Торкретирование — метод горячего ремонта футеровки конвертера, заключающийся в нанесении при помощи специальных торкрет-машин огнеупорной массы на внутренние, изношенные участки футеровки. Известны и находят применение мокрое, полусухое и факельное торкретирование. При первых двух способах увлажненную огнеупорную массу наносят на футеровку конвертера при помощи сопла-распылителя торкрет-машины струей сжатого воздуха. Увлажненная масса прилипает к футеровке, а в последующем приваривается к ней. При полусухом торкретировании смешение огнеупорной массы с водой происходит в сопле; при мокром (пульповом) торкретировании огнеупорную массу предварительно смешивают с водой и подают в сопло сжатым воздухом в виде пульпы. В качестве огнеупорной массы при полусухом и мокром торкретировании применяют периклазовые, доломитовые, хромитовые порошки и их различные смеси с добавкой связующих — жидкого стекла, силикатной глыбы, фосфатов, солей магния, шлаков, смол и др. Количество связующих в массе составляет 1 —15%.
Полусухой способ торкретирования чаще применяют при ремонте локальных разгаров футеровки, мокрый — при планово-предупредительных ремонтах. Достоинствами мокрого и полусухого торкретирования являются их простота и относительно невысокая стоимость. Однако из-за наличия влаги структура нанесенного слоя получается сравнительно рыхлой, в связи с чем стойкость торкрет-покрытия невысока. Кроме того, длительность операции торкретирования значительно больше, чем при факельном торкретировании, происходит охлаждение футеровки и зачастую требуется последующий подогрев нанесенного слоя. Эти способы наиболее приемлемы для цехов, имеющих резервы мощности (работающие с простоями конвертеров). При напряженном жеритме работы конвертеров такое торкретирование приведет к снижению производительности цеха, увеличению расходов по переделу и капитальных затрат.
По этим же причинам на отечественных заводах применяют почти исключительно факельное торкретирование; полусухое и мокрое используют на зарубежных заводах.
Факельное торкретирование заключается в том, что при помощи водоохлаждаемой фурмы в полость конвертера вводят кислород и торкрет-массу, содержащую топливо (коксовую пыль). Масса и кислород смешиваются на выходе из сопла фурмы; сгорание кокса в кислороде обеспечивает формирование факела с температурой 1800—2000 °С. При этой температуре огнеупорный порошок оплавляется (переходит в пластическое состояние) и наносимый факелом на поверхность футеровки прочно сваривается с ней. При этом не требуется обжиг нанесенного покрытия. Торкрет-массы состоят из топливной (20—30% коксовой и реже угольной пыли) и огнеупорной составляющих (периклазовые и доломитовые порошки); стоимость таких масс высока. Начинают внедряться значительно более дешевые массы на основе извести, в которые вводят до 10% легкоплавких спекающих добавок(сталеплавильные и доменные шлаки и др.).
Факельное торкретирование используют как для локального ремонта участков повышенного износа, так и всей поверхности футеровки. Находят применение вертикальный (рисунок 1) и горизонтальные (рисунок 2) способы торкретирования. Комплекс оборудования для факельного торкретирования включает (рисунок 2 и 3) размещаемые у цеха приемные камерные питатели (или бункера с пневмовинтовым или пневмокамерным насосом), в которые торкрет-массу доставляют автоцементовозами; рабочий камерный питатель (бункер с пневмонасосом) у конвертера; торкрет-установку; систему пневмотрубойроводов. Горизонтальное торкретирование осуществляют при помощи перемещающихся по рабочей площадке конвертерного цеха рельсовых или на гусеничном ходу машин, снабженных механизмом вращения фурмы и ее перемещения в вертикальной и горизонтальной плоскостях, что позволяет направить факел на любой участок футеровки конвертера.
