Использование вакуума в металлургии
С целью повышения качества стали в сталеплавильных цехах применяют вакуумную (при давлениях газа значительно ниже атмосферного) обработку металлических расплавов.
Основной характеристикой вакуума является остаточное давление в системе. Приближенную оценку остаточного давления можно давать, пользуясь понятием глубины вакуума. Условно различают низкий > 100 Па, средний 100…0,1 Па, высокий 0,1…0,0001 Па и сверхвысокий < 0,0001 Па вакуум. В вакуумных установках для выплавки и обработки стали применяют низкий, средний и высокий вакуум. Сверхвысокий вакуум в металлургии используют лишь в научных исследованиях.
В сталеплавильном производстве вакуум используют в технологических процессах, существенно разнящихся по предельным допустимым давлениям, объемам вакуумных камер, газовыделению из металла в единицу времени, содержанию пыли в удаляемых газах. В зависимости от конкретных условий установки комплектуют соответствующими системами вакуумирования. Основными элементами любой вакуумной установки, кроме рабочей камеры, в которой создается разрежение, являются насосы для эвакуации газов и приборы для измерения остаточного давления.
Вакуумные насосы
Укажем важнейшие характеристики вакуумного насоса, по которым оценивают его пригодность для данных условий.
Быстрота действия (скорость откачки) — определяется объемом газа, проходящим через сечение выпускного патрубка при данном давлении. С изменением давления в системе изменяется и быстрота действия насосов (рис. 66). Характер зависимости скорости откачки от давления определяет целесообразность использования тех или иных насосов в требуемом диапазоне давлений.
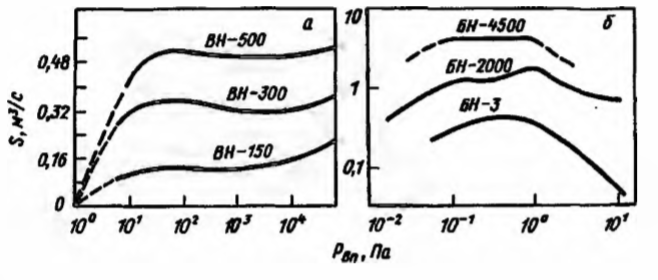
Начальное давление — выпускное давление, начиная с которого насос начинает нормально работать. Насосы некоторых типов могут работать начиная с атмосферного давления (рис. 66, а), однако существуют и насосы, которые характеризуются начальным давлениєм ниже атмосферного (рис. 66, б). Перед включением таких насосов в системе необходимо создавать предварительное разрежение (форвакуум).
Максимальное выпускное давление — предельное давление на стороне выпускного патрубка насоса, превышение которого приводит к возрастанию давления на стороне патрубка. Некоторые типы насосов не могут выбрасывать откачиваемый газ в атмосферу, и для обеспечения их нормальной работы сжатый газ со стороны выпуска необходимо удалять другими насосами.
Предельный вакуум — минимальное давление, которое может быть достигнуто данным насосом.
Принцип работы насосов разных типов в значительной мере определяется характером движения газов в диапазоне рабочих давлений насоса. В зависимости от степени разрежения движение газа может происходить в турбулентном, инерционном, вязкостном, молекулярно-вязкостном или молекулярном режимах.
В начальный момент откачки газовый поток характеризуется большой скоростью истечения и наличием завихрений, т. е. его движение происходит в турбулентном режиме. С увеличением давлення и скорости истечения завихрения исчезают, а режим движения определяется силами инерции газовой среды, вследствие чего его называют инерционным. При дальнейшем понижении скорости истечения инерционный режим переходит в вязкостный. При этом режиме газ у стенок почти не движется, а по мере удаления от стенок одни слои газа скользят относительно других. Скорость потока в этом случае не достигает максимума в центре трубопровода. Характер движения такого потока определяется вязкостью газа. В области низких давлений, когда длина свободного пробега молекул становится соизмеримой с диаметром трубопровода, молекулы перемещаются, почти не взаимодействуя одна с другой. При этом влияние внутреннего третя (вязкости) несущественно, и поток движется в молекулярном режиме. В переходном от вязкого к молекулярному режиму наряду с внутренним трением газа наблюдается независимое движение молекул.
В зависимости от диапазона давлений, в пределах которого достигается максимальная производительность, насосы подразделяют на форвакуумные, высоковакуумные и бустерные (промежуточного разрежения). В металлургии получили распространение насосы, которые по принципу действия могут быть разделены на две группы:
- механические с вращающимся ротором, действие которых основано на вытеснении движущимися частями газа, заполняющего рабочий объем;
- пароструйные, в которых используется эжектирующее действие струи пара рабочей жидкости в результате диффузии молекул газа в струю или вязкостного захвата их.
В механических насосах возможен прорыв газа через зазоры между трущимися частями со стороны сжатия на сторону выпуска. Для уплотнения зазоров и смазки трущихся деталей в насосах многих типов применяют специальное вакуумное масло. Эти насосы образуют группу механических масляных насосов. Кроме того, имеются сухие механические насосы, в которых масло для уплотнения не применяют.
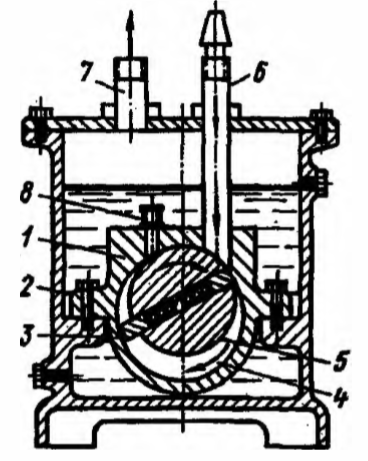
Из масляных насосов нашли широкое применение пластинчато-роторные, пластинчато-статорные и золотниковые насосы. В корпусе пластинчато-роторного насоса (рис. 67) вращается эксцентрично расположенный ротор, в пазах которого находятся две пластины. Пружиной пластины прижимаются к стенкам корпуса. Точки касания пластин и ротора стенок камеры делят рабочий объем камеры на несколько частей: увеличивающийся при вращении объем впуска, уменьшающийся объем выпуска и промежуточный. В результате увеличения объема на стороне впуска создается разрежение и откачиваемый газ из камеры засасывается в насос. На стороне выпуска газ сжимается и при давлении, превышающем давление пружины выпускного клапана, выбрасывается из насоса. Корпус насоса погружен в бак с маслом, которое, просачиваясь в насос, уплотняет зазоры и предотвращает обратный прорыв газа. Одновременно масло охлаждает трущиеся часта насоса и препятствует поступлению газа в насос из атмосферы. В пластинчато-статорных насосах (рис. 68) ротор эксцентрично насажен на ось, совпадающую с геометрической осью камеры. Точка касания ротора стенок камеры описывает при вращении окружность. Для уменьшения трения ротор изготовляют по типу роликового подшипника. Точка касания ротора стенок камеры и пластина, проходящая через паз в статоре и прижимаемая к ротору пружиной, делят рабочую камеру на объемы впуска и выпуска. Газ засасывается на стороне впуска, сжимается и через выхлопные клапан и патрубок выбрасывается из насоса.
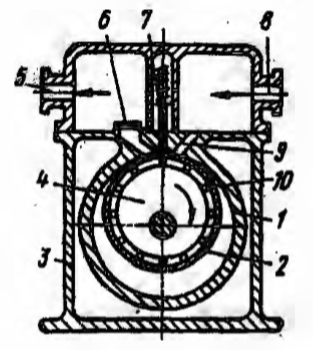
Производительность всех механических насосов определяется объемом рабочей камеры и скоростью вращения ротора. В пластинчато-роторных и пластинчато-статорных насосах между подвижными частями возникают значительные силы трения, что ограничивает возможную скорость вращения ротора и соответственно производительность насоса. Поэтому производительность насосов этих типов невелика, и их используют либр как вспомогательные, либо как самостоятельные для создания разрежения до 1 Па в системах с малым объемом. Из этой группы насосов наибольшее распространение получили пластинчато-роторный ВН-494 и пластинчато- статорные ВН-461 и РВН-20 насосы.
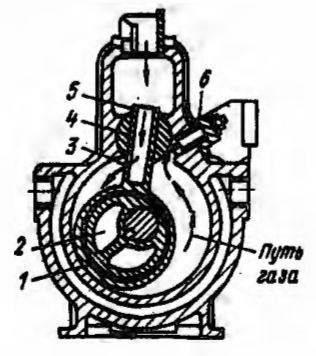
Значительно более производительными являются масляные насосы золотникового (плунжерного) типа (рис. 69), в которых на эксцентричный ротор насажена цилиндрическая обойма, выполненная заодно с полым параллелепипедом, открытым сверху и через прорези на боковой поверхности сообщающимся с камерой насоса. При вращении ротора обойма скользит по стенке камеры, а параллелепипед совершает в золотнике возвратно-поступательное и колебательное движения. Газ через полость параллелепипеда и прорези поступает в увеличивающийся объем выпуска, затем сжимается и выбрасывается через выпускной клапан.
В этих насосах параллелепипед выполняет роль впускного канала и разграничивающей пластины. Отсутствие пластин, а следовательно, и трения между их торцами и ротором позволит увеличить число оборотов и повысить производительность насоса. Насосы этого типа (ВН-10-2; ВН-20-1; ВН-150; ВН-300; ВН-500) имеют быстроту действия десятки и сотни литров в секунду (см. рис. 66, а), и их широко применяют в промышленных установках для создания разрежения до 1 Па.
Механические насосы всех типов с масляным уплотнением не приспособлены для откачки паро-газовых смесей, в частности влажного воздуха. В этих насосах к моменту открытия выпускного клапана газ сжимается и степень сжатия его может достичь 700. При этом водяной пар, если даже его парциальное давление в камере, из которой он откачивается, невелико, конденсируется, вода смешивается с маслом и вместе с ним попадает на сторону впуска. Там вода вновь испаряется и совершает новый кругооборот.
Для удаления влажного воздуха масляные насосы снабжают газобалластными устройствами, при помощи которых в определенный момент в объем сжатия подается некоторое количество сухого атмосферного воздуха. За счет балластного газа выпускной клапан открывается прежде, чем парциальное давление достигает точки росы, и из насоса выбрасываются и газ, и пары.
Применение газобалласта уменьшает быстроту действия насосов и снижает предельный вакуум, но расширяет возможности использования насосов. В насосах с масляным уплотнением используют специальное вакуумное масло ВМ-4 и ВМ-6, представляющее собой машинное масло, из которого в результате вакуумной перегонки удалены низкокипящие фракции. В процессе работы в местах трения вследствие местных перегревов происходит разложение масла, в результате которого в масле вновь появляются легкие углеводороды. Они увеличивают упругость паров и снижают предельный вакуум, создаваемый насосом. Кроме того, вакуумное масло способно поглощать влагу и окисляться, теряя первоначальные свойства. Поэтому масло в вакуумных насосах необходимо периодически заменять. Наряду с масляными насосами в металлургических установках иногда применяются сухие механические насосы.
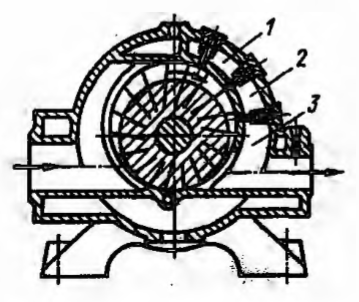
На рис. 70 показан разрез сухого многопластинчатого насоса. Большое число пластин, свободно перемещающихся в пазах ротора, при его вращении центробежными силами прижимается к стенкам камеры. Вследствие эксцентричного расположения ротора объем, заключенный между двумя соседними пластинами, стенками камеры и поверхностью ротора, при вращении ротора все время изменяется, увеличиваясь на стороне впуска и уменьшаясь на стороне выпуска. В результате этого газ сжимается, и между сторонами впуска и выпуска поддерживается перепад давлений. Для предохранения от чрезмерного сжатия газа при работе в области высоких давлений на стороне впуска со стороны выпуска в корпус вмонтированы предохранительные клапаны (1-3).
На металлургических заводах получили распространение одноступенчатые (РВН-25; РВН-50; РВН-75) и двухступенчатые (ДРВН-25; ДРВН-50; ДРВН- 75) насосы этого типа. Цифры в маркировке насоса указывают его производительность, м3/мин, при разрежении 87 и 98% соответственно. Предельное разрежение, создаваемое одноступенчатыми насосами, достигает 98 %, двухступенчатыми — 99,5 %, что соответствует 2…0,5 кПа. Многоступенчатые насосы применяют в качестве вспомогательных для быстрого удаления основного количества газа из больших объемов, а также в качестве самостоятельных в системах, не требующих большого разрежения, но характеризующихся значительным газовыделением.
В последнее время все более применяются двухроторные сухие механические насосы серии ДВН или насосы Рута (рис. 71).
