Особенности процессов внепечной обработки стали
Первоначально все процессы по доводке стали до нужного химического состава (операции легирования, раскисления, рафинирования, модифицирования) и температуры выполняли непосредственно в сталеплавильном агрегате. Это приводило к увеличению времени плавки (соответственно снижению производительности агрегата) и большому угару легирующих элементов (которые могут быть очень дорогими). Постепенно вышеуказанные операции стали переносить в сталеразливочный ковш и специальные агрегаты.
Данные процессы получили название внепечной обработки стали или ковшевой металлургии.
Внепечная обработка стали начала активно применяться с 60-х годов ХХ века, главным образом для повышения производительности дуговых сталеплавильных печей и конвертеров, позволяя вынести часть процессов рафинирования из этих агрегатов в ковш.
Однако уже начало внедрения современных процессов внепечной обработки показало, что они позволяют не только существенно улучшить качество стали (механические свойства, коррозионную стойкость, электротехнические показатели и др.), но и получить сталь с принципиально новыми свойствами.
Подвергать внепечной обработке можно сталь, выплавленную любым способом. Таким образом, внепечная обработка стали позволяет:
- увеличить производительность основного сталеплавильного агрегата за счет выноса операций раскисления, рафинирования и легирования в агрегат внепечной обработки;
- повысить качество металла за счет удаления вредных газовых примесей и неметаллических включений;
- повысить эффективность процессов раскисления и десульфурации;
- обеспечить более точное соблюдение химического состава металла;
- получать металл с принципиально новыми свойствами;
- обеспечить необходимую температуру металла перед разливкой;
- уменьшить угар дорогих легирующих элементов.
Металлургические процессы, обеспечивающие получение указанных результатов, протекают эффективнее при внепечной обработке, чем в сталеплавильных печах благодаря ряду особенностей:
- создание наиболее благоприятных термодинамических условий для развития данного процесса, в частности наводка шлака, обеспечивающего более глубокую десульфурацию;
- увеличение скорости взаимодействия с газовой фазой или шлаком вследствие дробления металла на порции (капли) с развитой контактной поверхностью;
- повышение интенсивности массопереноса в металле вследствие его дробления на порции (капли) и, следовательно, увеличение градиента концентраций растворённых в нём элементов.
Методы внепечной обработки стали могут быть условно разделены на простые (обработка одним способом) и комбинированные (обработка металла несколькими способами одновременно). К простым методам относятся:
- обработка металла вакуумом;
- продувка инертным газом;
- обработка металла синтетическим шлаком, жидкими и твёрдыми шлаковыми смесями;
- введение реагентов вглубь металла.
Основными недостатками перечисленных простых способов обработки металла являются: необходимость перегрева жидкого металла в плавильном агрегате для компенсации падения температуры металла при обработке в ковше и ограниченность воздействия на металл.
Лучшие результаты воздействия на качество металла достигаются при использовании комбинированных или комплексных способов, когда в одном или нескольких последовательно расположенных агрегатах осуществляется ряд операций. Выбор необходимого оборудования определяется той или иной технологией обработки металла.
Внепечная обработка металла комбинированными методами может производиться:
- в обычном сталеразливочном ковше;
- в сталеразливочном ковше, оборудованном для вдувания газа или газопорошковой струи снизу через смонтированные в днище устройства;
- в установке ковш-печь с крышкой (сводом), через которую опущены электроды, нагревающие металл в процессе его обработки;
- в агрегате типа конвертера с продувкой металла кислородом, аргоном;
- в агрегате типа конвертера, снабжённом оборудованием для вакуумирования расплава и т. д.
Рассмотрим различные способы внепечной обработки стали в отдельности.
