Виды электрошлаковых отливок
В настоящее время ЭШЛ осуществляется по двум технологическим схемам. Первая (рисунок 1) состоит в том, что расходуемые электроды переплавляются непосредственно в кристаллизаторе, в котором формируется отливка. При этом происходят ее последовательное наплавление и кристаллизация.
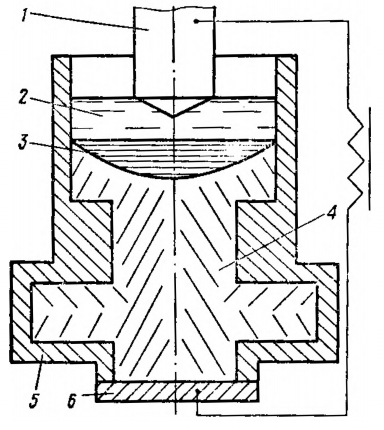
ванна; 4 — отливка; 5 — кристаллизатор; 6 — поддон.
Рисунок 1 — Схема ЭШЛ при выплавке в кристаллизаторе отливки целиком
В кристаллизаторе может быть выплавлена целиком вся отливка или ее объединяющая часть (рисунок 2). В этом случае заранее выплавленные или приготовленные другим методом элементы будущей литой заготовки устанавливаются в соответствующие отверстия кристаллизатора и при выплавке объединяющей части приплавляются к ней.
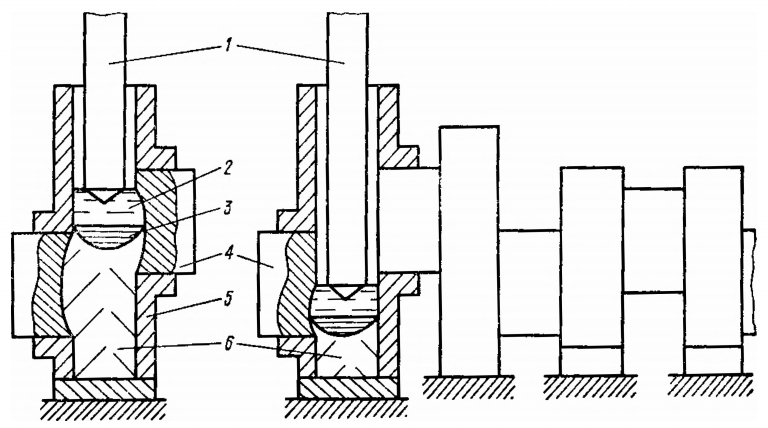
Вторая схема (рисунок 3) состоит в том, что, переплавляя расходуемые электроды в специальной плавильной емкости, накапливают жидкий электрошлаковый металл и затем заливают его в соответствующую форму. Этот способ получил название фасонного электрошлакового литья (ФЭЛ) и кокильного литья (ЭКЛ).

Метод ЭШЛ разработан в ИЭС им. Е. О. Патона АН УССР и внедрен в промышленность. Наибольшее применение он нашел в производстве заготовок для машиностроения и в первую очередь для деталей ответственного назначения. Это стало возможным благодаря исключительно высоким свойствам литого электрошлакового металла, его изотропности, химической и физической однородности. Показатели механических свойств электрошлаковой отливки такие же, как у кованого металла открытой выплавки и даже выше.
Отливки, производимые методом ЭШЛ и ФЭЛ, отличаются разнообразием как по конфигурации, так и по назначению. Их масса колеблется от нескольких десятков граммов (зубные протезы и коронки) до нескольких десятков тонн (коленчатые валы судовых дизелей). Такие отливки условно можно разделить на два типа.
К первому следует отнести отливки, имеющие внутренние несквозные полости, к другому — отливки сплошного сечения с приливами на наружной поверхности.
Наиболее типичным и простым по форме представителем первого типа отливок являются цилиндрические отливки, имеющие наружную поверхность без приливов и несквозную симметрическую полость, напоминающие по внешнему виду стакан.
Такие отливки используются в качестве заготовок сосудов давления. При этом отпадает необходимость в трудоемкой операции изготовления днищ, так как каждый стакан уже снабжен днищем, которое получается при выплавке отливки. Два стакана, сваренные друг с другом кольцевым швом, представляют собой не что иное, как заготовку сосуда или баллона. Обрабатывать наружную поверхность такого сосуда практически не требуется: ее форма и размеры получаются уже при выплавке половинок сосуда.
Цилиндрические отливки с несквозным отверстием применяются также в трубном производстве в качестве заготовок для последующего изготовления труб среднего диаметра путем горячей протяжки этих заготовок.
Отливки такого типа, но уже с приливами на наружной поверхности, например кольцевыми у края полого торца стакана, становятся заготовками сосуда (рисунок 4), у которого один торец заглушается съемной крышкой. Приливы на наружной поверхности отливки «стакан» в виде цилиндрических выступов служат патрубками, к которым приваривают трубы необходимых коммуникаций.
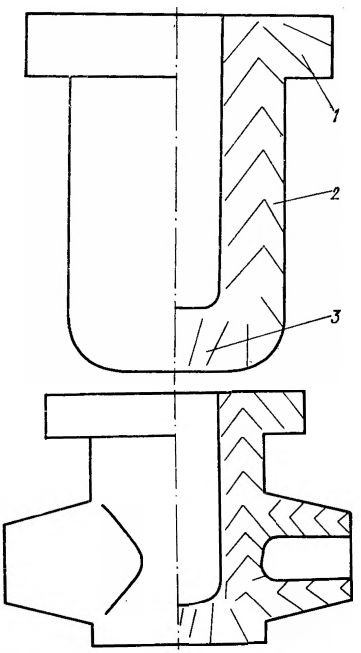
Глуходонная полая отливка с фланцем и цилиндрическими приливами на боковой цилиндрической поверхности также является заготовкой корпуса энергетической запорной арматуры. Методом ЭШЛ получаются корпуса арматуры с условным диаметром 100 — 500 мм.
По традиционной технологии корпуса арматуры отливаются в песчано-глинистые формы или изготовляются из поковок. Оба технологических варианта по эффективности существенно уступают технологии ЭШЛ заготовок корпусов арматуры.
Традиционная технология изготовления сосудов высокого давления предусматривает приварку к их корпусам патрубков. Такая технология чрезвычайно трудоемка. Это прежде всего связано с тем, что патрубок вваривается в корпус сосуда многослойной сваркой в течение многих часов. При обнаружении дефектов швы вырубаются и завариваются вновь. Цикл изготовления такого сосуда весьма длителен.
Электрошлаковая технология получения сосудов высокого давления с патрубками на их поверхности предусматривает два решения. Когда сосуд имеет в диаметре несколько метров, заготовка патрубков выплавляется непосредственно на его корпусе. Если диаметр сосуда невелик, он может быть выплавлен одновременно с патрубками.
Отливки с полостью могут иметь приливы, расположенные вдоль образующей цилиндрической поверхности. Такие приливы используются для последующего изготовления патрубков. Пространство между патрубками может быть образовано путем соответствующей механической обработки прилива (рисунок 5) для удаления лишнего металла.
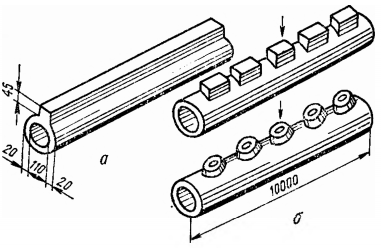
В энергетическом машиностроении большим спросом пользуются отводы (их еще называют коленами) под разными углами, например 90 и 180°, для присоединения прямых участков трубных коммуникаций при строительстве энергоблоков тепловых и атомных электростанций. Электрошлаковые отливки с полостью и криволинейной осью могут заменить отводы, которые обычно производят методами штамповки и сварки.
Требование энергетиков изготавливать отводы со стенкой переменного сечения для более рационального использования металла как нельзя лучше соответствует возможностям ЭШЛ и чрезвычайно затруднительно при других методах их производства.
Имеется еще один тип отливок. Это отливки, которые получают в виде заготовок сплошного сечения с приливами или углублением самой разнообразной формы на наружной поверхности. В качестве примера такой отливки можно привести заготовку небольшого по размерам запорного клапана энергоблока атомной электростанции, валок прокатного стана или калибры трубопрокатного стана.
Заготовка шатуна судового дизеля имеет переменное по высоте сечение, а заготовка коленчатого вала имеет пространственную форму. К отливкам, имеющим переменное сечение по высоте, можно также отнести заготовки кривошипов крупных судовых дизелей. В качестве примера отливки, но с криволинейной осью можно привести заготовку бандажа цементной печи или элемент венца шестерни.
Развитую поверхность и постоянное по высоте сечение имеют электрошлаковые отливки нестандартного профиля.
К отливкам сплошного сечения можно отнести мелкие заготовки зубных протезов и коронок, штамповых вставок, отливаемых вместе с гравюрой.
Следует отметить, что новая технология не ставит целью замену традиционных способов литья. Она должна применяться лишь в тех случаях, когда к отливке предъявляются повышенные требования по качеству металла или получение такой отливки сопряжено с большой трудоемкостью и затратами на изготовление оснастки, а также в случае необходимости производства изделий относительно мелкими сериями.
Выносливость электрошлакового металла
Опыт эксплуатации многих изделий на протяжении ряда лет показал, что детали, изготовленные из электрошлакового металла, обладают большим ресурсом, длительным сроком службы и повышенной надежностью. Это объясняется прежде всего тем, что электрошлаковый металл значительно лучше противостоит переменным или повторным нагрузкам, т. е. в большей степени сопротивляется усталости.
Технический прогресс неизбежно обусловливает повышение мощности, уровня нагрузок, рабочих скоростей и увеличение масс различных установок, аппаратов и деталей, расширение температурного интервала их работы. В связи с этим важным критерием качества металла, предназначенного для их изготовления, становятся не показатели статической прочности (σв, σо,2) или пластичности (δ, ψ), определяемые по результатам статических испытаний образцов на растяжение, а характеристики сопротивления металла повторным нагрузкам, т. е. показатели выносливости, в частности предел выносливости σ-1 при обычной (многоцикловой) усталости или долговечность N (циклы до разрушения) при малоцикловой, контактной и некоторых других видах усталости.
Отмеченные показатели выносливости становятся еще более существенными для характеристики высококачественного металла, особенно конструкционных сталей, предназначенных для изделий ответственного назначения. Естественно, улучшение качества металла в результате ЭШП должно найти свое отражение в повышении его выносливости вследствие благоприятного изменения количественных (содержание, размер, форма) и качественных (природа, физические, химические и другие свойства) характеристик загрязненности металла неметаллическими включениями.
Необходимо отметить, что неметаллические включения играют исключительно важную роль при усталости стали — они являются инициатором зарождения усталостных трещин. В научно-технической литературе последних лет наблюдается тенденция повышенного внимания к вопросам инициирования усталостного разрушения, причем отмечается факт зарождения трещин усталости именно у неметаллических включений.
В настоящее время существуют две отличные друг от друга точки зрения на роль неметаллических включений при усталости металла. Согласно одной из них, более ранней, главная причина опасности неметаллических включений — создаваемая ими (как внутренними надрезами) концентрация напряжений при действии внешних нагрузок. Исследования по расчету и измерению напряжений у включений показали, что максимальная концентрация напряжений возникает у полости (поры) и неметаллических включений, у которых модуль упругости Е меньше, чем у стали (пластичные силикаты, сульфиды и т.д.). Неметаллические включения, имеющие модуль упругости больше, чем у стали (глинозем и его производные, нитриды титана и т.п.), напротив, не представляют опасности. Однако указанный вывод находится в противоречии с экспериментальным материалом, свидетельствующим о том, что наиболее опасными включениями, у которых возникали трещины усталости в высокопрочных сталях, являются глиноземистые включения, хотя в некоторых случаях отмечены факты появления трещин усталости в низко- и среднеуглеродистых сталях у пластичных включений сульфидов.
Указанное противоречие послужило основанием для появления другой, сравнительно новой, точки зрения, согласно которой основной причиной опасности неметаллических включений является возникновение очага зарождения усталостной трещины при охлаждении металла (при кристаллизации, термообработке, ковке и т. д.) вследствие различия в физических свойствах (прежде всего коэффициента термического расширения α и модуля упругости Е) матрицы и включения, остаточных термических напряжений, величина которых может в отдельных случаях превысить предел текучести металла и вызвать появление зоны предразрушения.
Поскольку наиболее опасные с точки зрения усталости включения (глинозем и его производные) обладают высокими значениями Е и имеют сравнительно малую величину α, в их окрестности возникают остаточные термические напряжения максимальной величины, что и обусловливает возникновение усталостного разрушения именно в районе этих включений.
Дальнейшие исследования показали, что если для высокопрочных сталей, в частности шарикоподшипниковой стали ШХ15, вторую точку зрения можно считать обоснованной, то для крупнозернистых пластичных сталей ее выводы ошибочны. Косвенные измерения величины остаточных термических напряжений в районе неметаллических включений показали, что на крупнозернистых сталях Х18Н9Т и 12Х1МФ уровень этих напряжений сравнительно невелик и поэтому они вряд ли могут стать решающим фактором, влияющим на зарождение усталостной трещины. В связи с этим нам представляется, что вопрос о главной причине опасности неметаллических включений при усталости металлов надо рассматривать в зависимости от химического состава металла, его структуры, уровня прочности и пластичности.
Что же касается высокопрочных, например мартенситных мелкозернистых металлов и сплавов с повышенной чувствительностью к хрупкости, то для них справедлив тезис о превалирующей роли остаточных термических напряжений. Наиболее опасными неметаллическими включениями для таких металлов являются частицы глинозема и его производных (алюминаты кальция, муллит, шпинели и т. п.). Меньшую опасность представляют сульфиды и другие пластичные включения.
Для мягких, пластичных, крупнозернистых металлов и сплавов основной причиной опасности неметаллических включений следует считать концентрацию напряжений при действии внешних нагрузок, поэтому для них наиболее опасны неметаллические включения сульфидов, пластичных силикатов и т. п. Следует учитывать и другие факторы, которые в этом чисто качественном анализе не рассматривались. В частности, наиболее существенным фактором, влияющим на выносливость металлов, следует считать размер включений. Несмотря на то что четких рекомендаций относительно так называемого критического размера включения до сих пор нет (по различным данным от 3 до 35 мкм), ясно, что уменьшение размеров включений, их раздробление (диспергирование), происходящее в результате рафинирования, в том числе и ЭШП, играют определяющую роль в повышении выносливости рафинированного металла, так как у неметаллического включения малого размера и концентрация напряжений, и уровень остаточных термических напряжений значительно снижаются.
В связи с тем что в результате ЭШП происходит диспергирование крупных, особенно строчечных, включений следует ожидать, что выносливость электрошлакового металла будет более высокой, чем у металла обычных способов производства. Действительно, уже первые испытания на усталость стали ШХ15, подвергнутой ЭШП, подтвердили эти предположения. Начиная с середины 60-х годов такие испытания становятся уже массовыми и им подвергаются электрошлаковые стали почти всех марок, предназначенные для внедрения в различные отрасли народного хозяйства. Результаты этих испытаний однозначно свидетельствовали о больших преимуществах ЭШП. Тем не менее до последнего времени встречаются работы, где либо говорится об отсутствии влияния на предел выносливости неметаллических включений, либо ставится под сомнение необходимость рафинирования металла, поскольку его более высокая стоимость якобы не компенсируется соответствующим увеличением комплекса механических свойств. В других работах утверждается, что рафинирование целесообразно проводить лишь в двух случаях — для высокопрочной стали (σв>140 кгс/мм2) в массивных сечениях и для сталей высокой и средней прочности в тонких сечениях (лента, проволока и т. п.)
В связи с существованием таких, по нашему мнению, ошибочных взглядов, основанных на односторонней или неполной информации, возникает необходимость рассмотреть более подробно вопрос о влиянии различных сопутствующих факторов на выносливость исходной и электрошлаковой стали.
Что касается многоцикловой (обычной) усталости, то преимущество металла ЭШП по пределу выносливости перед металлом обычных методов производства обычно составляет несколько процентов и зависит от влияния различных факторов (уровень прочности и пластичности металла, направление силового потока относительно оси детали, наличие надреза и т. д.). В общем случае предел выносливости стали после ЭШП тем больше, чем выше уровень прочности стали и чем больше прирост пластичности в результате ЭШП. При наличии острого надреза преимущество стали ЭШП в выносливости уменьшается.
Особо следует упомянуть о влиянии величины напряжений (деформаций) на выносливость загрязненных и рафинированных сталей. Здесь следует четко разграничить два различных показателя: предел выносливости и циклическую долговечность.
При многоцикловой усталости металлов критерием сопротивления усталости является предел выносливости, определяемый по ГОСТ 23026—78 при изгибе с вращением цилиндрического образца диаметром 6—8 мм. В этом случае различие между рафинированным и исходным металлом существенно зависит от прочности стали и колеблется от 20—30% (для высокопрочных сталей, например ШХ15) до 2—5% (для низкоуглеродистых пластичных сталей), что, видимо, и явилось основанием для утверждения о сравнительно незначительном влиянии рафинирования на выносливость конструкционных сталей.
Однако нельзя забывать, что предел выносливости — это в некоторой степени усредненная критическая величина напряжения, ниже которой не развиваются трещины усталости. Эта величина самым существенным образом зависит от параметров приповерхностного слоя образца (шероховатости поверхности, наклепа, величины и знака остаточных напряжений и т.д.), которые, естественно, нивелируют влияние загрязненности металла.
Если попытаться сравнить показатели тех же образцов, но в области ограниченной выносливости (при напряжении выше предела выносливости сравниваемых металлов), т. е. сопоставить их циклическую долговечность, картина существенно меняется. При различии в пределах усталости 2—2,5 кгс/мм2 (что типично, например, для стали 20 и аналогичных пластичных сталей) циклическая долговечность рафинированных металлов выше, чем исходных, в 2—3 раза, а у высокопрочных сталей это отличие нередко достигает одного-двух порядков. Поэтому при анализе свойств обычного металла и ЭШП использование показателя предела выносливости, по нашему мнению, недостаточно для объективного и разностороннего сравнения их характеристик, особенно в условиях, приближенных к эксплуатационным. Это давно поняли специалисты тех отраслей промышленности, где особенно высоки требования к качеству металла, в частности авиационной, судостроительной, подшипниковой и т.п. Например, при испытании подшипниковой стали на контактную усталость можно, конечно, определять предел выносливости. Однако во всех технически развитых странах, которые производят подшипниковые стали, испытания этих сталей проводятся в области ограниченной выносливости, т. е. при напряжениях, превышающих предел выносливости.
При более высоком уровне напряжений намного эффективнее, чем при низких напряжениях, проявляется влияние неметаллических включений и кристаллизационных дефектов, т. е. факторов металлургической наследственности. Таким образом, наличие высоких напряжений способствует более четкому выявлению роли неметаллических включений в процессе усталостного разрушения металлов и, как следствие, более объективному сравнению показателей выносливости рафинированных и исходных металлов. Вероятно, именно этим можно объяснить широко известный факт, что максимальное влияние неметаллические включения оказывают именно при контактной усталости, где уровень напряжений (400—600 кгс/мм2) во много раз выше, чем при многоцикловой усталости, и значительно превышает предел контактной выносливости стали ШХ15. По той же причине различия во влиянии разных способов производства и рафинирования на выносливость металлов значительно лучше выявляются при их испытании не на многоцикловую, а на малоцикловую усталость, т. е. при низкочастотном упруго-пластическом циклическом деформировании.
Имеется еще одно немаловажное обстоятельство, на которое надо обращать внимание, когда обсуждаются вопросы влияния неметаллических включений (или рафинирования) на выносливость металлов. Анализ исследований последних лет свидетельствует о том, что влияние включений в значительной степени зависит от вида напряжений — нормальных или касательных.
Казалось бы, испытания при растяжении, где в напряженном состоянии оказывается весь объем, все сечение металла, а не только поверхностный слой (как при изгибе или кручении), должны быть в этом случае самыми эффективными, однако опыты показали противоположные результаты: при нормальных напряжениях влияние неметаллических включений оказалось несущественным. В то же время испытания металлов на усталость при изгибе или кручении, особенно при высоких уровнях деформаций, дают достаточно объективные (в сравнительном и абсолютном аспектах) данные, которые являются достоверным показателем влияния неметаллических включений на выносливость конструкционных сталей.
Анализ многочисленных фрактограмм разрушения исходной (электродуговой) и электрошлаковой стали показал, что в металле ЭШП микропластическая деформация распределена более равномерно. Отсутствие в металле ЭШП грубых, особенно строчечных, включений, локализующих пластическую деформацию в сравнительно малом объеме и вызывающих поэтому более раннее разрушение, обеспечивает высокий уровень выносливости электрошлаковой стали.
Таким образом, сравнивать металл ЭШП с исходным загрязненным следует при довольно высоком уровне деформаций, т. е. при контактной и малоцикловой усталости. Однако и здесь различие в выносливости рафинированного и загрязненного металлов зависит от различных факторов. Например, при малоцикловой усталости (рисунок 1) повышение содержания углерода, приводящее к росту прочности хромистых и хромоникелемолибденовых сталей, в большинстве случаев увеличивает преимущества стали, рафинированной ЭШП. Наибольшее преимущество ЭШП наблюдается на высокопрочных сталях, это объясняется тем, что в результате ЭШП повышаются пластичность и вязкость металла (это не всегда выявляется стандартными испытаниями на растяжение), что в свою очередь значительно увеличивает способность стали длительное время сопротивляться повторным нагрузкам.
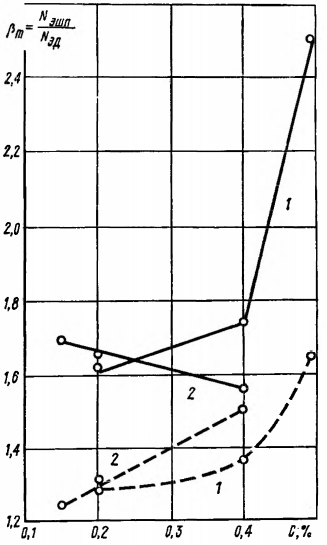
Отметим еще один характерный момент. Электрошлаковый металл характеризуется весьма высокой живучестью при усталости, т. е. большой длительностью периода распространения усталостной трещины. Это качество металла имеет исключительно важное значение для тех случаев, когда уровень действующих напряжений в изделии достаточно высок, срок его службы ограничен, а возможность срочной замены исключена.
В загрязненной исходной стали энергия деформации сосредоточивается главным образом у структурных дефектов (в основном у неметаллических включений), поэтому по сечению детали энергия распределяется неравномерно, для такой стали характерны большие колебания величины поглощаемой энергии, косвенно оцениваемой по площади петли гистерезиса (рисунок 2). Металл ЭШП, свободный от крупных включений, способен распределять энергию деформации значительно равномернее, площадь петли гистерезиса в этом случае изменяется всего лишь на 3—5% (а не на 30%, как у исходного металла), что позволило электрошлаковой стали, несмотря на весьма высокий уровень напряжений и наличие трещины усталости уже после 50-го цикла, выдержать более 2000 циклов повторных нагрузок (исходная сталь выдержала лишь 500 циклов).
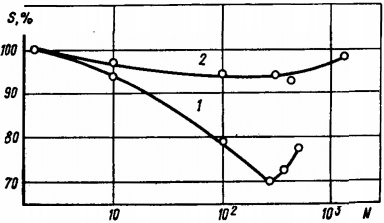
Выше подробно освещен вопрос об эффективности десульфурации металла при ЭШП. Для низко- и среднеуглеродистых (особенно сваривающихся) сталей удаление серы из металла исключительно важно и благоприятно отражается почти на всех свойствах стали, в том числе и на выносливости. Однако удаление серы не всегда является необходимым. В некоторых случаях максимальная десульфурация вообще не нужна, а при переплаве шарикоподшипниковой стали, имеющей включения специфических оксисульфидов небольшого размера и повышенное содержание серы, иногда вовсе нет необходимости в десульфурации металла.
Технологическая маневренность и гибкость ЭШП и его преимущество перед всеми существующими рафинирующими методами заключаются именно в том, что, изменив тип флюса, можно, существенно изменяя загрязненность переплавляемого металла, повысить его свойства, в частности выносливость. В справедливости этого можно убедиться, проанализировав результаты исследований выносливости шарикоподшипниковой стали исходной выплавки и после ЭШП (рисунок 3). Несмотря на то что в исходной стали было очень много серы (93% включений —сульфиды, 6% — оксиды, содержание кислорода 0,008%), ее выносливость достаточно высока. ЭШП на глиноземистых флюсах (4, 5) вследствие повышения загрязненности оксидами вызвал снижение выносливости, а электрошлаковый переплав на безглиноземистых флюсах снизил количество оксидов (и содержание кислорода), что сразу же обусловило повышение выносливости стали.
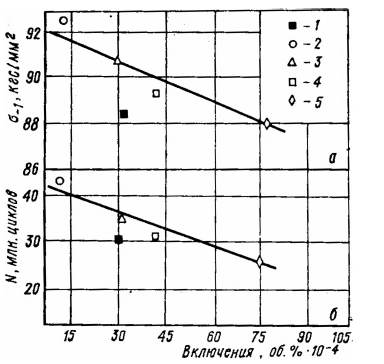
Одним из наиболее жестких современных требований, предъявляемых к качественным конструкционным материалам, в частности к сталям, является требование минимальной анизотропии механических свойств, в том числе и выносливости. Несмотря на то что детали машин могут быть изготовлены из заготовок, вырезанных вдоль (продольные образцы), поперек (поперечные образцы) и перпендикулярно (вертикальные или толщинные образцы) оси прокатки металла, все они должны удовлетворять определенным техническим условиям по прочности, пластичности, выносливости и другим показателям. Особенно высокими являются сейчас требования к изотропности корпусных материалов, так как в реальной конструкции корпуса технологические и иные нагрузки могут быть направлены по всем трем осям листа.
Необходимо отметить, что обычные методы производства конструкционных сталей не могли удовлетворить возросшие требования к уменьшению анизотропии. Это объясняется тем, что для сталей обычных методов производства к анизотропии, вызванной различным направлением прокатанных волокон металла относительно действия внешней нагрузки, добавляется анизотропия от различной ориентации строчечных неметаллических включений.
Такие неметаллические включения (сульфиды, пластичные силикаты и особенно оксиды), дробящиеся или вытягивающиеся при прокатке металла, в случае действия внешних нагрузок поперек направления ориентации включений существенно нарушают сплошность металла. Они вызывают преждевременное его разрушение либо при значительно меньших напряжениях (при обычной усталости), либо при значительно меньшем числе циклов переменных нагружений (при малоцикловой усталости), чем в случае, когда нагрузки направлены вдоль направления ориентации включений.
Рафинирование металла методом ЭШП, приводящее к большому снижению загрязненности металла, прежде всего уменьшает количество крупных включений, исчезают или значительно диспергируются строчечные включения. Именно этот фактор способствует значительному снижению анизотропии выносливости электрошлакового металла, так как остающиеся в стали точечные включения практически индифферентны к направлению действия внешних нагрузок.
Как видно из рисунка 4, предел выносливости продольных образцов стали 25Х2ГНТРА электродуговой выплавки и рафинированной ЭШП различаются не очень существенно (примерно на 7%).
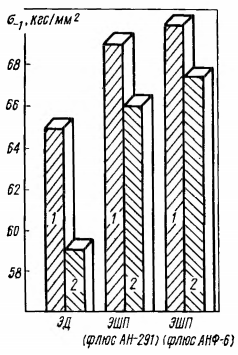
В то же время предел выносливости поперечных образцов стали ЭШП намного превышает аналогичный показатель нерафинированной, анизотропной стали. Еще более значительным оказывается анизотропия малоцикловой долговечности листовых сталей (рисунок 5).
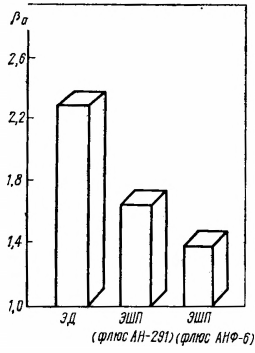
Особо следует остановиться на мартеновской стали 16ГНМА, анизотропия долговечности которой достигает 500% (рисунок 6). Использование ЭШП позволяет не только существенно повысить уровень выносливости, но и резко (более чем в 3 раза) уменьшить степень анизотропии такого важного механического свойства, как долговечность.
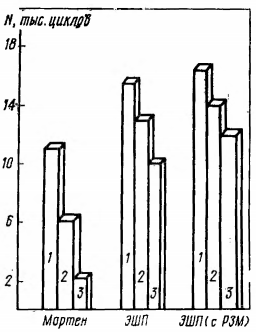
При этом, конечно, надо учесть, что уменьшение анизотропии показателей выносливости зависит от ряда сопутствующих факторов, таких, как прочность стали и т. п. Обычно, чем выше прочность стали, тем сильнее анизотропия прочностных свойств. Соответственно ЭШП более прочной стали эффективнее повлияет на уменьшение анизотропии. Значительное повышение изотропности свойств, в частности выносливости металла, является громадным преимуществом ЭШП.
Как известно, предел выносливости малых образцов и деталей выше, чем у образцов и деталей большого размера. Это снижение прочности у последних названо масштабным эффектом, а причина снижения прочности вследствие увеличения размеров — масштабным фактором.
Для объяснения природы масштабного эффекта выдвинуты различные теории, в том числе статистические, согласно которым в силу того, что в реальных поликристаллических телах всегда имеется большое количество неоднородностей и дефектов, представляющих собой потенциальные очаги разрушения, вероятность наличия таких дефектов на поверхности образца малого диаметра меньше, чем на поверхности образца большого диаметра.
Это и обусловливает меньшую циклическую прочность последнего. Поскольку неметаллические включения являются именно такими дефектами, которые вызывают усталостное разрушение, их наличие или отсутствие, по всей вероятности, может отразиться на масштабном эффекте. Несмотря на то что этот вопрос представляет собой значительный интерес, влияние рафинирования стали на проявление масштабного эффекта совершенно не изучено ни в теоретическом, ни в практическом аспектах. В статистических теориях возможность такой постановки вопроса даже не рассматривается.
Испытания мартеновской и электрошлаковой стали типа 12ХНЗА показали (рисунок 7), что масштабный эффект проявляется по-разному у загрязненной и рафинированной стали. Так, если различие в пределах выносливости мартеновской и электрошлаковой стали типа 12ХНЗА на образцах диаметром рабочей части 5мм было всего 2 кгс/мм2, то на образцах диаметром 25мм оно составляло уже 6 кгс/мм2. Это значительное (в 3 раза) различие с увеличением диаметра образца в пределах выносливости исходной и электрошлаковой стали свидетельствует о том, что электрошлаковое рафинирование стали ослабляет масштабный эффект.
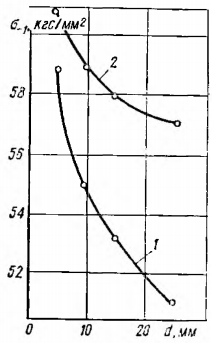
Приведенные результаты свидетельствуют о том, что указанное явление нужно учитывать, когда решается вопрос о конкретном применении ЭШП для производства стали, идущей на крупногабаритные изделия. В данном случае не рекомендуется проверять выносливость на образцах малых диаметров (даже стандартных), поскольку результаты таких испытаний приведут к искаженной информации, нивелирующей свойства разных по загрязненности сталей и вуалирующей истинную эффективность применения стали, рафинированной ЭШП.
Представляется важным еще один вывод: ЭШП оказывается особенно эффективным (по критерию выносливости) для тех случаев, когда переплавляемая сталь предназначается для изделий большого сечения.
От плавильной печи до готового изделия металл проходит очень длинный путь, в течение которого его свойства не остаются постоянными. Поэтому, получив металл высокого качества, следует к нему относиться бережно. Во многих отраслях народного хозяйства применение рафинированного металла стало уже массовым, однако рекомендаций о том, как его обрабатывать, нет.
В связи с этим были проведены исследования, ставившие задачу изучить совместное влияние дефектов металлургического (неметаллических включений) и технологического (различное состояние приповерхностных слоев) происхождения на контактную выносливость стали. В качестве объекта исследований выбрали шарикоподшипниковую сталь ШХ15, контактная выносливость которой очень чувствительна к наличию указанных дефектов. Вариации количества неметаллических включений обеспечивали применением металла различных способов производства и рафинирования, а критерием загрязненности служил объемный процент содержания хрупких неметаллических включений (оксидов и нитридов).
Применением различных режимов шлифования и шлифовальных кругов достигали определенных различий в состоянии приповерхностных слоев, которое оценивали градиентом микротвердости ΔНμ — разностью между стабильным значением микротвердости металла и минимальным ее значением (рисунок 8). Режим А — шлифовка электрокорундовым кругом, твердость СТ, поперечная подача 0,03 мм/дв хода (ΔНμ=180кгс/мм2); режим Б — то же,что и режим А, но подача 0,02 мм/дв. хода (ΔНμ=150кгс/мм2); режим В — твердость круга СМ 1, подача 0,015 мм/дв. хода (ΔНμ=75кгс/мм2); режим Г — то же, что и режим В, но круг алмазный (ΔНμ=30 кгс/мм2). После шлифования все образцы полировали алмазными пастами. Испытания на контактную выносливость проводились на машинах МКВ-К в стандартной («Индустриальное-50») смазке. Результаты испытаний обрабатывали методом математической статистики.
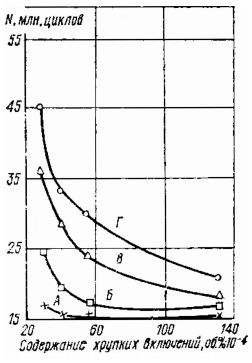
Как следует из рисунка 8, контактная выносливость стали ШХ15 существенно зависит от степени загрязненности металла и от выбранных режимов обработки. Различие в выносливости самой чистой и самой загрязненной стали в значительной степени зависит от механической обработки изделия.Если при самой грубой обработке это различие составляло всего 40%, то при самом мягком режиме различие составляет 165%, то есть возрастает в 4 раза. Интересно, что стали, очень заметно отличающиеся по загрязненности, будучи обработанными по грубому режиму (а он не очень отличается от типового заводского), практически нивелировали свою контактную выносливость. Другими словами, преимущество высококачественных рафинированных сталей перед исходными после такой обработки исчезает. Напротив, обработка на мягких режимах увеличивает это преимущество.
Результаты опыта свидетельствуют о необходимости учета факторов механической обработки (или так называемой технологической наследственности). Если будет обеспечена качественная обработка (т. е. ее режимы не будут грубыми, жесткими), рафинированный металл, безусловно, оправдает свое назначение и компенсирует затраченный на него труд. В противном случае незачем, видимо, применять дефицитный и дорогой металл.
Повышение выносливости электрошлаковых сталей объясняется, как правило, уменьшением количества и размеров неметаллических включений, улучшением макро- и микроструктуры слитка и увеличением плотности металла. Вместе с тем при тщательных и всесторонних исследованиях выявляется ряд фактов, объяснить которые с помощью указанных причин не представляется возможным. Обращает на себя внимание непропорционально высокое увеличение выносливости электрошлакового металла. В связи с этим интересный материал для сравнения дают результаты испытаний исходных и рафинированных сталей ЗОХГСНА, ВКС-1 и ЭИ643 на обычную и малоцикловую выносливость.
Известно, что величина пределов выносливости конструкционных сталей коррелирует с произведением σвψ. Как видно из рисунка 9, эта зависимость действительно имеет место для сталей открытой выплавки, ВДП и ЭЛП. Электрошлаковая сталь такой закономерности не подчиняется.
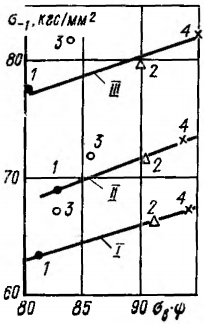
Если сопоставить долговечность стали при малоцикловой выносливости с показателем
то можно наблюдать картину, почти аналогичную предыдущей (рисунок 10): показатели металла открытой плавки, ВДП и ЭЛП (по каждой марке стали в отдельности) свидетельствуют о достаточно хорошей корреляции сравниваемых величин, а на электрошлаковый металл эта закономерность не распространяется.
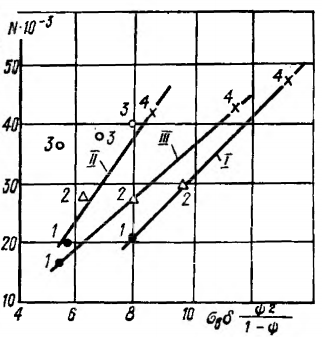
Надо полагать, что металл ЭШП обладает каким-то специфическим свойством,которого не имеют остальные сравниваемые стали и которое в достаточной степени не отражают показатели
и σвψ. Это свойство благоприятно влияет на выносливость высокопрочных конструкционных сталей. Объяснить это явление, по-видимому, можно наличием мельчайших неметаллических включений, возникающих при кристаллизации слитка при ЭШП, и вызываемым ими эффектом упрочнения. Наиболее типичными неметаллическими включениями в электрошлаковых сталях следует считать мелкодисперсные включения оксидов и нитридов; именно они обусловливают эффект упрочнения стали, который не отражается на показателях статической прочности металла ЭШП.
Как было показано выше, в результате существенных отличий физических свойств металлической матрицы и неметаллических включений в металле возникают остаточные термические напряжения. В окрестности сравнительно крупных включений глинозема, муллита и других, обладающих высокими значениями Е и малыми значения α, эти остаточные напряжения зачастую превышают предел текучести металла, происходит его локальная пластическая деформация, что вызывает появление зон предразрушения, т. е. потенциальных очагов разрушения металла. Однако в том случае, когда включение весьма мало, возникающие в металле остаточные напряжения, как правило, не превышают предела текучести металла и зоны предразрушения не появляются, несмотря на то, что напряженность металла сохраняется.
Громадное количество таких мелкодисперсных включений и их равномерное распределение в матрице способствуют созданию более или менее однородного напряженного состояния в электрошлаковой стали, т. е. сталь ЭШП оказывается как бы внутренне упрочненной. Упрочненный электрошлаковый металл может поглощать больше водорода, его электродный потенциал более отрицателен, а коррозионная стойкость может оказаться ниже, чем у неупрочненного металла. Возможны также некоторые другие отрицательные эффекты упрочнения (например, увеличение водородной проницаемости, снижение гелиевой плотности и т. д.). Однако положительное влияние мелкодисперсных неметаллических включений в электрошлаковой стали и вызываемого ими упрочнения вполне компенсируют эти недостатки. Во-первых, в результате упрочнения конструкционные стали ЭШП по своей выносливости превосходят не только металл обычной выплавки, но и стали других рафинирующих технологий. Это преимущество сохраняется и зачастую становится решающим фактором при эксплуатации сталей в рабочих средах (адсорбционных, коррозионных, наводороживающих и др.). Во-вторых, упрочненная структура электрошлаковой стали более изотропна, т. е. менее чувствительна к анизотропии механических свойств (особенно выносливости), зависящей от направления действия сил относительно направления прокатки. По изотропности электрошлаковая сталь превосходит металл всех других способов выплавки. В-третьих, упрочнение способствует существенному повышению стабильности механических свойств (особенно выносливости) металла электрошлаковых конструкционных сталей.
Наличие упрочненной структуры металла в окрестности мелкодисперсных неметаллических включений является специфическим признаком электрошлаковой конструкционной стали и обусловливает ее существенное преимущество перед сталями других способов производства и рафинирования по ряду свойств.
Итак, ЭШП повышает выносливость металлов и сплавов. Факторами, увеличивающими преимущество в выносливости металла ЭШП перед обычным, являются: повышение прочности, более мелкозернистая структура, увеличение размера детали, мягкие режимы механической обработки деталей, высокий уровень напряжений. Снижают преимущество электрошлакового металла перед обычным следующие факторы: более низкая прочность вследствие соответствующей термообработки, крупнозернистая, грубая структура, наличие надреза (концентратора напряжений), малые размеры детали, грубая механическая обработка деталей, низкий уровень напряжений.
Понимание причин различного качественного воздействия указанных факторов представляется весьма важным для уяснения влияния ЭШП на комплекс служебных свойств самых разнообразных металлов и сплавов.
Сортамент электрошлакового металла
Из металла ЭШП производят практически все виды проката, поковок, штамповок, прессовок, которые выпускают и из металла обычных методов выплавки. Существенное различие между этими видами продукции состоит прежде всего в более высоком и, что особенно важно, стабильном качестве переплавленного металла. У металла ЭШП есть еще одно важное преимущество — более высокий выход годного, более высокая технологичность при горячей и холодной деформации.
Плотная макроструктура слитка ЭШП, отсутствие дефектов ликвационного и усадочного происхождения, всевозможных пустот, рыхлот и, наконец, прекрасная гладкая поверхность, не требующая перед дальнейшим переделом никакой обработки или зачистки, предопределили существенное изменение геометрии самого слитка. Слиток ЭШП имеет правильную геометрическую форму без так называемой кюмпельной или хвостовой и головной частей. Если слиток выплавляется в стационарном кристаллизаторе, он, как правило, имеет некоторую конусность, необходимую для облегчения операции раздевания (рисунок 1, а). Если же переплав осуществляется при относительном перемещении кристаллизатора и слитка, последний, конусности не имеет (рисунок 1, б).
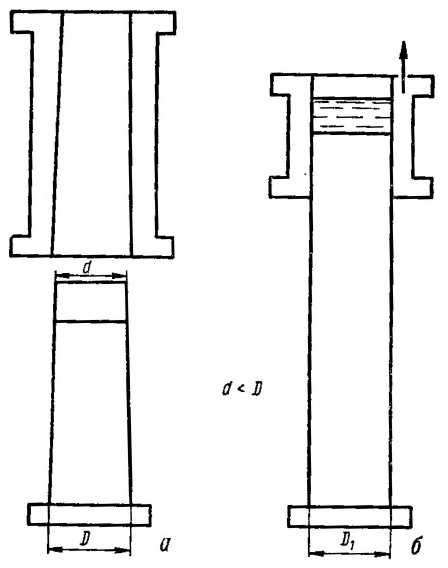
перемещении кристаллизатора и слитка (б).
Исторически сложилось так, что на первом этапе освоения ЭШП в конце 50-х гг. передельные слитки для сортового проката имели только круглое сечение. Это обстоятельство можно объяснить, во-первых, относительной простотой изготовления кристаллизаторов из готовых медных труб (в то время наша промышленность уже выпускала медные прессованные трубы диаметром до 425 мм) и, во-вторых, наличием некоторого опыта прокатки слитков ВДП, имевших только круглое сечение.
Из слитков ЭШП диаметром от 150 до 425 мм прокатывали прутки круглого сечения для последующего изготовления тел качения шариковых и роликовых подшипников, квадрат, полосу, трубную заготовку для последующей прошивки или прессования.
Известно, однако, что основным типом передельного слитка, идущего на обжимные и сортопрокатные станы, является слиток квадратного сечения. Поэтому по мере развития мощностей по ЭШП и увеличения развеса слитка был осуществлен переход от круглого сечения к квадратному (естественно, при этом пришлось перейти к кристаллизаторам сварной конструкции).
По условиям прокатного производства максимальное сечение слитка, обжимаемого на блюминге, не превышает 800 х 800 мм, а масса — 8—10 т. Поэтому и передельные слитки ЭШП сортового сортамента имеют массу и сечение не выше указанных. Наиболее распространен слиток ЭШП квадратным сечением от 400 до 600—650 мм. Имея такие слитки ЭШП, можно изготовить практически любой сортамент, любой профиль, получаемый из металла открытой выплавки.
Передельные слитки ЭШП круглого сечения, идущие на прокатку, составляют теперь лишь небольшую часть общего производства металла ЭШП. Они, как и раньше, чаще всего используются в трубном производстве.
Отдельную группу составляют слитки круглого сечения, имеющие полость. Такие полые слитки большей частью идут на последующий горячий передел, например на раскатку, раздачу, прессование, протяжку. Иногда их подвергают и различным видам холодной деформации. Однако все большее значение приобретает производство из металла ЭШП полых слитков круглого сечения, используемых в литом виде, т. е. без всякой деформации. По существу это уже не слитки, а трубы, подлежащие лишь некоторому технологическому переделу (зачистке, термической обработке, неразрушающему контролю, торцовке и т. д.). Сортамент таких слитков-труб достаточно широк — наружный диаметр изменяется от нескольких десятков до нескольких сотен миллиметров, а внутренний диаметр назначается таким, чтобы в зависимости от требований толщина стенки составляла, например, 15—20 мм, но могла бы достигать и сотни миллиметров.
Не обязательно, чтобы полость такой трубы была круглой и коаксиальной. В зависимости от назначения труб, меняя соответствующим образом оснастку, можно получать слитки-трубы с любой фасонной полостью.
Строго говоря, нет никаких принципиальных трудностей в производстве методом ЭШП слитков-труб практически любого сортамента и любого диаметра. Такому виду слитков ЭШП, несомненно, принадлежит большое будущее.
В нашей стране впервые в мировой практике было организовано крупномасштабное производство горяче- и холоднокатаного листа из металла ЭШП. Сначала для этих целей использовали слитки квадратного и даже круглого сечения, так как еще не умели выплавлять слитки прямоугольного сечения (как известно, при ВДП и теперь не удается получать слитки прямоугольной формы).
С появлением бифилярных многоэлектродных печей ЭШП в 1966—1967гг. задача производства листовых слитков ЭШП любой массы и сечения была успешно решена.
Как известно, толщина листового слитка обычно не превышает 800 мм, что определяется конструкцией всех современных обжимных станов, высота листового слитка достигает 4—4,5м, а ширина — 2,5—3м. Самый крупный в мире листовой слиток ЭШП весит более 40 т и имеет при толщине 500 мм, ширине 2500 мм высоту более 4м. Из такого слитка прокатывают листы толщиной до 280 мм. Эти размеры и масса листового слитка ЭШП отнюдь не предельны.
Выше отмечалось, что металл ЭШП и в литом виде достаточно плотен и практически не нуждается в деформации. По этой причине нет необходимости подвергать большим обжатиям листовые слитки ЭШП. В случае передела слитков ЭШП следует разграничивать понятия «деформация» и «формоизменение». Главной задачей при переделе электрошлаковых слитков является придание металлу необходимых геометрических размеров и формы, а не обжатие его для повышения плотности и обеспечения заданных механических свойств. Именно поэтому в случае ЭШП нет необходимости стремиться к получению слитков большой толщины.
Наоборот, толщина листового слитка может быть минимальной, наиболее близкой к толщине будущего листа. Так, например, при прокатке на лист толщиной 70—80 мм достаточно иметь слиток толщиной 150 мм. Это фактически уже не листовой слиток, а слиток-сляб и прокатывать его нужно только на листовом стане, минуя слябинг или другой обжимный стан.
Для повышения производительности печей ЭШП (как известно, этот показатель прямо пропорционален сечению слитка) слитки-слябы производят по двухручьевой схеме. Здесь имеется прямая аналогия между непрерывным литьем и ЭШП: чем меньше сечение отливаемой заготовки, тем больше должно быть число ручьев для обеспечения требуемой производительности агрегата.
Идея многоручьевого ЭШП полностью оправдала себя и в производстве сортовых слитков малого сечения, например 150 х 150 мм. В этом случае используют четырехручьевые печи ЭШП. Действительно, нецелесообразно выплавлять слитки крупного сечения и пропускать их через блюминг или заготовочныйстан, если можно пустить слиток ЭШП малого сечения непосредственно в сортопрокатный стан.
Значительный непрерывно возрастающий удельный вес в производстве металла ЭШП занимают кузнечные слитки. Первый кузнечный слиток диаметром 500 мм и массой до 2т получен на Ново-Краматорском машиностроительном заводе (НКМЗ) в Донбассе еще в 1958 г. Очень скоро выявилась замечательная особенность электрошлаковых кузнечных слитков: способность подвергаться прямой осадке, минуя предварительную вытяжку. Именно так стали изготавливать первые поковки из жаропрочных хромистых сталей для дисков компрессора газотурбинного двигателя.
С развитием ЭШП в тяжелом и энергетическом машиностроении непрерывно возрастала и масса кузнечного слитка. Первый в мире 10-тонный слиток ЭШП диаметром 1100 мм и высотой примерно 1,5 м был получен на НКМЗ уже в 1961г. Затем диаметр слитка был увеличен последовательно до 1300, 1500 и 1700мм, а масса — соответственно до 17, 30 и 40 т. При диаметре 1800—2300 мм масса кузнечного слитка ЭШП достигла 100—160 т; на очереди слиток массой до 200т.
Типичная для кузнечных слитков ЭШП форма правильного цилиндра или усеченного конуса (с весьма небольшой конусностью) уступила место многогранной форме. Выход годного благодаря малой донной и головной обрези электрошлакового кузнечного слитка примерно вдвое выше, чем при переделе обычного кузнечного слитка. Это очень важно, поскольку слиток ЭШП массой 150—200т может быть использован для получения заготовки, требующей наличия слитка обычного производства массой соответственно не менее 300—450т. Если учесть значительно более высокое качество металла ЭШП по сравнению с металлом обычной выплавки, то станет ясно, почему во всем мире придается самое серьезное значение созданию мощностей по производству сверхкрупных кузнечных слитков ЭШП. Такие слитки совершенно необходимы для изготовления заготовок валов роторов сверхмощных альтернаторов, роторов паровых турбин тепловых и атомных электростанций, опорных валков уникальных толстолистовых прокатных станов с длиной точки более 5 м, валков листосгибочных машин и т. д.
Вместе с тем можно и нужно идти не только по пути получения моноблочных заготовок, но и использовать современные достижения сварочной техники, т. е. ориентироваться на укрупнение заготовок за счет электрошлаковой сварки между собой слитков ЭШП или поковок из нихотносительно меньшей массы, например до 100—150 т.
Итак, современный сортамент металла ЭШП практически охватывает все известные нынешней технике виды проката и поковок, все виды и классы сталей, начиная от ферритных и кончая аустенитными. В первые годы ЭШП подвергали преимущественно дорогие высоколегированные стали и сплавы, а также шарикоподшипниковые стали. Удельный вес последних и теперь достаточно велик. Однако с каждым годом все большее и большее значение приобретает ЭШП дешевых низколегированных конструкционных сталей, преимущественно в виде горячекатаного листа для крупногабаритных сварных конструкций. В настоящее время количество марок сталей ЭШП измеряется многими сотнями. Несмотря на серьезную конкуренцию со стороны других переплавных процессов, достаточно велик сортамент электрошлаковых жаропрочных сталей и сверхсплавов. Непрерывно растет сортамент штамповых и инструментальных сталей ЭШП. Неоспоримы преимущества ЭШП при переплаве ряда сплавов на медной основе, например высокопрочных бронз. Есть основания считать, что потенциальные возможности ЭШП еще далеко не раскрыты и тем более не исчерпаны в применении к высокореакционным и тугоплавким металлам (в США, например, успешно подвергают ЭШП уран, цирконий, молибден, вольфрам).
Уже сегодня объемы производства металла ЭШП измеряются многими сотнями тысяч тонн. К концу нашего столетия это будут уже миллионы тонн. В зависимости от потребностей народного хозяйства страны будет расширяться и сортамент электрошлакового металла.
Механические свойства электрошлакового металла
Общим показателем, отражающим все благоприятные изменения в чистоте, структуре, плотности и в других физических параметрах металла ЭШП, являются механические свойства стали, в частности прочность, пластичность, вязкость, сопротивление хрупкому и усталостному разрушению.
Хотя в работе утверждается, что чистота стали практически не влияет на ее прочность и пластичность, уже первые публикации по ЭШП констатировали высокое качество, в том числе и прочность, переплавляемого металла.
Прочность металла — весьма интегральный показатель, характеризующий усредненную способность металла сопротивляться деформации. Сравнивая прочность загрязненного и рафинированного металла, нельзя забывать, что на прочность оказывают влияние много факторов. Поскольку прочность характеризует прежде всего величину межатомных связей, то с этой точки зрения влияние рафинирования, обеспечивающее более упорядоченные атомные связи, безусловно, благоприятно. Например, по данным работы, модуль нормальной упругости стали ЭИ736 у переплавленного металла на 12% выше, чем у исходного.
Удаление неметаллических включений в результате рафинирования мягких пластичных металлов, например низкоуглеродистых сталей, армко-железа и т. п., может иногда привести не к увеличению, а к некоторому снижению предела прочности и предела текучести металла. Для высокопрочных металлов и сплавов результаты ЭШП однозначны — повсеместно фиксируется повышение прочностных характеристик, особенно на образцах, вырезанных поперек направления проката или по толщине.
Очень показательными в этой связи являются результаты сравнительных испытаний толстолистовых (50х110х300 мм) образцов с надрезом мартеновской и электрошлаковой стали 18Х2М. Если образцы мартеновской стали после нормализации с отпуском разрушились при усилии 48 тс, а после закалки с отпуском— при усилии 120 тс, то образцы стали ЭШП разрушились при усилиях соответственно 75 и 180 тс.
Особенно проявляется преимущество в прочности металла ЭШП при действии высоких температур (т. е. в жаропрочности и длительной прочности). Так, например, если долговечность при температуре 650° С и напряжении 38 кгс/мм2 продольных и поперечных образцов исходной электродуговой стали ЭИ481 составила соответственно 54 и 23, то у стали ЭШП долговечность составила соответственно 171 и 136 ч. Особенно характерными являются показатели испытаний поперечных образцов — долговечность металла ЭШП возрастает почти в 6 раз.
Очень велико влияние ЭШП на пластические свойства металлов. Удаление и особенно диспергирование крупных включений в результате ЭШП существенно повышает пластичность металла, в частности поперечное сужение ψ. Так, например, в работе отмечается, что ЭШП до 4 раз повысил показатель ψ хромистых и хромоникелемолибденовых сталей. Аналогичные данные приведены и в других публикациях. Определенную роль в повышении пластичности электрошлакового металла играет также повышение скорости кристаллизации слитка, обеспечивающее меньшую загрязненность междендритных участков, где и происходят преимущественное зарождение и развитие трещин.
Особенно заметно воздействие ЭШП на ударную вязкость — характеристику металла, наиболее чувствительную к особенностям строения и степени чистоты. Еще не найдено удовлетворительной корреляции величины ударной вязкости с различными эксплуатационными свойствами металлов и сплавов. Тем не менее для конструкционных сталей испытания на ударную вязкость представляют собой пока незаменимый сравнительно простой, экономичный, эффективный и достаточно надежный способ определения вязкостных свойств, характеристик отпускной хрупкости, показателей хладноломкости и степени сопротивления динамическим нагрузкам и хрупкому разрушению.
Ударная вязкость является не только одним из сертификатных показателей стали, ее величина до сих пор служит главным критерием оценки влияния различной технологии выплавки стали на ее свойства. Испытания на ударную вязкость остаются в арсенале исследователей и по сей день, а их результаты весьма убедительно свидетельствуют о достоинствах или недостатках различных факторов, воздействующих на сталь.
Уменьшение загрязненности стали неметаллическими включениями в результате ЭШП приводит к весьма существенному повышению ее ударной вязкости. Особенно здесь следует отметить роль удаления из металла серы и, как следствие, резкого уменьшения размера сульфидных строчек. Поскольку испытания на ударную вязкость проводятся на большом количестве образцов, результаты таких испытаний более наглядно показывать частотной характеристикой (рисунок 1), анализ которой неопровержимо свидетельствует о преимуществе стали ЭШП.
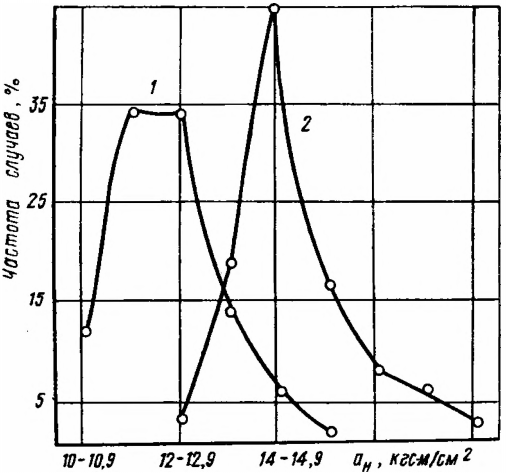
Повышая ударную вязкость стали, ЭШП оказывает положительное воздействие на ее сопротивление хрупкости при отрицательных температурах (рисунок 2).
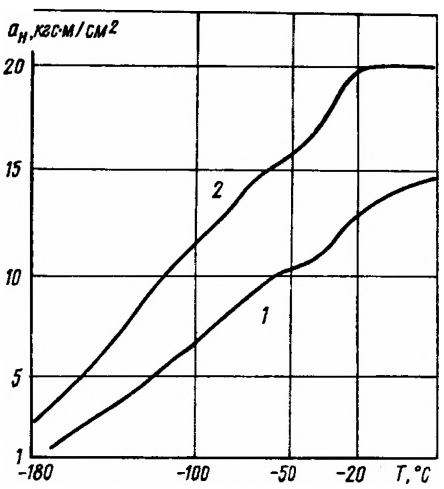
Так, ЭШП существенно снижает склонность стали к обратимой хрупкости (рисунок 3) и ослабляет склонность к необратимой хрупкости (рисунок 4).
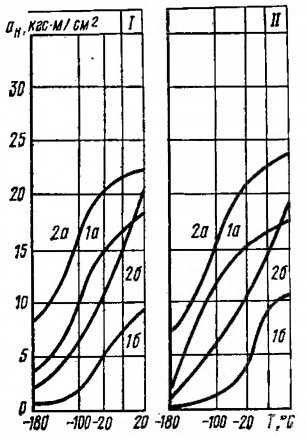
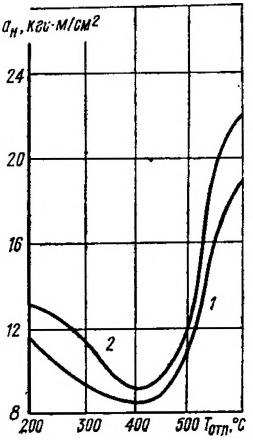
ЭШП не только повышает абсолютные значения ударной вязкости, но и существенно сдвигает в минусовую область критическую температуру хрупкости. Так, если для кислой мартеновской хромоникелемолибденовой дисковой стали эта температура была в диапазоне 35— 15°С, то для стали ЭШП она составила —35°С.
Некоторые исследования считают, что ЭШП повышает ударную вязкость стали только за счет увеличения работы развития трещины, т. е. повышения сопротивления вязкому разрушению. В то же время имеются данные, свидетельствующие о том, что ЭШП увеличивает работу зарождения трещины, т. е. сопротивление хрупкому разрушению.
Последние годы характерны быстрым развитием линейной механики разрушения материалов и, в частности, введением новых характеристик для оценки свойств металлов, по которым можно определить величину допустимого дефекта (длину трещины) и средний уровень допускаемых напряжений из условий предотвращения опасности хрупкого разрушения. Несмотря на то что методика таких испытаний не стандартизирована и многие ее положения все еще дискуссионны, определение коэффициентов интенсивности напряжений К1С и G1С получило широкое распространение.
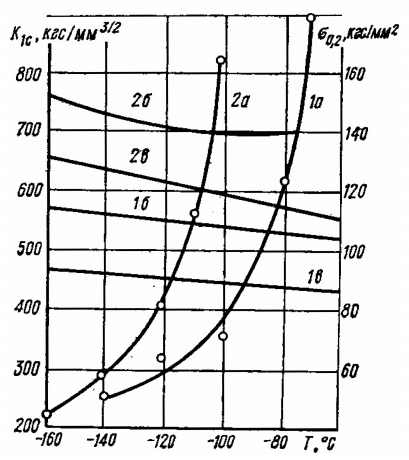
Исследуя сталь 25ХНЗМФА мартеновской выплавки и ЭШП, авторы работы определили критические коэффициенты интенсивности напряжений К1С, предварительно создав на образцах толщиной 100 мм для внецентренного растяжения усталостные трещины. Результаты этого исследования, обобщенные на рисунки 5, убедительно показывают, что металл ЭШП обладает значительно более высоким сопротивлением хрупкому разрушению, чем мартеновская сталь, причем критическая температура, соответствующая резкому снижению вязкости разрушения, у стали ЭШП на 30°С ниже, чем у мартеновского металла.
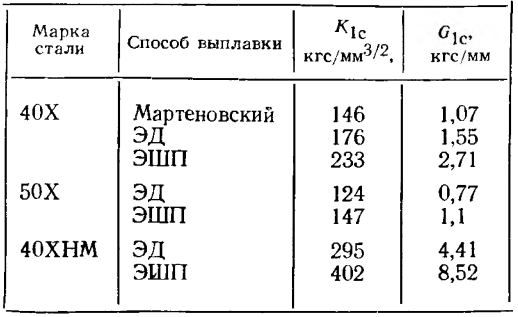
Аналогичные результаты, свидетельствуют (таблица 1) о значительном преимуществе металла ЭШП по характеристике вязкости разрушения перед металлом обычных методов производства. Следует отметить, что и в высокоотпущенном состоянии металл ЭШП также сохраняет свои преимущества: величина критического раскрытия трещины при —70° С у электрошлаковых сталей в 2,5— 10 раз больше, чем у электродугового металла. Если у образцов из стали ЭД развитая магистральная трещина появилась при запасе работы 2,4 кгс·м (испытания на ударный изгиб без доведения образца с усталостной трещиной до разрушения), то у образцов стали ЭШП при запасе работы 5 кгс·м появления магистральной трещины не наблюдается, происходит лишь раскрытие усталостной трещины.
Приведенные данные являются достаточным основанием для утверждения, что ЭШП способствует существенному увеличению энергоемкости стали в процессе деформации и разрушения при наличии концентрации напряжений (т.е. в условиях стесненной пластической деформации).
Особо следует остановиться на факте существенного понижения критической температуры хрупкости металлов и сплавов в результате ЭШП. Эта проблема сейчас приобрела особую актуальность, во-первых, из-за назревшей необходимости быстрого освоения многих районов Арктики. Восточной Сибири, Якутии, а также обеспечения надежности исследований в Антарктиде; во-вторых, в связи с бурным развитием авиационной и особенно космической техники, в-третьих, вследствие возросших требований криогенной техники (производство, транспортировка и хранение жидкого азота, кислорода, водорода, природного газа и т. д.).
Отмеченная положительная особенность ЭШП, а также его достаточно высокая технико-экономическая эффективность должны привести к массовому применению в указанных областях электрошлаковых сталей.
Есть еще одна сторона у этой проблемы. Известно, что для снижения критической температуры стали проводится ее легирование никелем — весьма дефицитным и дорогостоящим металлом. Для низкоуглеродистой стали 06НЗ (0,06% С, 3% Ni) ЭШП снижает порог хладноломкости от —150 до — 180°С. Следует ожидать, что с помощью ЭШП можно эффективно экономить никель, снижая содержание его в стали, не снижая ее хладостойкость.
Интересным представляется использование преимуществ ЭШП для повышения прочности стали. Сейчас уже нет сомнений в том, что по сравнению с металлом открытой выплавки сталь ЭШП имеет намного более высокие показатели пластичности и вязкости, особенно в вертикальном направлении (по толщине листа). Имеется реальная возможность повысить каким-либо способом (снижением температуры отпуска, повышением содержания легирующих элементов, в том числе углерода или азота) прочность металла ЭШП, несмотря на неизбежное при этом ухудшение пластических и вязкостных свойств. При этом уровень этих свойств все же не опустится ниже аналогичных показателей мартеновской стали. Исследования углеродистых, хромоникелемолибденовых и аустенитных сталей однозначно свидетельствуют о перспективности этого направления.
Все отечественные и зарубежные публикации, посвященные исследованию влияния ЭШП на качество переплавленного металла, отмечают как одно из основных преимуществ металла ЭШП весьма близкие значения показателей различных механических свойств образцов, вырезанных вдоль, поперек и перпендикулярно направлению прокатки. Действительно, уменьшение анизотропии механических свойств — это замечательное качество электрошлакового металла.
Допускаемые напряжения для деталей машин выбираются, как правило, по результатам испытаний образцов, вырезанных вдоль и поперек направления прокатки, т. е. с учетом так называемого коэффициента анизотропии. Однако по пластичности и ударной вязкости показатели поперечных образцов металла ЭШП не уступают аналогичным показателям продольных образцов сталей рядовых методов производства (а иногда и превосходят их). Следовательно, детали, которые изготавливаются из металла ЭШП, могут иметь меньшее сечение.
Накопленный к настоящему времени экспериментальный материал неопровержимо свидетельствует о том, что наряду с высокими абсолютными значениями механических свойств и высокой их изотропностью металл ЭШП характеризуется еще одним примечательным свойством — значительно меньшим, чем у сталей рядовой выплавки и многих других рафинирующих технологий, разбросом экспериментальных данных при различных испытаниях. Это свойство обеспечивает высокую эксплуатационную надежность металла ЭШП, особенно в качестве конструкционного материала. К сожалению, еще нет удовлетворительных методов расчета, которые могли бы учесть указанное свойство. Это обстоятельство иногда сдерживает применение электрошлакового металла.
Структура электрошлакового металла
Высокая химическая однородность электрошлакового металла благоприятно сочетается с высокой структурной его однородностью, которая обусловлена специфическими условиями кристаллизации электрошлакового слитка или отливки.
Строение электрошлаковых слитков
Деформированная электрошлаковая сталь, катаная или кованая, отличается от стали обычного производства значительно более высоким качеством структуры. Это существенно предопределяет повышение общего уровня физико-механических характеристик и их изотропности, а также служебно-эксплуатационных свойств, в том числе и таких факторов, как надежность и долговечность работы изделий.
Качественная основа структуры стали как конструкционного материала закладывается еще в период ее кристаллизации. Результаты протекающих при этом физико-химических и теплофизических процессов фиксируются в затвердевшем металле в виде структурной, физической и химической неоднородности.
Как известно, макроструктура обычных слитков состоит из поверхностной зоны мелких неориентированных кристаллов, зоны транскристаллизации, переходной зоны направленных и неориентированных кристаллов, зоны крупных равноосных кристаллов и, наконец, зоны осаждения индивидуальных кристаллов, образующих «конус» в нижней части слитков (рисунок 1). Каждая из перечисленных зон отражает определенные изменения теплофизических условий кристаллизации стали. Таких изменений при затвердевании обычного слитка происходит четыре.
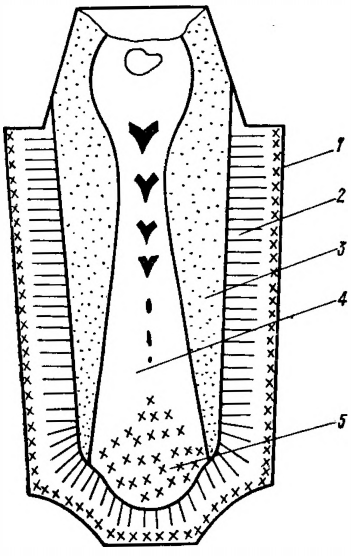
Кристаллическое строение электрошлаковых слитков более однородно. Их макроструктура характеризуется сквозной транскристаллизацией и, следовательно, отражает высокую стабильность теплофизических условий затвердевания металла. И только в крупных электрошлаковых слитках, диаметр которых превышает 500 мм, наблюдается двухзонное строение — периферийная область столбчатых кристаллов и центральная область равноосных кристаллов (рисунок 2).
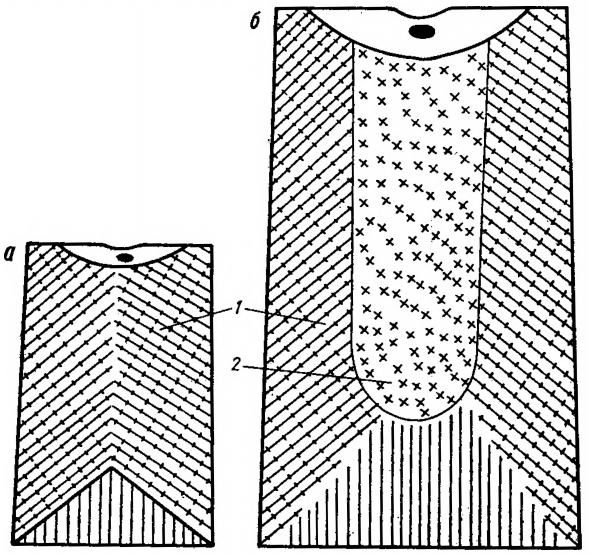
Сравнивая дендритную структуру, следует отметить, что высокие скорости кристаллизации и температурный градиент у фронта затвердевания электрошлакового металла создают благоприятные условия для роста относительно более тонких кристаллов. Расстояние между осями второгопорядка (дисперсность структуры) в литом металле электрошлакового переплава на 20% меньше, чем в металле обычного производства.
В. А. Ефимов отмечает, что неоднородность размеров, формы и мест распределения кристаллов в объеме слитка является главной проблемой получения качественного слитка. Эта проблема успешно решается на основе ЭШП.
Физическая неоднородность обычных слитков, если исключить дефекты разливочного происхождения, проявляется в наличии газовых пор различных размеров и раковин (см. рисунок 1). Поры располагаются преимущественно в переходной зоне и зоне равноосных кристаллов, а раковины — в осевой части слитков. Возникновение этих несплошностей в металле вызвано затрудненностью или полным отсутствием подпитки жидким металлом фронта затвердевания. Поэтому обычный слиток в литом состоянии не может быть использован непосредственно для получения изделия и подвергается обязательной горячей деформации не только с целью формоизменения, но и для заваривания внутренних дефектов. При прокатке слитков степень деформации их сечения составляет не менее 6, а при ковке — не менее 3. Заваривание газовых пустот способствует некоторому повышению удельной плотности деформированного металла.
Пористость в металлической матрице обычных слитков вызывается также выделением неметаллических включений. Размер таких пор в отдельных случаях может достигать 500 мкм. В процессе прокатки и ковки металла такие поры не исчезают, не завариваются, а только изменяют свою форму, вытягиваясь в сплошные или прерывистые строчки.
Электрошлаковый слиток отличается от обычного резким повышением физической однородности. Направленное снизу вверх последовательное затвердевание металла в условиях беспрепятственной подпитки жидким металлом фронта кристаллизации практически блокирует появление физической неоднородности в виде газовых пор и раковин. Это подтверждает тот факт, что горячая деформация электрошлакового металла практически не влияет на его удельную плотность. Суммарная площадь пор, образованных неметаллическими включениями, у электрошлаковой стали в несколько раз меньше, чем у обычной, а размер единичных пор не превышает 30 мкм. Поэтому удельная плотность литой электрошлаковой стали превосходит удельную плотность деформированной стали обычного производства (таблица 1). По этой же причине и литая и деформированная электрошлаковые стали при прочих равных условиях всегда обладают более высокими пластическими и вязкими свойствами. Высокая физическая однородность электрошлаковых слитков обеспечила возможность использования их в литом состоянии для изготовления различных изделий.
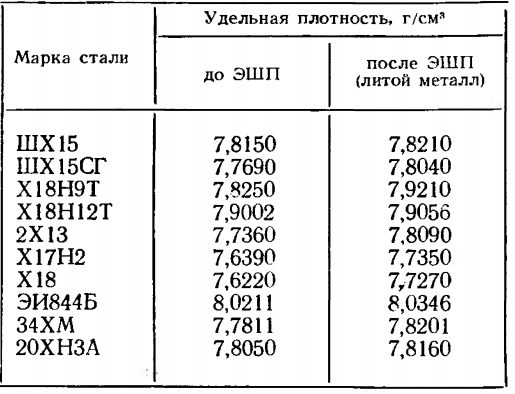
В макроструктуре обычного слитка химическая неоднородность проявляется ввиде V-образной внецентренной зоны положительной ликвации, Λ-образной осевой зоны положительной ликвации, подприбыльной зоны положительной ликвации и зоны отрицательной ликвации, расположенной в его нижней трети. Зоны положительной ликвации характеризуются повышенным (в 2—5 раз выше, чем в других зонах) содержанием углерода, серы, фосфора, кислорода, водорода и некоторых других примесей. В зоне отрицательной ликвации содержание перечисленных элементов понижено, за исключением кислорода. Всем зонам присуща повышенная загрязненность неметаллическими включениями. Горячая деформация и термообработка не устраняют химической неоднородности, и она наследственно передается прокату или поковкам. Это приводит к разнородности физико-механических свойств деформированного металла, полученного из одного слитка.
В электрошлаковых слитках с однородной транскристаллитной структурой зональная химическая неоднородность отсутствует. Макроструктура характеризуется равномерным распределением основных и легирующих элементов, а также примесей — серы, фосфора, кислорода и неметаллических включений. Макроструктура деформированного металла отличается высокой плотностью и однородностью.
В крупных электрошлаковых слитках, диаметр которых более 1000 мм, при равномерном распределении серы по сечению наблюдается некоторое укрупнение сульфидных включений в зоне равноосных кристаллов. Вместе с тем при оценке распределения серы по отпечаткам Баумана, снятым с сечений поковок, электрошлаковый металл превосходит металл обычной выплавки. Высокая плотность структуры крупных электрошлаковых поковок подтверждается статистикой контроля качества в производственных условиях — не известны случаи забракования поковок из-за трещин и раковин, образующихся в центральных объемах обычных слитков при их кристаллизации.
Повышение структурной, физической и химической однородности металла в результате ЭШП наследственно передается деформированному металлу в виде проката, поковок и штамповок. Многочисленные данные исследований и промышленного контроля макроструктуры деформированного электрошлакового металла позволили выявить следующие его преимущества, по сравнению с деформированным металлом обычного производства:
- Снижение загрязненности сульфидными включениями на 2—4 балла при контроле на серных отпечатках.
- Резко выраженная пониженная травимость вследствие повышения общей плотности и однородности металла. Длительность травления темплетов из металла ЭШП возрастает в 1,5—3,0 раза по сравнению с травлением металла обычного производства.
- Значительное снижение механической текстурованности, проявляющейся в виде волокнисто-строчечной структуры, в результате уменьшения общего содержания, размеров и более равномерного распределения неметаллических включений. Вместе с тем кристаллографическая ориентация деформированного металла улучшается, что предопределяется более высокой структурной однородностью слитков. Это особенно важно для электротехнических сталей.
- Тонковолокнистое строение излома, отсутствие дефектов типа сколов, слоистости, расслоений, шиферности, вызываемых локальным отложением неметаллических включений по границам литых кристаллов.
Перечисленные достоинства оказываютнепосредственное влияния на изотропность свойств электрошлакового металла. Особенно ярко это проявляется в листовом прокате. Если в обычном листе механические свойства, особенно пластические и вязкие, в продольном, поперечном и перпендикулярном направлениях находятся в зависимости 1:0,9:0,2—0,4, то в электрошлаковом листе эта зависимость 1:0,98:0,7—0,9. Из этого очевидно, что свойства листа по толщине в металле ЭШП в 2—4 раза выше, чем в обычном металле.
Строение электрошлаковых отливок
Служебные свойства отливок в большой степени зависят от качества металла, их строения и структуры. Последние факторы в свою очередь тесно связаны с конструкцией отливок. Важное значение имеют температура заливки металла, характер отвода тепла в стенку литейной формы.
Литой электрошлаковый металл, как известно, имеет направленную и в основном ориентированную структуру. Это связано с постепенным наплавлением отливки, наличием мелкой металлической ванны, повышенным отводом тепла в стенку охлаждаемой литейной формы. Металл электрошлакового слитка имеет преимущественно радиально-осевую направленность кристаллического строения (см. рисунок 2) благодаря прямолинейной форме внутренней стенки кристаллизатора.
У литейной формы электрошлаковой отливки внутренняя стенка не имеет прямолинейной формы, это накладывает определенный отпечаток на характер теплоотвода в стенку формы и, следовательно, кристаллизацию металла отливки. Как видно на макрофотографии продольного сечения отливки корпуса запорного клапана энергоблока атомной электростанции (рисунок 3), в отливке образуются зоны встречной кристаллизации с четко выраженной границей встречи кристаллов. Эти зоны образуются в результате изменяющегося в соответствии с очертанием внутренней стенки формы направления фронта отвода тепла.
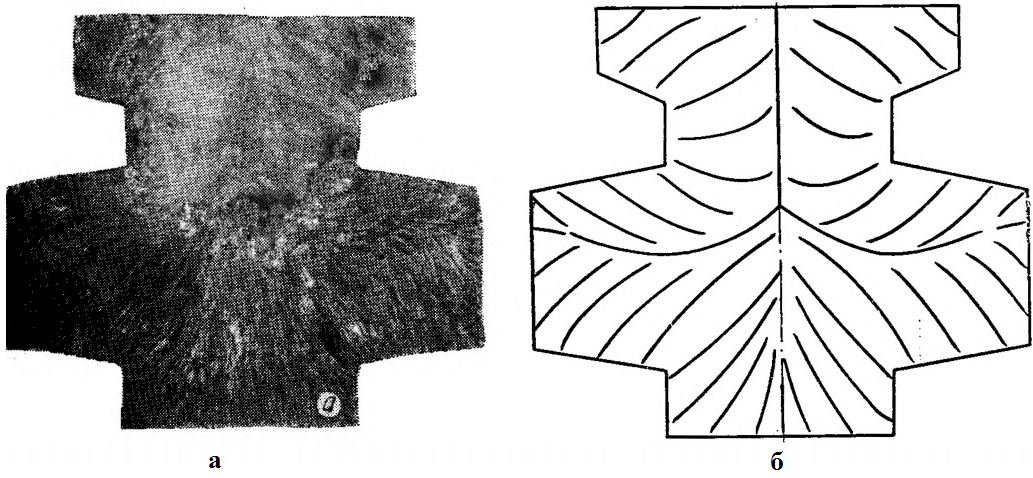
Количество зон встречной кристаллизации еще более увеличивается, если электрошлаковая отливка отливается вместе с полостью (рисунок 4). Внутренний дорн, формирующий центральное отверстие в той же отливке корпуса клапана, создает дополнительный отвод тепла. Отвод тепла в дорн более интенсивен, чем в боковую стенку отливки, так как при усадке отливка отходит от внутренней стенки формы и обжимает дорн. В результате этого граница встречи кристаллов смещается в сторону наружной поверхности стенки отливки.
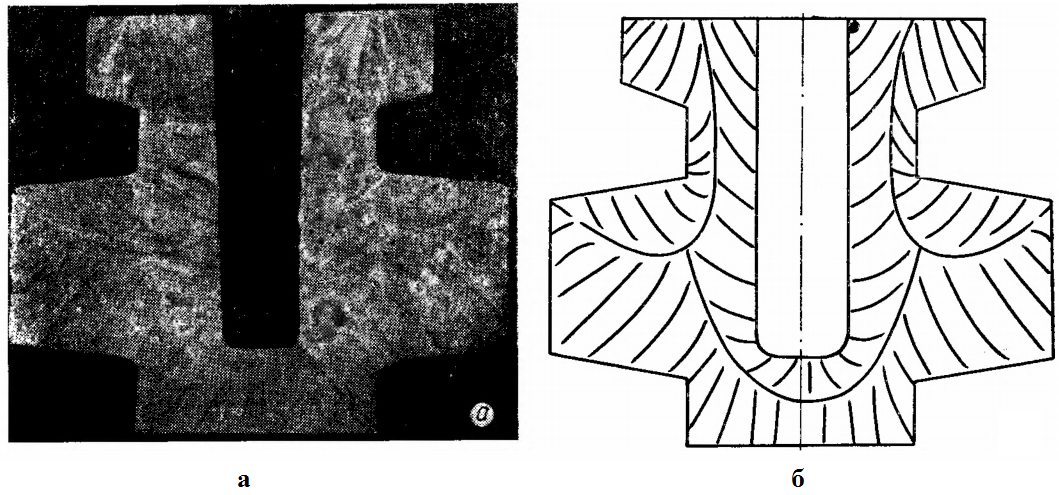
Зоны встречных кристаллов в отливках ЭШЛ традиционно вызывают определенное опасение, основанное на представлениях, сложившихся под влиянием результатов многочисленных исследований качества литого металла открытой выплавки. Действительно, в обычном стальном литье в местах встречи кристаллов отливка всегда имеет пониженные свойства. Это объясняется тем, что здесь скапливаются неметаллические включения и зона встречи кристаллов поражается микропористостью вследствие развития усадочных явлений.
Обычно стальные отливки характеризуются трехзонным строением. У поверхности стенок отливки это зоны столбчатых кристаллов, между которыми находится зона равноосных кристаллов. Последняя зона, особенно в центральной части, имеет низкие служебные свойства, отличается более низкой плотностью, чем другие зоны отливки.
Электрошлаковые сварные швы большой толщины, выполненные на теплоустойчивой стали 15Х2МФ, тоже имеют зону равноосных кристаллов. Однако эта зона имеет такие же плотность и механические свойства, как и зона столбчатых кристаллов:
То же можно сказать и об электрошлаковых отливках. Рафинированный электрошлаковый металл как в шве, так и в отливках имеет значительно более низкое содержание неметаллических включений. Границы кристаллов здесь гораздо чище границ кристаллов металла литья открытой выплавки. В результате механические свойства электрошлаковых отливок отличаются высокими показателями и изотропностью в направлении вдоль и поперек кристаллов, а также по границе встречи кристаллов. На рисунки 5 представлена схема вырезки образцов из литой электрошлаковой плиты (сталь 20Х2М), а в таблице 2 приведены механические свойства литого электрошлакового металла в зависимости от направления вырезки образцов для испытаний.

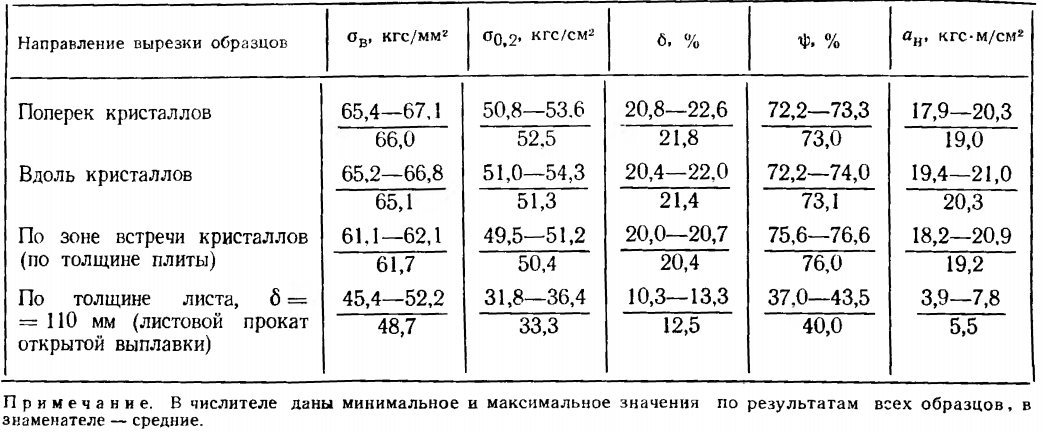
Как видно из представленных в таблице 2 данных, в литом электрошлаковом металле нет традиционной для обычных отливок зоны слабины.
Характерной особенностью кристаллизации электрошлаковых отливок из аустенитных сталей является отсутствие зоны равноосных кристаллов. Тем не менее зона встречи кристаллов и в этом случае имеет высокие физико-химические и механические свойства, такие же, как в остальных частях отливки.
При изучении макростроения зоны встречи кристаллов в электрошлаковой отливке обращает на себя внимание вид кончиков кристаллов встречающихся кристаллизационных фронтов. Они, как правило, невелики по размерам, изгибаются и вытягиваются вдоль общей границы встречи кристаллов в направлении кристаллизации жидкого металла. Такое расположение кристаллов в этой зоне обусловлено постепенным характером кристаллизации наплавляемого металла, когда исключается возможность защемления между их концами порций металлического расплава.
Видимо, эта особенность строения зоны встречи кристаллов, связанная с относительно низкими скоростями кристаллизации электрошлаковых отливок, и обусловливает высокие свойства металла в этом месте.
С увеличением скорости кристаллизации литого металла, например, на порядок, как это имеет место при полунепрерывной или непрерывной разливке стали (ПНРС и НРС), строение зоны встречи кристаллов изменяется. Угол встречи кристаллов при ПНРС или НРС увеличивается по сравнению с отливками ЭШЛ. На их стыке отсутствуют кристаллы, изогнутые в направлении кристаллизации слитка. Граница встречи кристаллов четко выражена, а их концы притуплены. В этих условиях возможны защемление порциижидкого металла между вершинами растущих кристаллов в месте их встречи и образование пористости вследствие его усадки, что неизбежно влечет за собой снижение механических свойств слитка в этой зоне.
Зоны встречной кристаллизации могут образовываться также в электрошлаковых отливках, получаемых путем приплавления заранее выплавленных частей будущей заготовки к объединяющей их части, выплавляемой на заключительной стадии изготовления заготовки.
В этом случае приплавляемые части устанавливаются в соответствующих отверстиях боковой стенки литейной формы для выплавки объединяющей части заготовки. Они являются как бы неохлаждаемыми элементами боковой стенки формы. Во время выплавки объединяющей части эти элементы частично оплавляются и приплавляются к отливке. В результате теплоотвода в них со стороны отливки образуются зоны встречной кристаллизации (рисунок 6). При этом граница встречи кристаллов смещается в сторону этих элементов, так как превалирует отвод тепла в охлаждаемую стенку литейной формы.
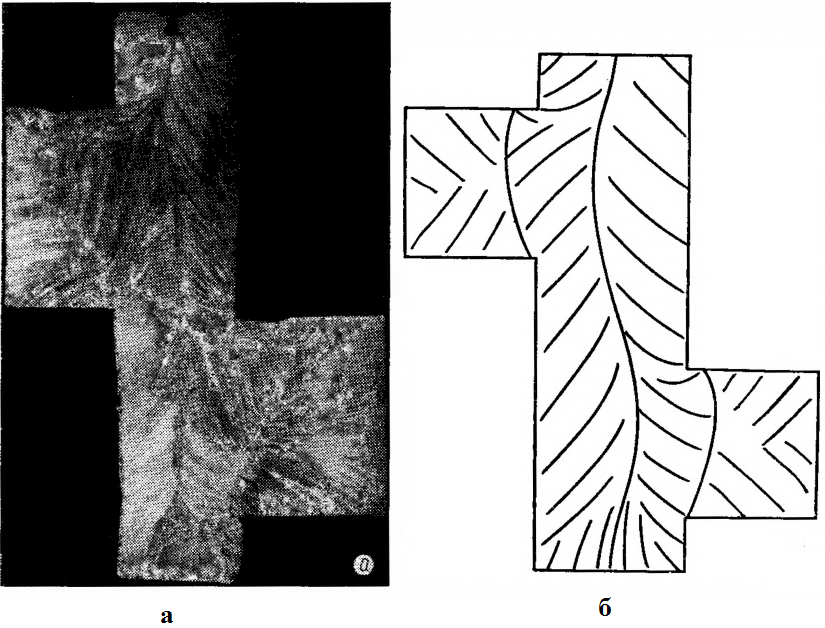
Применение дорнов, формирующих внутренние полости в электрошлаковых отливках, способствует улучшению их кристаллизационной структуры. Это связано с тем, что наличие границ встречи кристаллов приводит к сдерживанию роста последних. Однако при больших скоростях наплавления отливок под дорнами иногда могут образовываться дефекты в виде усадочных раковин.
Обычно для улучшения свойств литого металла его подвергают деформации с целью дробления первичной структуры и термической обработке. Дробление необходимо, чтобы разобщить участки скопления неметаллических включений, какими являются границы кристаллов, и тем самым повысить стойкость металла против хрупких разрушений.
Особенность электрошлаковых отливок состоит в том, что необходимые механические свойства отливок могут быть обеспечены применением лишь одной термической обработки. Это связано с тем, что на границах первичных кристаллов в отливках ЭШЛ нет скопления неметаллических включений. Границы чисты, и поэтому с точки зрения хрупких разрушений они не представляют такой опасности, как у обычного литого металла открытой выплавки.
Дополнительно улучшить структуру электрошлаковой отливки можно путем введения электромагнитных колебаний в зону плавления, кусковых присадочных материалов в металлическую ванну для искусственного переохлаждения металлической ванны и создания дополнительных центров кристаллизации, а также путем ведения выплавки в импульсном режиме.
Специфические особенности кристаллического строения электрошлакового металла
Как уже отмечалось, ЭШП улучшает кристаллическую структуру слитка, или так называемый дендритный остов. Так, если оси дендритов занимают в стали ШХ15 открытой выплавки 65% объема слитка, то в металле ЭШП этот показатель возрастает до 80%, причем дендритная ликвация в слитках ЭШП на 10—30% меньше. Металл ЭШП отличается от исходного более упорядоченными атомными связями, отражающими своеобразное генетическое влияние структуры расплава. В хромоникелевом сплаве исходной выплавки плотность дислокаций составляла (4—10)·105 линий на 1см, а у металла ЭШП она не превышала 4·105 линий на 1 см.
Исследования показали, что зерна металла ЭШП являются монокристальными образованиями, причем разориентировка главных дендритных осей в пределах одного зерна не превышает 0° 10′, в то время как у металла открытой плавки эта величина в 3 раза больше (0°30′). Если количество фрагментов в кристаллитах металла обычной выплавки достигает четырех — шести, то в металле ЭШП их количество не превышает двух. Угол разориентировки по фрагменту в металле ЭШП постоянен — 0°08′, а в обычном металле этот угол переменный и больше по величине (0°09’—0°13′).
В литом металле ЭШП наблюдаются два типа границ: четко очерченные границы кристаллитов, проходящие по междендритным объемам без грубых выделений избыточных фаз и без зубчатого характера границ, а также более тонкие субграницы внутри кристаллитов. Физико-химическая микронеоднородность металла ЭШП намного меньше, чем у металла открытой выплавки. Так, например, разность микротвердости зерен электростали 12Х2Н4А составила ΔНμ= 150 кгс/мм2, а у металла ЭШП — всего 85 кгс/мм2.
В отличие от слитков аустенитной стали обычной выплавки, где наблюдается значительное увеличение содержания первичного феррита (δ-фаза) по мере приближения от периферии к оси слитка, а также огрубления зерен феррита в осевой части, в слитках электрошлаковой стали феррит распределен равномерно (рисунок 7) и его структура гомогенна по сечению.
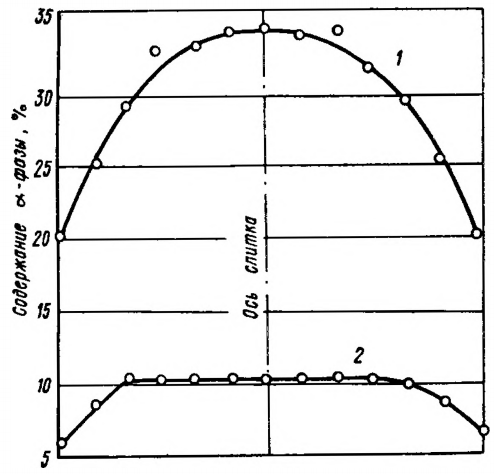
То же имеет место и в других двухфазных сталях и сплавах.
При кристаллизации сложнолегированных сталей и сплавов обычного производства наблюдается большая структурная неоднородность слитка по сечению. Возникает так называемая карбидная ликвация, карбидная сетка в центре слитка более грубая, чем на периферии. При наличии боридной фазы она располагается в виде грубых скоплений, гроздьев. То же имеет место и при наличии карбидов или карбонитридов в аустенитных сталях. ЭШП существенно ослабляет структурную неоднородность (рисунок 8).
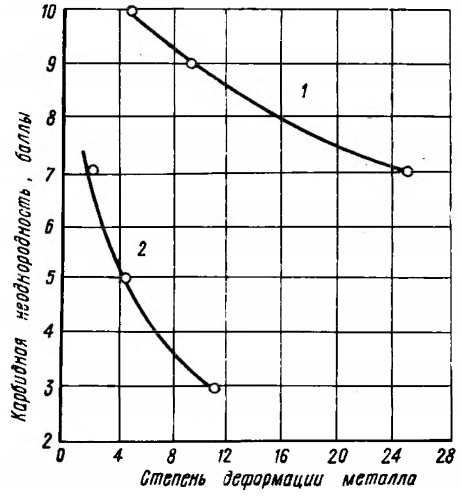
Удаление газов, неметаллических включений и вредных примесей, особенно серы, а также весьма благоприятные условия кристаллизации переплавляемого металла в охлаждаемом кристаллизаторе, обеспечивающие преимущественное наличие развитой зоны столбчатых кристаллов, наряду с улучшением структуры способствуют повышению плотности металла. Многочисленными измерениями плотности, проведенными различными исследователями, установлено, что электрошлаковый металл обладает более высокой плотностью по сравнению не только с обычным металлом, но и с металлом других рафинирующих переплавов.
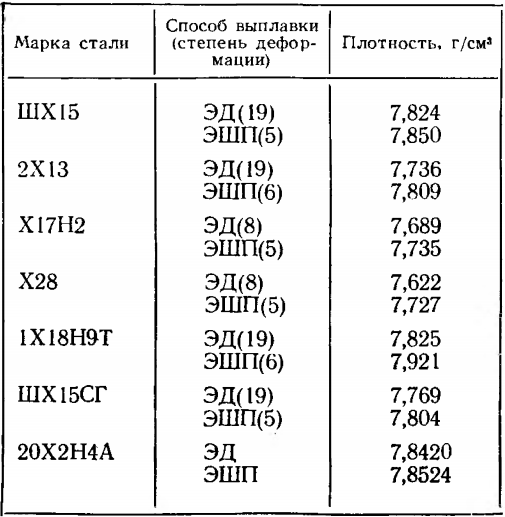
Характерно, что величины плотности металла ЭШП превышают аналогичный показатель исходного металла и тогда, когда степень укова переплавленного металла намного меньше, чем исходного.
Таблица 3 дает наглядное представление о большом преимуществе сталей ЭШП перед исходным металлом электродуговой выплавки (ЭД). Следует отметить, что приведенные в таблице данные — результаты первых, часто опытных, плавок. Дальнейшие работы в этом направлении позволили получить еще более высокие результаты.
Установлено, что литой металл ЭШП по плотности не только не уступает, но и нередко превосходит деформированный исходный металл. Именно этот факт послужил основанием для использования электрошлаковой литой стали без последую щей ковки для изготовления крупногабаритных изделий.
Необходимо отметить, что существенно большая плотность электрошлакового металла является главным преимуществом макроструктурного характера, обеспечивающим резкое снижение брака по дефектам макроструктуры. Если, по рекомендации авторов работы, в качестве меры сравнения плотности металла при различных методах изготовления принять относительную плотность (отношение плотности металла в различных частях слитка к плотности матрицы), то для металла ЭШП этот показатель является максимальным (0,994—0,996) и превышает показатель металла ЭД (0,982—0,993).
Преимущество металла ЭШП в значительной степени связано с резким уменьшением пористости. Как видно из таблицы 4, пористость металла ЭШП (особенно в центральной части слитка) заметно меньше, чем у обычной стали. Естественно, все это благоприятно отражается на плотности электрошлаковой стали.
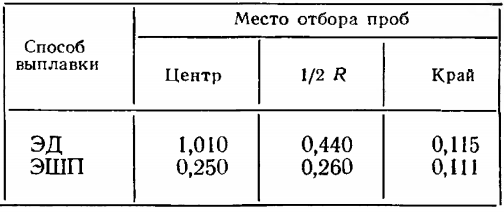
Из таблицы 5 видно, что в любой из исследованных девяти зон плотность металла ЭШП (7,8140—7,8180 г/см3) выше, чем самый высокий показатель плотности металла ЭД (7,8124 г/см3).
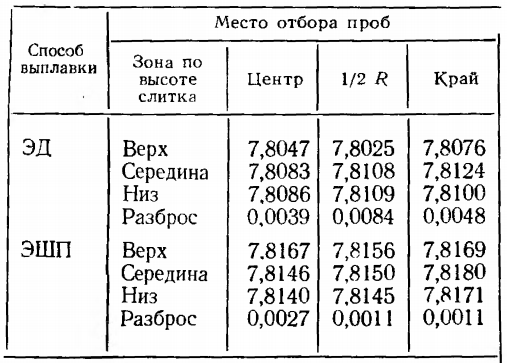
Весьма существенное повышение плотности металлов и сплавов при ЭШП имеет большое значение не только потому, что, как показано выше, это улучшает микро- и макроструктуру слитка, благоприятно отражается на механических и других свойствах металла. Есть отрасли техники, для которых очень важно обеспечить наиболее высокую плотность применяемых металлов. Такой отраслью является прежде всего вакуумная техника, для которой вакуум-плотность является важнейшим критерием качества металла. Естественно, что для вакуумной техники широкое использование электрошлакового металла весьма перспективно.
Химический состав электрошлакового металла
Электрошлаковому переплаву, как правило, подвергается металл конечного химического состава. При этом стремятся к тому, чтобы слиток имел тот же состав, что и электрод, исключая вредные примеси (S, О, Н, N и др.). При ЭШП возможно, а в ряде случаев и целесообразно до легирование металла. Этот вариант процесса пока используется недостаточно, но ему принадлежит большое будущее.
В процессе ЭШП обеспечивается практически полное соответствие химического состава металла слитка и электрода по основным легирующим элементам. Трудности, имеющие место при вакуумных переплавах в связи с испарением некоторых летучих элементов (Мп, Сг), в случае ЭШП отсутствуют. Испарение этих элементов при ЭШП незначительно и не приводит к существенным изменениям состава металла.
Некоторые затруднения при ЭШП возникают при наличии в переплавляемом металле легкоокисляющихся элементов (Аl, Ti, В, Zг), особенно при малом их содержании. Однако значительная гибкость процесса позволяет избежать этих трудностей и достичь оптимального уровня рафинирования металла от примесей. Современная технология и техника ЭШП располагает целым арсеналом средств активного воздействия на металлургические процессы, протекающие при переплаве.
Процесс ЭШП протекает в условиях активного взаимодействия двух жидких фаз — металла и шлака и газовой атмосферы. Равновесие на границе раздела металл—шлак связано с процессами, протекающими в тройной системе металл—шлак—атмосфера над шлаком.
Взаимодействие металла со шлаком зависит от химического состава обеих фаз, состава газовой фазы, а также от температурных и электрических условий на границе раздела. Взаимодействие фаз обусловливает протекание химических и электрохимических реакций, в результате которых осуществляется массоперенос элементов из одной фазы в другую.
Поведение высокоактивных элементов
Окисление активных легкоокисляющихся элементов в металле происходит в результате взаимодействия их с кислородом,основным источником которого является атмосфера над шлаком. На открытой поверхности электрода и шлаковой ванны протекают реакции окисления, в результате которых осуществляется переход кислорода из газовой фазы в шлак с образованием ионов кислорода. На границе металл—шлак протекают реакции восстановления, в результате которых ионы кислорода разряжаются и кислород переходит в металл. В металле кислород связывается активными элементами, которые обладают наибольшим сродством к кислороду и выполняют роль раскислителей.
Реакции раскисления протекают на поверхности раздела металл—шлак, и образовавшиеся окислы поглощаются шлаком, что приводит к некоторому уменьшению содержания в металле элементов-раскислителей.
Кроме атмосферы источником кислорода в системе металл—шлак может являться и сам шлак, поскольку кроме фторидов в нем имеется и некоторое количество окислов. В результате взаимодействия металла и шлака между ними происходят реакции обмена, направленные на приближение системы к равновесию. Содержащиеся в металле активные элементы, обладающие большим сродством к кислороду, восстанавливают менее активные элементы из их окислов в шлаке. При этом происходит обмен элементами между шлаком и металлом. Окислившийся элемент переходит из металла в шлак, а восстановленный — из шлака в металл.
Например, по реакции окисления алюминия закисью железа:
Эту реакцию можно представить также в виде реакции обмена зарядом: Протекание обменных реакций между металлом и шлаком зависит от состава шлака и содержания в нем непрочных окислов, к числу которых в первую очередь относят закись железа FеО. При наличии в шлаке FеО могут быть окислены не только такие активные элементы, как Аl, Тi, В, Zr, Si, но также Мn и Сr. Окисление этих элементов сопровождается восстановлением железа:
Образованию закиси железа способствует наиболее высокое значение свободной энергии системы. Обменные реакции между металлом и шлаком идут с уменьшением свободной энергии системы, при этом образуются окислы с более низким значением термодинамического потенциала. Поэтому при взаимодействии металла со шлаком, содержащим закись железа, активно могут протекать обменные реакции окисления всех металлических элементов, более активных, чем железо.
Кроме закиси железа к числу непрочных окислов в шлаке, определяющих его окислительный потенциал, относят также закись марганца МnО и двуокись кремния SiO2. Понятие прочности окисла весьма относительно, поскольку участие окисла в обменных реакциях зависит от химического состава металла и определяется наличием в нем элементов, более активных, чем металл окисла в шлаке. Поэтому один и тот же окисел в условиях взаимодействия с различным металлом может вести себя по-разному. В одних условиях он участвует в обменных реакциях с металлом, в других — не участвует и рассматривается как прочный окисел, присутствие которого в шлаке не приводит к окислению элементов металла.
Таким образом, закись железа является наиболее универсальным окислом, окислительное действие которого распространяется на все основные элементы в стали. Почти столь же широким спектром
действия обладает закись марганца. Окислительная способность двуокиси кремния проявляется только при наличии в металле элементов, более активных, чем кремний.
Протекание обменных реакций и их развитие зависят не только от активности окислов и элементов, а также и от их концентрации. С увеличением концентрации активность возрастает. При этом оказывается возможным восстановление металла из окисла менее активным металлом, например алюминием, титаном и даже кремнием:
Возможно восстановление кальция алюминием или титаном:
Переход кальция в металл ограничен его малой растворимостью. Поэтому при протекании реакций восстановления возможно образование нейтральных атомов кальция, находящихся в шлаковом расплаве:
Присутствие в шлаке атомов кальция может способствовать поглощению кислорода по реакции:
В результате этой реакции в шлаке увеличивается содержание окиси кальция и возрастает количество свободных ионов кислорода. Это приводит к увеличению окислительной способности шлака, которая проявляется не только по отношению к таким активным элементам, как титан и алюминий при переплаве сталей и сплавов, но и к кремнию в случае отсутствия в сталях более активных элементов.
Развитие реакции определяется значением ее константы равновесия, вычисляемой как отношение активностей элементов и соединений, участвующих в реакции.
Изменяя отношение активностей окислов в шлаке, можно регулировать развитие реакций. На практике управление ходом реакций осуществляется подбором шлака с нужным соотношением содержаний окислов. При этом учитывают взаимодействие системы с газовой фазой над шлаком и образование окислов на поверхности электрода.
Кроме развития окислительных реакций и реакций обмена для обеспечения заданного химического состава в слитке необходимо учитывать также различную интенсивность этих реакций в различные периоды плавки. Например, реакция восстановления кремния получает наибольшее развитие в начальный период плавки и замедляется по мере наплавления слитка вследствие расходования двуокиси кремния, содержащейся в шлаке.
Для предупреждения попадания в шлак окислов, образовавшихся на поверхности электродов при горячей обработке давлением или литье, используют электроды с зачищенной и протравленной поверхностью. В качестве дополнительных мер защиты при наличии в металле легкоокисляющихся элементов применяют различного рода краски и покрытия электродов.
С целью уменьшения угара активных элементов в некоторых случаях над поверхностью шлаковой ванны создают защитную атмосферу. При этом исключается окисление металла кислородом атмосферы, однако не устраняется возможность окисления вследствие обменных реакций между металлом и шлаком. Создание защитной атмосферы при ЭШП снижает степень десульфурации и имеет другие отрицательные стороны, одной из которых является увеличение интенсивности протекания обменных реакций между металлом и шлаком.
Более приемлемым решением вопроса уменьшения окисления активных элементов является раскисление шлака. Существенное улучшение в отношении снижения угара элементов в начальный период плавки достигается уже при предварительном раскислении шлака в ковше перед заливкой в кристаллизатор. Однако вследствие непрерывного поступления в шлак окислов железа FеО и кислорода атмосферы в процессе ЭШП возникает необходимость непрерывного раскисления по ходу плавки.
Наибольшее распространение получил ввод алюминия. Раскисление шлаковой ванны алюминием и алюмокальцием предотвращает угар кремния, титана и других легирующих элементов, а также способствует более эффективному обессериванию металла. Наиболее равномерное распределение титана, алюминия и других элементов по высоте слитка достигается при дифференцированном раскислении, учитывающем интенсивность окислительных процессов в различные периоды плавки. При введении алюминия в шлаковой ванне протекают реакции его окисления, на которые расходуется окислительный потенциал шлака. Окисление алюминия в первую очередь происходит за счет кислорода, поглощаемого шлаком из атмосферы. При этом происходят реакции восстановления катионов трехвалентных металлов (Fе3+, Мn3+, Тi3+) до двухвалентных с образованием Аl2Оз. Во вторую очередь идут реакции восстановления менее активных металлов из их окислов. В результате изменения содержания окислов в шлаке и отношения их активностей изменяются условия равновесия системы металл—шлак. Состояние равновесия достигается при значительно более высоких значениях концентраций активных элементов. При этом удается обеспечить практически полное усвоение таких элементов, как титан, алюминий, бор.
Раскисление шлаковой ванны алюминием позволяет также регулировать содержание в металле кремния и марганца. Процессы раскисления шлака описываются соответствующими реакциями окисления алюминия. Возможность регулировать распределение кремния и марганца объясняется изменением отношения активностей глинозема и окислов этих элементов.
Раскисление шлака возможно также углеродом. При температурах ЭШП углерод обладает значительной раскислительной способностью, которая с повышением температуры возрастает. Преимущество этого варианта раскисления состоит в том, что продуктами реакций являются газообразные вещества, которые к тому же создают над шлаком защитную атмосферу. Использование плавающих угольных или графитовых поплавков позволяет резко снизить окисление титана при переплаве нержавеющей стали.
Раскисление шлаковой ванны алюминием или другим раскислителем используется в основном при переплаве сталей и сплавов, содержащих легкоокисляемые элементы. Сохранение легирующих элементов при ЭШП основной массы сталей обеспечивается подбором состава шлака и другими технологическими мерами (температурный режим, коэффициент заполнения кристаллизатора и др.).
Одним из важных моментов взаимодействия металла и шлака при ЭШП является переход в металл алюминия из шлаков, содержащих глинозем. Восстановление алюминия происходит в результате обменных реакций между металлом и шлаком. В этом случае глинозем шлака является источником кислорода для окисления активных элементов металлического расплава. При высоком содержании в шлаке глинозема возможно протекание реакций восстановления алюминия титаном и кремнием. В реакциях восстановления алюминия может принимать участие также углерод. Алюминий может переходить из шлака в металл также в результате протекания катодных реакций:
Переход алюминия из шлака в металлпри ЭШП осуществляется в малых количествах (тысячные — сотые доли процента). Присутствие его способствует измельчению структуры и улучшению свойств. Однако в некоторых конструкционных сталях алюминий даже в очень малом количестве оказывает отрицательное влияние. Даже незначительное увеличение содержания алюминия выше его остаточного содержания в некоторых сталях обусловливает их склонность к трещинам. Выделение включений глинозема при кристаллизации трансформаторной стали препятствует образованию требуемой текстуры и снижает магнитные свойства. Поэтому увеличение содержания алюминия при ЭШП этих сталей недопустимо.
Увеличению интенсивности перехода алюминия в металл может способствовать отсутствие или ослабление других источников окисления металла. В условиях переплава в нейтральной или слабоокислительной атмосфере возможно протекание реакций восстановления алюминия железом. Снижению интенсивности реакций восстановления алюминия способствуют повышение содержания в шлаке двуокиси кремния, а также одновременное увеличение содержания окиси кальция.
Содержание алюминия при ЭШП регулируют подбором шлака. В соответствии с законом распределения интенсивность процессов восстановления алюминия зависит от отношения активностей глинозема и других окислов в шлаке. Изменяя это отношение, можно достичь нужного распределения элементов.