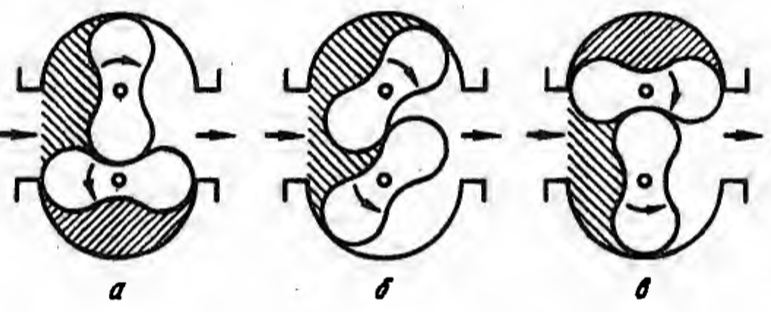
В рабочей камере такого насоса синхронно встречно вращаются две восьмеркообразные лопасти, приводимые в движение через шестеренную передачу от общего вала. Благодаря точному исполнению и регулировке лопасти при вращении не касаются одна другой и стен камеры, сохраняя зазоры порядка десятых долей миллиметра. Отсутствие трения между движущимися частями позволяет вращать лопасти со скоростью 2500…3000 об/мин, что обеспечивает высокую производительность насосов.
При сжатии газа через неуплотненные зазоры возможен его обратный прорыв, поэтому коэффициент сжатия газа в этих насосах, как правило, составляет 10…50, и давление на впуске определяется давлением выхлопа. Использование двухступенчатых насосов Рута в сочетании с механическим масляным, подключенным последовательно со стороны выпуска, позволяет получать предельное разрежение ~ 10-2 Па. В настоящее время в нашей стране выпускают высокопроизводительные двухроторные насосы, скорость откачки которых в интервале давлений 100…5 Па достигает 5 м3/с. Эти насосы целесообразно использовать в качестве бустерных в сочетании с механическими масляными.
В металлургических вакуумных установках широко используют также пароструйные насосы, важным преимуществом которых является отсутствие в них движущихся частей. В связи с этим пароструйные насосы более долговечны, характеризуются высокой производительностью, менее чувствительны к содержанию в откачиваемых газах металлургической пыли и паров воды.
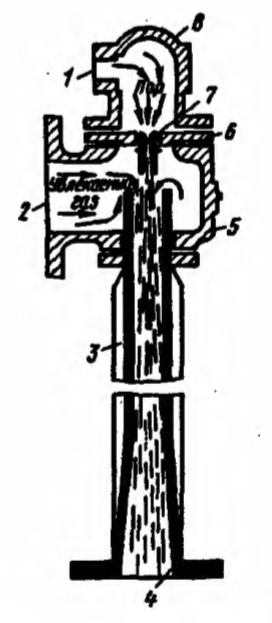
1 — впускное отверстие, 2 — впускной патрубок удаляемого газа, 3 — диффузор, 4 — выпускной патрубок, 5 — воздушная камера, 6 — фланец сопла, 7 — паровое сопло, 8 — паровая камера
Пароструйные насосы по принципу работы в свою очередь подразделяют на пароэжекторные и диффузионные. Принцип действия пароэжекгорного насоса (рис. 72) основан на вязкостном (под действием сил внутреннего трения) захвате газа струей рабочего пара. Пар, подводимый под давлением 0,6…3,0 МПа в паровую камеру, через специальное сопло истекает в воздушную камеру. Потенциальная энергия давления пара при этом превращается в кинетическую, и струя пара в воздушной камере движется со сверхзвуковой скоростью, увлекая близлежащие слои газа. Струя пара и газ попадают в сужающуюся часть диффузора, где скорость движения возрастает, возникают турбулентные завихрения и происходит более полное перемешивание пара и газа. В плавно расширяющейся части диффузора движение пара и газа постепенно замедляется, и кинетическая энергия струи вновь превращается в потенциальную энергию давления. Вследствие этого между входом в диффузор и выходом из него поддерживается 4—10-кратный перепад давления. Таким образом, одноступенчатый пароэжекгорный насос с выхлопом в атмосферу позволяет создавать в воздушной камере разрежение 10…20 кПа. Для получения более низких давлений насос должен быть, многоступенчатым.
Широкое распространение на металлургических заводах пароэжекторных насосов объясняется дешевизной водяного пара, его однородностью, возможностью практически неограниченного его потребления, позволяющими проектировать пароводяные насосы на любую требуемую скорость откачки газа (до сотен тысяч литров в секунду). Их можно изготовлять из любых материалов и откачивать любые газы, в том числе агрессивные и загрязненные пылью, причем установка фильтров перед ними необязательна, и поэтому предоставляется возможность полностью использовать их производительность. Они дешевы в эксплуатации, могут работать на отработанном паре ТЭЦ и котельных. Для их установки в цехе не требуется дополнительных площадей, так как отдельные элементы насоса могут быть размещены по стенам, колоннам, потолкам как внутри цеха, так и снаружи его.
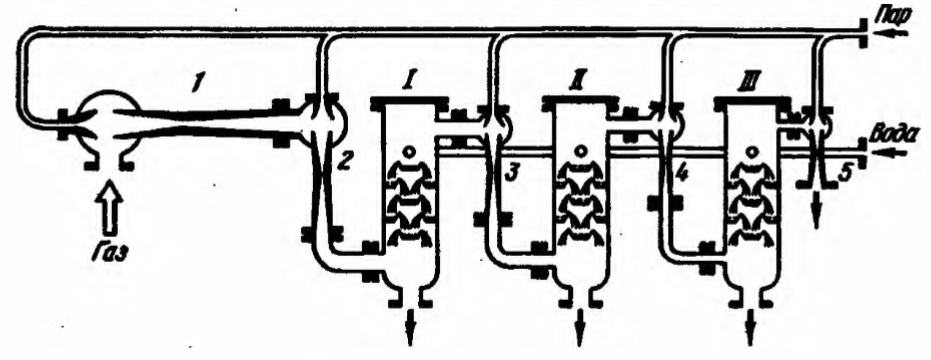
На рис. 73 представлена схема типичного пятиступенчатого пароэжекторного насоса. В многоступенчатых насосах для уменьшения расхода пара целесообразно устанавливать за эжекторной ступенью промежуточный конденсатор, в котором пар охлаждается водой, конденсируется и исключается из процесса дальнейшей откачки, а газ откачивается следующей ступенью. Однако в этом случае давление, создаваемое предыдущей ступенью, зависит от температуры воды в конденсаторе, так как давление на выхлопе не может быть меньше давления насыщенного пара охлаждающей воды в конденсаторе. При температуре воды 25…30 °С это давление составляет ~4 кПа. Следовательно, при коэффициенте сжатия 4…10 давление на входе не может быть менее 0,4…1 кПа. Для создания более низкого давления за первой ступенью конденсатор не устанавливают, а давление за ней обусловливается производительностью следующей ступени. Такая установка позволяет получать давление 60…130 Па. Устанавливая две, три и более ступеней без конденсации, при помощи пяти-шестиступенчатых насосов можно создавать разрежение до 10 мПа. Но отсутствие конденсаторов существенно увеличивает расход пара.
В пароэжекторных насосах наибольшее распространение получили так называемые барометрические конденсаторы смещения, принцип работы которых показан на рис. 73. Недостатком конденсаторов этого типа является необходимость отвода воды по барометрическим трубкам высотой > 10 м, обеспечивающим водяной затвор во избежание прорыва в насос атмосферного воздуха, поэтому эти конденсаторы необходимо размещать на высоте не менее 11 м от уровня воды в дренажном колодце. При включении пароэжекторных насосов пар подают вначале в последнюю ступень, а затем последовательно включают остальные, заканчивая первой. Многоступенчатые пароэжекторные насосы широко применяют в установках для внепечной дегазации стали. За рубежом пяти-шестиступенчатые насосы, работающие при давлениях 10…1 Па, применяют и в установках дуговых и индукционных плавильных печей, а также в качестве выхлопных ступеней диффузионных насосов.
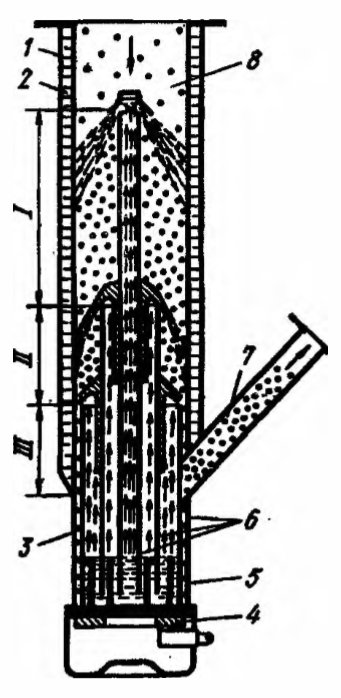
На рис. 74 представлена схема диффузионного паромасляного насоса. Насос имеет водоохлаждаемый металлический корпус в виде цилиндра с глухим днищем, в которое вставлены паропроводы с соплами. Рабочую жидкость заливают в кипятильник, и она подогревается электроподогревателем. Пары жидкости поднимаются по паропроводам к соплам, выходят через них в объем насоса и конденсируются на стенках, а образующийся конденсат по стенкам стекает вниз и вновь попадает в кипятильник.
В результате постоянного испарения и конденсации рабочей жидкости между паропроводами и объемом насоса поддерживается значительный перепад давлений. Вследствие этого, а также благодаря специальной конструкции сопел пар истекает в объем корпуса насоса со сверхзвуковой скоростью. Молекулы откачиваемого газа диффундируют в струю пара, при соударении с более тяжелыми частицами пара получают направленное движение вниз и к стенкам корпуса и скапливаются в зоне конденсации пара. Там они увлекаются в движение следующей ступенью откачки, последовательно сжимаются каждой ступенью, пока не попадут в зону действия насоса предварительного разрежения и удаляются из насоса.
Предельное разрежение, создаваемое диффузионными насосами, определяется числом ступеней насоса, конструкцией сопел, типом рабочей жидкости и температурой ее нагрева. В зависимости от создаваемого разрежения диффузионные насосы могут использоваться в качестве бустерных или высоковакуумных.
Обычно у диффузионных насосов предусматривают не более пяти ступеней откачки, что позволяет создавать разрежение порядка 10-5 Па. Высоковакуумные насосы характеризуются максимальной скоростью откачки при давлении 10-2…10-3 Па, бустерные — при давлении порядка 10-1 Па. Насосы обоих типов могут работать при противодавлении не более 102 Па.
В качестве рабочих жидкостей для диффузионных насосов, применяемых на металлургических заводах, получило распространение специальное вакуумное масло типа Г марок ВМ-1, ВМ-2, ВМ-3, ВМ-5, ВМ-7, представляющее собой продукт перегонки нефти, и кремнийорганические жидкости — силиконы. Недостатками нефтяных масел являются их чувствительность к перегреву и окисляемость при контакте в разогретом состоянии с воздухом. При перегреве масло разлагается с образованием легких углеводородов, в результате чего изменяются упругость паров и характеристики насоса. Окисление масла может вызвать осмоление насоса и резко изменить его характеристики. Силиконовые масла более однородны по составу и выдерживают длительное нагревание на воздухе до 150…200 °С, поэтому они более удобны для использования в диффузионных насосах. Однако использование силиконовых масел сдерживается сложностью их получения и более высокой стоимостью.
Вакуумные насосы предназначены для создания в замкнутом объеме давления ниже атмосферного. Диапазон давлений, используемых в современной вакуумной технике, очень широк: 105…10-10 Па. Существует много различных типов вакуумных насосов, которые различаются по физическим принципам, лежащим в основе их работы (рис. 2.1 ), однако ни один из них не способен эффективно функционировать во всем диапазоне давлений. В зависимости от значения давления, или глубины создаваемого вакуума, можно подразделить вакуумные насосы на два класса:
- форвакуумные насосы (диапазон давлений от атмосферного до 0,1 Па);
- высоковакуумные насосы (создают давление ниже 0,1 Па).
Форвакуумные насосы используют для предварительной откачки вакуумной камеры и последующего поддержания необходимого давления на выходе из высоковакуумных насосов. Все форвакуумные насосы являются механическими газоперекачивающими насосами объемного действия. Их применение эффективно только в условиях вязкостного режима течения откачиваемого газа. По чистоте создаваемого вакуума форвакуумные насосы подразделяют на насосы, в которых для уплотнения рабочих областей используется смазка (роторно-пластинчатые, пластинчато-статорные, плунжерные, поршневые), и насосы, в которых смазка не применяется (мембранные, спиральные, насосы Рутса, кулачковые).