Продувка стали инертным газом в ковше
Продувку металла инертным газом осуществляют или отдельно в сталеразливочном ковше или применяют как операцию, сопутствующую другим процессам. В качестве инертного газа используют в основном аргон, реже азот. При продувке массу металла пронизывают тысячи пузырей инертного газа, каждый из которых представляет собой миниатюрную вакуумную камеру, поскольку парциальные давления водорода и азота в таком пузыре равны нулю. Внутрь таких пузырей вовлекаются вредные газовые примеси, а к их поверхности прилипают неметаллические включения, которые выносятся на поверхность металла. Также при продувке инертным газом происходит интенсивное перемешивание металла и усреднение его состава. Если требуется понизить содержание углерода в металле, то к инертному газу можно добавить кислород.
Продувка инертным газом сопровождается снижением температуры металла (газ нагревается и интенсивно уносит тепло), поэтому продувку инертным газом часто используют для регулирования температуры металла в ковше.
Продувку металла осуществляют путем ввода инертного газа различными способами в нижнюю часть ковша (рис. 58).
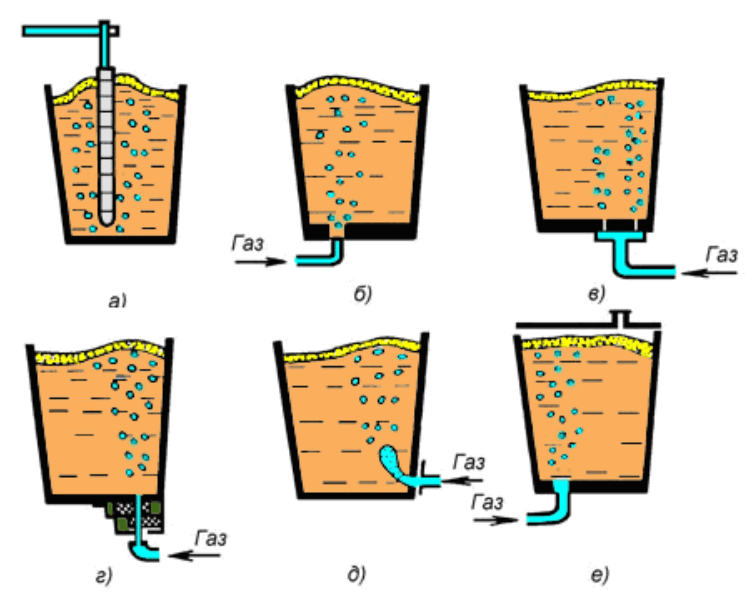
Расход инертного газа поддерживают в пределах 0,5…2,5 м3/т в зависимости от необходимой степени обработки. Совмещение продувки инертным газом с выдержкой в условиях разрежения (вакуумированием) позволяет уменьшить расход инертного газа. Применение синтетического шлака при продувке инертным газом способствует более эффективному удалению из металла вредных примесей и неметаллических включений.
Обработка синтетическими шлаками
Для интенсификации и повышения полноты перехода в шлак серы, фосфора и кислорода применяют перемешивание металла с жидким синтетическим шлаком (рис. 59).
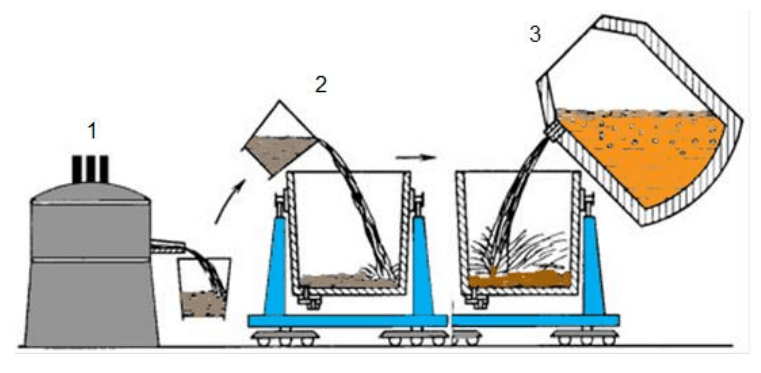
Для снижения содержания серы в металле и его раскисления применяют известково-глиноземистый шлак, для дефосфорации — известково-железистый, а для снижения содержания кислорода и оксидных включений — кислый.
