Проведенные в последние годы разработки процессов газификации угля, в том числе процесс Texaco газификации угольной суспензии, открывают возможность объединения установки газификации угля и шахтной установки прямого восстановления. Впервые такую комбинацию предложили на фирме «Shanghai Baosteel Согр.» и приняли решение о совместном с «Baosteel» и «Lunan Chemicals» строительстве в 1996 году полупромышленной установки для проверки этой схемы. Новый процесс получил наименование «процесс прямого восстановления BL».
В комплекс экспериментальной установки входят следующие основные элементы: установка газификации угольной суспензии Texaco (процесс TQP), установка очистки газа NHD (удаление из синтез-газа сероводорода и углекислого газа); нагреватели с шаровой насадкой для нагрева восстановительного газа до определенной температуры; шахтная установка прямого восстановления (рис. 4.40).
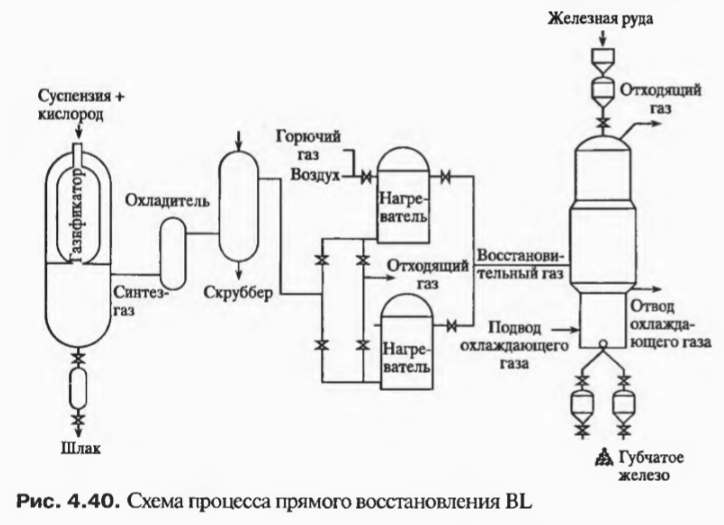
Процесс протекает следующим образом. Угольная суспензия в смеси с кислородом вдувается в газификатор, в котором образуется синтетический газ (синтез-газ), содержащий в качестве основных компонентов монооксид углерода, водород и диоксид углерода, а также водяной пар. Синтез-газ охлаждается и очищается в скруббере в зоне охлаждения установки газификации, а затем отводится из верхней камеры газификатора для последующей очистки. После очистки в скруббере из синтез-газа удаляют влагу и направляют его в установку очистки, где удаляются кислые компоненты, такие как Н2S и СO2, и происходит восстановление серы. В процессе ВL используется технология физической очистки газа по способу NHD. В результате очистки получают восстановительный газ с содержанием (Н2+СО) ≥ 95%.
Перед подачей в восстановительную установку этот газ нагревается до требуемой температуры в используемых в процессе ВЬ двух нагревателях регенеративного типа с шариковой насадкой, которые действуют поочередно в режиме нагрева насадки, а затем дутья. Восстановительная шахтная установка действует в режиме подвижного слоя с противотоком, где железосодержащие материалы загружаются в верхнюю часть через герметизированный бункер под повышенным давлением, а восстановительный газ движется в противоположном направлении, образуя восходящий поток. Восстановление железорудного сырья происходит в реакционной зоне шахты. Отходящий газ процесса восстановления отвод ится через верх шахты и после очистки в скруббере направляется в газовод и на утилизацию. Губчатое железо поступает в зону охлаждения шахтной установки, выгружается шнековым устройством и после охлаждения поступает в бункер с атмосферным давлением.
Ключевым моментом комбинации описанных выше процессов является очистка синтез-газа от кислых компонентов. Для удобства работы на установке с экспериментальными параметрами в газовой системе предусмотрен дополнительно трубопровод подачи чистого водорода, что дает возможность настраивать при необходимости химический состав восстановительного газа, задавая определенное соотношение Н и СО.
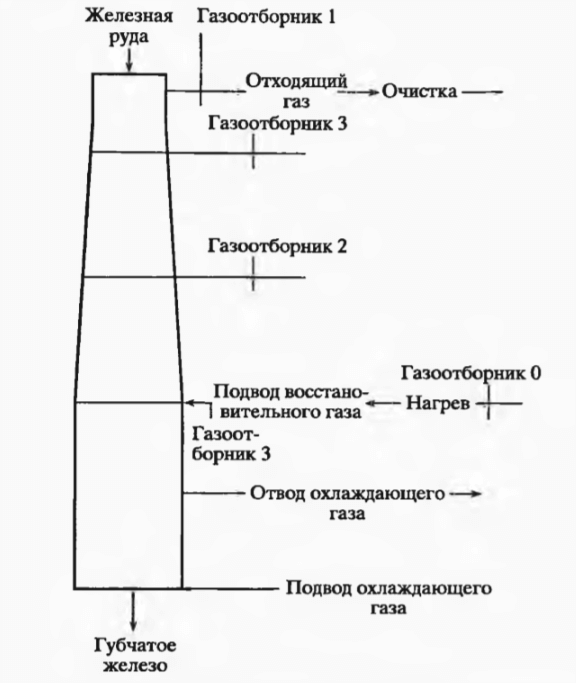
Экспериментальная установка (рис. 4.41) имеет производительность 5 т/сут восстановленного железа и оборудована системами регулирования давления и массового расхода газов, что позволяет управлять расходом и распределением газов. В шахте предусмотрены пять позиций отбора проб газа, которые обозначены на схеме как газоотборник 0, 1, 2 и т. д. Предусмотрены также средства измерения температуры отбираемого газа и температуры металлизованного продукта восстановления. Все эти средства контроля и измерения дают возможность следить за всеми параметрами процесса в шахте. Шахта является главным реакционным аппаратом в процессе BL и состоит из трех зон: зона восстановления, герметизированная зона и зона охлаждения. В восстановительной зоне шахта имеет цилиндрическую форму объемом 0,58 м3. Система загрузки шахты включает загрузочный бункер, бункер наддува и два газоуплотнительных клапана.