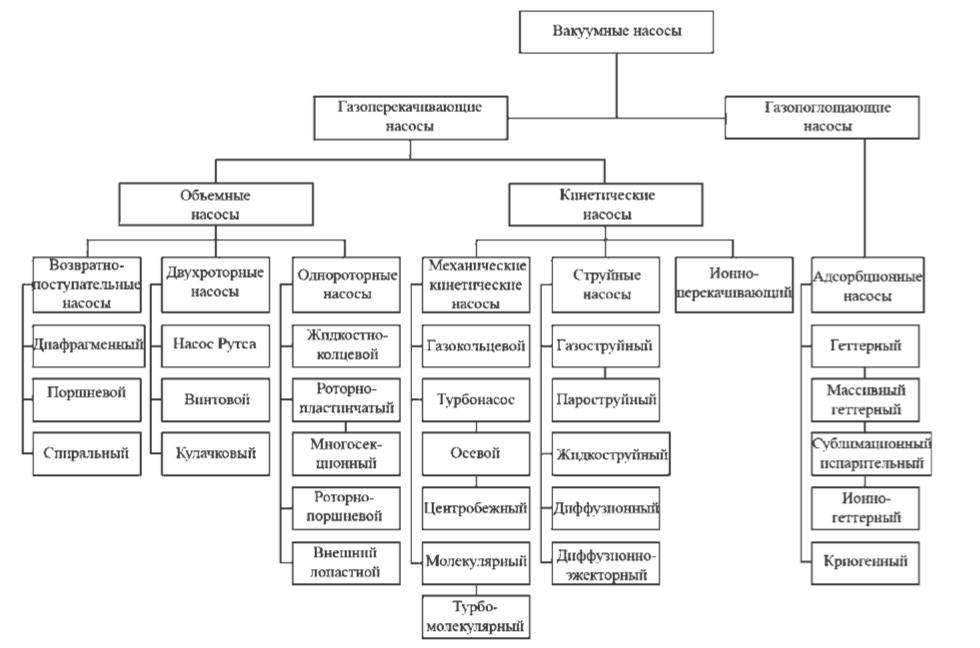
Высоковакуумные насосы служат для создания высокого и сверхвысокого вакуума в предварительно откачанной камере. Высоковакуумные насосы бывают кинетическими и газопоглощающими. В отличие от форвакуумных высоковакуумные насосы работают только в условиях молекулярного режима течения газа.
Кинетические высоковакуумные насосы удаляют газ из вакуумной камеры; в процесссе их работы требуется непрерывная откачка газа из выходного патрубка, в то время как газопоглощающие насосы «связывают» газ внутри себя. Такие насосы нуждаются в периодической регенерации, или замене поглощающего материала.
Роторно-пластинчатый насос
Роторно-пластинчатый насос в настоящее время является наиболее распространенным типом форвакуумных насосов. Такие насосы есть в ассортименте всех крупных производителей откачных средств. Они применяются для откачки воздуха и неагрессивных газов в диапазоне давлений от атмосферного до среднего вакуума и часто обеспечивают предварительное разрежение для высоковакуумных насосов в системах, в которых не предъявляются высокие требования к содержанию углеводородов в остаточной атмосфере.
Роторно-пластинчатый насос представляет собой машину объемного действия, в которой откачка осуществляется в результате сжатия газа в рабочих полостях переменного объема (рис. 2.2). Он состоит из корпуса, в цилиндрической внутренней камере которого вращается ротор, причем ось вращения не совпадает с осью камеры. В пазах ротора установлены пластины. При вращении под воздействием центробежной силы или упругой силы пружины пластины прижимаются к стенкам камеры, благодаря чему обеспечивается непрерывное изменение объема внутренних полостей насоса.
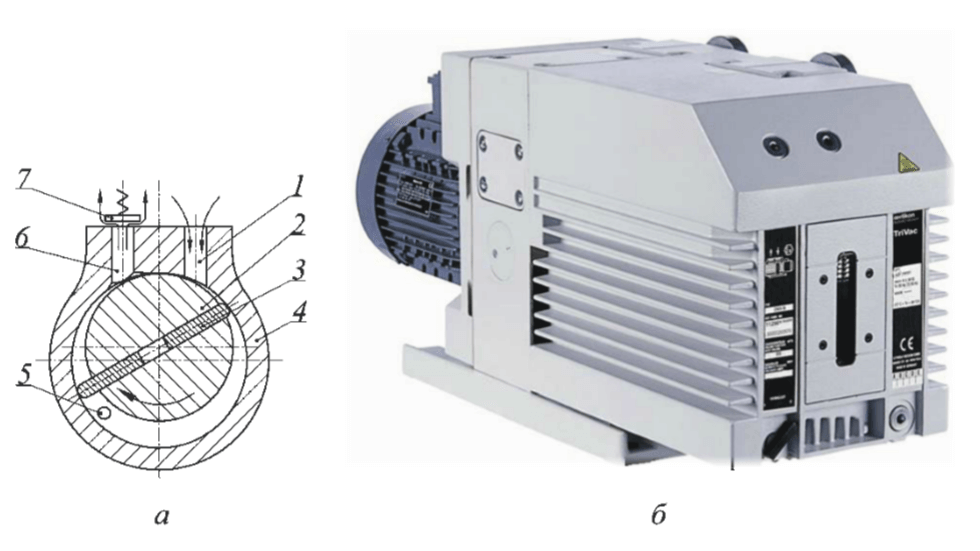
В начальный период времени объем, ограниченный ротором, корпусом и пластинами, увеличивается, и газ всасывается внутрь полости. Затем вторая пластина отсекает полость от входного патрубка и начинается сжатие газа. Когда давление достигает атмосферного, открывается выходной клапан и сжатый газ выталкивается в выхлопную магистраль.
Для снижения предельного остаточного давления применяют двухступенчатые схемы, в которых выходной патрубок первой ступени соединен с входным патрубком второй. Предельное остаточное давление роторно-пластинчатых насосов определяется отношением полезного объема к «мертвому» ( объем полости, ограниченной точкой касания ротора с корпусом, а также положением верхней точки выходного патрубка), перетеканием газа из полости выхлопа в полость всасывания, а также давлением насыщенных паров рабочей жидкости. Одноступенчатые насосы позволяют получать предельное остаточное давление 50…80 Па, а двухступенчатые — 0,25…0,40 Па. Производительность одноступенчатых насосов варьируется в диапазоне 2· 10-3 … 0,55 м3/с. Производительность двухступенчатых насосов ниже — 5 · 1о-4 … 8 · 10-2 м3/с. Типичные характеристики двухступенчатых роторнопластинчатых насосов показаны на рис. 2.3.
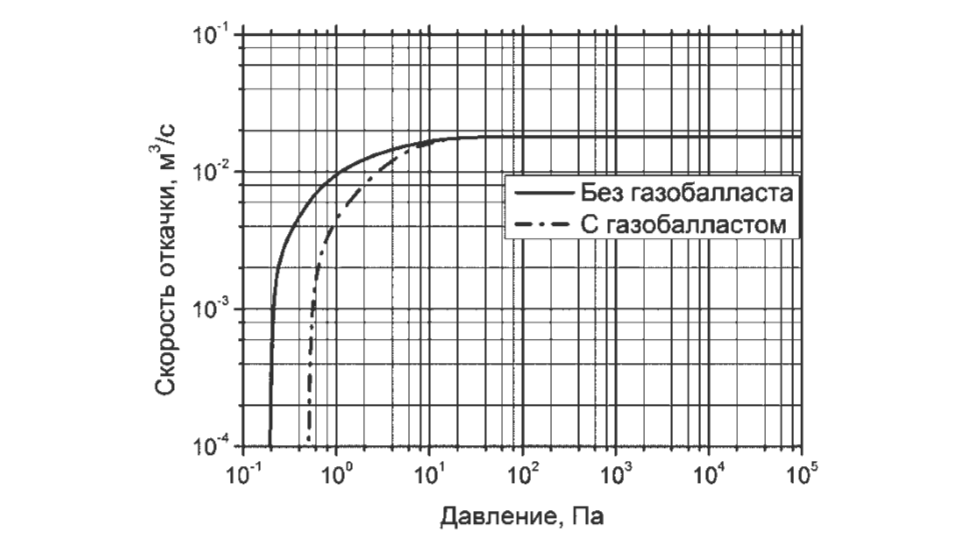
но-пластинчатого насоса производительностью 1 8· 10-2 м3/с
В большинстве роторно-пластинчатых насосов зазоры между корпусом и пластинами, пластинами и ротором, ротором и корпусом уплотняют с помощью вакуумного масла. Это позволяет получать высокие степени сжатия, сравнительно низкое остаточное давление, а также эффективно охлаждать трущиеся поверхности. Однако пары масла проникают из насоса в вакуумную магистраль, особенно при низком давлении на входе, когда газовый поток из вязкостного становится переходным. Для многих технологических процессов, проводимых в вакуумных установках, подобное недопустимо.
Существует ряд мер, позволяющих минимизировать поток масляных паров из насоса в откачную магистраль и вакуумную камеру. Во-первых, подбирают производительность роторнопластинчатого насоса таким образом, чтобы давление во входном патрубке было максимальным, а предварительную откачку вакуумной камеры проводят до такого давления, при котором течение газа в магистрали еще не становится молекулярным (следует принимать во внимание максимальные впускное и выпускное давления высоковакуумного насоса). Во-вторых, на входной патрубок насоса устанавливают сорбционные (или охлаждаемые) лабиринтные ловушки. И, в-третьих, перед роторно-пластинчатым насосом устанавливают безмасляный двухроторный насос, который эффективно препятствует попаданию масла в вакуумную камеру.
При откачке конденсирующихся газовых смесей (например, смеси воздуха и паров воды) максимальное давление сжатия может ограничиваться давлением насыщенных паров, при достижении которого начинается конденсация (для воды, находящейся при температуре 70 °С, это давление равно 3,13·104 Па). Если это давление ниже значения, необходимого для открытия выпускного клапана, то откачка прекращается. При этом возможен ряд отрицательных последствий: загрязнение масла, ухудшение качества уплотнения и охлаждения трущихся частей, коррозия элементов насоса, гидроудары в «мертвом» объеме. Для предотвращения этого в рабочую область сразу после окончания цикла всасывания напускают балластный атмосферный воздух, пока давление не станет равным значению, при котором возможно открытие выхлопного клапана, прежде чем парциальное давление паров достигнет критического значения. Применение газового балласта повышает предельное остаточное давление примерно в 10 раз.
При правильной эксплуатации роторно-пластинчатые насосы могут проработать несколько десятков тысяч часов. Их обслуживание в основном заключается в периодической замене вакуумного масла и чистке воздушных и масляных фильтров. При первом пуске насоса и всякий раз после замены в нем масла рекомендуется дать насосу поработать с заглушенным входным патрубком и открытым газобалластным клапаном в течение как минимум 30 мин. Несмотря на то что роторно-пластинчатые насосы способны функционировать при атмосферном давлении на входе, длительная их работа в таком режиме недопустима вследствие повышенных тепловых нагрузок. Также эти насосы не допускают увеличения выходного давления выше установленного значения. Поэтому при проектировании вакуумной системы необходимо предусмотреть достаточную пропускную способность выхлопной газовой магистрали. Для предотвращения потерь масла через выходную магистраль на выходе из насоса устанавливают маслоотделитель.
Спиральный насос
Спиральный насос — это полностью безмасляный вращательный насос объемного действия с полным внутренним сжатием. Впервые конструкция спирального насоса была предложена французским инженером Леоном Круа в 1905 г., однако широкое коммерческое распространение эти насосы получили только спустя 86 лет по причине недостаточного развития механообрабатывающей промышленности тех времен.
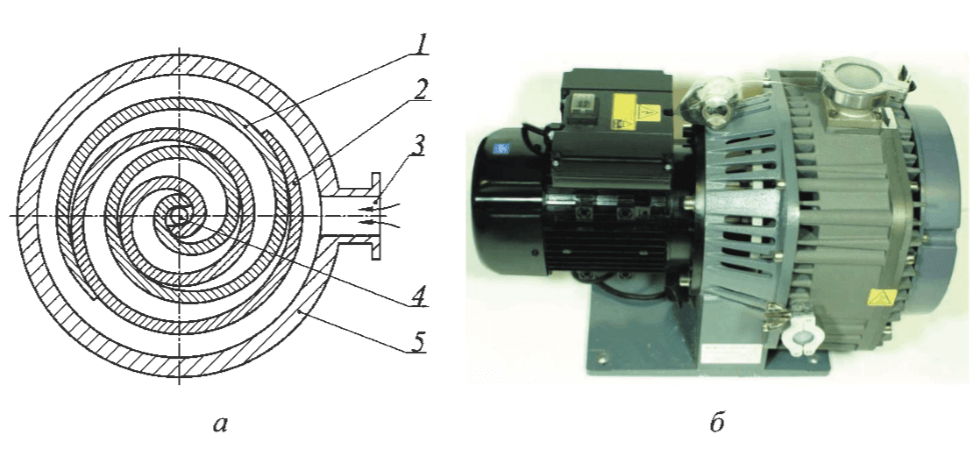
Принцип действия спирального насоса (рис. 2.4) основан на периодическом изменении объема полостей, образующихся между двумя спиралями, повернутыми друг относительно друга на 180°. Во время работы насоса подвижная спираль, установленная на эксцентриковом валу, совершает орбитальные движения вокруг выпускного отверстия. Вторая спираль неподвижна и присоединена к корпусу. Во время движения спирали недопустимо даже ее небольшое вращение относительно собственной оси, поэтому она установлена на эксцентриковом валу через специальную противоповоротную муфту.
