Назначение и характеристика электродов
Электроды служат для подвода электрического тока в рабочее пространство дуговой электропечи. Электроды должны иметь высокую электропроводность, достаточную механическую прочность, высокую термическую стойкость, а также низкую стоимость. Этим требованиям удовлетворяют электроды из углеродистых материалов.
Результаты рассмотрения основных свойств различных электродов (табл. 6) показывают, что наилучшими являются графитированные электроды, а качество самоспекающихся (самообжигающихся) электродов близко к качеству угольных электродов. В практике производства электростали графитированные электроды обычно называют графитовыми.
Преимущества графитированных электродов настолько существенны, что, несмотря на их высокую стоимость (в два раза выше стоимости угольных электродов), они используются на средних и крупных электросталеплавильных печах. Графитированные электроды выпускают диаметром от 75 до 555 мм со следующей допустимой плотностью тока (ГОСТ 4426—71):
В некоторых случаях производят электроды диаметром 610, 710 мм и более. На практике иногда допускается более высокая рабочая плотность тока на электродах (до 35 А/см2 для электродов диаметром 555 мм). Расход электродов при этом возрастает.
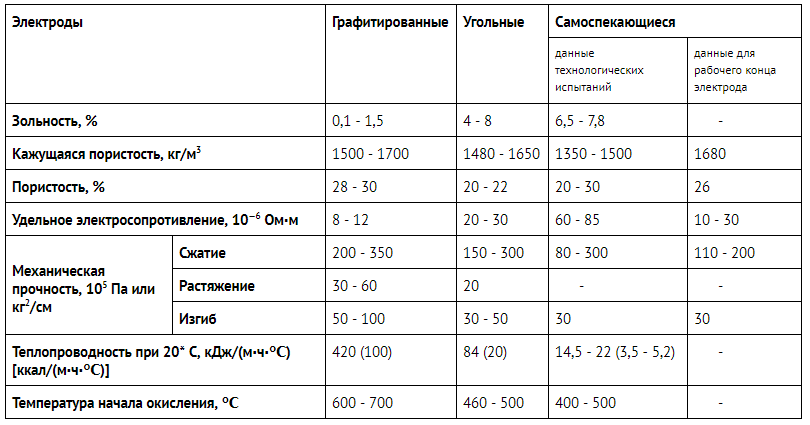
Электрод при плавке подвергается механическим воздействиям (обвал шихты, наклон печи и т. д,), часто направленным под углом к оси электрода, и поэтому он должен иметь достаточную механическую прочность. Повышенная пористость (пониженная плотность) электрода вызывает интенсивное его окисл.ение при высокой температуре. Угольные электроды по ГОСТ 4425—72 изготавливают диаметром от 100 до 750 мм, и рекомендуемая плотность трка на них составляет 7—12 А/см2.
В ферросплавной промышленности широкое применение получили самоспекающиеся электроды, заменяющие угольные и графитированные электроды там, где допускается некоторое науглероживание сплава и разбавление его железом. Угольные электроды применяют при выплавке кристаллического кремния, а графитированные при производстве безуглеродистого феррохрома, металлических хрома и марганца и т. п. Обычно используют. круглые самоспекающиеся электроды диаметром ≥2000 мм, реже (на прямоугольных печах) применяют плоские самоспекающиеся электроды размером до 3200×800 мм. Допустимая рабочая плотность в самоспекающемся электроде составляет 5—8,5 А/см2 (верхнее значение относится к малым электродам).
Изготовление графитированных электродов
Основными составляющими угольных электродов и электродной массы для самоспекающихся электродов являются антрацит и каменноугольный кокс. Для изготовления графитированных электродов применяют малозольные нефтяной, сланцевые и пековый коксы.
Для повышения эксплуатационных свойств электродов в шихту вводят искусственный и реже естественный графит, а также бой графитированных электродов. Для связывания твердых составляющих шихты электродных изделий применяют средне- и высокотемпературный каменноугольные пеки, а для производства электродной массы — среднетемпературный каменноугольный пек или смесь его с каменноугольной смолой.
При производстве электродной продукции сырые материалы дробят и прокаливают (за исключением графита и обожженного боя) в ретортных или трубчатых вращающихся печах, в результате чего увеличивается их плотность, удаляется основное количество летучих, повышается электропроводность и механическая прочность. Прокаленные материалы измельчают на дробилках и в мельницах различных типов с последующим рассевом материалов на барабанных ситах или вибрационных грохотах.
Подготовленные материалы точно дозируют по видам сырья и его гранулометрическому составу и затем подают в смесительные машины, куда задают и связующее, причем жидкие пек и смолу предварительно нагревают для удаления влаги и частично летучих веществ. В результате тщательного перемешивания при температуре ~150° С получается однородная смесь, называемая электродной массой, которую используют для последующей переработки на электроды, или выдается в качестве готовой продукции, применяемой для самоспекающихся электродов.
