Электрошлаковый переплав (ЭШП) — это бездуговой процесс переплава расходуемого металлического электрода в шлаковой ванне, при котором необходимая для плавки теплота выделяется при прохождении электрического тока через расплавленный электропроводный шлак, поддерживая в нем температуру 1800-2000 °С. Часть тепла, выделяемого в шлаковой ванне, передается расходуемому (с оплавленным торцом) электроду. Капли металла с торца электрода проходят через химически активный шлак, рафинируются там и формируются в кристаллизаторе в виде слитка.
Процесс ЭШП разработан в 1952-1953 гг. в Институте электросварки им. Е. О. Патона (Киев, Украина). ЭШП применяют для получения стальных 1—20-т слитков, а тж. для производства крупных 40—200-т кузнечных слитков.
Установка электрошлакового переплава
Схема установки ЭШП показана на рис 107, а. Переплав осуществляется в водоохлаждаемом кристаллизаторе. К расходуемому электроду и наплавляемому слитку подведен ток. Между слитком и электродом имеется слой шлака, в котором и выделяется тепло при прохождении через него тока. Кристаллизатор, изготовленный из меди, может иметь дно (см. рис. 107, а) или слиток можно непрерывно вытягивать из кристаллизатора.
При использовании трехфазного трансформатора возможно одновременное расплавление в одном кристаллизаторе трех электродов (рис. 107, б) или подключение к одному трансформатору трех кристаллизаторов (рис. 107, в)
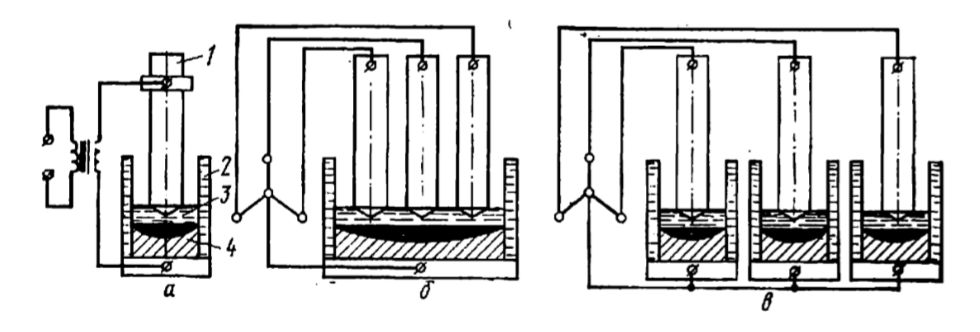
Однофазная установка ОКБ-1065, предназначенная для переплава электродов на слитки квадратного сечения массой 3500 кг, представлена на рис. 108. Расходуемый электрод, закрепленный в электрододержателе каретки, перемещается по вертикальной стойке при помощи троса от электромеханического привода. Привод перемещения электродов состоит из электродвигателей, дифференциального редуктора и двух пар открытых цилиндрических передач. Удерживается электрод в электрододержателе усилием пружин, а освобождается при помощи пневматического цилиндра. Слиток наплавляется в кристаллизаторе, к поддону которого крепится токопровод в виде медных шин. К электроду ток подводится по гибким водоохлажденным кабелям. Кристаллизатор по мере наплавления слитка поднимается специальной кареткой с самостоятельным реечным приводом. Кристаллизатор с поддоном устанавливается на самоходную тележку, предназначенную для выкатывания наплавленного слитка.