Чтобы отделить полости насоса, контактирующие с откачиваемой средой, от смазываемых маслом механизмов привода, подвижную спираль соединяют с корпусом с помощью металлического сильфона большого диаметра. Благодаря этому полностью исключена возможность попадания паров масла в вакуумную камеру.
При движении две спирали не касаются, но в некоторых местах подходят друг к другу очень близко (зазор может составлять 0,10..0,01 мм и менее). В результате этого образуется ряд полостей, объем которых при движении спирали непрерывно уменьшается от периферии к центру системы. Входной патрубок насоса находится на боковой стороне корпуса, а выходное отверстие — в центре неподвижной спирали. Для предотвращения перетечек торцы спиралей уплотняют фторопластовыми уплотнителями.
Благодаря конструкции спирального насоса в нем практически отсутствуют «мертвые» объемы и степень сжатия ограничивается в основном перетечками газа между соседними полостями сквозь малые зазоры, образованные подвижной и неподвижной спиралями. Однако такие перетечки сравнительно невелики, что объясняется большим числом полостей и, следовательно, небольшой разницей давлений между ними, а также малой проводимостью щелевых каналов. Благодаря этому современные спиральные насосы обеспечивают достаточно низкие значения остаточного давления. Их типичные откачные характеристики показаны на рис. 2.5. Предельное остаточное давление таких насосов может составлять менее 1,33 Па. Производительность спиральных насосов лежит в диапазоне 1,0· 10-3 … 1,8· 10-2 м3/с.
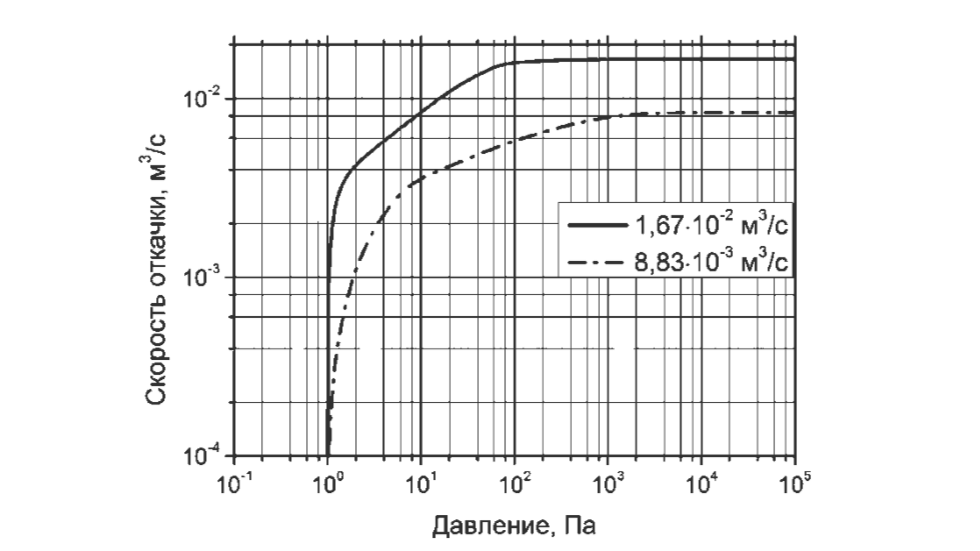
Конструкции большинства спиральных насосов исключают контакт откачиваемой среды и элементов приводного механизма, а также любые утечки газа через зазоры. Такие насосы можно применять для откачки агрессивных и опасных сред. Спиральные насосы работают в сверхчистых системах, где недопустимо попадание в вакуумную камеру даже небольшого количества углеводородов. Благодаря высокой производительности и низкому остаточному давлению их можно использовать в качестве насосов предварительного разрежения для любых типов высоковакуумных насосов. Большинство спиральных насосов выпускается со встроенным газобалластным устройством, что позволяет применять их для регенерации криогенных насосов, особенно чувствительных к парам масла.
Благодаря малому трению в механических узлах и отсутствию контакта между спиралями для работы спиральных насосов требуются значительно меньшие затраты электроэнергии, чем для насосов других типов. Например, роторно-пластинчатый насос производительностью 1,3 · 10-2 м3/с оснащается электродвигателем мощностью 2,2 кВт, а спиральный насос производительностью 1,7 · 10-2 м3/с — всего 1,4 кВт. Низкая рассеиваемая мощность позволяет таким насосам неограниченно долго работать при давлении на входе, близком к атмосферному.
Надежность спиральных насосов часто определяется ресурсом сильфона, который в процессе работы постоянно испытывает деформацию. Вследствие больших нагрузок, вызванных эксцентричным движением подвижной спирали, снижается ресурс подшипников. При использовании спиральных насосов предъявляют жесткие требования к чистоте откачиваемого газа. Небольшие попавшие в насос твердые частички могут вызвать заклинивание спиралей и выход насоса из строя, поэтому в спиральных насосах всегда применяют входные фильтры.
Мембранный (диафрагменный) насос
Принцип действия мембранного насоса (рис. 2.6) напоминает принцип действия любой поршневой машины. На шатуне с помощью держателя закреплена гибкая мембрана, плотно зажатая между корпусом и головкой. В результате объем, в который поступает откачиваемый газ, герметично изолирован от приводных механизмов насоса. Шатун подсоединен к коленчатому валу, который через муфту приводится в движение электродвигателем. Движение шатуна вызывает периодическое уменьшение и увеличение объема между мембраной и головкой. При увеличении объема под воздействием перепада давлений открывается входной клапан и происходит всасывание откачиваемого газа. На обратном ходу шатуна газ сжимается и выбрасывается через выпускной клапан.
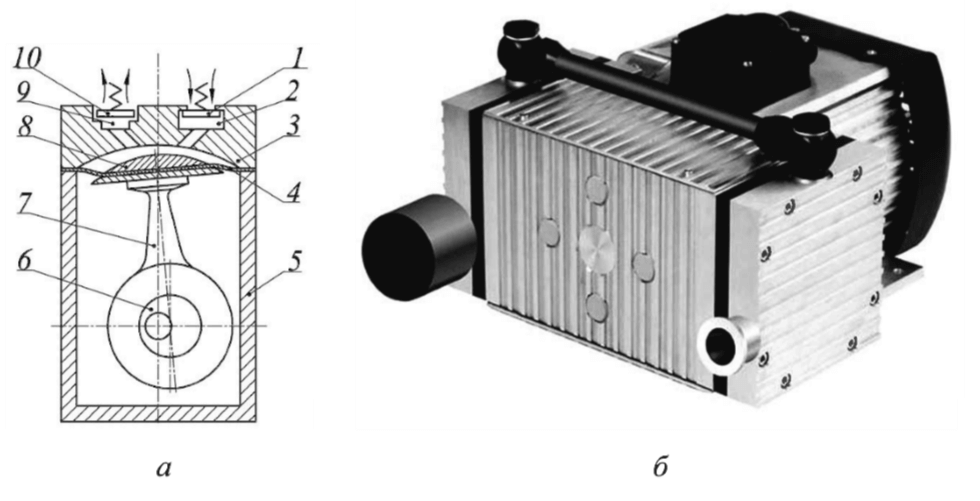
Степень сжатия мембранного насоса ограничивается «мертвым» объемом между выпускным клапаном и рабочей камерой. Обычно степень сжатия в одной ступени насоса примерно равна 10, поэтому одноступенчатые диафрагменные насосы редко способны обеспечить предельное остаточное давление ниже 9,3 · 103 Па. Чтобы преодолеть это ограничение, применяют многоступенчатые схемы с последовательным соединением ступеней. В этом случае предельное остаточное давление ограничивается эффективностью работы механических клапанов. При низких перепадах давления клапаны просто перестают открываться. Практический смысл имеет последовательное соединение на более трех-четырех ступеней. Предельное остаточное давление, достигаемое современными диафрагменными насосами, равно примерно 13,3 Па. Типичная откачная характеристика двухступенчатого мембранного насоса показана на рис. 2.7.
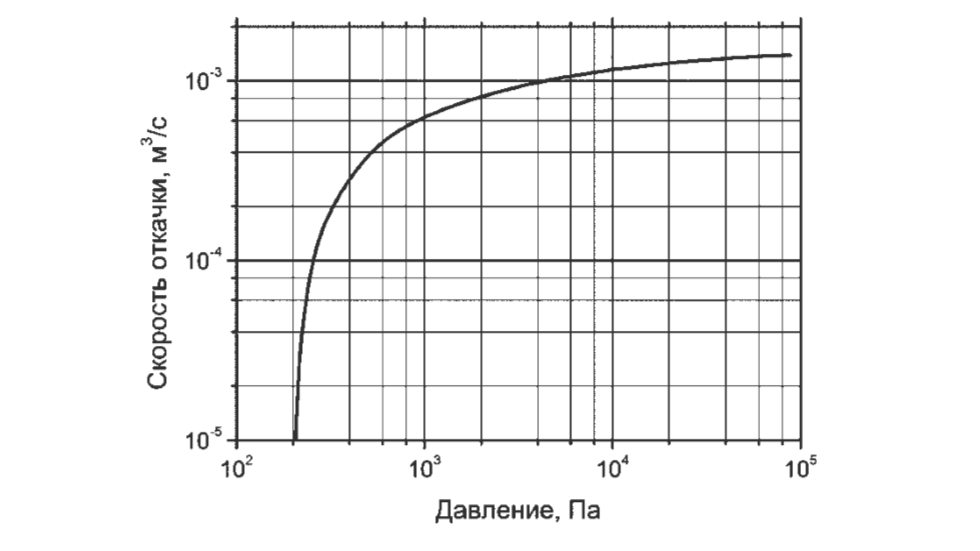
Мембранные насосы всегда имеют низкие скорости откачки. Это объясняется снижением ресурса мембраны при увеличении ее размеров. Для повышения производительности несколько ступеней насоса можно располагать параллельно. Представленные на рынке современные диафрагменные насосы имеют производительность 7,0·10-5… 3,5·10-3 м3/с.
Мембрану и другие детали, контактирующие с откачиваемым газом, часто изготовляют из химически стойких материалов либо наносят на них пассивные покрытия, благодаря чему такие насосы можно применять в откачных системах установок микроэлектронной промышленности, где используются агрессивные рабочие вещества (фтор, хлорит. д.), а также в химических лабораториях.
Небольшая быстрота откачки ограничивает применение мембранных насосов относительно небольшими лабораторными установками. Однако полное отсутствие масла в областях насоса, контактирующих с откачиваемыми газами, позволяет создавать на их основе сверхчистые сухие откачные системы. Например, сочетание мембранного насоса с двухроторным насосом Рутса позволяет значительно расширить диапазон предельных остаточных давлений и производительность системы. Такую связку можно использовать в качестве форвакуумного агрегата для турбомолекулярных насосов. Диафрагменные насосы можно использовать в качестве насосов предварительного разрежения для турбомолекулярных насосов, оснащенных молекулярной ступенью, поскольку они имеют повышенное значение выпускного давления (до нескольких тысяч паскалей).
При эксплуатации мембранных насосов нужно избегать откачки легко конденсируемых газов, так как даже незначительное количество жидкости может привести к серьезному повреждению мембраны и выходу насоса из строя. Для предотвращения конденсации рекомендуется использовать газобалластное устройство, которым, однако, оснащаются далеко не все модели. Ресурс работы диафрагменного насоса определяется ресурсом мембраны и может достигать 5000 ч, что относительно немного по сравнению с ресурсами других механических вакуумных насосов.
Насос Рутса
Производительность форвакуумных насосов рассмотренных выше типов резко уменьшается при понижении входного давления. Данного недостатка частично лишены двухроторные вакуумные насосы. Их схема впервые была предложена Рутсом в 1867 г. для воздуходувок.
Двухроторный вакуумный насос Рутса является ротационным насосом объемного действия, откачка которого обеспечивается сжатием газа. Газ в насосе сжимается в результате его нагнетания в область с повышенным давлением; откачка обеспечивается перемещением объема газа из области с низким давлением в область с более высоким давлением.
