Энергосбережение на действующих предприятиях
Для снижения потребления топливно-энергетических ресурсов, а также для уменьшения загрязнения окружающей природной среды необходимо:
- совершенствование и оптимизация существующих технологических процессов;
- внедрение новых энергосберегающих и безотходных технологий и оборудования;
- структурная перестройка отрасли за счет снижения доли энергоемких производств;
- расширение использования ВЭР.
Остановимся более подробно на некоторых примерах эффективных мероприятий по энергосбережению.
В доменном производстве актуально снижение расхода кокса на тонну выплавляемого чугуна (стоимость кокса составляет до 60% стоимости чугуна). Это достигается, например, за счёт использования природного газа, обогащения дутья кислородом, вдувания пылеугольного топлива как частичного заменителя кокса.
В сталеплавильном производстве целесообразна замена мартеновских печей двухванными сталеплавильными агрегатами, дальнейшее развитие конвертерного, электросталеплавильного производства и внепечной обработки стали.
В прокатном производстве необходимо осуществить широкое внедрение технологии непрерывного литья заготовок.
До настоящего времени на металлургических заводах не используется физическое тепло доменного газа (температура газа порядка 300 °С), на большинстве заводов не используется потенциальная энергия давления доменного газа.
Не используется физическое тепло кокса, для его использования необходимо дальнейшее строительство установок сухого тушения кокса.
Конвертерный газ отводится с полным дожиганием, не используется как топливо.
На ряде предприятий имеются возможности более полного использования физического тепла готового продукта в последующих технологических переделах: чугуна в сталеплавильном производстве, а стали — в прокатном.
Не используется физическое тепло металлургических шлаков.
Энергосбережение на создаваемых объектах
При строительстве новых объектов должны использоваться все прошедшие проверку на действующих предприятиях способы снижения энергозатрат. О некоторых из них мы говорили. Здесь затронем одну из важнейших для отрасли проблем.
В настоящее время большинство металлургических агрегатов имеют водяное охлаждение. Все тепло, отобранное водой, безвозвратно теряется. Если вместо водяного охлаждения использовать испарительное, это существенно снизит потребность в воде, многократно увеличит срок службы систем охлаждения, а пар, полученный при охлаждении металлургических агрегатов, может использоваться на технологические нужды, для отопления и горячего водоснабжения, а также в различного рода энергетических установках: турбогенераторах, турбовоздуходувках.
Существенно снижает энергоемкость сталеплавильного процесса и прокатного производства непрерывная разливка стали. Выполняется такая разливка с помощью машин непрерывного литья заготовок (МНЛЗ). В расчёте на одну тонну заготовок МНЛЗ даёт экономию 60 кг коксующихся углей, более 50 кг нефти, 40 м3 природного газа, 9 м3 кислорода и около 1500 кВт-ч электроэнергии.
Значительное внимание должно быть уделено более полному использованию топливных и тепловых ВЭР, в частности, конвертерного и ферросплавного газов. Должны использоваться низкопотенциальные ВЭР: пар низкого давления, теплая вода, вентиляционные выбросы и др. Так как улучшению использования ВЭР способствует применение сухих методов очистки гаэов, следует отдавать предпочтение аппаратам для сухой очистки газов.
При строительстве и реконструкции ТЭЦ-ПВС следует применять оборудование, работающее на паре высоких параметров (давление до 14 МПа при температуре 550°С). Это обеспечивает повышение к. п. д. паросиловых установок, а, следовательно, ведет к экономии энергоресурсов.
В заключение отметим, что эффективное энергосбережение невозможно без внедрения автоматизированных систем управления производством и технологическими процессами.
Вторичные энергоресурсы
Являясь крупнейшей топливопотребляющей отраслью промышленности, чёрная металлургия облагает рядом особенностей. Высокотемпературные технологические процессы в металлургии имеют относительно низкую эффективность использования топлива. Значительная часть вносимой в процесс энергии уходит из агрегата с основной продукцией, побочными продуктами, продуктами сгорания. Эта энергия может и должна быть использована в качестве вторичных энергоресурсов.