Обработку ведут в ковше во время выпуска металла из сталеплавильного агрегата, одновременно из шлакового ковша подавая струю жидкого шлака на струю жидкой стали. Синтетический шлак предварительно выплавляют и нагревают до температуры ~1600 °С в электродуговой печи и перед обработкой металла выпускают в шлаковый ковш.
Расход синтетического шлака не превышает 6 % от массы металла. Такое количество шлака позволяет стабилизировать его состав и свойства и поддерживать их постоянными от плавки к плавке. Продолжительность обработки стали синтетическим шлаком ограничивается лишь длительностью выпуска металла из агрегата в ковш.
Возможно и совмещение обработки синтетическим шлаком с продувкой инертным газом или вакуумированием.
Агрегат «печь-ковш»
Наиболее эффективным приемом внепечной обработки стали является комплексная обработка расплава в сталеразливочном ковше с применением мощного высокотемпературного источника локального нагрева, который обеспечивает непрерывную компенсацию тепловых потерь. Агрегаты, обеспечивающие нагрев и перемешивание стали в ковше, ее рафинирование и корректировку химического состава, получили название «печь-ковш» (от английского ladle-furnace (LD).
Печь-ковш представляет собой установку, состоящую из крышки для ковша с отверстиями, через которые установлены три электрода. Под крышку помещается сталеразливочный ковш с металлом после выпуска из сталеплавильной печи. Кроме того, в состав установки «печь-ковш» обычно также входят средства для перемешивания металла инертным газом, система подачи ферросплавов и материалов для рафинирования стали в ковше.
В настоящее время непрерывный ввод различных веществ (углерода, раскислителей, модификаторов) проводят с применением порошковой проволоки, имеющей в своем сечении круг или прямоугольник, стальная оболочка которой обычно завальцована. Такая проволока большой длины поставляется в катушках на металлической или деревянной раме.
Ввод порошковой проволоки в расплав осуществляется по направляющей трубе с помощью специального трайбаппарата, состоящего из подающего и разматывающего устройств. Схема установки «печь-ковш» производства фирмы SMS Mevac приведена на рис. 60.
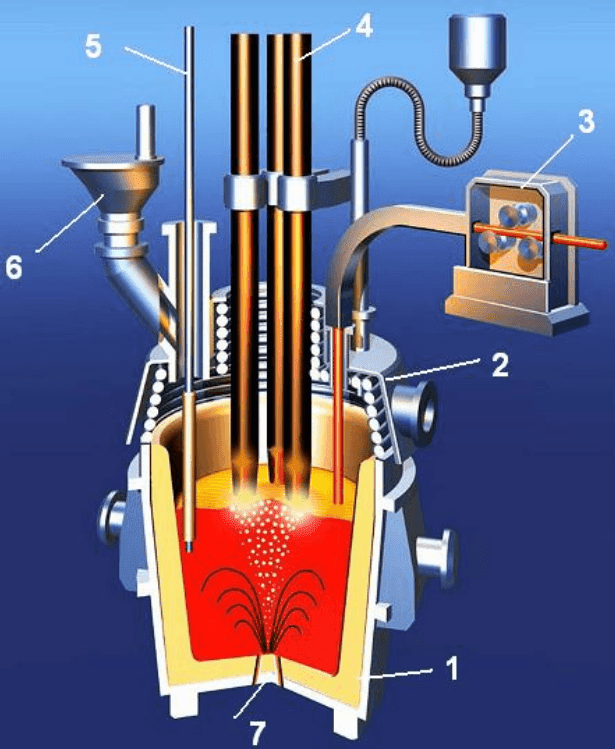
Одним из энергосберегающих способов при обработке стали на печи ковш является подача аргона через полые электроды. Данная технология позволяет сократить расход электроэнергии и угар электродов.