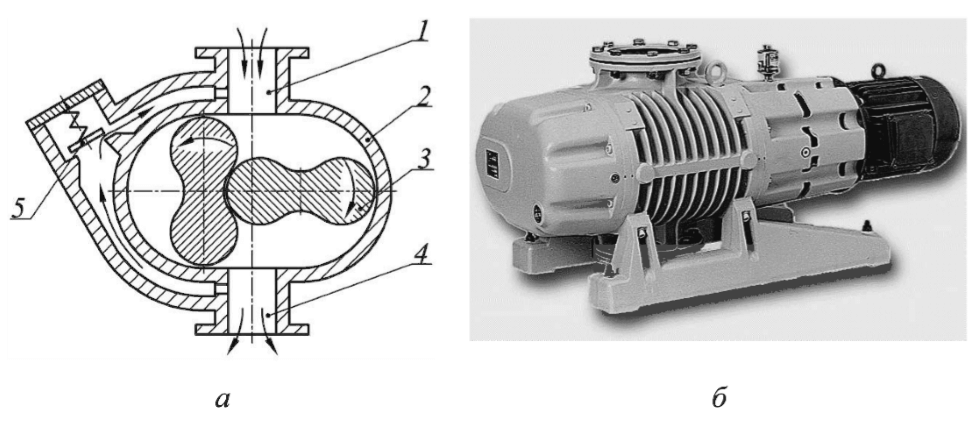
Насос Рутса (рис. 2.8) имеет два профилированных ротора, вращающихся синхронно навстречу друг другу. Профили роторов имеют специальную форму, благодаря которой при их вращении всегда сохраняется небольшой зазор между поверхностями роторов. С помощью зубчатой передачи оба ротора приводятся во вращение одним электродвигателем. Частота вращения обычно лежит в пределах 1800…3600 мин-1. Благодаря высокой точности изготовления и сборки зазоры между роторами, а также между ротором и корпусом составляют в современных насосах сотые доли миллиметра.
При вращении каждый ротор захватывает порцию газа из входного патрубка и перемещает ее в область выхлопа. В насосе с двухлопастными роторами за один поворот вала двигателя осуществляется перемещение четырех порций газа.
Область максимальной эффективности откачки и предельное остаточное давление ограничиваются перетеканием газа через зазоры между роторами, а также между роторами и корпусом. Подобное перетекание газа значительно снижает производительность насоса в области высокого давления. Наличие зазоров и отсутствие масляного уплотнения ограничивают степень сжатия насосов Рутса до значений 10…100, что намного меньше, чем у рассмотренных типов форвакуумных насосов. Насосы Рутса имеют наибольшую быстроту действия при давлении 130…0,13 Па. При одинаковых габаритах производительность насосов Рутса в этой области в десятки раз выше, чем у форвакуумных насосов других типов. Скорость откачки современных двухроторных насосов лежит в пределах 1,5·10-3 … 8 м3/с. Предельное остаточное давление достигает значения 1,33 · 10-2 Па.
При повышенном давлении на входе в насос во время сжатия газа выделяется большое количество теплоты, что может привести к заклиниванию роторов. Для предотвращения этого в современных насосах искусственно снижают степень сжатия при высоком давлении с помощью перепускного клапана. Когда разница давлений между входным и выходным патрубками становится выше допустимого значения, пружинный клапан открывается, и часть сжатого газа перетекает обратно на вход насоса. Тем самым обеспечивают оптимальный тепловой режим насоса и высокую производительность в широком диапазоне давлений.
В большинстве случаев последовательно с насосом Рутса устанавливают форвакуумный насос для откачки газа из выходного патрубка. Существуют системы, в которых благодаря применению комбинации из нескольких ступеней Рутса и нескольких двухроторных ступеней с частичным внутренним сжатием достигается возможность откачки прямо от атмосферного давления. Предельное остаточное давление таких насосов примерно 6,65 Па.
Насосы Рутса эффективно предотвращают обратный поток паров масла из форвакуумных систем в рабочую камеру, поэтому их часто применяют в паре с имеющими масляное уплотнение роторно-пластинчатыми насосами, при этом скорость откачки форвакуумного насоса должна составлять не менее 1/15 скорости откачки насоса Рутса. Выпускаются вакуумные агрегаты, в которых насос Рутса и последовательно соединенный с ним форвакуумный насос установлены на единой раме. Применение насоса Рутса расширяет возможности форвакуумных систем в области низких давлений. Характеристики таких систем приведены на рис. 2.9. Если насос Рутса оснащен перепускным клапаном, то его включают одновременно с форвакуумным насосом прямо на атмосферном давлении. Если такого клапана нет, то форвакуумный насос включают первым и откачивают им объем вакуумной камеры до давления несколько тысяч паскалей, и только потом запускают насос Рутса.
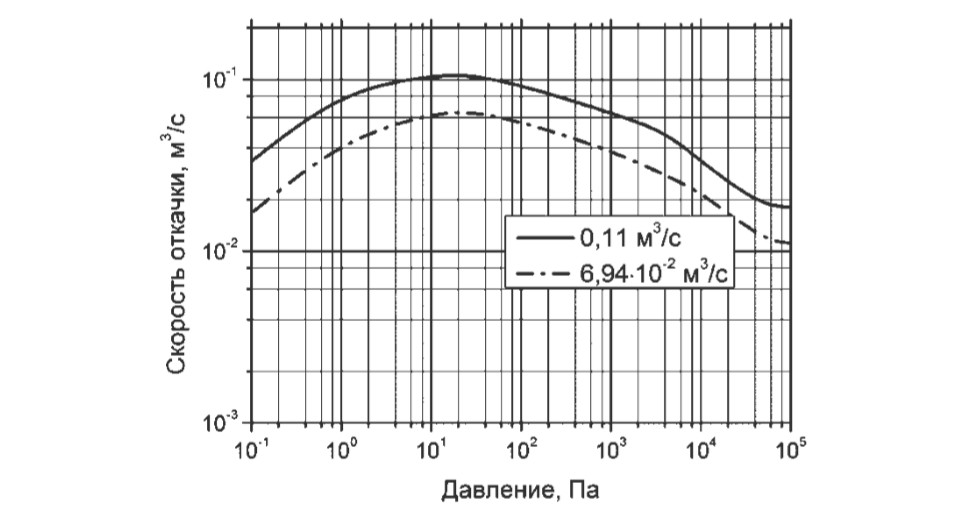
Во время эксплуатации насосов Рутса необходимо следить за тем, чтобы во входной патрубок не попадала жидкость. Даже небольшое количество жидкости, попавшей в насос, может привести к гидроудару и выходу насоса из строя. Со временем в результате износа подшипников и зубчатых колес синхронизирующей передачи зазоры в насосе постепенно изменяют форму, и при очень длительной эксплуатации его может заклинить. Поэтому насосы Рутса нуждаются в периодической замене подшипников и зубчатых колес. Часто насосы Рутса перегреваются и чрезмерно шумят.
Диффузионный насос
Диффузионные насосы являются самыми первыми промышленно выпускаемыми высоковакуумными насосами. Прообраз диффузионного насоса, изготовленный из стекла и работающий на ртути, был запатентован немецким ученым Вольфгангом Геде в 1913 г. В России производство подобных насосов началось в 1915 г. на заводе им. Федорицкого в Петрограде. В настоящее время такие насосы применяют для высоковакуумной откачки неагрессивных газов в установках, где не предъявляется повышенных требований к отсутствию паров углеводородов в рабочей камере.
Диффузионный насос является кинетическим струйным вакуумным насосом. Молекулы газа, влетающие в насос через входной патрубок, под воздействием разности концентраций диффундируют в сверхзвуковую струю пара рабочей жидкости насоса. Попав в струю, они получают от более тяжелых молекул рабочей жидкости импульс, направленный в сторону выходного сечения насоса. Парогазовая смесь движется к стенкам насоса, на которых пар конденсируется и стекает в испаритель, а молекулы откачиваемого газа продолжают движение в сторону следующей ступени насоса.
Конструкция диффузионного насоса представлена на рис. 2.10.
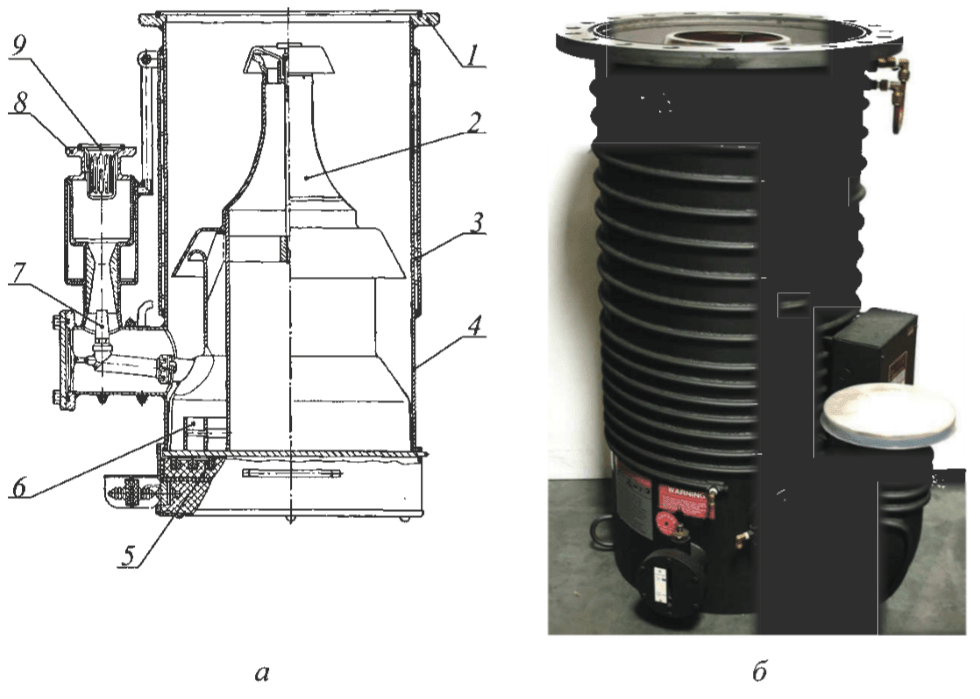
Основным элементом насоса является сопловой аппарат, установленный в корпус над испарителем. Во время работы насоса рабочая жидкость нагревается электрическим нагревателем, закрепленным снаружи на корпусе насоса, и, испаряясь, попадает в сопловой аппарат, состоящий из нескольких последовательных ступеней, которых в современных насосах от двух до пяти. Первые ступени определяют предельное остаточное давление и быстроту действия насоса, а последующие — давление в выходном патрубке и степень сжатия.
Все ступени, кроме последней, представляют собой сверхзвуковое сопло зонтичного типа. Последняя ступень всегда эжекторная, так как в области выходного патрубка давление газа столь высоко, что течение становится вязкостным, и откачка осуществляется уже не благодаря диффузии молекул в струю, а за счет трения на границе между струей и газом. В соплах пары жидкости ускоряются до сверхзвуковых скоростей и направляются в сторону охлаждаемых водой или воздухом стенок, на которых происходит конденсация. Затем рабочая жидкость стекает обратно в испаритель. Испаритель имеет лабиринтную конструкцию, благодаря чему происходит разделение фракций жидкости. Наиболее легкие составляющие имеют низкую теплоту парообразования и испаряются на периферийных участках, попадая в последние ступени насоса. Тяжелые фракции дотекают до центральной части и, испаряясь, попадают в первые ступени. На выходе из насоса всегда устанавливают маслоуловитель для предотвращения потерь рабочей жидкости через выходной патрубок.
Поскольку скорость откачки диффузионных насосов определяется эффективностью передачи импульса от молекул рабочей жидкости молекулам газа, такие насосы несколько лучше откачивают легкие газы. Скорость откачки современных диффузионных насосов может достигать 50 м3/с. Предельное остаточное давление диффузионных насосов ограничено давлением насыщенных паров рабочей жидкости и обратным потоком ее паров в вакуумную камеру. В современных насосах предельное давление лежит в диапазоне 6,65·10-3…1,33·10-8 Па. Нижний предел давления достижим только при использовании устанавливаемых перед входным патрубком насоса охлаждаемых жидким азотом ловушек, предотвращающих обратный поток паров рабочего вещества в вакуумную камеру. Типичные характеристики диффузионных насосов представлены на рис. 2.11.
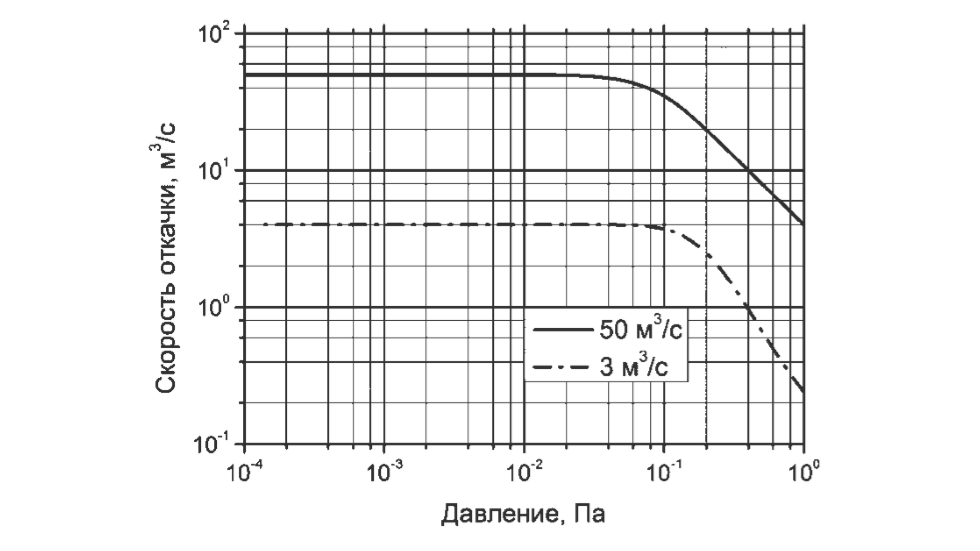
К рабочим жидкостям диффузионного насоса предъявляют ряд требований:
- низкое давление насыщенного пара при нормальных условиях и высокое при температуре испарителя;
- высокая молекулярная масса;
- термическая и термоокислительная стойкость;
- малая теплота парообразования.
В первых диффузионных насосах в качестве рабочей жидкости использовали ртуть, основными недостатками которой являются токсичность и относительно высокое давление насыщенных паров при нормальных условиях (0,16 Па). В 1928 г. впервые были применены минеральные масла, а в современных насосах часто используются кремнийорганические жидкости и полифиниловые эфиры.
Эксплуатация диффузионных насосов имеет ряд особенностей.
Диффузионные насосы не могут работать при высоких давлениях во входном сечении и тем более не терпят прорывов атмосферного давления. В случае, когда в качестве рабочей жидкости используется минеральное масло, такой прорыв приведет к его окислению и полимеризации, а иногда и к возгоранию. Эта аварийная ситуация приведет к сильному загрязнению вакуумной камеры продуктами разложения масла и на длительный срок выведет установку из строя. Для восстановления работоспособности насоса его необходимо полностью разобрать и очистить от нагара все внутренние поверхности. Последствий прорыва атмосферы в камеру можно избежать при использовании кремнийорганических жидкостей и полифиниловых эфиров, которые не окисляются и не воспламеняются на воздухе при температурах испарителя. Кроме химической стойкости эти жидкости обладают очень низким давлением насыщенных паров, однако такие жидкости на порядок дороже обычных масел.
Для работы диффузионных насосов требуется непрерывная откачка газа со стороны выходного патрубка. Максимальное допустимое выходное давление определяется давлением паров в кипятильнике и редко превышает 66 Па. Выбирая форвакуумный насос, необходимо рассчитать требуемую производительность так, чтобы давление в выходном сечении диффузионного насоса не превышало допустимого при наибольшем возможном газовом потоке. При превышении предельного выпускного давления происходит значительный выброс паров рабочей жидкости в вакуумную камеру.
Откачку диффузионного насоса допускается прекращать только на короткое время, когда форвакуумный насос используется для откачки камеры от атмосферного давления до максимального впускного давления паромасляного насоса. При этом после достижения необходимого разрежения перед открытием высоковакуумного затвора необходимо в течение некоторого времени откачивать диффузионный насос, отсеченный от вакуумной камеры. Это снизит обратный выброс паров рабочей жидкости при открытии
затвора.
Диффузионные насосы имеют низкую и нестабильную производительность при входном давлении выше 0,133 Па. Такие насосы плохо подходят для систем, в которых техпроцесс требует работы при больших газовых нагрузках и высоком рабочем давлении. Перед подключением диффузионного насоса к процессу откачки вакуумной камеры необходимо выполнить предварительное вакуумирование с помощью форвакуумного насоса.
Диффузионные насосы чрезвычайно чувствительны к качеству и чистоте рабочей жидкости. При наличии в ней растворенпых газов нормальная работоспособность насоса достигается только после многих часов работы вхолостую, когда все газы будут удалены из жидкости.
При правильной эксплуатации ресурс работы диффузионного насоса практически не ограничен, что обеспечивается отсутствием в нем движущихся частей. Насосу требуется периодическая замена рабочей жидкости, особенно при откачке агрессивных газов.
Турбомолекулярный насос
Впервые идея высоковакуумной откачки газов путем передачи его молекулам импульса от быстро движущихся поверхностей была применена в 1913 г. В. Геде при создании молекулярного насоса. Идея Геде заключалась в том, что при быстром движении поверхности, контактирующей с разреженной газовой средой, молекулы газа приобретают дополнительную скорость в направлении движения. В том же году фирма Leybold’ s Nachfolgers начала промышленное производство высоковакуумных молекулярных насосов. Эти первые насосы имели много существенных недостатков: чрезвычайно сложная (по тем временам) для изготовления конструкция, маленькая быстрота откачки и низкая надежность. Кроме того, в начале ХХ в. потребность в таких насосах была очень низкой.
Конструкция турбомолекулярного насоса, применяемая в настоящее время, была запатентована В. Беккером в 1957 г. Сегодня турбомолекулярные насосы являются наиболее распространенными насосами для получения высокого и сверхвысокого вакуума во всех отраслях промышленности. Их применяют для высоковакуумной откачки неконденсируемых газов в установках, в которых недопустимо даже малейшее присутствие молекул углеводородов в вакуумной камере.
Турбомолекулярный насос — это кинетический насос, в котором откачка осуществляется благодаря передаче молекулам газа импульса от быстро вращающихся лопастей турбины. Насос (рис. 2.12) состоит из серии чередующихся роторных и статорных лопаточных дисков, причем их лопатки расположены зеркально по отношению одна к другой. Роторные диски собраны на едином роторе, а статорные установлены в корпус. Ротор приводится во вращение с помощью высокоскоростного электродвигателя. Частоту вращения выбирают так, чтобы линейная скорость лопаток была не меньше средней тепловой скорости молекул газа. В зависимости от размеров насоса эта скорость лежит в диапазоне 20 000 … 90 000 мин-1.
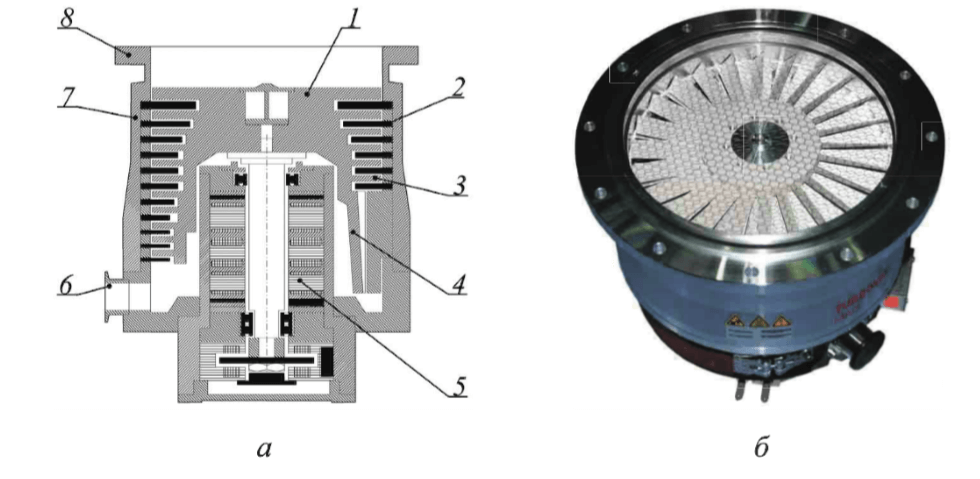
В процессе откачки молекулы, движущиеся в сторону выхлопного патрубка (рис. 2.13), проходят сквозь лопасти без соударений, а движущиеся в обратную сторону сталкиваются с поверхностью лопаток и отражаются назад. В результате проводимость насоса в прямом направлении становится значительно выше его проводимости в обратном направлении.
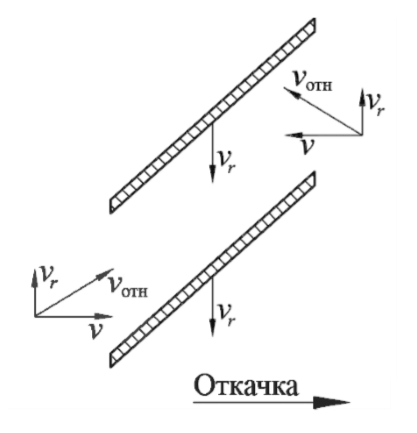
Турбомолекулярные насосы могут работать только в условиях молекулярного течения газа, поскольку для их эффективной работы необходимо, чтобы молекулы откачиваемого газа сталкивались преимущественно с лопатками ротора и статора, а не друг с другом. Поэтому такие насосы требуют предварительного разрежения вакуумной камеры и непрерывной откачки газа из выходного патрубка насоса. Максимальное давление в этом патрубке обычно не более 200 Па. Но существуют конструкции, в которых вместо последней группы дисков расположена молекулярная ступень Геде (см. рис. 2.12, а, справа от оси), благодаря чему максимальное давление форвакуумной линии достигает 5320 Па.
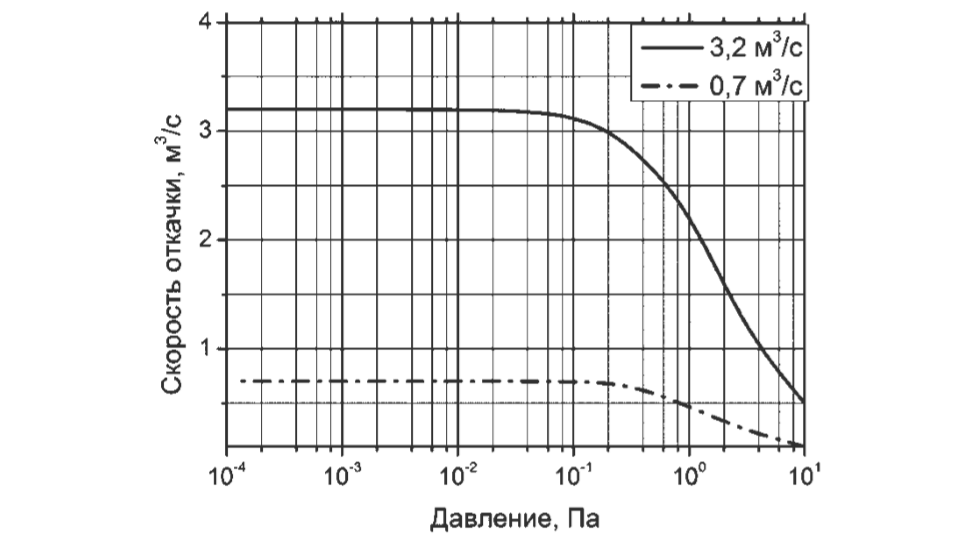
Производительность турбомолекулярных насосов лежит в диапазоне 0,01…6 м3/с. На рис. 2.14 приведены их типичные характеристики. Так как скорость теплового движения молекул сильно зависит от молекулярной массы, производительности откачки разных газов турбомолекулярным насосом различаются: легкие газы откачиваются хуже тяжелых. Предельное остаточное давление таких насосов зависит от способа уплотнения входного патрубка и лежит в диапазоне 1о-6…1o-8 Па.
Подвеска ротора в турбомолекулярных насосах может быть механической и магнитной. В насосах с механической подвеской ротор устанавливается в корпус с помощью механических подшипников, чаще всего с керамическими телами качения и консистентной смазкой. В системах, оборудованных такими насосами, редко удается полностью избавиться от проникновения молекул смазочного вещества в вакуумную камеру. Но несмотря на это, количество вносимых загрязнений намного ниже, чем у диффузионных насосов, даже если последние оборудованы криогенной ловушкой.
В турбомолекулярных насосах с магнитной подвеской ротор во время вращения не касается поверхностей статора. Механические подшипники в таких насосах используются только во время разгона ротора до скоростей, при которых возможна работа магнитного подшипника (около 5000 … 9000 мин-1). Ресурс таких насосов примерно в 2 раза выше ресурса насосов с механической подвеской. Кроме того, эти насосы не содержат смазочных материалов, поэтому не являются источниками загрязнений откачиваемого объема. Однако недостатком магнитных подшипников является повышенная чувствительность резким скачкам давления при прорыве атмосферного давления. Во время такой аварии вращающийся ротор ударяется о парковочные подшипники, что может привести к выходу их из строя. Современные насосы могут выдерживать около пяти таких ударов, затем требуется замена подшипников и ремонт ротора.
Для откачки газа из выходного патрубка турбомолекулярных насосов можно применять форвакуумные насосы любых типов при условии, что они способны обеспечить достаточно низкое давление при рабочем потоке газа. Наилучшим вариантом являются спиральные насосы и насосы Рутса. Они не содержат смазочных материалов, обладают высокими скоростями откачки и достаточно низким предельным остаточным давлением. Если допускается попадание в объем вакуумной камеры небольшого количества паров масла, в качестве форвакуумных насосов используют роторно-пластинчатые насосы.
В случае применения турбомолекулярных насосов для откачки агрессивных сред (таких как фтор и хлор, которые часто применяются в полупроводниковой промышленности) область подшипников необходимо продувать осушенным азотом или аргоном, что препятствует их контакту с откачиваемыми газами. В комплект некоторых современных насосов включены дозирующие устройства и клапаны, управляемые источником питания насоса. Подшипники турбомолекулярных насосов всегда располагаются в области, сообщающейся с выходным патрубком, поэтому продувка увеличивает нагрузку на форвакуумный насос.
Для эффективной работы и предотвращения загрязнения вакуумной камеры (особенно при использовании форвакуумных насосов с масляным уплотнением) рекомендуется придерживаться следующих правил.
- Если вакуумная камера достаточно мала и форвакуумный насос способен откачать ее до максимального входного давления турбомолекулярного насоса за короткое время (это время всегда указывается в инструкции по эксплуатации), то оба насоса включаются одновременно при открытом высоковакуумном затворе и атмосферном давлении в камере. В процессе разгона турбомолекулярного насоса откачка ведется прямо через него, и поток газа не позволяет загрязнениям из форвакуумной магистрали проникать в насос и вакуумную камеру. Когда поток в магистрали станет для этого слишком разреженным, скорость вращения ротора турбомолекулярного насоса будет достаточно высокой и молекулы загрязнений не смогут проникать сквозь него.
- Во время торможения турбомолекулярного насоса его нужно вентилировать со стороны входного патрубка до полной остановки. Это предотвращает загрязнение вакуумной камеры при пониженных скоростях вращения ротора, а также снижает время торможения ротора.
- Во время простоя давление в насосе должно быть равно атмосферному.
Современные турбомолекулярные насосы не нуждаются в периодическом обслуживании в течение всего срока эксплуатации. Последний в современных насосах с магнитным подвесом ограничен усталостными напряжениями в лопатках ротора. При достижении заявленного производителем срока эксплуатации необходима его замена, осуществляемая в специализированных сервисных центрах. В насосах с механической подвеской ресурс может ограничиваться сроком службы подшипников, но и их заменяют только в условиях сервисного центра.
Криогенный насос
Принцип действия криогенного насоса основан на том, что при охлаждении газа ниже температуры кипения давление насыщенных паров резко снижается. При соударении с охлажденной поверхностью молекулы теряют энергию и конденсируются. Отличие криогенных насосов от насосов рассмотренных выше типов заключается в том, что они не удаляют газ за пределы вакуумной камеры, а «замораживают» его на своих рабочих поверхностях. Весь газ, удаленный из камеры, остается внутри насоса.
Схема криогенного насоса представлена на рис. 2.15.
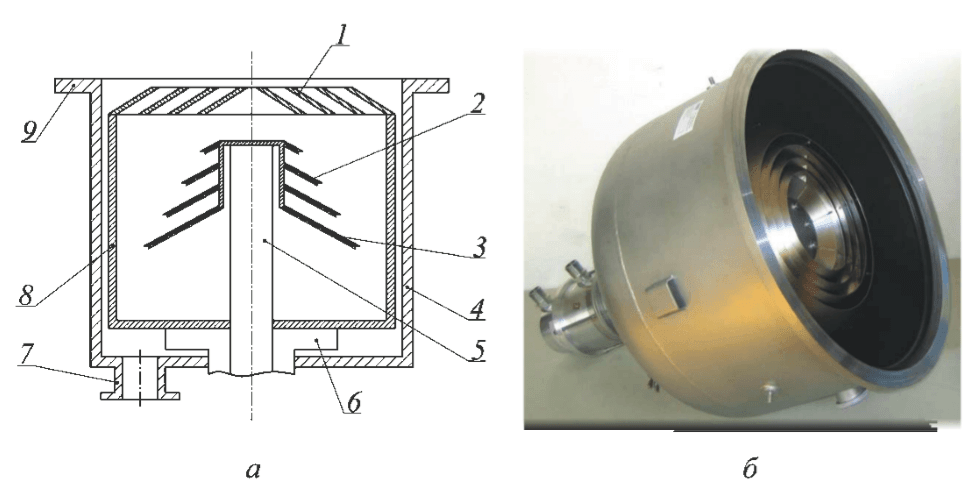
Основными откачивающими элементами насоса являются криопанели первой и второй ступеней. Первая ступень охлаждается до температуры 80 К и служит для откачки легко конденсируемых газов, паров воды и углеводородов. Температура второй ступени поддерживается равной 15 … 20 К. Эта ступень откачивает все газы, кроме водорода, гелия и неона. На входе в криогенный насос установлен оптически непрозрачный тепловой экран. Экран препятствует попаданию на криопанель второй ступени теплового излучения из объема вакуумной камеры. Тепловой экран является частью первой ступени насоса и имеет температуру 80 К. Охладитель, прокачиваемый компрессором через криоголовки, имеющие тепловой контакт с криопанелями, отводит теплоту, выделяемую при конденсации газов.
Температура конденсации водорода, гелия и неона меньше 20 К, поэтому их откачивают с помощью криосорбции. Для этого на поверхности криопанели второй ступени наносят слой активированного угля. При низких температурах легкие газы диффундируют в глубь слоя и удерживаются там при очень малом давлении насыщенных паров.
Предельное остаточное давление криогенного насоса ограничено давлением насыщенных паров откачиваемых газов при температуре криопанели первой ступени (20 К) и доходит до 1· 1o-8 Па. Производительность криогенных насосов определяется суммарной площадью криопанелей и проводимостью входных экранов и не зависит от давления. Быстрота откачки современных насосов лежит в диапазоне 0,3 … 60 м3/с. Для получения большей производительности (например, в больших установках для имитации космического пространства) криопанели большой площади вместе с теплозащитными экранами устанавливают прямо на стенки вакуумной камеры. Производительность таких систем может доходить до нескольких миллионов литров в секунду. Скорость откачки криогенных насосов больше, чем у всех высоковакуумных насосов остальных типов соответствующих размеров.
Существуют криогенные насосы, конструкция и тепловые параметры которых адаптированы для откачки конкретных газов. Например, при испытании электрических ракетных двигателей возникает необходимость в откачке большого количества ксенона. Для этого температура криопанелей должна быть ниже 65 К, поэтому обычные насосы откачивают ксенон только второй ступенью. Для увеличения производительности откачки и емкости насоса по ксенону температуру первой ступени снижают до 60 К.
Помимо производительности основными характеристиками криогенных насосов являются емкость и параметр запуска. При длительной непрерывной работе поверхности криопанелей покрываются слоем замороженных газов. Слой имеет низкую теплопроводность, и со временем производительность насоса начинает падать. Емкость — это количество газа, которое может связать насос без значительного снижения быстроты откачки. Емкость криогенного насоса зависит от типа откачиваемого газа и минимальна для гелия, неона и водорода. Например, у насоса с диаметром входного патрубка 500 мм емкость по аргону составляет 10 стандартных м3, а по водороду — всего 0,04.
При подключении насоса к вакуумной камере (при открытии высоковакуумного клапана) он подвергается значительной импульсной тепловой нагрузке, вызванной конденсацией большого потока газа. Мощность нагрузки может превысить максимальную мощность, отводимую теплоносителем, и температура панелей начнет увеличиваться, что приведет к обратным выбросам связанных газов в вакуумную камеру. Параметр запуска — это произведение давления в вакуумной камере на ее объем, при котором можно начинать откачку криогенным насосом без повышения температуры криопанелей. Например, если параметр запуска насоса равен 100 Па·м3, то при откачке вакуумной камеры объемом 0,75 м3 высоковакуумный клапан можно открывать при достижении давления 133 Па. Таким образом, в большинстве случаев для создания предварительного разрежения в вакуумной камере криогенных насосов требуется применять форвакуумные насосы. Когда давление достигнет значения, определяемого параметром запуска, форвакуумный насос можно отключать.
После достижения предельной емкости криогенный насос уже не может эффективно эксплуатироваться, требуется его регенерация. В самом простом случае достаточно отключить подачу теплоносителя и перекрыть высоковакуумный клапан. Температура насоса постепенно начнет увеличиваться, что вызовет испарение конденсированных газов. Когда давление в насосе превысит атмосферное, газ начнет выпускаться из насоса через предохранительный клапан. Такой способ регенерации не подходит для насосов, применяющихся для откачки опасных и дорогих газов. Кроме того, корпус насоса сильно охлаждается и снаружи покрывается конденсатом. Часто во время регенерации осуществляют непрерывную откачку объема насоса с помощью безмасляного форвакуумного насоса. Для уменьшения времени регенерации насос прогревают и продувают сухим инертным газом.
Криогенные насосы не имеют подвижных частей и смазки, контактирующих с откачиваемым газом, а также не требуют непрерывной поддержки форвакуумным насосом, поэтому их можно применять для создания высокого и сверхвысокого вакуума в установках, в которых предъявляются самые строгие требования к чистоте остаточной атмосферы. Однако небольшая емкость и пониженная скорость откачки легких газов несколько ограничивают область их применения и заставляют предъявлять определенные требования к эксплуатации. Например, применение гелиевого течеискателя для испытания вакуумной камеры приведет к необходимости длительной регенерации криогенного насоса.
Приборы для измерения вакуума
Манометры для измерения давления ниже атмосферного часто называют вакуумметрами. В вакуумной аппаратуре, используемой на металлургических заводах, наиболее широкое применение нашли деформационные, теплоэлектрические и ионизационные вакуумметры.
Чувствительным элементом деформационных вакуумметров является тонкостенная серповидная трубка Бурдона, мембрана или сильфон. При изменении перепада давлений внешнего (атмосферного) и внутреннего (соответствующего давлению в измеряемой системе) изменяется радиус кривизны трубки, прогиб мембраны или сильфона. Эти деформации очень малы, поэтому обычно используют усиливающие устройства, увеличивающие показания стрелки. Такими усиливающими устройствами могут быть механические системы, индукционные, емкостные датчики и т. д Деформационные вакуумметры позволяют измерять давления в интервале 1 • 105 … 1 • 10-2 Па, однако наиболее чувствительны они в области сравнительно высоких давлений и применяются, в основном, для измерения давлений от 1 • 105 до 1 • 102 Па.
Принцип работы термоэлектрических вакуумметров основан на зависимости теплопроводности разреженного газа от его плотности. Термоэлектрические вакуумметры подразделяют на термопарные и вакуумметры сопротивления (рис. 75, а, б). В термопарных вакуумметрах с изменением давления изменяется температура нити накала, подогреваемой током постоянной величины. Температура нити непрерывно измеряется термопарой, спай которой припаян к нити. По величине т. э. д. с. судят о давлении в лампе, соединенной с вакуумным объемом.
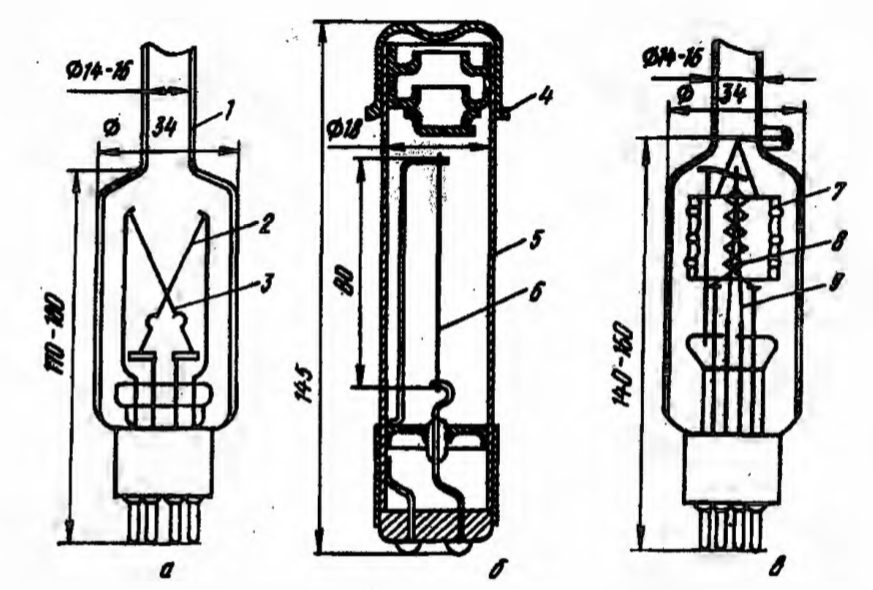
а — термопарный ЛТ-2, б — датчик сопротивления М1-6, в — ионизационный ЛМ-2, 1 — стеклянный баллон, 2 — нить накала, 3— термопара, 4 — защитный колпачок (в нерабочем состоянии), 5 — металлический корпус, 6 — рабочая нить, 7 — коллектор, 8 — сетка, 9 — катод
Термопарные датчики выпускаются в стеклянном баллоне и с платиновой нитью накала (лампа ЛТ-2) или в металлическом корпусе и с танталовой или никелевой нитью накала (лампа ЛТ-4М, термопара хромель-копелевая). В датчиках вакуумметров сопротивления при изменении давления изменяется сопротивление медной или платиновой нити, по которой пропускается стабилизированный ток. Сопротивление нити измеряют по мостовой схеме, и по степени разбалансировки моста судят о значении давления в лампе, соединенной с вакуумной системой. Датчики сопротивления также выпускают в стеклянных и металлических баллонах.