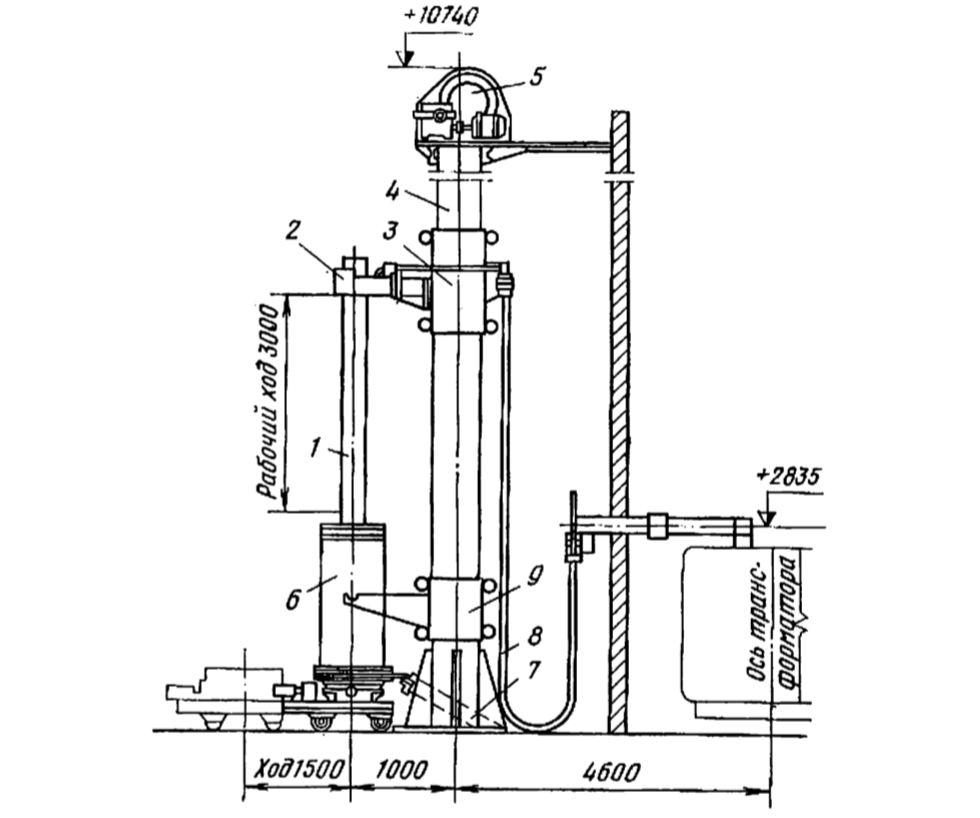
Недостатком однофазных установок является высокая реактивность токопровода низкой стороны вследствие большей длины токопроводящей части расходуемого электрода и наличия петель гибких проводов. Трехфазные установки обладают меньшей реактивностью, однако питание трех кристаллизаторов от трехфазного трансформатора нарушает стабильность режима на каждом электроде. Трехфазные установки с тремя электродами на одном кристаллизаторе целесообразны при выплавке крупных слитков.
Для снижения электрических потерь представляет интерес применение бифилярного токоподвода. В этом случае в одном кристаллизаторе одновременно переплавляют два электрода, включенных последовательно и подаваемых в кристаллизатор одним электрододержателем с двумя электрически изолированными друг от друга токоподводами. При бифилярном токоподводе достигается близкое и параллельное расположение токоподвода на всех участках, включая и расходуемые электроды, что снижает индуктивность короткой цепи.
Масса слитков, переплавляемых на установках ЭШП, достигает несколько десятков тонн. Этот способ переплава является наиболее экономичным из переплавных методов, и он находит все более широкое распространение для производства качественных сталей и сплавов.
https://youtu.be/jOYp1X-4EF0?t=522
Технология ЭШП
При ЭШП тепло выделяется благодаря прохождению тока через шлак. Плотность тока при этом процессе обычно составляет 0,1—0,5 А/мм2. Чем меньше плотность тока, тем труднее навести шлак в начале процесса, но тем легче поддерживать стабильность процесса, так как при малой плотности тока процесс идет достаточно устойчиво в широком диапазоне токов и напряжений. Шлак должен обладать следующими свойствами:
- большая легкоплавкость, чем металла расходуемого электрода, что обеспечивает лучшее рафинирование от газов и неметаллических включений;
- достаточное электросопротивление (при большой электропроводности шлака будет выделяться мало тепла);
- необходимая жидкотекучесть (иначе ухудшается теплопередача через шлаковую прослойку к кристаллизатору и ухудшается качество слитка).
В начале процесса применяют электропроводный флюс, например, марки С-1, состоящий из 17% калиевой селитры, 16,5% алюмомагниевого порошка и 66,5% наполнителя. Расход флюса С-1 составляет ~0,5 кг/т металла. Этот шлак предназначен для запуска процесса и был предложен институтом электросварки им. О. Е. Патона.