Обработка стали вакуумом
Вакуумирование металла осуществляют основным образом в сталеразливочном ковше. Лучшие результаты при этом получаются при вакуумировании нераскисленного металла. За счет создания разрежения над поверхностью металла происходит интенсивное выделение пузырьков растворенных в нем газов — водорода, азота и монооксида углерода. Также к поверхности этих пузырьков прилипают неметаллические включения, которые выводятся на поверхность и переходят в шлак. Кроме того, растворенный в металле кислород взаимодействует с углеродом, поэтому этот процесс используют и для получения безуглеродистых коррозионностойких сталей. После интенсивной дегазации в металл сверху из помещенного в вакуумной камере бункера вводят раскислители и легирующие добавки.
Различают две разновидности процесса:
- VD (Vacuum Degassing) — вакуумная дегазация металла;
- VOD (Vacuum Oxygen Decarburization) — вакуумно-кислородное обезуглероживание, при котором для удаления углерода из металла используют и продувку кислородом.
Однако в последнее время все большее распространение получают комбинированные агрегаты, сочетающие в себе обе разновидности.
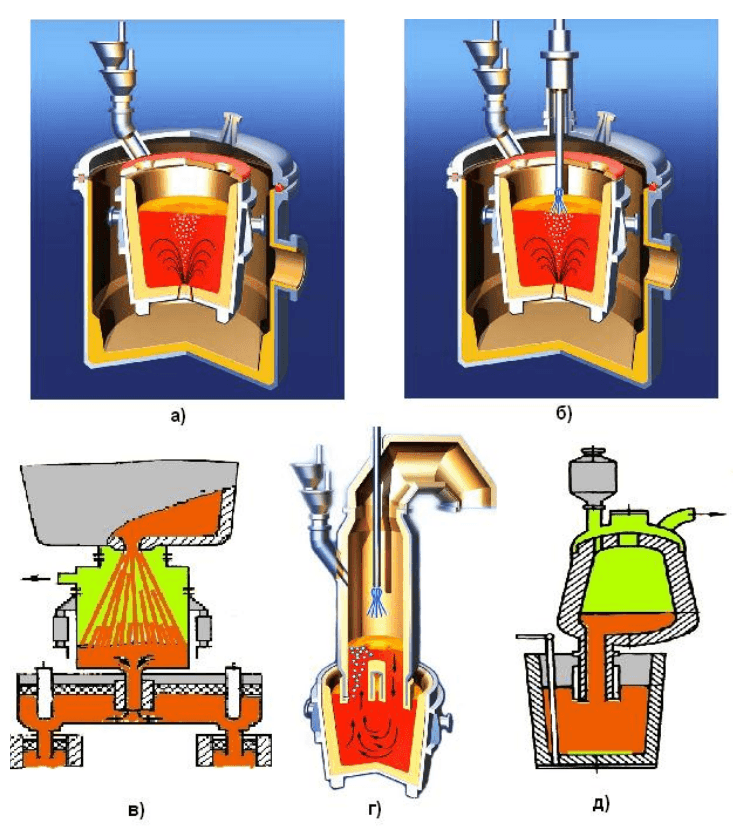
В настоящее время наиболее распространенными способами обработки металла вакуумом в ковше являются:
- помещение ковша с металлом в вакуумную камеру, последующее перемешивание металла инертным газом и ввод раскислителей из бункера, данный метод часто называют «ковшовым вакуумированием» (рис. 61, а), аналогичным образом происходит и обезуглероживание металла (рис. 61, б);
- вакуумирование при переливе из ковша в ковш или из ковша в изложницу. Поскольку обработке вакуумом подвергается «струя» металла, данный метод иногда называют «струйным вакуумированием» или «вакуумированием струи» (рис. 61, в);
- циркуляционное вакуумирование, когда металл под действием вакуума всасывается в специальную камеру, где и происходит удаление вредных примесей (рис. 61, г);
- порционное вакуумирование, при котором металла закачивается в камеру вакуумирования отдельными порциями (рис. 61, д).
Импульсно-динамическое устройство
Одним из недавно предложенных является способ внепечной обработки стали в ковше с применением импульсно-динамического устройства (ИДУ). Это устройство благодаря своей простоте существенно дешевле, чем установка печь-ковш и может выполнять ее основные функции.
Импульсно-динамическое устройство (рис. 62), представляет собой кассету (картридж), заполненную материалами, необходимыми для обработки стали в ковше. Материалы располагаются в кассете в необходимом порядке в секторах и разделены плавящимися перегородками сегментах.
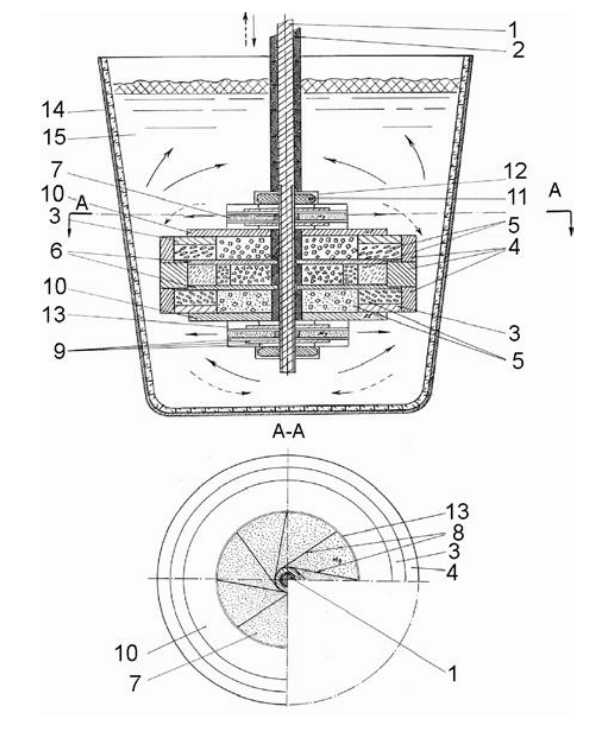
С помощью импульсно-динамического устройства возможно выполнять операции раскисления, легирования, рафинирования, модифицирования, дегазации, удаление шлака, усреднение химического состава и температуры.
Перемешивание металла в ковше осуществляется за счет использования реактивной энергии струйных течений, получаемых при помощи струйно-вихревых смесителей (рис. 63), работающих на основе испарения активной составляющей (Mg или Ca) и экзотермических реакций окисления примесей, что позволяет рассчитывать на эффективное перемешивание при рафинировании стали. Время обработки при помощи этого устройства не превышает 10 мин.
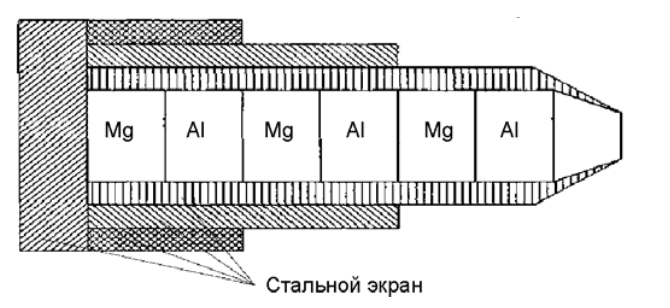
Устройство вводится в ковш с металлом при помощи подъемного механизма и экранного модуля. Во время обработки производятся попеременные подъем и опускание ИДУ с целью дополнительного перемешивания металла в ковше.
Источник: Скляр В. О. Инновационные и ресурсосберегающие технологии в металлургии. Учебное пособие. – Донецк.: ДонНТУ, 2014. – 224 с.