В настоящее время за счёт использования ВЭР покрывается от 30 до 80% потребности металлургических предприятий в тепловой энергии. Больше всего теплоты от утилизационных установок используют на металлургических комбинатах им. Ильича и Азовсталь, г. Мариуполь.
Отметим, что значительней выход ВЭР в ряде технологических процессов не является достоинством этих процессов. Рационально построенная энергетика технологии должна обеспечивать максимальное использование теплоты в рабочем процессе с минимальными тепловыми и другими отходами, что, в конечном счете, ведет к созданию безотходной технологии.
Источники вторичных энергоресурсов
Являясь одной из самых топливопотребляющих отраслей промышленности, металлургия обладает рядом особенностей. Высокотемпературные технологические процессы приводят к относительно низкой эффективности использования топлива. Одновременно значительная часть вносимой в процесс энергии уходит из агрегата с энергоносителями, которые могут быть затем использованы в виде вторичных энергоресурсов. Распределение ВЭР по основным переделам чёрной металлургии приведено в табл. 12.1.

Классификация ВЭР
По виду энергии ВЭР разделяют на горючие (топливные), тепловые и избыточного давления газа.
К горючим ВЭР относятся побочные продукты технологических процессов, которые могут быть использованы в качестве энергетического или технологического топлива.
Тепловые ВЭР — это физическая теплота основных и побочных продуктов технологических процессов, отходящих газов технологических агрегатов, а также систем охлаждения их элементов. Если эта теплота используется для подогрева сырья или воздуха, то есть возвращается в технологический процесс, то к ВЭР она не относится.
ВЭР избыточного давления газов — это потенциальная энергия газов, выходящих из технологических агрегатов с избыточным давлением, которое может быть использовано в утилизационных установках для получения других видов энергии.
Характеристика ВЭР
Характеристика горючих ВЭР
В чёрной металлургии к горючим ВЭР относятся доменный, ферросплавный и конвертерный газы, а иногда также и коксовый газ.
Доменный газ образуется при выплавке чугуна в доменных печах. Его выход и химсостав зависят от свойств шихты и топлива, режима работы печи, способов интенсификации процесса и других факторов. Выход газа колеблется в пределах 1500-2500 м3 на тонну чугуна. Доля негорючих компонентов (N2 и CO2) в доменном газе составляет около 70%, поэтому он имеет низкую теплоту сгорания (3-5 МДж/м3).
При сжигании доменного газа максимальная температура продуктов сгорания равна 1400-1500 °C. Если перед сжиганием газ и воздух подогреть, то температуру продуктов
сгорания можно значительно повысить.
На выходе из печи газ загрязнён колошниковой пылью, содержащей окислы железа, кремния, алюминия, марганца, серы, а также другие компоненты, имеющиеся в шихте. Запыленность доменного газа очень высока и достигает 20-25 г/м3, поэтому использовать его в качестве топлива можно только после очистки.
При применении доменного газа для обогрева коксовых печей, воздухонагревателей доменных печей, а также в утилизационных бескомпрессорных турбинах (ГУБТ) содержание пыли в нем не должно превышать 4 мг/м3.
Ферросплавный газ образуется при выплавке ферросплавов в рудовосстановительных печах. Газ, отходящий из закрытых печей, можно использовать в качестве топливных ВЭР. В открытых печах в связи со свободным доступом воздуха газ сгорает на колошнике.
Выход и состав ферросплавного газа зависит от марки выплавляемого сплава, состава шихты, режима работы печи, ее мощности и т.п. Состав газа: 50-90% CO, 2-8% H2, 0,3-1% CH4, 2-5% CO2 , O2 <1%, остальное N2. Максимальная температура продуктов сгорания около 2000 °C. Запыленность газа высока и составляет 30-40 г/м3.