Электроды получают на гидравлических прессах методом выдавливания массы через мундштук при давлении (50—200) · 105 Па (50—200 кгс/см2) в зависимости от сечения изделия.
Спрессованные электроды охлаждают водой на специальных рольгангах и затем обжигают в многокамерных газовых печах непрерывного действия. В результате обжига связующее превращается в кокс, что обеспечивает резкое повышение механической прочности, электропроводности и термической стойкости электродов. Обжиг ведут при температурах 1200—1300° С под сводом печи в защитной засыпке из мелкого коксика, предохраняющей электроды от сгорания и деформации. Продолжительность обжига зависит от размеров и плотности изделий и обычно составляет 320—400 ч.
Для получения графитированных электродов обожженную заготовку подвергают графитизации в электрических печах сопротивления при 2500—3000° С в течение 50—60 ч, причем сопротивлением в этих печах служат сами электроды и пересыпка — коксик фракции 10—30 мм. Общая продолжительность графитизации, включая загрузку, графитизацию, остывание и разгрузку печи, составляет 7—10 сут. В результате графитизации повышается электропроводность, теплопроводность и химическая стойкость, уменьшается твердость электродов.
Обожженные угольные и графитированные электроды подвергают механической обработке: обточке цилиндрической поверхности, обработке торцов и нарезке ниппельных гнезд. Ниппельное соединение обеспечивается ниппелем с винтовой нарезкой, ввинчиваемым в ниппельные гнезда в торцах электродов. У угольных электродов иногда нарезают на одном конце электрода конический ниппель, а на другом конце —коническое гнездо. Для графитированных электродов применяют цилиндрические и конические ниппели (рис. 43). Ниппели вытачивают из специальных заготовок, обладающих высокой плотностью и механической прочностью, что обеспечивается дополнительной пропиткой обожженных заготовок пеком под давлением 5-106 Па (5 ат) при температуре 280—300° С.
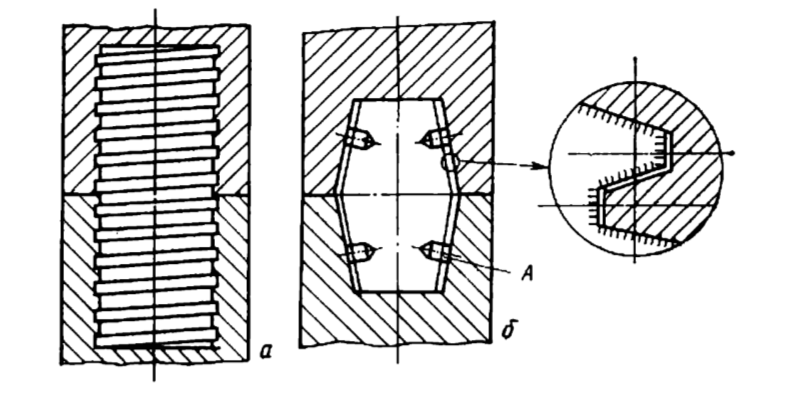
Для повышения эксплуатационных качеств графитированных электродов в ряде случаев на их поверхность наносят различные защитные покрытия, или их пропитывают различными солями, или вводят в массу при их изготовлении различные добавки, снижающие окисление электрода во время его службы. Это позволяет снизить расход электродов на 20—30%.
Самоспекающиеся электроды
Основными преимуществами самоспекающихся электродов при производстве ферросплавов являются возможность изготовления электродов большого диаметра и их низкая стоимость (они в три раза дешевле графитированных и в полтора раза дешевле угольных).
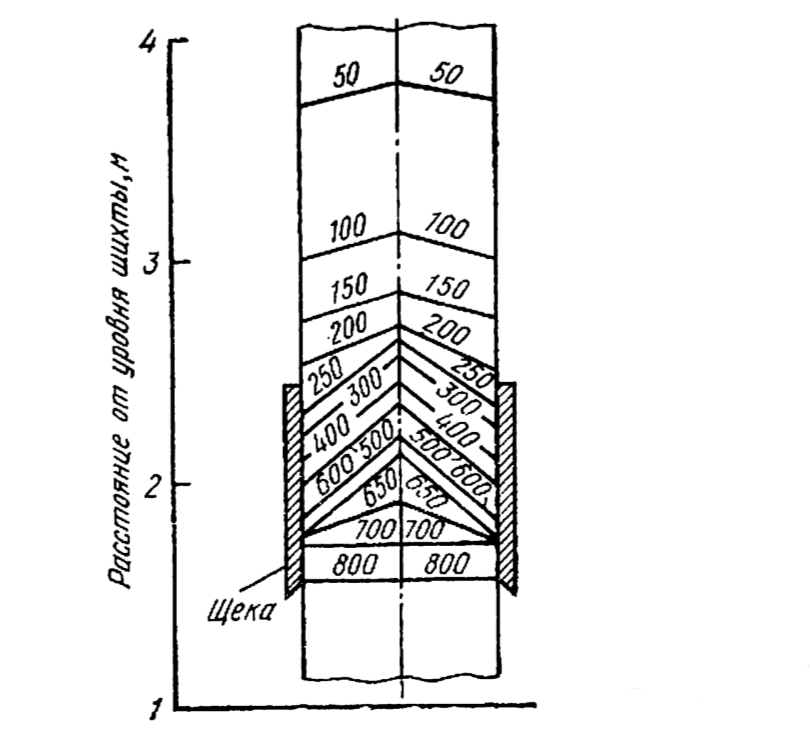
Самоспекающийся электрод представляет собой заполненный электродной массой металлический кожух с внутренними ребрами, выполненный из листового железа толщиной от 1,25 до 3 мм. Кожух, изготавливаемый из отдельных секций длиной 1,4—1,8 м, служит формой для электродной массы, предохраняет электрод от окисления воздухом, обеспечивает прохождение электрического тока от электрододержателя к обожженной части электрода, а также усиливает передачу тепла к верхней части электрода. Спекание и обжиг электродной массы протекают в печи.