После того, как процесс пойдет устойчиво, в кристаллизатор загружают рабочий флюс. Основой для большинства рабочих флюсов, применяемых при ЭШП, является фтористый кальций. Наиболее широко применяется рабочий флюс марки АНФ-6, содержащий 25—30% Al2O3, 57—65% CaF2, 4—5% CaO. Температура плавления этого флюса 1320—1340° С, расход составляет 3— 4% от массы слитка. Этот шлак обеспечивает десульфурацию металла и применяется для сталей и сплавов, не содержащих бор и титан. Флюс АНФ-111, содержащий 95% CaF2 и 5% СаО с температурой плавления ~ 1400° С, может быть использован для переплава сталей, содержащих бор и титан.
Флюсы необходимо хранить в сухом помещении; перед использованием для удаления влаги их нужно просушивать при температуре 300° С. Флюсы выплавляют в однофазной дуговой электропечи с углеродистой футеровкой или в водоохлаждаемом тигле. Выплавленный флюс дробят, размалывают и просеивают через сито с отверстием 2×2 мм.
При ЭШП жидкий металл расходуемого электрода переносится через шлаковую ванну в кристаллизатор в виде капель. Это увеличивает площадь соприкосновения металла со шлаком и обеспечивает более полное протекание рафинировочных процессов, чем в обычных дуговых электропечах. В связи с этим важным моментом ЭШП является обеспечение оптимальной частоты отрыва капель от расплавляемого электрода и их оптимального размера. Частота отрыва капель от конца электрода, их средний размер, длина пути, который они проходят в шлаке, зависят от параметров плавки: силы тока и напряжения, состава переплавляемого металла и др. В каждом конкретном случае подбирают технологию переплава, обеспечивающую при максимальной производительности установки ЭШП получение высококачественного металла.
Перед началом плавки тщательно осматривают кристаллизатор и при удовлетворительном его состоянии, прежде всего при отсутствии течи, зачищают дно кристаллизатора, на которое устанавливают затравку, представляющую собой пластину из того же металла, что и переплавленный металл. Затравка защищает дно кристаллизатора в первые моменты плавки. На затравку засыпают хорошо перемешанный электропроводный флюс. Это необходимо для получения жидкого шлака в начале процесса.
После засыпки рабочего флюса подают воду на охлаждение кристаллизатора и поддона, а затем включают ток. Максимальная сила тока, обеспечивающая устойчивое протекание процесса ЭШП, зависит от диаметра расходуемого электрода:
Через 10—15 мин после включения печи в кристаллизаторе образуется жидкая шлаковая ванна высотой 90—140 мм.
Электрический режим плавки оказывает решающее влияние на качество слитка и его поверхность. С увеличением подводимой мощности увеличивается глубина жидкой части металла в кристаллизаторе и продолжительность затвердевания заготовки. Это вызывает загрязнение металла неметаллическими включениями. Так, например, на заводе «Днепроспецсталь» снижение силы тока, подводимого к установке с диаметром кристаллизатора 300 мм, с 9 до 6 кА обеспечило снижение загрязненности стали неметаллическими включениями на 25—35%.
Однако понижение температуры металла при малой подводимой мощности приводит к повышению его вязкости и попаданию в металл частиц шлака, появлению корочек шлака. Поверхность заготовок резко ухудшается.
При небольшой высоте жидкого шлака и большой подводимой мощности наблюдается клокотание шлаковой ванны и значительное колебание силы тока. Для устранения отмеченного явления необходимо уменьшить силу тока. Производительность установки ЭШП зависит от диаметра кристаллизатора, выбранного электрического режима, марки стали и т. д. Например, при диаметре кристаллизатора 200 мм производительность установки составляет 100—150 кг/ч, а расход электроэнергии 1300—1600 кВт • ч на 1 т металла.
Улучшение технико-экономических показателей работы установок ЭШП достигается уменьшением простоев между плавками и повышением степени механизации вспомогательной операции, увеличением выхода годного.
Увеличение выхода годного на установках ЭШП может быть достигнуто при использовании жидкого шлака. Заливка жидкого шлака в кристаллизаторы установок ЭШП снизу (сифонным способом) была впервые внедрена на трехфазной установке завода «Электросталь».
На этой установке имеются три электрода диаметром 170 мм. Процесс ЭШП с сифонной заливкой жидкого шлака экономически целесообразен.
Совершенствование систем управления мощностью шлаковой ванны и скоростью подачи или массовой скоростью плавления электрода также повышает производительность установки.
Улучшение технико-экономических показателей установок ЭШП достигается и повторным использованием шлака в случаях, когда он не окисляется и не обогащается серой.