Конвертерный газ образуется при выплавке стали в кислородных конвертерах. Выход его колеблется, в среднем, от 80 до 100 м3 на тонну стали. Газ характеризуется высокой запыленностью, достигающей 200 г/м3. Состав зависит от свойств шихты, режима и интенсивности продувки, конструкции фурм, типа процесса и других факторов. Основная составляющая — оксид углерода СО. После очистки состав газа примерно таков: 70-80% CO; 15-20% CO2; 0,5-0,8% O2 ; 3-12% N2. Теплота сгорания — 8,4-9,2 МДж/м3. Максимальная температура сгорания достигает 2000 °С.
Коксовый газ образуется в процессе получения кокса (спекание угольной шихты) в количестве 400-460 м3 на тонну кокса. В качестве топлива он используется после извлечения ряда ценных химических продуктов.
Состав коксового газа зависит от свойств угольной шихты и условий коксования. Объёмные доли компонентов в газе находятся в следующих пределах: 52-62% H2; 0,3-0,6% O2; 23,5-26,5% CH4; 5,5-7,7% CO; 1,8-2,6% CO2. Теплота сгорания — 17-17,6 МДж/м3, максимальная температура продуктов сгорания около 2000 °С.
Характеристика тепловых ВЭР
Доля тепловых ВЭР к общему выходу ВЭР составляет около 30%.
Физическая теплота готового продукта и шлаков
Из печей и агрегатов металлургического производства готовый продукт и шлак выходят с высокой температурой. Чугун и сталь в большинстве случаев являются промежуточными продуктами металлургического производства и их физическая теплота, как правило, используется в последующих переделах: чугуна — в сталеплавильном, стали — в прокатном производстве. Поэтому физическая теплота их при таком использовании к ВЭР не относится.
Количество тепловой энергии, которое можно получить при использовании теплоты жидких шлаков, составляет около 6% от теплоты технологического процесса. Выход шлаков при выплавке чугуна составляет 0,4-0,6 т/т при температуре 1400-1500 °С, а при выплавке стали — 0,2-0,3 т/т при температуре 1500-1600 °С.
Физическая теплота вторичных газов
Вторичные газы подразделяются на горючие и негорючие (дымовые). Первые образуются непосредственно в технологическом процессе, вторые выделяются при сжигании топлива. Источниками их образования являются мартеновские, электросталеплавильные, нагревательные и обжиговые печи, коксовые батареи, кислородные конвертеры, агломерационные машины и воздухонагреватели доменных печей. В некоторых производствах (электросталеплавильном, обжиговом, агломерационном) продукты сгорания смешиваются с технологическими газами.
Коксовый газ выходит из коксовой печи с температурой 600-700 °С. Непосредственное использование физической теплоты этого газа затруднено в связи с большим содержанием в нём смол.
Температура доменного газа равна 150-350 °С. Использование его физической теплоты возможно только после сухой очистки.
Среди горючих газов наибольшую температуру (1400-1800 °С) имеет конвертерный газ.
Температура ферросплавного газа зависит от вида получаемого сплава. Так, при выплавке ферромарганца газ выходит из печи с температурой 200-300 °С, а при выплавке ферросилиция — 500-700 °С.
Отходящие газы мартеновских печей состоят из продуктов сгорания топлива и газообразных компонентов химических реакций, протекающих в технологическом процессе. Выход газа равен 60-80 м3 на тонну стали, запыленность его 10-15 г/м3. Температура непосредственно за ванной — 1650 °С, за регенераторами 600-850 °С.
В электросталеплавильных печах газы образуются в процессе химических реакций. При использовании топливно-кислородных горелок к газам добавляются продукты сгорания топлива. Температура газов до разбавления воздухом составляет 1600-1800 °С, запыленность — 50-60 г/м3.
Газы известково-обжиговых печей состоят, главным образом, из продуктов сгорания топлива и газов, образующихся при разложении карбонатов. Выход газов из вращающихся печей равен 2500-3000 м3/т, температура — 750-800 °С. Запыленность их зависит от типа печи и колеблется в пределах от 5 до 75 г/м3.
Отходящие газы агломерационных машин содержат компоненты продуктов сгорания газообразного и твёрдого топлив, летучих веществ коксовой мелочи, а также продуктов разложения карбонатов. По длине машины температура газов неравномерна, наиболее высока она (200-250 °С) в хвостовой части вакуум-камер. Запыленность газов — 4-7
г/м3.