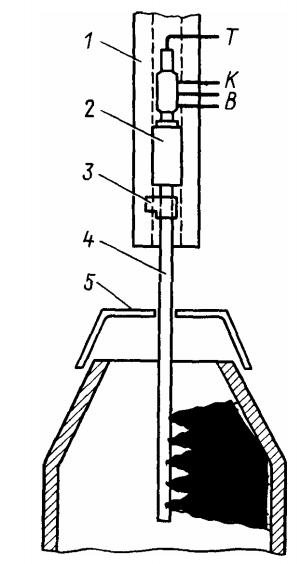
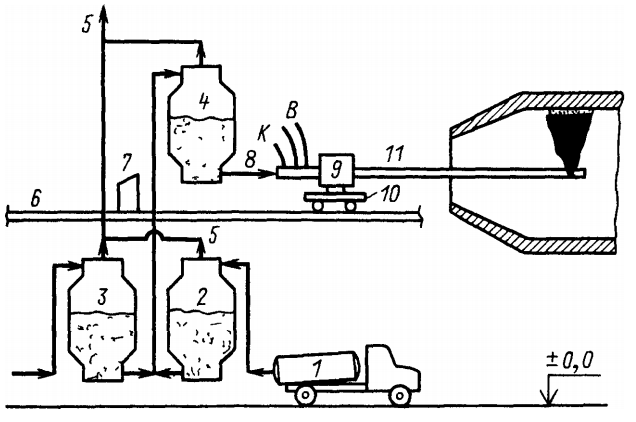
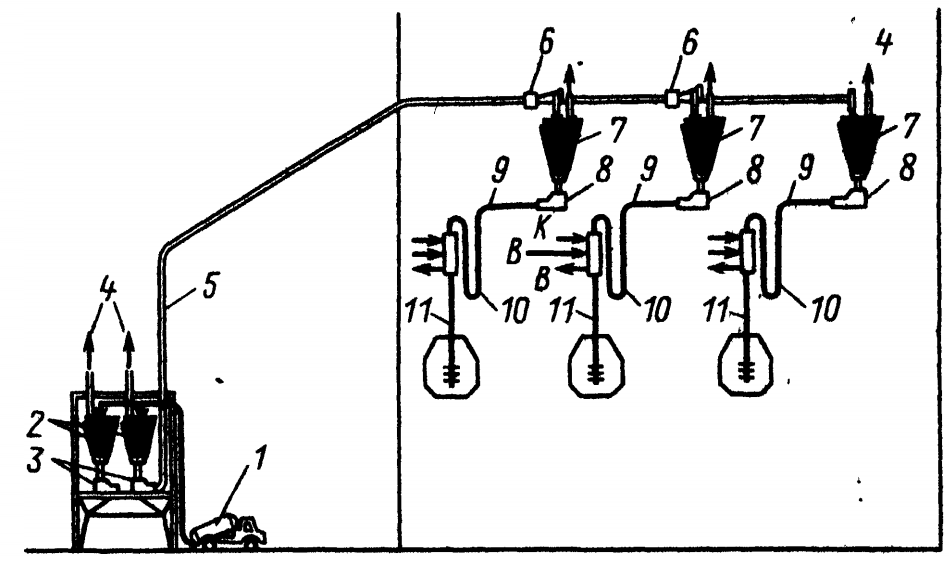
При вертикальном торкретировании применяют снабженные индивидуальным механизмом вращения торкрет-фурмы, взаимозаменяемые с продувочными кислородными фурмами. Перед торкретированием торкрет-фурму устанавливают в каретке машины для подачи кислорода (МПК) вместо одной из продувочных фурм. Каретка обеспечивает перемещение торкрет-фурмы в вертикальном направлении в процессе торкретирования. Для вновь сооружаемых цехов разработаны трехпозиционные МПК, позволяющие разместить две продувочные фурмы и одну вращающуюся торкрет-фурму.
Торкрет-фурма (рисунок 4) включает ствол с головкой и коллектор, служащий для подвода кислорода, воды и торкрет-массы; коллектор остается неподвижным привращении ствола с головкой. Фурму выполняют из четырех концентрически расположенных труб; внутренняя служит для подачи торкрет-порошка, следующая — для подачи кислорода, а две наружные — для подвода и отвода охлаждающей воды. Фурмы могут быть одно- и многосопловыми. У последних сопла в головке располагают в ряд вдоль оси фурмы, это создает плоский факел, охватывающий большой участок футеровки, что повышает производительность торкрет-машины. В последнее время применяют (рисунок 5) сопла типа «труба в трубе».