На рис. 44 показано примерное распределение температуры в электроде в области электродного зажима. Первая стадия обжига массы на длине ~ 1 м состоит в нагреве ее с 25 до 65° С, в результате чего кусковая масса размягчается и сливается в блок (если масса загружалась в твердом виде без предварительного подогрева).
На втором участке длиной также ~ 1 м температуру массы повышают от 60 до 200° С у кожуха и до 350° С в центре электрода, образуя так называемый конус спекания. Под контактные щеки масса поступает еще пластичной. На последней стадии обжига, под щеками, на участке длиной ~ 1 м, температуру массы повышают до 800° С и из-под щек электрод выходит обожженным.
В зависимости, от особенностей технологического режима (уровень колошника печи, длина рабочего конца электрода, температура охлаждающего воздуха и т. п.) отмеченное распределение температуры может меняться. Нижний торец электрода, работающий в зоне высоких температур, подвергается графитизации.
Эксплуатация электродов
Электроды необходимо транспортировать и хранить, не допуская попадания влаги и оберегая их от механических повреждений. Для предотвращения саморазвинчивания в процессе эксплуатации ниппельные соединения графитированных электродов закрепляют, используя пробки из специальных паст, которые, расплавляясь и коксуясь при нагревании, обеспечивают надежное крепление. Перед установкой на печь электроды желательно просушивать, а ниппельное гнездо должно быть продуто сжатым воздухом.
Хорошее свинчивание электродов в свечу обеспечивается при проведении этой операции вне печи на специальном стенде при помощи устройства, состоящего из опорного хомута, стягивающего хомута и механизма для создания крутящего момента, который должен составлять для электродов диаметром 350—400 мм около 2,45 кДж (250 кгс·м) и для электродов диаметром 500— 555 мм—примерно 4—5 кДж (400—500 кгс·м).
На стойкость электрода влияют не только его физико-механические свойства, но и условия эксплуатации. На электрод, находящийся в рабочем пространстве, воздействует большое число факторов, которые снижают его стойкость и увеличивают расход. К числу таких факторов относятся термические напряжения, связанные с неравномерным распределением температуры по длине и сечению электрода.
Заметное разрушение электродов происходит вследствие попадания на его поверхность капель металла и шлака. Особенно этот процесс получает развитие при близком расположении электродов к поверхности ванны, что соответствует режиму при минимальном напряжении. И, конечно, недопустимо науглероживание металла путем опускания электродов в ванну.
Около 70% общего расхода электродов приходится на окисление. Поэтому большое значение для повышения стойкости электродов приобретает создание хорошего уплотнения между электродом и сводом. Излишнее использование кислорода, особенно при плохом усвоении его металлом, увеличивает расход электродов.
На расход электродов, кроме перечисленных факторов, влияют тип процесса, длительность плавления, сортамент выплавляемых сталей, емкость печи и т. д. Причиной облома электродов может быть плохая центровка электрододержателей, плохой контакт в ниппельном соединении, неправильная завалка шихты и ее обвалы и т. п.
Необходимо стремиться к снижению расхода электродов, так как их доля в общей стоимости передела составляет заметную величину. Расход электродов колеблется в пределах 4—9 кг на 1 т выплавляемой стали. Нижний предел характерен для крупных печей при выплавке углеродистых сталей.
В случае применения самоспекающихся электродов транспортирование и хранение электродной массы должно производиться в условиях, исключающих возможность ее загрязнения. Набивку кожухов электродной массой производят без отключения печи, причем масса загружается как в твердом, в виде кусков размером не более 200 мм, так и в жидком состоянии. Набивка должна производиться не реже одного раза в сутки. Электрод сверху должен быть закрыт крышкой во избежание попадания в кожух пыли, что может привести к облому электрода в дальнейшем.