В системе отопления коксовых батарей образуются продукты сгорания, которые после регенератора имеют температуру 250-350 °С.
Отходящие газы нагревательных печей состоят из продуктов сгорания топлива и, в зависимости от типа печи, имеют температуру 800-1300 °С. Их теплота используется для нагрева воздуха, при этом температура понижается до 400-600 °С.
Температура дымовых газов воздухонагревателей доменных печей равна 200-300 °С и обычно не используется. При сжигании ферросплавного газа под сводом в закрытых печах с укрытым колошником образуются продукты сгорания с температурой 1600 °С.
К тепловым ВЭР относятся также энергоносители в виде водяного пара, горячей воды, полученные при охлаждении технологических агрегатов, а также вентиляционные выбросы.
Горючие ВЭР и отходящие газы технологических агрегатов характеризуются высокой запыленностью, поэтому их использованию должна предшествовать очистка.
Основные направления использования ВЭР
Утилизация теплоты готового продукта и шлаков
Потери физической теплоты с готовым продуктом в чёрной металлургии характеризуются следующими показателями (ГДж на 1 т продукции):
- с агломератом — 0,63;
- с коксом — 1,26;
- с жидким чугуном — 1,05;
- с жидкой сталью — 1,26;
- с жидким шлаком — 0,84; с прокатом — 0,5.
Физическая теплота высокотемпературных продуктов в общем случае может быть использована по одному из следующих вариантов:
- регенерация теплоты с ее возвратом в данный процесс;
- технологическое использование теплоты в последующем процессе;
- энергетическое использование теплоты.
Для металлургического производства характерно последующее технологическое использование теплоты. Так, жидкий чугун, полученный в доменной печи, поступает в мартеновские печи или в конвертеры. В этом случае физическая теплота жидкого чугуна входит в тепловой баланс последующего передела в качестве одной из приходных его статей. Использование теплоты жидкой стали возможно в печах прокатного производства (горячий посад) или в машинах непрерывного литья заготовок (МНЛЗ).
Такие виды сырья для доменного производства как агломерат и, особенно, раскаленный кокс, располагают значительной физической теплотой.
Агломерат в конце процесса спекания имеет температуру 600-900 °С. Физическая теплота агломерата может использоваться непосредственно в технологическом процессе и для энергетических нужд. Так, теплота горячего возврата используется при смешении агломерата с аглошихтой для её подогрева. Воздух, направляемый в зону спекания агломерата, предварительно используют для охлаждения готового агломерата, где он разогревается до 500-600 °С.
Кокс выдаётся из коксовой печи при температуре 1000-1100 °С. При его охлаждении на установках сухого тушения кокса (УСТК) до 70% теплоты раскаленного кокса используется в котлах-утилизаторах. Удельный выход пара составляет 0,4 т/т кокса.
Жидкая сталь из сталеплавильных агрегатов уносит значительное количество теплоты. Горячий посад слитков в нагревательные колодцы при температуре 800-900 °С снижает эти потери на 50%, что, соответственно, приводит к уменьшению расхода топлива на обогрев колодцев и повышению их производительности. Более полное использование физической теплоты жидкой стали происходит при ее разливке на машинах непрерывного литья заготовок (МНЛЗ). При этом исключается из баланса энергия, расходуемая обжимными станами, нагревательными колодцами и другим оборудованием, используемым при традиционной технологии получения проката.
Прокатные заготовки (блюмы, слябы), поступающие с обжимных станов, имеют температуру около 1000 °С. Охлаждение заготовок осуществляется в штабелях на воздухе до температуры 80 °С, при этом физическая теплота металла теряется безвозвратно. Существует способ охлаждения заготовок в камерах с отбором теплоты и ее использованием на производство пара, при этом сокращаются площади складов, ускоряется процесс охлаждения, снижается угар металла, облегчаются условия труда.