Термоэлектрические манометры позволяют измерять давление в пределах 102…10-2 Па с относительной погрешностью 10…50 %. Для измерений давлений в пределах 10-2… 10-5 Па используют ионизационные датчики. Из них наиболее распространена электронная ионизационная манометрическая лампа ЛМ-2 (см. рис. 75, в) с катодом, сеткой и коллектором ионов. Нагреваемый стабилизированным током катод эмиттирует электроны к сетке. На сетку подается положительный потенциал ∼ 200 В. Поскольку сетка выполнена из тонкой проволоки, электроны проскакивают через нее и по мере удаления тормозятся электрическим полем, а затем снова возвращаются к сетке. До попадания на сетку электроны совершают вокруг нее многократные колебания, благодаря чему увеличивается длина пробега каждого электрона.
При колебательном движении вокруг сетки электроны сталкиваются с молекулами газа и ионизируют их. Положительные ионы улавливаются коллектором — металлическим цилиндром, к которому приложен отрицательный потенциал 25 В. Количество ионов, попадающих на коллектор, при постоянном токе эмиссии зависят от плотности газа. Измеряя ионный ток, можно судить о давлении в лампе и в системе, к которой присоединена лампа. Недостатком электронных ионизационных датчиков является низкая стойкость раскаленного катода, который при повышении давления до 1 Па сгорает за несколько минут, поэтому в последнее время начали выпускать ионизационные лампы ЛМ-3 с иридиевым катодом, покрытым оксидом иттрия. Применение воздухостойкого иридиевого катода позволяет измерять давление в диапазоне от 1 до 10-5 Па при удовлетворительном сроке службы датчика.
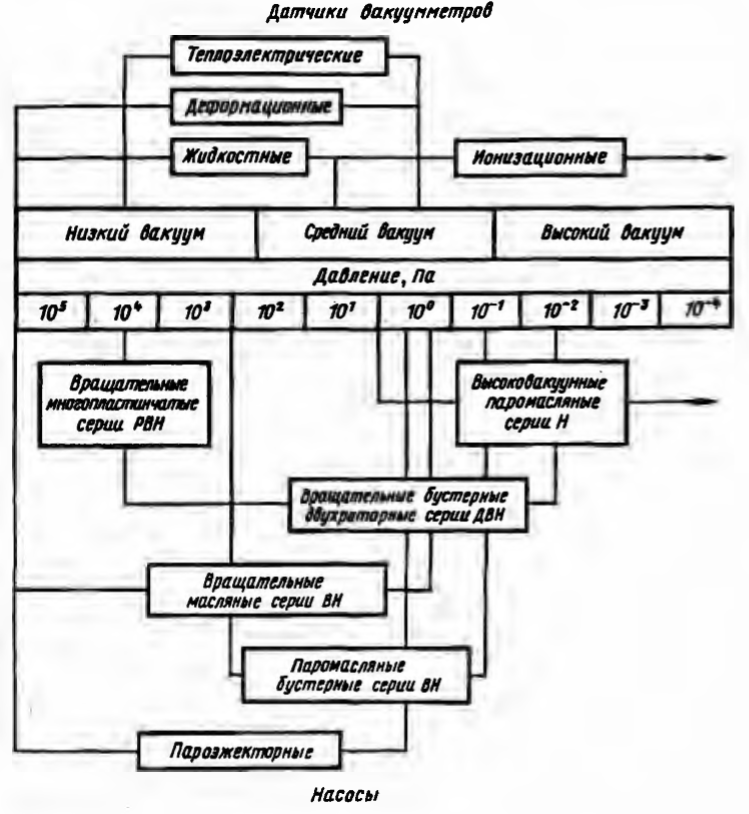
Рассмотренные конструкции вакуумных насосов и датчиков вакуумметров позволяют получать и измерять разрежение в широком диапазоне (рис. 76), обеспечивающем работу вакуумных установок металлургических заводов.
Вспомогательные элементы вакуумных систем
Типичная схема высоковакуумной установки (рис. 77), кроме вакуумной камеры 1 с вентилем 12, насосов 6 и 9, приборов для измерения разрежения 2, включает ряд вспомогательных элементов: вакуум-проводы 3 и 10, затворы 5 и 8, фильтры 11, ловушки 4, конденсаторы 7 и др.
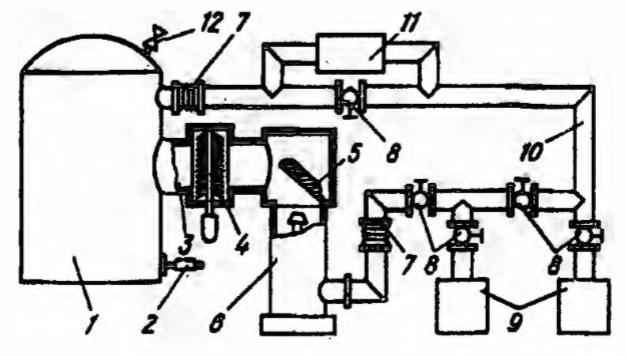
Вакуумные трубопроводы предназначены для соединения разных элементов вакуумных систем. Трубопровод должен иметь малую длину и большой внутренний диаметр, во всяком случае, условный диаметр (проход — ДУ) не должен быть меньше диаметра входного сечения насоса, так как большая длина и малый диаметр уменьшают пропускную способность системы и эффективную скорость откачки.
Вакуумные трубопроводы чаще всего выполняют из бесшовных труб из углеродистой или нержавеющей стали, а также из латуни и меди. Высоковакуумные участки 3 изготовляют, как правило, из нержавеющей стали. На стороне низкого и среднего разрежения широко применяют вакуумные шланги из специальных сортов вакуумной резины, которой свойственно малое газовыделение. В последнее время на этих участках начали широко применять шланги из искусственных синтетических материалов, например из поливинилхлорида и др. Для компенсации неточности изготовления, облегчения монтажа, а также для защиты установок от вибрации механических насосов и компенсации тепловых деформаций в вакуум-проводах предусматривают компенсаторы — участки резиновых труб, сильфоны, резиновые диски или тороиды и т. п. С целью герметичного перекрытия вакуум-проводов, напуска в вакуумную систему определенных количеств газов применяют разные затворы, краны, вентили, натекатели с дистанционным управлением от электромагнитных, электромашинных и пневматических приводов.
Для перекрытия низковакуумных трубопроводов, а также трубопроводов небольших диаметров применяют вешили (ДУ-25, ДУ-50, ДУ-80), напоминающие по конструкции водопроводные и газовые краны, но имеющие сильфонное уплотнение штока. В высоковакуумных ком м уникациях обычно применяют затворы форточного (ДУ-85, ДУ-160, ДУ-260, ДУ-380, ДУ-500) или шиберного (ДУ-900, ДУ-1200 и др.) типов. Затворы шиберного типа большого проходного сечения используют, как правило, в шлюзовых устройствах, позволяющих загружать в камеры крупногабаритные изделия без нарушения вакуума. Корпуса таких затворов изготовляют в виде прямоугольных коробок, и при открывании затвора клапанная тарелка и рычаги запирающего механизма полностью уходят в закрытую часть коробки (карман). Напуск в вакуумную систему атмосферного воздуха перед вскрытием вакуумной камеры или другого газа, необходимого для проведения технологических операций, осуществляется при помощи натекателей, напоминающих по конструкции игольчатые редукторы, в которых при вращении головки медленно перемещается запорная игла и медленно изменяется зазор между иглой и седлом. В результате обеспечивается плавное регулирование количества пропускаемого натекателем газа.
В металлургических вакуумных установках откачиваемые газы могут содержать много пыли. При попадании пыли в насосы вследствие трения между движущимися частями может происходить заклинивание трущихся поверхностей или резкое увеличение их износа. Для защиты механических насосов от пыли на вакуум-проводах устанавливают фильтры. Распространение получили фильтры очистки в основном двух конструкций. В фильтрах одной из этих конструкций фильтрующим элементом служат слои смоченных вакуумным маслом ВМ-4 колец длиной 15 мм из стальной трубы диаметром 3/4. В других фильтрах газ фильтруется, проходя через один или два слоя ткани, натянутой на стальной цилиндр с продольными прорезями.
Недостаток фильтров обеих конструкций заключается в сложности замены фильтрующих элементов, которые быстро забиваются пылью, вследствие чего резко снижается пропускная способность системы. При использовании диффузионных насосов возможно и загрязнение, происходящее с обратной стороны вследствие миграции из насосов в откачиваемый объем паров масла или другой рабочей жидкости, достигающей 5 мг /(ч • см2). Для защиты рабочих камер от загрязнения парами рабочей жидкости или продуктами ее разложения между насосами и камерой помещают специальные ловушки.
В вакуумных установках применяют механические (отражательные) и конденсационные (вымораживающие) ловушки одинаковых конструкций, но с разными режимами охлаждения: температура рабочих поверхностей у отражательных ловушек приблизительно равна температуре откачиваемого газа, а у вымораживающих значительно ниже. Рабочие поверхности ловушек выполняют в виде жалюзи, системы диафрагм, колец, пластин, образующих каналы в виде щелей так, чтобы прямолинейно движущиеся пары не могли пройти через них, не столкнувшись с поверхностью ловушки.
Для интенсификации конденсации паров на рабочих поверхностях ловушки охлаждаются водой (механические) или жидким азотом, фреоном и т. д. (конденсационные). Конденсационные ловушки не только предотвращают миграцию масла, но и являются своеобразным высоковакуумным насосом, так как на их рабочих поверхностях одновременно конденсируются некоторые углеводороды, углекислый и другие газы. Используют их, как правило, в высоковакуумных установках.
Важнейшим требованием, предъявляемым к вакуумным системам, является их герметичность. Установкой мощных насосов можно добиться требуемых давлений даже при наличии неплотностей в системе, но при этом вследствие натекания атмосферного воздуха в системе будут постоянно находиться вредные газы при таких парциальных давлениях, что их присутствие может резко снизить качество металла. Для оценки герметичности системы проверяют величину натекания по изменению давления в системе за определенный промежуток времени при закрытых затворах, перекрывающих вакуум-проводы к насосам. Величину натекания, м3 • Па/с, рассчитывают по формуле:
N = (VΔP)/τ,
где V — объем изолированной системы, Δ Р — изменение давления в системе объемом V за время измерения τ.
При отсоединении насосов давление в системе возрастает вследствие внутреннего газовыделения в результате главным образом десорбции газов и поступления атмосферного воздуха через неплотности, поэтому повышенное натекание не свидетельствует о негерметичности системы. Для установления причины повышенного натекания необходимо определить характер его изменения во времени. Если натекание определяется внутренним газовыделением, то оно постепенно уменьшается, и для достижения допустимых пределов натекания систему следует подольше подержать под вакуумом. При наличии неплотностей давление в изолированной системе в процессе измерения натекания монотонно возрастает. При такой зависимости давления от времени необходимо установить участок негерметичности и устранить ее. Простейшим способом обнаружения неплотностей является впрессовывание системы: в систему накачивают сжатый воздух или любой другой газ до давления 200…400 МПа, а места возможных утечек смазывают мыльным раствором; неплотности обнаруживаются по выделению пузырей.
Опрессованную систему можно проверить также посредством переносного галоидного течеискателя ГТИ-3, очень чувствительного к присутствию в атмосфере галоидов (реагирует при концентрации галоидов — фреона, тетрахлорида углерода и др. 0,0001 %). Для этого при опрессовании в систему добавляют галоидосодержащий газ и подозрительные места проверяют щупом в виде пистолета, в стволе которого находится чувствительный датчик, а в торцевой части — вентилятор для прокачивания газа через датчик. Датчиком является нагретая до 800…900 °С платиновая проволока. При появлении в газовой среде галоидов с поверхности платиновой нити резко возрастает испускание положительных ионов, улавливаемых коллектором. Резкое увеличение силы ионного тока регистрируется стрелочным прибором и генератором звуковых колебаний.
Имеется вакуумная модель галоидного течеискателя ВАГГИ-4, датчик которого вакуумплотно подсоединяется к системе, и с его помощью анализируют состав откачиваемых газов. В этом случае подозрительные участки обдуваются снаружи при непрерывной откачке.
Гелиевые течеискатели ПТИ-6 и ПТИ-7 представляют собой индивидуальный вакуумный блок со встроенной упрощенной масс-спектрометрической камерой, настроенной на гелий. Гелиевые течеискатели подключают на форвакуумной линии после диффузионных насосов. Собственный вакуумный блок течеискателя отбирает из общего потока откачиваемых газов небольшие порции и направляет их в масс-спектрометрическую камеру. В случае попадания в систему гелия, которым обдувают снаружи подозрительные места, в камере генерируется ионный ток, который регистрируется стрелочным прибором и преобразуется в звуковой сигнал.