодильник, где охлаждаются до 500 — 600 °С и стопками подаются краном в колодцевые печи, в которых с целью предупреждения образования флокенов выдерживаются 4 — 5 ч при 550 °С. Далее колеса нагревают в закалочной печи до 830 — 860 ° и направляют на вращающиеся столы, где рабочие поверхности колес обрызгивают водой из специальных сопел. После закалки колеса подвергают отпуску при 400 °, охлаждению, наружному осмотру и испытанию на твердость. Затем следуют операции механической обработки колес.
При производстве бандажей в старых бандажепрокатных цехах исходным материалом обычно служат слитки развеса, соответствующего только одному бандажу. Современные бандажепрокатные цехи работают на заготовке, вырезанной комплектами из круглого или многогранного слитка (рис. 215,а).
Последовательность операций изготовления бандажей следующая:
- резка слитков на заготовку (при комплектных слитках);
- нагрев заготовки или слитков (одиночных);
- предварительная ковка или прессовка;
- ковка на роговом молоте или прессовка для получения необходимой разводки;
- нагрев разводок;
- прокатка бандажа;
- растяжение на прессе;
- клеймение на специальном прессе;
- термическая обработка.
В результате третьей и четвертой операций часть слитка (рис. 215,а) отковывают в черновое кольцо (рис. 215,б), называемое разводкой.
Операция 3 состоит в осаживании заготовки на торец до толщины, немного превышающей ширину бандажа, а операция 4 — в последующей прошивке отверстия. Операция 6 состоит в прокатке разводки в готовый бандаж (рис. 215,в). На современных установках осаживание и прошивка отверстия бандажа происходят на том же прессе и без дополнительного нагрева. Разводку сразу передают на бандажепрокатный стан (рис. 216).
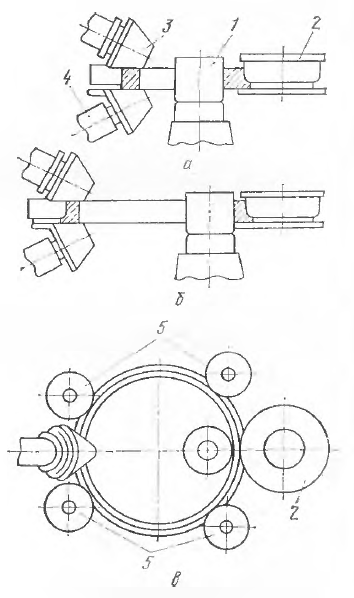
Стан состоит из двух вертикальных валков 1 и 2, двух наклонных 3 и 4 и четырех направляющих роликов 5. Для обработки рабочей и внутренней поверхностей бандажа служат валки 1 и 2, а для торцовых поверхностей — валки 3 и 4. Валки 2-4 — приводные, а валок 1 — холостой.
Подшипники валка 1 опираются на плунжер гидравлического цилиндра, при помощи которого достигается уменьшение расстояния между валками 1 и 2 по мере прокатки бандажа. Валки 3 и 4 установлены на специальной каретке, которая по мере увеличения диаметра прокатываемого бандажа перемещается в горизонтальном положении вместе с валками 3 и 4. На рис. 216, а — в можно видеть положение валков стана в начале и в конце прокатки бандажа.
По выходе из прокатного стана бандажи подвергают растяжке на прессе, которая делает их правильно круглыми и растягивает до нужного размера. Схема действия этого пресса показана на рис. 217. Вслед за растяжкой происходит маркировка бандажей специальным маркировочным прессом.
После этих операций бандажи термически обрабатываются закалкой с последующим отпуском. Далее их подвергают осмотру, испытанию на твердость и сортировке, после чего они поступают на склад.