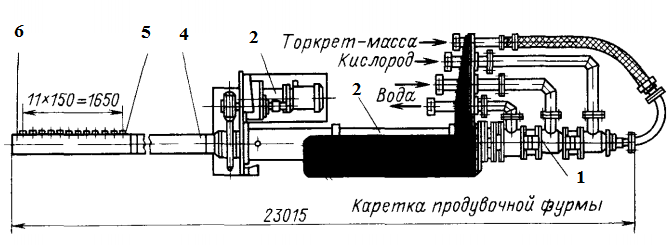
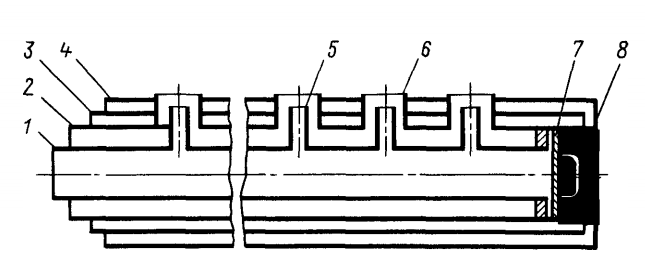
Торкрет-фурма (см. рис. 4), предназначенная для установки на МПК большегрузных (250—350 т) конвертеров, имеет следующие основные характеристики: подача торкрет-массы 200—700 кг/мин, расход кислорода 125—300 м3/ мин, расход сжатого воздуха 60 м3/мин, частота вращения торкрет-фурмы 0,78—1,56 мин-1.
Опыт выявил ряд существенных недостатков горизонтального способа торкретирования: выделение в цех из горловины конвертера горячих газов и пыли; неодинаковое торкретирование футеровки (верх горизонтально расположенного конвертера торкретируется хуже, чем боковые стенки; не торкретируется нижняя зона вследствие натекания шлака); торкрет-машины загромождают рабочую площадку цеха; сложность подвода к торкрет-машине гибких рукавов.
Способ вертикального торкретирования исключает эти недостатки. Он позволяет одинаково торкретировать всю поверхность футеровки конвертера (исключая днище); отводить через систему газоочистки все выделяющиеся запыленные высокотемпературные газы; упростить подвод кислорода и охлаждающей воды к торкрет-фурме, благодаря использованию трубопроводов, предназначенных для кислородной фурмы; высвобождаются операторы-торкретировщики, поскольку торкретированиемуправляет машинист центрального поста управления.
При оценке экономичности и целесообразности торкретирования учитывают следующие факторы:
- Уменьшение расхода формованных огнеупоров и дополнительный расход торкретмассы; возможная экономия зависит как от расхода, так и от стоимости этих материалов; снижение стоимости торкретирования обеспечивает применение недорогих торкрет-масс на основе извести.
- Дополнительные расходы, связанные с капитальными вложениями на оборудование для торкретирования и с его эксплуатацией.
- Снижение объема производства, вызванное простоями конвертера при торкретировании (1,5—2,0%); так, при проведении торкретирования длительностью 6 мин через пять плавок, продолжительность одной плавки возрастает на 1 мин, что снижает производительность примерно на 2%.
- Увеличение объема производства в связи с тем, что в результате повышения стойкости футеровки уменьшаются простои конвертера на холодных ремонтах.
- Снижение затрат на проведение холодных ремонтов.
- Улучшение условий труда, поскольку уменьшаются затраты тяжелого ручного труда на холодных ремонтах.
При одном-двух установленных в цехе и постоянно работающих конвертерах торкретирование наряду с другими преимуществами может обеспечить рост выплавки стали, если снижение простоев на холодных ремонтах больше дополнительных простоев конвертера при торкретировании. При трех установленных в цехе конвертерах, два из которых работают, а один находится в резерве, торкретирование вызывает снижение производительности на ~1,5% и может применяться для снижения расхода огнеупоров, уменьшения затрат труда на холодные ремонты и улучшения условий труда.
Основные показатели процесса торкретирования. Обычно этот процесс начинают с половины достигнутой без торкретирования стойкости футеровки. Длительность торкретирования составляет 4—20 мин; периодичность— через 2—18 плавок. Толщина наносимого торкрет-покрытия составляет от 5 до 100 мм; его наносят за одну операцию, либо за несколько последовательных операций (несколькими тонкими слоями).
Стойкость покрытия толщиной 5—10 мм составляет одну-две плавки, слоя толщиной 20—100 мм — от одной до восьми плавок; износ покрытия составляет 2—20 мм за плавку, т. е. заметно выше, чем самой футеровки. Расход торкрет-массы изменяется от 0,6 до 3,5 кг/т стали, достигаемое повышение стойкости футеровки от 20 до 100% и более. Стойкость футеровки 160-т конвертеров ЗСМК и НЛМК составляет 1000—1200 плавок. Расход огнеупоров при торкретировании на разных заводах приведен ниже: