Процесс Consteel
Процесс Consteel является инновационным решением в электросталеплавильном производстве, которое позволяет значительно экономить энергоресурсы и повышает эффективность и экологичность производства стали в электропечах.
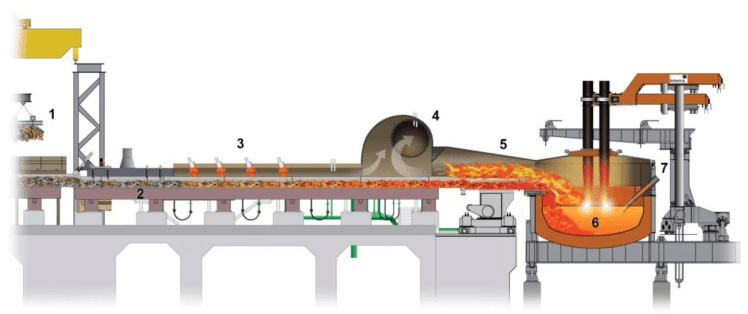
Особенностью этой технологии является непрерывная подача металлолома по конвейеру в электросталеплавильную печь (рис 47). Таким образом, процесс плавки становится фактически непрерывным. При этом обеспечивается постоянное плоское зеркало металла, над которым горят электроды, а расплавление поступающего металлолома происходит в ванне жидкого металла, что приводит к повышению стабильности процесса. Емкость таких печей составляет от 40 до 320 т. Внешний вид установки приведен на рис. 48.
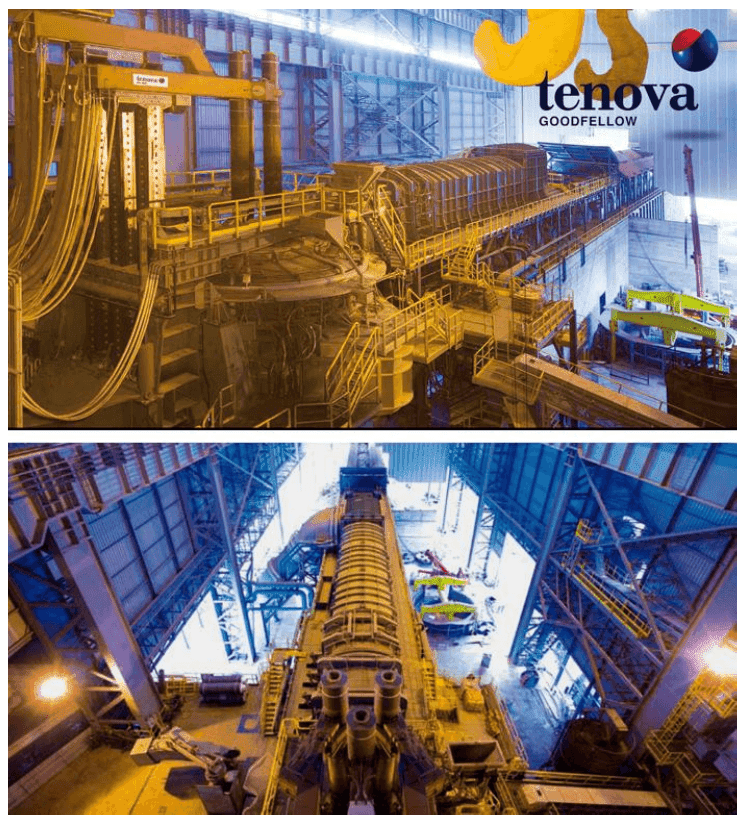
В соответствии с технологией, шихта, с помощью электромагнитного крана, из вагонов подается на загрузочный конвейер, подогреваемый отходящими печными газами, который транспортирует ее к ДСП. Существует вариант технологии с дополнительными горелками, установленными над конвейером. Преимуществом процесса является отсутствие необходимости окускования металлолома, возможно использование даже стружки.
Подогретая шихта загружается в ДСП, где происходит ее расплавление в ванне жидкого металла. Отходящие с ДСП печные газы подогревают движущуюся по конвейеру шихту, после чего направляются на станцию газоочистки.
В отличие от загрузки, выпуск стали из печи осуществляется периодически, а для автоматического обнаружения шлака при выпуске используется устройство на основе инфракрасного датчика.
В печь также можно заливать жидкий чугун, который непрерывно подается в рабочее пространство печи по специальному футерованному желобу.
Преимущества технологии Consteel:
- сокращение расхода электроэнергии на 80…120 кВт·ч/т и электродов за счет повышения стабильности процесса и подогрева шихты;
- повышение производительности печи за счет непрерывности процесса;
- лучшие условия для шлакообразования и более благоприятная атмосфера в печи.
- повышение стойкости футеровки печи;
- снижение более чем на 40% затрат на материально-техническое обеспечение, персонал и обработку отходов производства.
- пониженное содержание FeO в шлаке, снижение содержания азота, фосфора и водорода в стали;
- снижение уровня шума и повышение экологичности производства.
Двухкорпусные печи
Двухкорпусные печи в первую очередь характеризуются повышенной производительностью. Такая печь состоит из двух ванн (корпусов) и одной системы питания с одним (печь постоянного тока) или тремя (печь переменного тока) электродами, которые переставляются с одной ванны на другую. Схема расположения оборудования двухкорпусной печи постоянного тока приведена на рис. 49, а внешний вид на рис. 50.
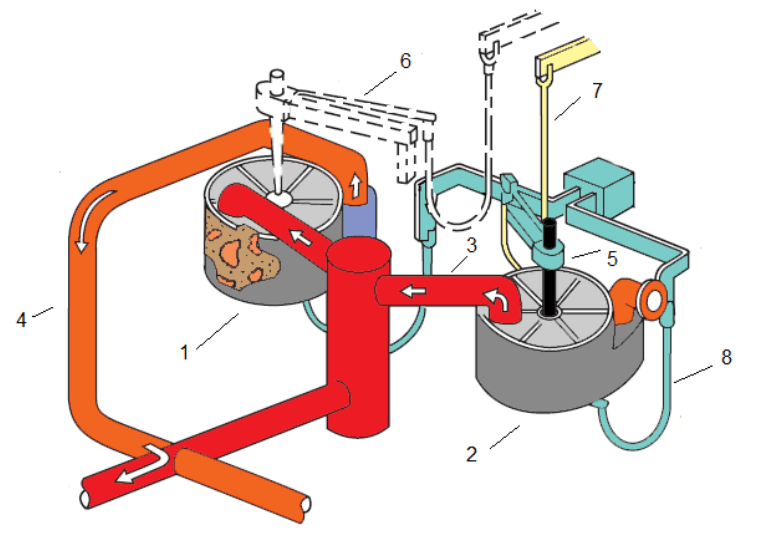
корпус, в котором происходит выплавка стали; 3 – канал для отходящих газов; 4 – канал к системе газоочистки; 5 – электрод с держателем; 6 – положение электрода на второй стадии; 7 — электрические кабеля к верхнему электроду; 8 — электрические кабеля к нижнему электроду
Пока в одном корпусе идет плавка металла с помощью электродов в другом корпусе происходит подогрев шихты отходящими газами из первого корпуса или газовыми горелками. При этом время плавки сокращается на 40%, а за счет подогрева шихты достигается снижение расхода электроэнергии на 40…60 кВт·ч/т. Встречаются печи, в которых электроды установлены на двух ваннах, однако в этом случае теряется экономический эффект от сокращения капитальных затрат на строительство агрегата.
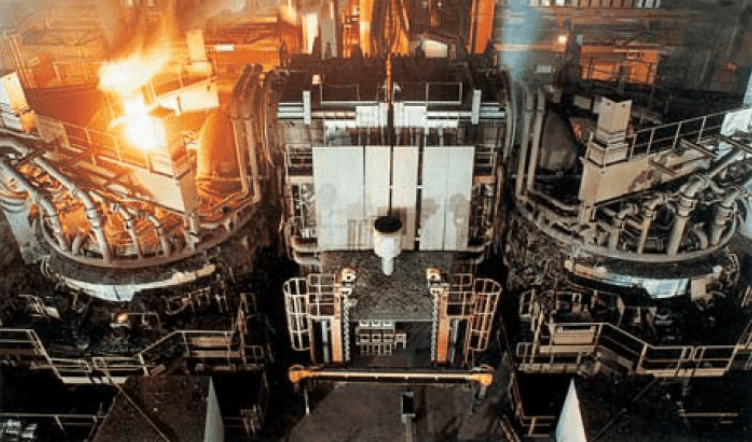
Еще одним вариантом реализации двухкорпусных печей является агрегат CONARC (СONverter + electric ARC furnance). Этот агрегат также имеет два корпуса печи, но помимо одного комплекта электродов на нем установлена и фурма для подачи кислорода (как в конвертере). Внешний вид агрегата приведен на рис. 51. Преимуществом данного агрегата является возможность выплавки стали из жидкого чугуна и металлолома (или DRI) практически в любых пропорциях.
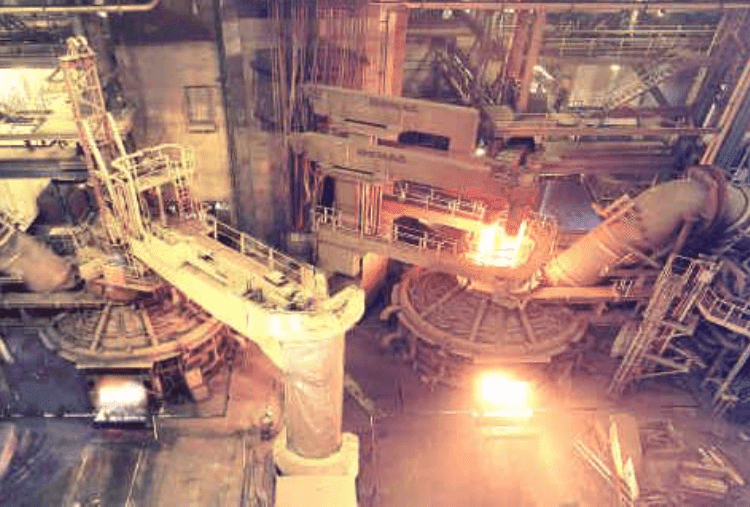
Процесс выплавки стали разделен на две стадии (рис. 52). Вначале в один корпус заливают чугун, в печь устанавливают фурму и начинают продувку кислородом. На этой стадии производится обезуглероживание металла.
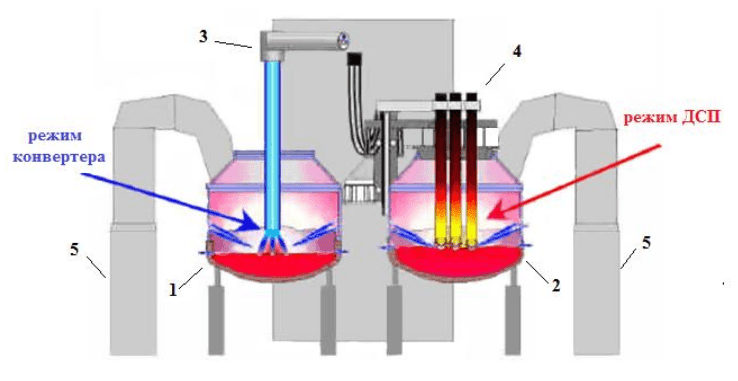
Во избежание перегрева ванны из-за происходящих во время продувки процессов окисления углерода, кремния, марганца и фосфора, в печь добавляют охладители в виде металлолома или DRI. После завершения продувки, кислородную фурму переставляют на второй корпус (или отводят в сторону), а на первый корпус устанавливают электроды. На этой стадии в печь добавляют оставшееся количество твердой шихты и начинают ее расплавление с помощью электродов.
После достижения необходимой температуры металл выпускают в ковш. Затем процесс циклически повторяется снова. Таким образом, выплавка стали идет одновременно в двух корпусах печи, а электроды и фурма переставляются на них поочередно, что обеспечивает высокую производительность агрегата, которая на 30 % выше чем у двух обособленных агрегатов аналогичной емкости). Время плавки составляет от 40 до 60 мин.
Аналогичный принцип использован и в агрегате «Arcon-процесс», разработанном компанией «Concast Standard AG». Отличием является то, агрегат питается постоянным током и корпус агрегата фактически соответствует корпусу конвертера. Поскольку используется постоянный ток, то на агрегате установлено не три, а два электрода – один верхний графитовый и один донный пластинчатый медный электрод (см. рис. 49).
Агрегат «Arcon» имеет производительность 1,6 млн.т/год. В качестве металлошихты используют жидкий чугун (40%), гранулированный чугун (5%) и HBI (55%). Масса выпускаемой плавки — 170 т. Цикл работы каждого корпуса агрегата составляет 92 мин.
В целом, комбинация конвертера и дуговой печи в одном агрегате дает следующие преимущества по сравнению с обычной дуговой печью:
- широкий выбор металлошихты;
- высокая производительность;
- низкий расход электроэнергии в результате использования химической энергии окисления примесей металлошихты;
- уменьшение требуемой электрической мощности;
- снижение удельного расхода электродов;
- меньшее влияние на токоподводящие сети, возможность работы при маломощных электросетях;
- снижение затрат на электрооборудование.
Шахтные электросталеплавильные печи
Особенностью конструкции шахтной электросталеплавильной печи является наличие шахты, в которой производится подогрев металлолома перед загрузкой его в печь. Такая шахта устанавливается сверху над сводом обычной дуговой печи. Шахт может быть одна или две. Температура до которой можно подогреть металлолом составляет 800 °С. Экономия электроэнергии за счет такого предварительного подогрева металлолома составляет 70…100 кВт·ч/т. Через шахту загружается до 60% металлолома, остальной (например крупногабаритный) загружается в саму ванну печи, для этого шахта отодвигается в сторону. Цикл плавки составляет 35…50 минут от выпуска до выпуска. Кроме экономии электроэнергии обеспечивается также сокращение расхода электродов на 30% и повышение производительности на 40%.
Данный процесс появился сравнительно недавно (в конце 80-х годов 20 века), поэтому поиск оптимальных конструкции такой печи продолжается. Рассмотрим два наиболее современных варианта.
SIMETAL EAF Quantum – самое современное конструкторское решение печи с подогревом металлома. На настоящий момент установлена только одна печь на заводе мексиканской сталелитейной компании Talleres y Aceros S.A. de C.V. (г. Тиаса).
Масса плавки по выпуску составляет 100 т, но при этом масса болота (металл и шлак, оставленный после предыдущего выпуска) составляет 70 т. Схема печи приведена на рис 53.
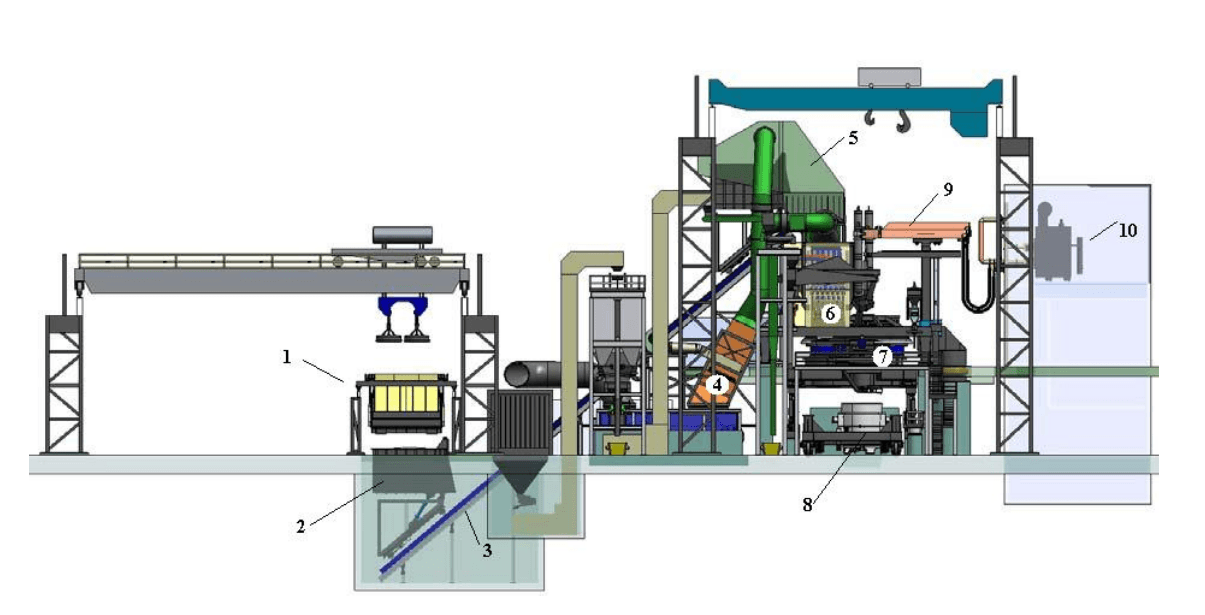
Металлолом краном загружается в бадью и перегружается в подъемник, который поднимается на верх шахты и после открытия люка высыпается вовнутрь, где происходит его подогрев. В этой печи применена новая конструкция шахты, с удерживающими металлолом водоохлаждаемыми пальцами (рис. 54).
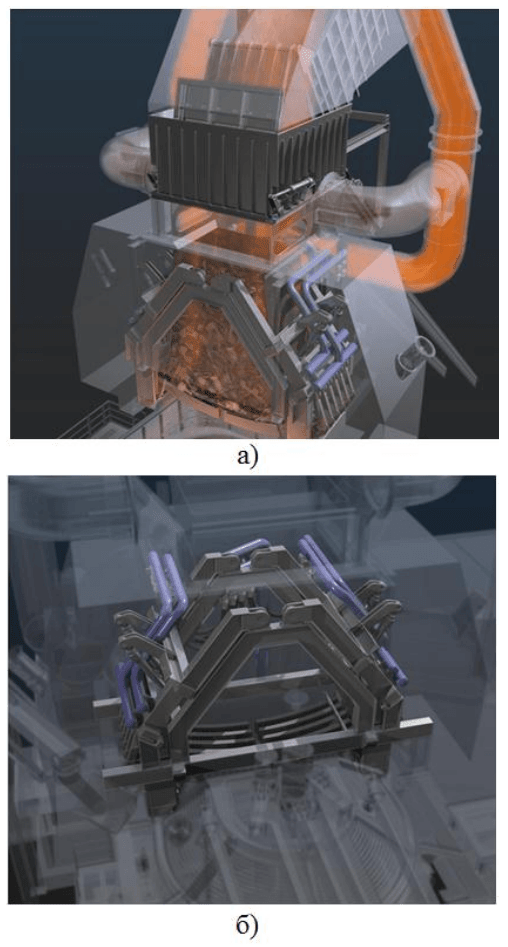
После подогрева пальцы разводятся в стороны и металлолом высыпается в ванну печи. Всего за цикл плавки, продолжительность которого составляет 33 мин, предусмотрена подача трех порций металлолома. Продолжительность нагрева каждой порции – 9 минут. Выпуск металла осуществляется через канал в виде сифона (рис. 55) что позволяет наклонять печь всего на 4° и отсекать полностью шлак.
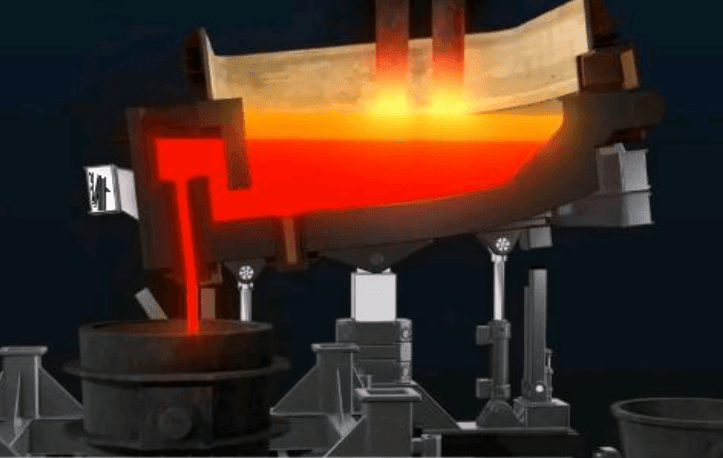
Еще одним инновационным решением, которое совмещает в себе преимущество шахтных печей и печей с непрерывной загрузкой является система EPC (Environmental Preheating and Continuous Charging), которую разработали компании CVS MAKINA и KR Tec GmbH (Турция).
Схема печи с установкой EPC приведена на рис. 56.
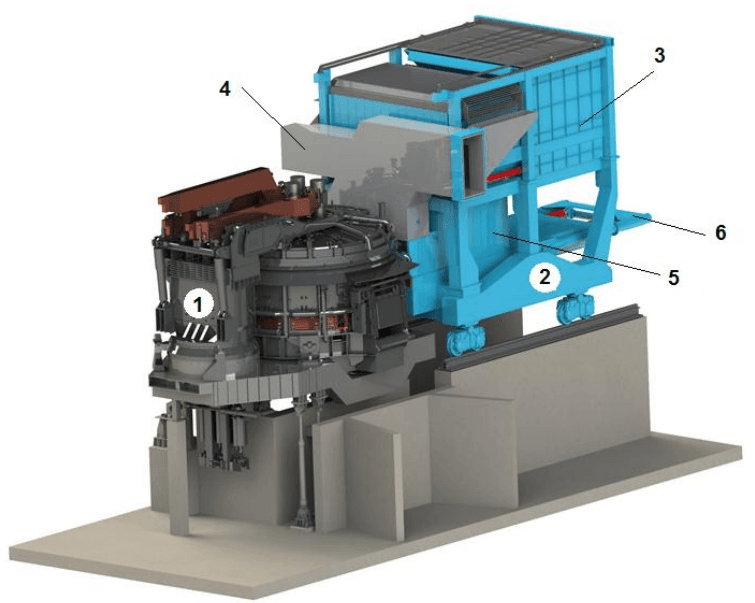
Система ЕРС работает следующим образом (рис. 57). С помощью завалочной корзины шихта загружается в завалочную камеру системы EPС, через отрытую крышку (рис. 57, а).
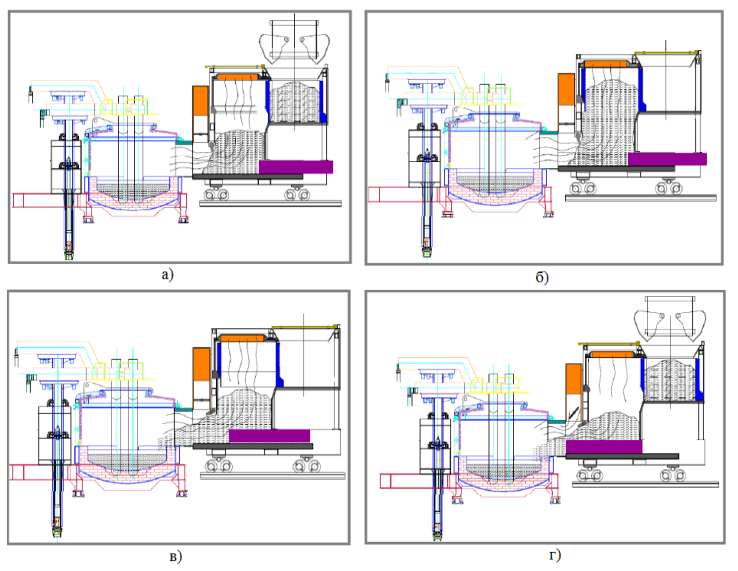
В этой позиции передняя стенка завалочной камеры закрывает шахту (камеру предварительного нагрева) в которой уже подогревается первая порция шихты. Во время загрузки шихты в завалочную камеру процесс плавления в ДСП и процесс предварительного нагрева шихты не останавливаются.
После загрузки шихты из корзины в завалочную камеру крышка закрывается и с помощью гидравлических цилиндров завалочная камера помещается сверху шахты, в которую высыпается шихта для ее предварительного нагрева (рис. 57, б).
После подогрева шихты, с помощью толкателя часть ее ссыпается в пространство печи (рис 57, в), а затем происходит загрузка новой порции металлолома (рис 57, г).
Время плавки в печи, оснащенной системой ЕРС составляет 36 мин, масса плавки по выпуску – 100 т, температура подогрева шихты 800 °С.
Преимущества системы EPС:
- энергосбережение до 100 кВт·ч/т;
- увеличение производительности на 20%;
- независимая завалка лома;
- минимальный выброс пыли;
- быстрая окупаемость (около 12 месяцев).
Источник: Скляр В. О. Инновационные и ресурсосберегающие технологии в металлургии. Учебное пособие. – Донецк.: ДонНТУ, 2014. – 224 с.