Особенностью процессов взаимодействия металла и шлака, в состав которого входит глинозем, является то, что при реакциях перехода в металл алюминия содержание кислорода в металле выше обычного. Для объяснения этого явления протеканием термохимических реакций диссоциации глинозема:
необходимо допустить существование в шлаковой ванне зон с температурой выше 2000°С. Однако реальное содержание кислорода в металле не соответствует стехиометрическому соотношению 2Аl:3O. Кислород оказывается в избытке. Связь процессов перехода алюминия в металл с кислородом объясняют протеканием электрохимических реакций. Согласно этим представлениям, переход алюминия в металл сопровождается одновременным переходом в металл кислорода в результате протекания реакций анодной нейтрализации ионов алюминатов:
Соотношение алюминия и кислорода по этой реакции (1:2) удовлетворительно согласуется с данными практики. Существуют и другие объяснения. По мнению авторов работы, повышение содержания кислорода в металле, сопутствующее переходу алюминия из шлака в металл, можно объяснить протеканием цепи электрохимических реакций, одним звеном в которой является реакция восстановления алюминия на катоде, а другим — анодная реакция поляризации железа:
Образование в шлаке ионов Fе2+, как известно, ведет к поглощению кислорода и его переходу в металл.
Возможно также, что поведение кислорода объясняется изменением условий на межфазной поверхности металл—шлак и затруднением реакций раскисления металла в условиях протекания процессов восстановления алюминия, поскольку активность продуктов раскисления и скорость их удаления зависят от состава и свойствшлака у межфазной поверхности.
Эффект рафинирования металла
Основными задачами повышения качества металла, которые успешно решает ЭШП, является рафинирование металла и получение совершенной структуры. Решение второй задачи в определенной степени связано с решением первой. Поэтому рафинирование металла приобретает первостепенное значение.
Наиболее важными показателями рафинирования металла при ЭШП является удаление серы и кислорода и других примесей.
Десульфурация металла является одним из важных преимуществ ЭШП перед вакуумными видами переплавов. Степень десульфурации металла при ЭШП в открытом кристаллизаторе составляет 70—80%. При вакуумных видах переплава десульфурация металла практически отсутствует.
Десульфурация металла в вопросах рафинирования имеет большое значение, поскольку сера не только отрицательно влияет на механические свойства металла, его деформируемость и устойчивость против трещин, но и как сильноликвирующий элемент способствует образованию несовершенств макроскопического строения слитка, чем снижает качество металла.
Степень удаления кислорода при ЭШП, как и серы, составляет 40—80%. Степень деазотации металла в зависимости от композиции сплава составляет 10—80%. Удаление всех этих элементов также имеет большое значение как для обеспечения качества металла в изделии, так и для получения слитка без макронесовершенств.
Эффективность рафинирования металла при ЭШП по кислороду и азоту иллюстрируют данные таблицы 1 и 2.
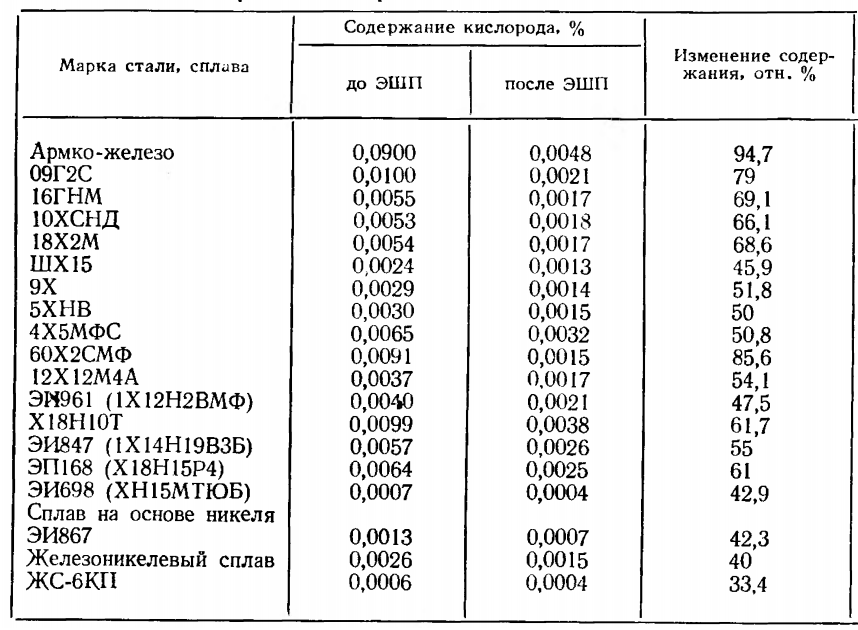
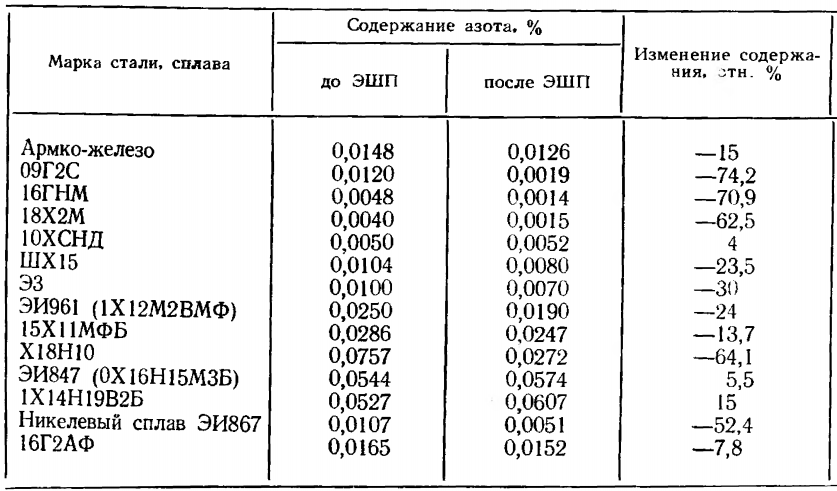
Особое место в металлургии ЭШП занимает вопрос удаления водорода. В условиях плавки в открытом кристаллизаторе и наличии в атмосфере повышенного содержания водяных паров процессы поглощения водорода из атмосферы превалируют над процессами удаления его из металла, в результате чего содержание водорода в металле возрастает. Интенсификация процессов удаления водорода требует применения специальной технологии (продувка шлака и металла инертным газом, применение дополнительной цепи постоянного тока с не расходуемым электродом), что ведет к усложнению процесса. Поэтому в практике ЭШП в отношении водорода ограничиваются мерами предотвращения попадания влаги в реакционную зону процесса. При этом удается получать слитки с относительно низким содержанием водорода (не более 2·10-4% даже в очень крупных слитках). К тому же образование флокенов в металле ЭШП менее вероятно, чем в металле обычного слитка. Как известно, флокены образуются преимущественно в местах появления ликвации и по границам неметаллических включений. Более высокая чистота металла ЭШП обусловливает уменьшение вероятности образования флокенов, что позволяет считать допустимым содержание водорода в слитках ЭШП на уровне его содержания в кузнечных слитках (2·10-4%).
Эффект рафинирования металла при ЭШП наглядно проявляется в уменьшении загрязнения металла неметаллическими включениями, поскольку основная часть их связана с наличием примесей. На рисунки 1 приведены частотные диаграммы загрязненности шарикоподшипниковых сталей ШХ15СГ и ШХ15 оксидными и сульфидными включениями до и после ЭШП.
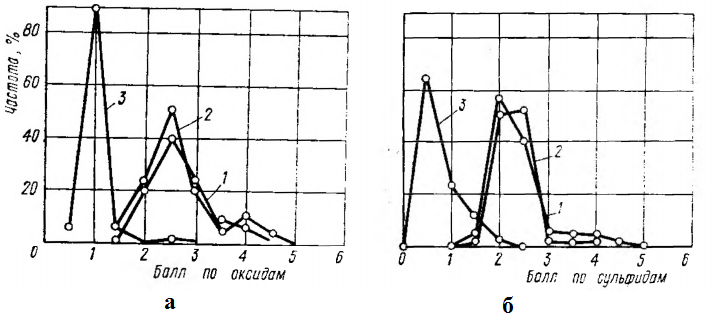
Указанные диаграммы иллюстрируют высокую эффективность ЭШП в удалении оксидных и сульфидных включений. После ЭШП чистота металла повышается в 2—3 раза. Аналогичные данные получены при исследовании различных марок сталей и сплавов.
На рисунки 2 показано изменение чистоты по оксидным включениям легированной стали, ЭИ847.
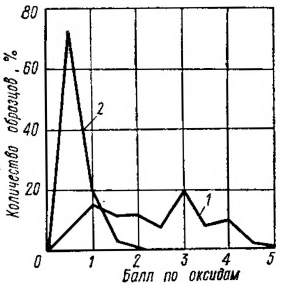
Распределение неметаллических включений в металле определенным образом может характеризовать однородность металла по химическому составу, в частности по распределению примесей. Однородность металла ЭШП в отношении распределения таких примесей, как сера и кислород, хорошо иллюстрирует распределение окисных и сульфидных включений. Распределение этих включений по высоте и сечению слитка котельной стали 12Х1МФ электродуговой выплавки и ЭШП, по данным исследования, показано на рисунки 3.
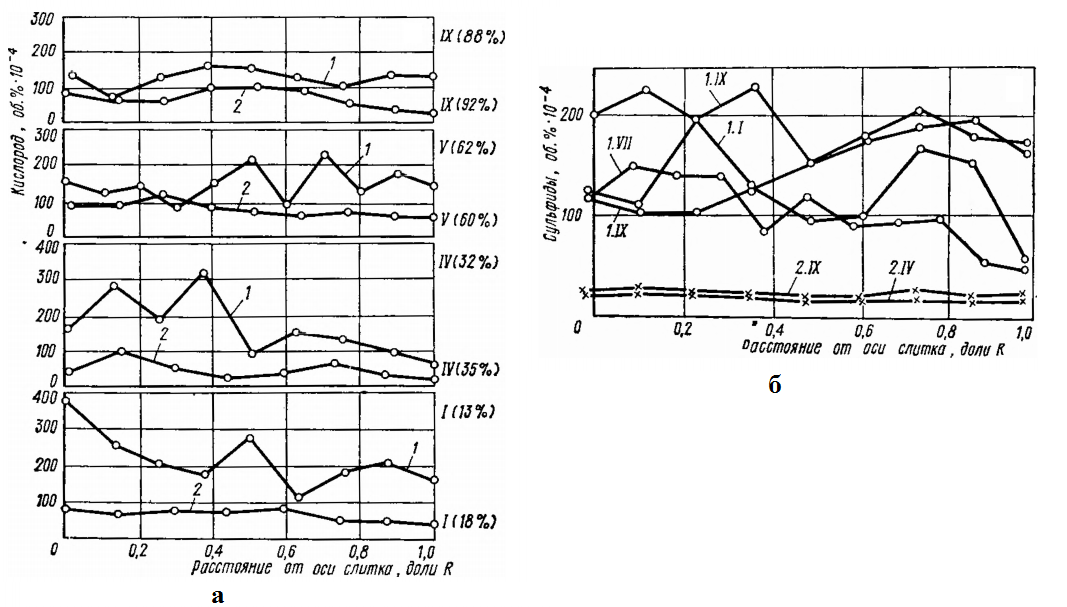
В слитке электростали обычного производства оксидные и сульфидные неметаллические включения распределены неравномерно. Эта неоднородность в распределении включений и связанных в них примесей в слитке ЭШП отсутствует.
Еще более контрастным является повышение в результате ЭШП однородности стали 12Х1МФ мартеновской выплавки. Мартеновская сталь отличается более высоким содержанием серы, ликвация которой приводит к образованию неоднородности. Поэтому сульфидные включения в слитке мартеновской стали 12Х1МФ распределены еще более равномерно, чем у электростали (рисунок 4). В слитке ЭШП значительно меньше содержание сульфидов и распределены они равномерно.
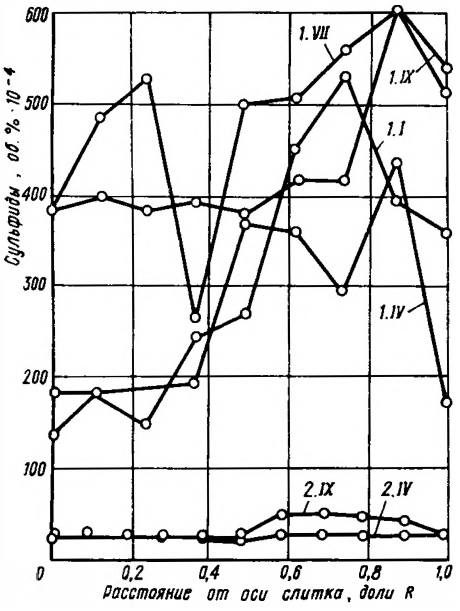
Эффект рафинирования металла при ЭШП тем выше, чем более загрязнен металл примесями. С уменьшением содержания примесей эффект рафинирования уменьшается, однако достигаемая степень чистоты металла, т. е. глубина рафинирования, возрастает. Поэтому для получения металла наиболее высокой чистоты необходимо, чтобы металл электродов был по возможности более чистый.
Влияние чистоты исходного металла на глубину рафинирования электростали показано на рисунки 5. Наибольшая глубина рафинирования достигается при использовании электродов из стали, обработанной систематическим шлаком, а также из вакуумированного металла, т. е. более чистого исходного металла. При переплаве стали с очень низким содержанием серы получена сталь, практически не содержащая сульфидных включений.
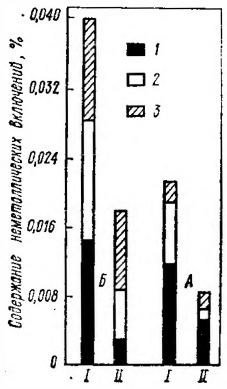
Исключительно высокая чистота металла может быть достигнута при двойном ЭШП (рисунок 6).
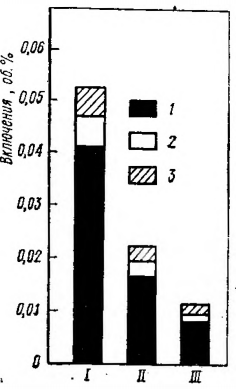
Особенно эффективен двойной переплав под разными флюсами. Изменение загрязненности стали ШХ15 при двойном ЭШП по специальной технологии Запорожского машиностроительного института показано на рисунок 7. Чистота этой стали выше, чем стали двойного переплава ЭШП + ВДП.
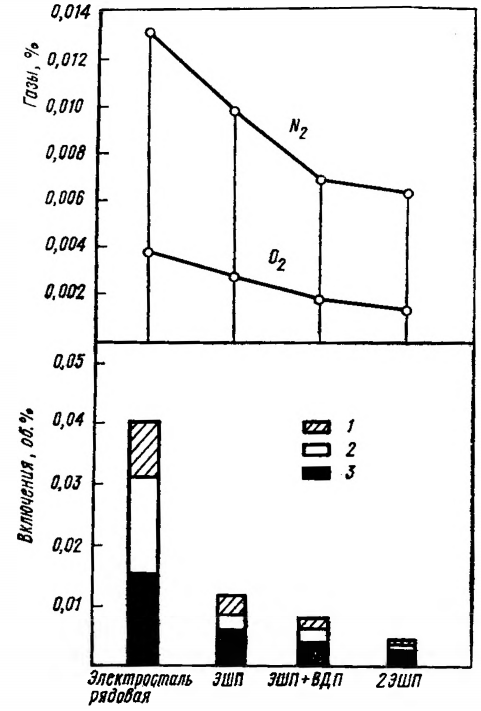