В верхней части шахты установлен гравитационный детектор высоты столба шихты, который контролирует степень загрузки шахты. Специально сконструированы два шнековых питателя (податчика шихты), которые установлены в нижней части герметизированной зоны и предназначены, в частности, для дробления крупных сростков, которые могут образовываться при восстановлении шихты.
В нижней части зоны охлаждения расположено шнековое разгрузочное устройство, которое выгружает продукт в два бункера разгерметизации. Отходящий газ на выходе из шахты имеет температуру около 450 °С. После очистки в скруббере отходящий газ направляется в газовую магистраль предприятия «Lunan Chemicals» и используется в производстве удобрений. Используемый в процессе BL охлаждающий газ поступает от установки для производства карбамида (отходящий газ), после охлаждения содержимого установки прямого восстановления (в зоне охлаждения) газ отводится из верхней части зоны охлаждения и направляется в газопровод на утилизацию.
Особенности шахтной установки
Шахтная установка имеет следующие отличительные особенности:
- относительно высокое рабочее давление в шахте BL равное 0,15—0,4 МПа, позволяет приспособить установку к восстановительным газам различного состава и обеспечить высокую производительность;
- разделение контуров циркуляции газа, исходя из поперечного сечения и соответствующих диаметров шахты, являющихся важнейшими проектными параметрами установки, гарантирует высокую производительность, а также разделение потоков в контурах циркуляции восстановительного и охлаждающего газов исключая возможность их смешивания;
- шнековое разгрузочное устройство и питатели шихты для ритмичной работы шахтной установки способны обеспечить непрерывное опускание шихты и приводятся в действие от генератора регулируемой частоты, что позволяет легко регулировать скорость разгрузки. Питатели для шихты (податчики) также необходимы при возникновении непредвиденной ситуации во время эксперимента.
Основным сырьем при экспериментах служили окатыши CVRD, окатыши LKAB и кусковая руда Numan. Чтобы решить проблему прямой загрузки мелкозернистой руды в шахтную установку, использовали также некоторое количество окомкованного сырья и кусковой руды.
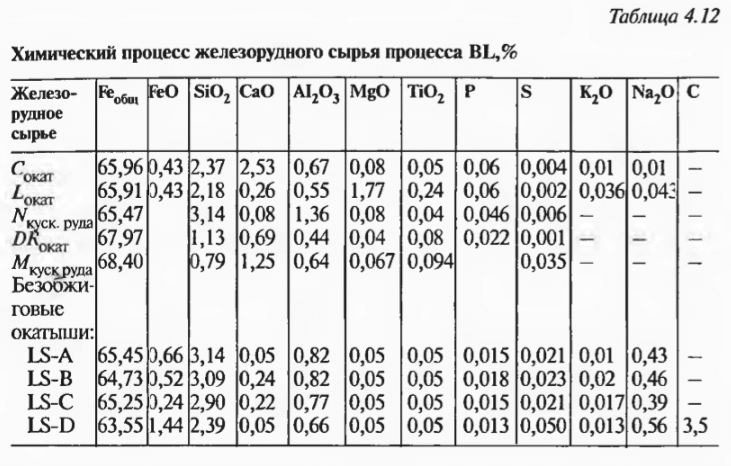
В ходе экспериментов изучали безобжиговые окатыши из пылевых руд. Для получения губчатого железа приготовили безобжиговые окатыши четырех типов: LS-A, LS-B, LS-C, LS-D. Химический состав железорудного сырья и ГЖ в экспериментах процессом BL показан в табл. 4.12 и 4.13.
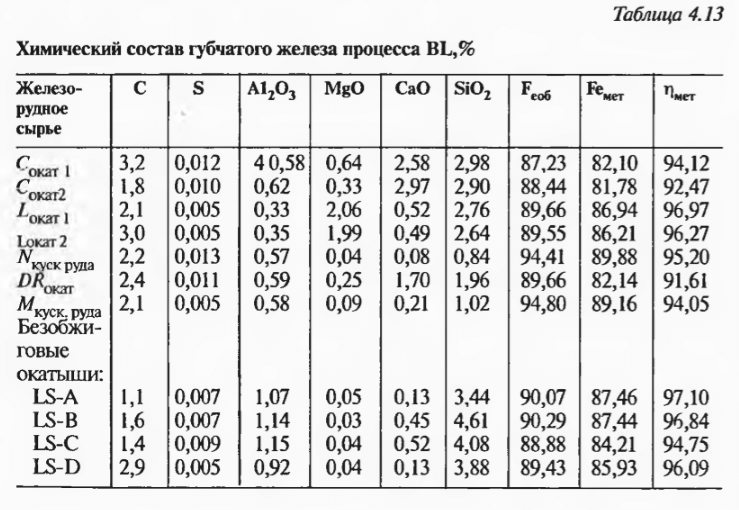
На основе данных, полученных в экспериментах, и местных цен в 1998 году определили производственные затраты, включая капитальные, которые составили приблизительно 100 дол. СШ Д/т губчатого железа. Это означает, что процесс BL экономичен в производстве губчатого железа в регионах с большими запасами каменного угля и высокими ценами на природный газ.