Особенности службы футеровки дуговых электропечей
При выборе огнеупорных материалов для футеровки дуговых сталеплавильных печей необходимо учитывать, что отдельные участки футеровки работают в разных условиях. В связи с этим следует отдельно рассматривать условия службы огнеупоров подины и откосов, стен и свода.
Подина и откосы
В течение длительного времени огнеупорная футеровка подины непосредственно контактирует с расплавленными металлом и шлаком. После выпуска плавки и при загрузке холодной шихты происходит резкое охлаждение подины. При загрузке шихты корзиной подина в целом испытывает механический удар, а поверхностный слой подины повреждается врезающимися кусками скрапа.
В период плавления при неудачно составленной завалке, когда под электродами оказывается легковесная шихта, электроды могут опуститься до подины прежде, чем на ней образуется достаточный слой жидкого металла. Горящие при тонком слое металла дуги перегревают и вымывают материал подины, образуя ямы.
Во время плавления и в окислительный период футеровка подины насыщается закисью железа. В восстановительный период окислы железа переходят в обратном направлении — из футеровки подины и откосов в металл и шлак. Восстановительная среда после выпуска плавки снова меняется и становится окислительной.
При сливе и после слива металла футеровка подины непосредственно контактирует со шлаком и насыщается им. В значительно большей степени, чем подина, воздействию шлаков при высоких температурах подвержена футеровка откосов, поэтому откосы являются наиболее слабым участком футеровки электропечей. Футеровка подины и откосов не только подвержена влиянию указанных выше факторов, но и сама влияет на ход процесса в сталеплавильной ванне. Попадающая в шлак окись магния снижает жидкотекучесть шлака, уменьшает его химическую активность. В связи с этим не только увеличивается расход огнеупорных материалов, но и требуется больше времени на рафинирование металла, повышается расход шлакообразующих на нейтрализацию вредного влияния MgО, увеличивается расход электроэнергии.
Исходя из назначения и условий работы футеровки подины и откосов, к ней можно предъявить ряд требований. Рабочий слой по дины, непосредственно контактирующий с металлом и шлаком, должен обладать высокой огнеупорностью, термостойкостью, противостоять химическому и механическому воздействию металла и шлака. Подина в целом должна быть достаточно механически прочной, чтобы воспринимать механические удары при загрузке шихты, и обладать большим тепловым сопротивлением.
Стены
Температурные условия работы внутренней поверхности стен особенно тяжелы, так как в отдельные периоды плавки температура некоторых участков стен может превысить огнеупорность материала, а при открывании рабочего пространства и загрузке шихты стены быстро охлаждаются. Скорость изменения температуры внутренней поверхности стен может достигать, как уже отмечалось, 10 000 °С/ч, что создает значительные термические напряжения в футеровке.
В связи с этим внутренний слой футеровки должен быть выполнен так, чтобы ему были свойственны высокая огнеупорность и термостойкость, низкий коэффициент теплового расширения и высокий коэффициент температуропроводности, а для получения большого теплового сопротивления футеровка стен должна быть хорошо теплоизолирована с внешней стороны.
В особо тяжелых температурных условиях работает нижний пояс футеровки стен шириной 300—400 мм, находящийся под прямым излучением дуг и воспринимающий нагрузку от верхних слоев кладки стен. Поэтому нижнюю часть стен следует выполнять из особо огнеупорных материалов, или в крайнем случае, делать ее достаточно большой толщины.
Свод
Свод является наименее долговечной частью футеровки дуговых печей.
Как и футеровка стен, свод испытывает значительные температурные колебания. По ходу плавки свод может прямо воспринимать излучение выдуваемых из-под электродов дуг, а также поглощать отражаемое шлаком и футеровкой стен излучение. В результате температура свода, особенно его центральной части, может превысить огнеупорность материала, и свод может подплавляться. Особенно часто подплавление свода происходит при работе с очень жидкими шлаками, обладающими большой отражательной способностью.
При открывании рабочего пространства и отвороте свода его излучение воспринимается холодными элементами конструкции печи, и свод быстро остывает. Это вызывает появление больших термических напряжений, приводящих к скалыванию свода.
Свод постоянно испытывает сжимающую нагрузку от распора, что снижает температуру начала его деформации. Выбивающиеся из печи раскаленные газы содержат много пыли, которая оседает на своде и при высокой температуре может вызвать его химическое разрушение.
Исходя из особенностей службы огнеупоров в сводах дуговых печей, к ним можно предъявить ряд особых требований. Эти огнеупоры должны характеризоваться высокой огнеупорностью, термостойкостью, химической стойкостью по отношению к плавильной пыли, большим тепловым и электрическим сопротивлением. Последнее вытекает из того, что при недостаточном электрическом сопротивлении материала свода электрическая цепь между фазами может частично замкнуться по своду. Это может привести к возникновению электрических дуг между сводом и водоохлаждаемыми элементами уплотнений электродов в своде, прогоранию водяной рубашки и по паданию в печь воды.
Материалы для футеровки
Так как огнеупорных материалов, в которых сочетаются одновременно все требуемые свойства, не существует, то футеровку дуговых печей приходится изготовлять состоящей из нескольких слоев, выполняющих те или иные функции. Это приводит к тому, что в фу теровке дуговых печей используют разнообразные огнеупорные материалы, обладающие разными свойствами и используемые для разных целей.
В зависимости от технологического процесса футеровку дуговых печей можно выполнять из кислых или основных огнеупорных материалов.
Для изготовления кислой футеровки используют кварцит и изделия из него (динас) с содержанием основного компонента (SiО2) в количестве 95—97%. При изготовлении динасового кирпича в качестве связующего материала применяют известковый раствор (2,0—2,2%) и раствор сульфитного щелока или патоки.
Для футеровки печей с основной кладкой применяют материалы и изделия из магнезитового порошка с добавлением бедной хромистой и железной руды. На ряде заводов в качестве огнеупорного материала для футеровки электропечей применяют доломит и изделия из него.
На отечественных заводах для изготовления основной футеровки используют главным образом магнезитовый порошок. Качество его зависит от химического и гранулометрического состава, а также плотности, позволяющей судить о степени обжига порошка. Содержание примесей в магнезитовых порошках, используемых для набивки подин и заправки откосов электропечей, не превышает по СаО 2,5—4,0% , по SiО2 4,0—5,0%; потери при прокаливании находятся в пределах 0,6—0,8%. Зерновой состав указанных порошков должен быть в следующих пределах: мельче 0,5 мм — не более 60%, мельче 1 мм — не более 80%.
Для кладки сводов используют высокоогнеупорные обожженные магнезитохромитовые изделия, изготавливаемые из магнезитового порошка и хромовой руды. Изделия прессуют под большим давлением и подвергают высокотемпературному обжигу при температуре 16000С.
Огнеупорные материалы характеризуются следующими свойствами: огнеупорностью, температурой начала размягчения под нагрузкой, термостойкостью, механической прочностью при сжатии, химическим составом, способностью к взаимодействию с основными и кислыми шлаками и стоимостью:
- огнеупорностью называется свойство материала противостоять, не расплавляясь, воздействию высоких температур;
- температура начала размягчения под нагрузкой характеризует ту температуру, при которой образец огнеупорного материала высотой 50 мм, находящийся под нагрузкой 2 кг/см2 сжимается на величину, равную 40 % от первоначальной длины образца;
- термостойкость — способность выдерживать резкие изменения температуры без разрушения: она определяется числом теплосмен, которые выдерживают огнеупорные кирпичи до того, как они частично разрушатся и потеряют 20 % своего первоначального веса. Теплосмена осуществляется следующим образом: кирпичи нагревают до 850 «С и затем быстро охлаждают в проточной воде.
Кроме высокой огнеупорности не менее важным свойством является температура начала размягчения под нагрузкой. В этом отношении явные преимущества имеют динасовые кирпичи, несмотря на более низкую их огнеупорность. Особенно это свойство присутствует в сводах, в печах, как с кислой, так и с основной футеровкой. В таблице 1 приведены свойства огнеупорных материалов.
Наиболее термостойким из перечисленных огнеупоров являются хромомагнезитовые, но они очень дорогие. Наибольшее увеличение размеров и объема при нагревании имеют магнезитовые и динасовые кирпичи, однако при высокой температуре магнезитовые кирпичи имеют дополнительную усадку (-1,0 %), что приводит к образованию щелей между отдельными кирпичами. Увеличение размеров желательно при кладке сводов и арок, так как они увеличивают стрелу выпуклости и повышают прочность кладки, поэтому магнезитовые кирпичи не применяют для сводов. В тех случаях, когда увеличение размеров кладки должно быть уменьшено, следует класть между отдельными кирпичами легко сгорающие прокладки из фанеры, толя или папки. Своды из магнезитовых кирпичей и хромомагнезитовых следует утеплять. Для теплоизоляционных материалов главным свойством является низкая теплопроводность в виду того, что температура на границе внутреннего и наружного слоя достигает 1200—1300°С. Необходимо сразу за высокоогнеупорными материалами располагать шамотные, а еще лучше легковесные кирпичи.
Высокоогнеупорные магнезитохромитовые изделия подразделяют на следующие марки:
- ПШСП — периклазошпинелидные магнезитохромитовые плотные с тонкомолотой хромовой рудой в шихте;
- МХСП — магнезитохромитовые плотные с крупнозернистым хромитом в шихте;
- ПШСО — периклазошпинелидные магнезитохромитовые обычные с тонкомолотой хромовой рудой в шихте;
- МХСО — магнезитохромитовые обычные с крупнозернистой хромовой рудой в шихте.
Основной составляющей (65—70%) этих изделий является окись магния. Содержание хромовой руды в зависимости от марки кирпича находится в пределах 7—18% при применении кимперсайской руды и в пределах 5—12% при применении сарановской руды.
Плотные изделия (ПШСП и МХСП) предназначены для изготовления работающих в особо тяжелых условиях сводов электропечей емкостью более 40 т. Обычные изделия (ПШСО и МХСО) могут быть использованы для изготовления сводов печей меньшей емкости.
Изделия указанных марок изготавливают в виде прямого и пятового кирпичей. Длина прямого кирпича (и, следовательно, толщина свода) составляет 230, 300, 380, 460 и 520 мм.
Для кладки стен и изготовления сводов электропечей малой и средней емкости применяют высокоогнеупорные хромомагнезитовые изделия огнеупорностью не ниже 2000°С, изготавливаемые из хромита и спекшегося магнезита. Содержание основных компонентов в этих изделиях (кирпичах) должно быть в следующих пределах: окиси магния не менее 42%, окиси хрома не менее 15%.
Кладку подин и откосов выполняют из магнезитовых (периклазовых) изделий огнеупорностью выше 2000° С, изготовляемых прессованием из обожженного до спекания магнезита. Магнезитовые изделия подразделяют в зависимости от химического состава на три марки: М-91 (магнезитовые изделия обычной плотности, предназначаемые для кладки подин и откосов электросталеплавильных печей ниже уровня шлака), МП-91 (изделия плотные, предназначаемые главным образом для кладки откосов в районе шлакового пояса), МП-89 (плотные изделия, используемые для кладки футеровки электропечей в исключительных случаях).
Физико-механические свойства магнезитовых изделий приведены в таблице 2.
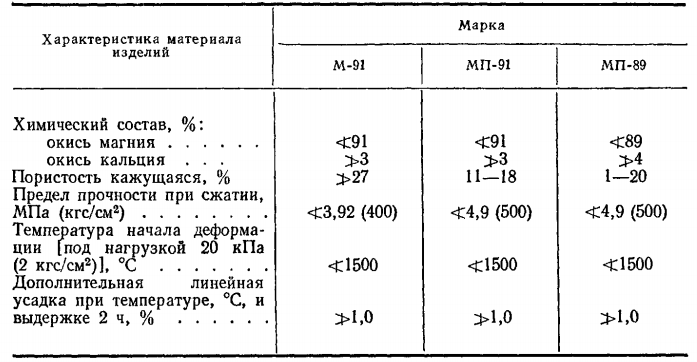
Для тепловой изоляции подины и стен, а также для футеровки сливного желоба используют шамотный кирпич, который обладает низкой теплопроводностью и высокой термостойкостью. Вследствие низкой огнеупорности (1680—1730° С) шамотный кирпич нельзя использовать для изготовления рабочего слоя футеровки, но вследствие высокой термостойкости его широко применяют для футеровки сталеразливочных ковшей и сталеразливочного припаса.
Шамотные изделия обычно содержат 60—62% SiO2 и 35—37% Аl2O3. Изготавливают их методом пластической формовки или полусухого прессования, причем метод полусухого прессования сейчас преобладает.
В футеровке для тепловой изоляции применяют также асбест, порошок шамота и другие теплоизоляционные материалы.
Связующие материалы
В качестве связующих наибольшее применение в производстве находят жидкое стекло и огнеупорная глина, однако возможно использование каменноугольной смолы и песка.
Жидкое стекло представляет собой технический силикат натрия, растворимый в воде. По ГОСТ 13078 применяется содовое стекло.
Огнеупорная глина в сухом молотом виде применяется как связующее вещество для кварцевого песка.
Кладка рабочего пространства печи
В качестве примера на рисунки 1 приведен разрез футеровки печи емкостью 100 т.
Изготовление футеровки новой печи начинают с подины. Подина печи состоит, как правило, из трех слоев: верхнего набивного, образующего после спекания монолитную массу, кирпичной кладки, являющейся основанием для набойки, и теплоизоляционного слоя. Возможна работа печи и без набивного слоя, но при этом толщина кирпичной кладки должна быть увеличена.
На большинстве электропечей общая толщина футеровки подины равна максимальной глубине ванны. На печах, оборудованных располагаемым под днищем механизмом электромагнитного перемешивания металла, толщину подины уменьшают, что улучшает магнитную связь между ванной и перемешивающим устройством, позволяет уменьшить мощность перемешивающего устройства, его стоимость и расход электроэнергии. Но выигрыш в стоимости перемешивающего устройства по мере уменьшения толщины подины уменьшается, а опасность прорыва металла через подину увеличивается; при этом быстро возрастают и тепловые потери через подину. Поэтому на печах, оборудованных электромагнитным перемешивающим устройством, толщину подины целесообразно принимать равной 70—80% от глубины ванны.
Толщина огнеупорной кладки по центру 100-т печи, оборудован ной механизмом электромагнитного перемешивания, составляет 800—900 мм (рисунок 1).
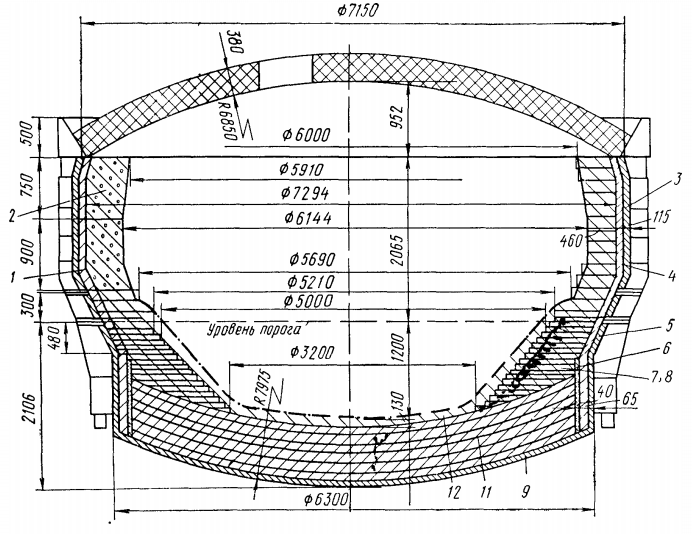
На металлическое днище укладывают изоляционный слой футеровки, состоящий из листового асбеста 9 толщиной около 20 мм, шамотного порошка и двух рядов на плашку шамотного кирпича 10. Для перекрытия швов кладки подины каждый последующий ряд кирпича разворачивают на 45° по отношению к нижележащему. Магнезитовую кладку подины 11 выполняют из пяти-шести рядов кирпича марки М-91, уложенного на ребро. Швы между кирпичами засыпают сухим подогретым магнезитовым порошком крупностью 0,5—0,8 мм.
На ряде заводов кладку подины ведут «елочкой» от центра печи к периферии. Для уплотнения кладки и хорошего заполнения швов после каждого ряда кирпичи тщательно простукивают деревянными молотками. Между кладкой подины и изоляцией стенок кожуха оставляют температурный зазор 70—80 мм, который засыпают порошкообразным асбестом 5, 6. Откосы выкладывают прямым и клиновым кирпичом 7, 8 марки М-91 или МП-91.
До недавнего времени рабочую часть подины 12 (150—200 мм) набивали из смоломагнезитовой массы, которую готовили из мелко зернистого магнезитового порошка (крупность зерен до 2 мм) и каменноугольной смолы с содержанием влаги не более 0,4%. Для обезвоживания смолу предварительно кипятили в течение суток, после чего в нее добавляли 10% каменноугольного песка. Перед замешиванием магнезитовый порошок подогревали до 80—100° С и добавляли в него 10—12% смеси смолы с песком. Набивку вели слоями не более 50 мм при помощи пневматических трамбовок. Такой трудоемкий и длительный (2—3 суток) способ изготовления набивной подины еще сохранился на некоторых предприятиях и в настоящее время.
В 1961—1962 гг. был опробован и внедрен способ набивки подины, заключающийся в следующем. Магнезитовый порошок марки МПП-85 (зерновой состав: фракции мельче 0,1 мм 15—25%, З-т-6 мм 10—30% и крупнее 6 мм — не более 3%) увлажняют водным раствором жидкого стекла. Полусухой массой заполняют уступы в кирпичной кладке, затем ее наносят на подину слоями толщиной 50 мм и трамбуют пневматическими молотками.
На 100-т печах Челябинского металлургического завода подину набивают вообще сухим порошком марки МПП-85 в один прием (масса порошка —12 т). Плотность набивной подины и откосов про веряют металлическим стержнем диаметром 5 мм, который при нажатии рукой должен входить на глубину не более 10 мм.
По окончании набивки подины и откосов по всей сферической ванне укладывают листовое железо, предохраняющее набивной слой от разрушения при первой завалке шихты и способствующее лучшей свариваемости набивного слоя на первой плавке. Стойкость подины, изготовленной таким способом, оказалась вполне удовлетворительной, а продолжительность набивки сократилась до 8 ч против 2—3 суток при набивке смоломагнезитовой массой.
Футеровку стен также, как правило, выполняют из двух слоев — защитного и рабочего (рисунок 1).
Защитный ряд 100-т печи от кожуха выкладывают хромомагнезитовым кирпичом 3 толщиной 115 мм в перевязку от последнего ряда откосов до песочного затвора свода. На откос шириной 570 мм насыпают магнезитовую прослойку 20—30 мм из набивной массы или мелкого заправочного магнезитового порошка на жидком стекле.
Кладку рабочего слоя из кирпича марок ПШСП, МХСП или ПШСО, МХСО начинают с выпускного отверстия и ведут к завалочному окну, а верхние два ряда кладут в обратном направлении. Выпускное отверстие выкладывают размером 350—450 мм; столбики у завалочного окна выкладывают вперевязку до упора в арку. Каждый ряд кладки стен просыпают мелкозернистым магнезитовым порошком.
Толщина футеровки стен без защитного ряда на печах большой и средней емкости составляет 460 мм, а на печах малой емкости (5—10 т) толщина футеровки на уровне откосов 400—450 мм, а вверху 300 мм.
Существует и способ изготовления стен из блоков (позиции 1, 2, рисунок 1), изготовленных из магнезитового порошка (50%) и обожженного доломита (50%). Для связки в смесь добавляют 7—10% каменноугольного пека. Набивку блоков выполняют вручную пневматическими трамбовками в металлических разъемных шаблонах. Обычно футеровка состоит из двух или трех блоков. Но большинство заводов отказалось от этого тяжелого и малоэффективного способа изготовления блоков для футеровки стен Электропечей и перешло на применение кирпичной кладки.
Футеровку свода выполняют на специальном шаблоне вне печи. Установленное по центру шаблона сводовое кольцо проверяют на гидравлическую плотность, для чего его опрессовывают под давлением 700—900 кПа (7—9 ат) для печей емкостью 100 т и 500 кПа (6ат) для печей малой емкости. Между кладкой свода и сводовым кольцом выполняют тепловую изоляцию из листового асбеста на шамотном растворе.
Свод 100-т печей выкладывают из кирпича марок ПШСП и МХСП длиной 380 мм. Существуют различные способы наборки сводов.
На рисунки 2 изображена схема кладки свода с центральной аркой.
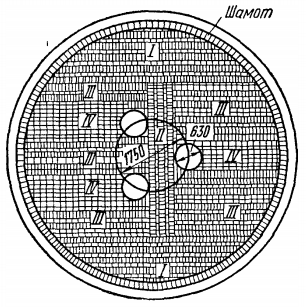
При наборке свода по такой схеме центральная арка проходит между отверстием для электрода второй фазы с одной стороны и первой и третьей — с другой. По бокам электродных отверстий в центральную арку упираются опорные арочки. Для укрепления площадки под экономайзер на некотором расстоянии от края отверстий для электродов в «ребре» устанавливают кирпич длиной 460 мм.
Для печей малого тоннажа своды набирают из кирпича длиной 230 мм. Наборку свода начинают с установки пятовых кирпичей. Затем концентрическими рядами всухую выполняют купольную кладку свода. Центральную часть магнезитохромитового свода можно выкладывать на растворе из 80% тонкомолотого магнезитового порошка и 20% огнеупорной глины, затворенных на жидком стекле. При кладке на каждые 2—3 м длины концентрического ряда оставляют один замковый кирпич, выступающий не более чем на 1/3 своей длины. Замковые кирпичи забивают после окончания всей кладки свода.
Центральная часть свода изнашивается быстрее, чем периферийная, поэтому иногда целесообразно подвергать своды частичным ремонтам, при которых на шаблоне заменяют лишь кладку центральной части свода. На некоторых заводах центральную часть свода выполняют увеличенной толщины (рисунок 3).
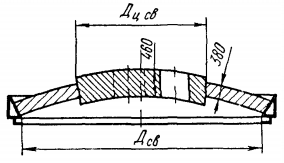
Для увеличения стойкости футеровки отдельные ее участки целесообразно выполнять из огнеупоров с особыми свойствами. Так, на некоторых заводах США футеровку стен по шлаковому поясу и немного выше выполняют из плавленых огнеупоров, обладающих повышенной огнеупорностью и шлакоустойчивостью. Электродные отверстия иногда футеруют высокоглиноземистым кирпичом с содержанием Аl2O3 не менее 70%. Такой кирпич обладает высоким электросопротивлением, что уменьшает опасность замыкания цепи между фазами по своду.
Предпринимаются попытки увеличить стойкость футеровки, используя для этого водяное охлаждение. В США применяли водоохлаждаемые кожухи с двойными стенками, а в стены напротив дуг закладывали водоохлаждаемые трубы. Однако ни тот, ни другой способ охлаждения стен распространения не получил, так как при этом резко возросли тепловые потери печи и расход электроэнергии.
На одном из отечественных заводов работает 10-т электропечь с водоохлаждаемым сводом. Свод представляет собой конструкцию коробчатого типа, на поверхность которой со стороны рабочего пространства нанесена тепловая изоляция — набивка. Масса для набивки состоит из хромомагнезитового порошка (93%), огнеупорной глины (6%) и кремнефтористого натрия (1%); затворяется она на жидком стекле. Толщина набивки составляет 65 мм. Для удержания набивки рабочая поверхность свода армирована стальной лентой в виде ячеек 100х100 мм.
Применение водоохлаждаемого свода, по предварительным данным, увеличивает расход электроэнергии на 9—10%.
На крупных электропечах имеется возможность периферийную часть свода выполнять по типу сводов мартеновских печей — распорно-подвесной. Стойкость распорно-подвесного свода несколькобольше стойкости распорного свода, так как в этом случае часть силы тяжести кладки свода воспринимается металлоконструкциями подвески и сжимающие напряжения в кладке уменьшаются. Использование распорно-подвесных сводов на печах малой и средней емкости затруднено из-за опасности замыкания электрической цепи между фазами по металлоконструкциям подвески.
Производительность электропечей может быть повышена не только увеличением стойкости футеровки, но также и ускорением ее ремонта.
В настоящее время ломку износившейся футеровки стен часто осуществляют еще вручную. Для этого после снятия или отворота свода на подину мостовым краном устанавливают водоохлаждаемую площадку, а стены обдувают вентилятором. Кирпич обрушивают вручную ломиками.
На ряде электросталеплавильных цехов конструкция кожухов каркаса выполнена разъемной (на болтах или клиньях), что позволяет поднять часть кожуха с футеровкой стен мостовым краном и полностью исключить ручной труд при ломке футеровки.
В старых электросталеплавильных цехах для ломки футеровки стен можно пользоваться штангой, надеваемой на хобот завалочной машины. Футеровку стен обрушивают на подину, а обрушенную футеровку удаляют через рабочее окно специальным гребком, также надеваемым на хобот завалочной машины.
Футеровка электропечи — кислый процесс
Для футеровки кислой электропечи применяется динасовый кирпич, кремнеземистый песок и теплоизоляционные материалы.
Динасовый кирпич изготавливается из измельченного кристаллического или аморфного кварцита. В процессе отжига динасовый кирпич увеличивается в объеме, что связано с аллотропическим превращением кварца при нагревании. При температуре 575 °С a — кварц переходит в b — кварц с увеличением в объеме на 2 %. Дальнейшее нагревание до 870 °С b — кварц перерождается в тридимит, который при температуре 1470 °С превращается в кристаллобалит; последний при температуре 1710 °С переходит в аморфное состояние и начинает плавиться. В результате объем увеличивается на 14,3 %. Качество динасового кирпича определяется его плотностью, показывающее результаты превращений.
Кварцевый песок состоит из кварца и некоторого количества примесей и окислов. В зависимости от содержания окислов меняется цвет песка от белого до красного. Для набивки и заправки подины применяется кварцевый песок.
Шамотный кирпич изготавливается путем обжига из огнеупорного шамота и огнеупорной глины и содержит не менее 30 % глинозема. Шамотный кирпич применяется для футеровки внутренней части стенок и нижнего ряда подины кислой электропечи. Попытка замены динасового кирпича шамотным на своде кислых электропечей не увенчались успехом.
Главная причина преждевременного разрушения состоит в выпадении кирпичей из свода. Частичное применение кирпича в местах, не прилегающих к плавильному пространству и не соприкасающегося с расплавленным металлом, способствует некоторому уменьшению расхода тепла, так как теплопроводность шамотного кирпича меньше, чем динасового.
Асбест применяется как теплоизоляционный материал, стойкий при температурах до 700 °С. С повышением температуры асбест теряет свою форму и резко ухудшает свои теплоизоляционные и диэлектрические свойства. При высоких температурах асбест химически неустойчив и реагирует с расплавленными шлаками. Асбест применяется в виде тонких листов и волокон. Теплопроводность асбеста весьма низка.
Теплопроводность некоторых материалов приведена в табл. 1.5.
Футеровка подины
При футеровке электропечи в первую очередь выкладывается подина. Выкладка подины начинается с выкладки на сферической и плоской поверхности дна печного кожуха асбестовых листов, являющихся подкладкой для нижнего ряда шамотных кирпичей. На шамотные кирпичи набирается несколько рядов в соответствии с установленной толщиной подины динасового слоя: стенки печи воздвигаются динасовой кладкой. Средняя часть подины набивается массой из кварцевого песка. Набивка подины является весьма простой операцией, и соблюдение известных практических правил при набивке обеспечивает хорошую спекаемость при разогреве печи. Полиморфные превращения кварца, в результате которых получаются тридимит и кристалобалит, сопровождаются ростом зерен и возможны для определенных сортов песка.
Хорошие заправочные пески должны состоять больше половины из зерен одинаковой величины и средней крупности (например: 1К02А (В) Люберецкого карьера) с содержанием кремнезема не менее 98—99 %. Для повышения пластичности набивной массы к песку примешивается жидкое стекло.
Набивка подины производится в следующей последовательности.
После окончания работ по кладке кирпичной футеровки печь очищается от остатков кирпича и мусора, после чего на кладке подины разводится костер из дров для нагрева до 50—100 °С и одновременно подготавливается масса для набивки подины. Сырой песок тщательно просушивается для хорошей его смешиваемости с жидким стеклом. Жидкое стекло прибавляется к песку в количестве 10 % по объему, и после перемешивания масса легко образует рассыпающиеся комочки.
На нагретую поверхность динасовой кладки наносится из пульверизатора тонкий слой жидкого стекла, на него накладывается приготовленная набивочная масса и уплотняется ручными трамбовками до тех пор, пока не исчезнут следы ударов трамбовки. При набивке откосов для проверки величины углов стыка с подиной применяется деревянный шаблон, имеющий форму профиля ванны (рис. 1.3). Измененные толщины набивного слоя подины в пределах 110—150 мм достигается не за счет высоты плавильной ванны, а путем изменения толщины кирпичной кладки.
Футеровка стенок
Кирпичные стенки электропечи в соответствии с формой ее корпуса цилиндрические, что затрудняет применение для ее кладки цельного нормального кирпича. При кладке стенок электропечи при отсутствии фасонного клиновидного кирпича обычно прямоугольный кирпич вытесывают в форме клина, но правильнее выкладывать стенки из целого прямоугольного кирпича за счет уступов на поверхности стенок заполняемой кварцевой набивкой. Качество кладки стенок зависит от тщательности подгонки граней кирпича, кладка заключается в составлении рядов из заранее приготовленных кирпичей без заполнения швов раствором всухую, с просыпкой швов кварцевым песком.
Перед началом кладки стенок корпус печи с внутренней стороны обкладывается асбестовыми листами. В притык к асбестовым листам выкладываются ряды шамотного кирпича общей толщиной 65 мм и далее возводятся динасовые стенки толщиной не менее, чем в один кирпич.
Требуемая плотность кладки стенок достигается, помимо качественной тески и подгонки кирпичей, заполнением кварцевым песком остающихся зазоров и швов. Кирпичная кладка не доводится до края железного корпуса на 40—60 мм; это пространство после окончания кладки засыпается сырым кварцевым песком и служит как для компенсации расширения кирпича стенок, так и для необходимой плотности между сводом и стенками. В процессе роста стенок печи сырой песок высыхает, а излишки его высыпаются.
При выкладке стенок из фасонных кирпичей через каждые 300—400 мм проставляются фанерные или картонные прокладки для того, чтобы плотно пригнанные ряды кирпичей при росте динаса не выпучивались. При кладке тесанного кирпича установка прокладок не требуется, поскольку температурные швы между ними образуются за счет неровностей граней. Грани кирпичей, обращенные в сторону рабочего пространства печи, должны быть ровными.
Футеровка свода
Независимо от сорта и качества кирпича выкладка сводов производится по шаблону, представляющему собой площадку по форме свода с установленными на ней шаблонами отверстий для электродов. Шаблонная площадка заканчивается кольцевым углублением для размещения каркаса свода с отметкой установки его замка. Шаблоны изготавливаются из дерева. Для выкладки сводов электропечи применяют нормальный кирпич.
Применяются три способа выкладки круглых сводов: секторно-арочный, концентрическими рядами и секторами (рис. 1.4, 1.5), куполообразный свод, выложенный концентрическими рядами, имеет хорошую стойкость только при наличии фасонного кирпича.
Секторный свод выкладывается одновременно с четырех сторон от кольца свода к центру. При этом отверстия для электродов находятся в квадратном участке, выполняемом перпендикулярными рядами. Наиболее прочным является секторно-арочный свод (см. рис. 1.5). Порядок наборки этого свода следующий: сначала выкладывается сплошная арка, проходящая между отверстиями среднего электрода и отверстиями крайних электродов шириной в 3-4 ряда, толщиной каждый в полкирпича (115 мм), затем набираются половинки по ту и другую сторону от центральной арки, образуемые из рядов, набираемых перпендикулярно арке толщиной 115 мм. Ряды половинок не доводятся до арки с таким расчетом, чтобы электродные отверстия образовались в рядах, идущих параллельно центральной арке, которые в свою очередь являются арками.
После образования электродных отверстий забиваются замки на всех рядах половинок. Замки соседних рядов половинок не должны совпадать друг с другом.
Как секторный свод, так и секторно-арочный набираются из тесаных кирпичей и температурные прокладки можно не ставить. При выкладке свода из фасонного кирпича необходимо делать своды концентрическими рядами.
Для каждой работающей печи необходимо всегда иметь готовый набранный запасной свод.
Футеровка электропечи — основной процесс
Материалы для футеровки
При выплавке стали основным процессом, особенно легированных сталей, футеровка печей работает при весьма тяжелых условиях. Температура ванны в конце продувки ее кислородом поднимается до 1800 °С и даже 1850 °С. Перегрев металла приводит к размягчению и разрушению футеровки.
Принцип кладки подины, откосов и свода не отличается от кислой футеровки, различия только в применении основных огнеупоров: шамотного кирпича класса А, магнезитового кирпича 1 -го сорта, магнезитового порошка, хромитового порошка. Магнезитовый и хромитовый порошки должны иметь следующий зерновой состав: мельче 2 мм — 75 %, от 2 до 4 мм — 25 %, крупнее 4 мм не допускается.
Для засыпки швов шамотной кладки подины используют шамотный порошок с величиной зерна не более 0,5 мм. Для засыпки швов магнезитовой кладки используют магнезитовый порошок с величиной зерна не более 0,5 мм. Для набивки подины применяется жидкое стекло по ГОСТ 13078-80 в виде водного раствора в пропорции — одна часть жидкого стекла, одна часть воды по объему; плотность жидкого стекла должна равняться
1,4 г/см3; асбест листовой ГОСТ 9347, толщина 5—10 мм.
Кладка подины и откосов
После очистки от остатков старой футеровки днище каркаса выстилают листовым асбестом, углы в местах сопряжения днища и каркаса, а также головки болтов выравнивают засыпкой шамотного порошка. На асбест укладывают нормальный шамотный кирпич на плашку в один ряд. Затем укладывают магнезитовый кирпич на плашку и на ребро в зависимости от емкости печи: на плашку до 5 т — один ряд, 10—30 т — два ряда.
Кладку подины и откосов производят всухую с притеской и притиркой швов. Выкладку подины начинают “елочкой” от центра печи к стенкам. Кладку последующего ряда по отношению к предыдущему ведут под углом 45°. Швы магнезитовой кладки засыпают горячим магнезитовым порошком. Температурный зазор между кирпичной кладкой подины и откосов и кожухом печи должен быть 30—50 мм. Этот зазор засыпают крупным магнезитовым порошком после окончания кладки каждого ряда. После окончания кладки подины выкладывают уступами откосы магнезитовым кирпичом на плашку в соответствии с чертежом печи до уровня основания стен. Кладку откосов производят аналогично кладке подины.
Перед набивкой подину разогревают по всей поверхности дровами или газом в течение двух часов, затем ей дают остыть до температуры 70—80 °С, после чего тщательно очищают от мусора и пыли и приступают к набивке.
Набивка подины и откосов дуговых электропечей
Для дуговых электропечей, выплавляющих нержавеющие марки стали типа Х18НЮТ, применяют набивку подины массой из магнезитового и хромитового порошков и жидкого стекла.
Смесь магнезитовою и хромитовою порошков готовят в пропорции: магнезитового порошка — 65 % по объему, хромитового — 35 %.
Смесь в сухом виде перемешивают в механическом смесителе в течение 15—20 мин., а затем увлажняют раствором жидкого стекла (20 % по весу смеси) вновь тщательно перемешивают до равномерной влажности. Масса наносится равномерным слоем толщиной не более 40 мм по всей поверхности ванны и набивается ручными пневматическими трамбовками без подогрева бойков.
Общая толщина набивного слоя в центре 110-200 мм в зависимости от емкости печи.
После окончания набивки устанавливается свод и производится сушка подины дровами и газом в течение 8-10 ч.
Наборка сводов
Своды для печей — основной процесс для выплавки нержавеющих сталей, набирают из динасового или магнезитохромитового кирпича. В настоящее время применяют преимущественно магнезитохромитовые своды, наборку которых осуществляют двумя способами; насухо и на высокоогнеупорном цементном растворе.
Наборку магнезитохромитовых сводов насухо выполняют в металлическом водоохлаждаемом кольце со стрелой прогиба 1/7—1/8 от диаметра свода. Перед наборкой кольцо проверяют на герметичность водой под давлением 0,6 Мн/м2 (6 атмосфер). Толщина магнезитового свода для печей от 5 до 20 т рекомендуется 230 мм.
Наборку сводов из магнезитохромитового кирпича на высокоогнеупорном цементном растворе выполняют в том же металлическом кольце, при этом во время кладки на поверхность кирпича мастерком наносят раствор. Во избежании выжимания раствора из швов, уплотнение кладки клиновыми замками не производят. Набранный свод выдерживают в неподвижном состоянии не менее суток. Стойкость магнезитохромитовых сводов составляет около 200 плавок.