Шлаки являются побочным продуктом всех плавильных металлургических процессов. Обладая высокой температурой (1300-1600 °С), металлургические шлаки уносят 3-6% тепла, расходуемого на технологический процесс. В настоящее время значительная часть шлаков доменного, сталеплавильного и ферросплавного производств используется как сырье для переработки в строительные материалы. При утилизации теплоты шлаков имеются определенные трудности. Главная — их периодический выпуск из печей. Возможные схемы использования теплоты шлаков определяются способом их грануляции: мокрой (водой), сухой (воздухом) и контактной (на подвижных охлаждаемых поверхностях). Использовать теплоту шлаков можно для технологических и энергетических целей. В основном, в теплоутилизационных установках, предназначенных для использования теплоты шлаков, получают горячую воду на нужды теплоснабжения.
Утилизация теплоты уходящих газов металлургических печей
Теплота уходящих газов металлургических печей может быть использована по трём основным схемам: замкнутой или технологической; разомкнутой или энергетической; и комбинированной. В замкнутой схеме (рис. 13.1) за счёт теплоты уходящих газов в регенеративных (поочередное соприкосновение горячего и холодного теплоносителей с одними и теми же поверхностями аппарата) или рекуперативных (теплообмен между теплоносителями осуществляется непрерывно через разделяющую их стенку) теплообменниках нагревается дутьевой воздух, иногда сжигаемый газ или шихтовые материалы. При этом часть теплоты уходящих газов возвращается в агрегат что позволяет снизить расход топлива.
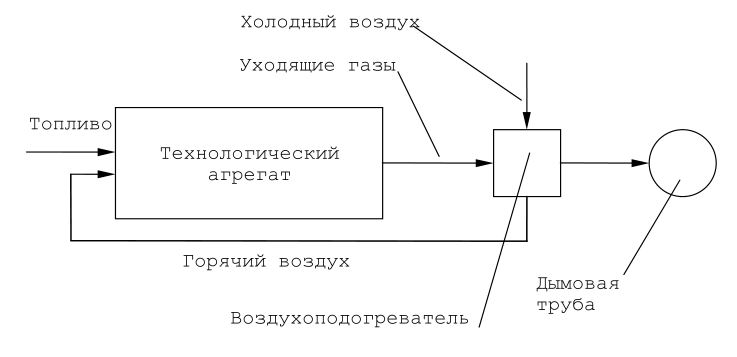
В разомкнутых схемах теплота уходящих газов используется в котлах-утилизаторах, а пар, производимый ими, в турбогенераторах или на технологические нужды.
В комбинированных схемах, представляющих собой комбинацию замкнутой и разомкнутой схемы, используются как теплообменники, так и котлы-утилизаторы.
Утилизация теплоты охлаждения элементов печей
В высокотемпературных технологических установках условия службы огнеупорной кладки и металлических конструкций исключительно тяжелые. Поэтому применяют охлаждение элементов, обеспечивающее надежность печного агрегата и увеличивающее срок его службы. На охлаждение печей расходуется более половины всей воды, потребляемой металлургическим предприятием. Для охлаждения печей используют техническую воду, что приводит к отложению солей в деталях и часто к их быстрому прогару. Теплота охлаждения в тепловых балансах печей составляет 10-30% теплоты, внесенной в печь. При водяном охлаждении вся отобранная теплота теряется.
В 1946 году советскими инженерами С.М. Андоньевым и Г.Е. Крушелем была разработана система испарительного охлаждения (СИО), в которой вода превращается в пар и интенсивно отбирает теплоту от стенок охлаждаемых элементов (рис. 13.2). Естественная циркуляция воды в контуре охлаждения осуществляется благодаря разности плотностей воды и пароводяной смеси, образующейся в охлаждаемом элементе за счёт его обогрева. Так как на испарение 1 кг воды затрачивается примерно 2260 кДж теплоты (при атмосферном давлении), а на нагрев ее до температуры кипения примерно 250-290 кДж, то каждый килограмм воды при испарительном охлаждении отбирает около 2500 кДж теплоты. При водяном охлаждении 1 кг воды может отобрать не больше 40-45 кДж, так как нагрев технической воды, во избежание выпадения солей и образования накипи, не должен превышать 60-65 °С.
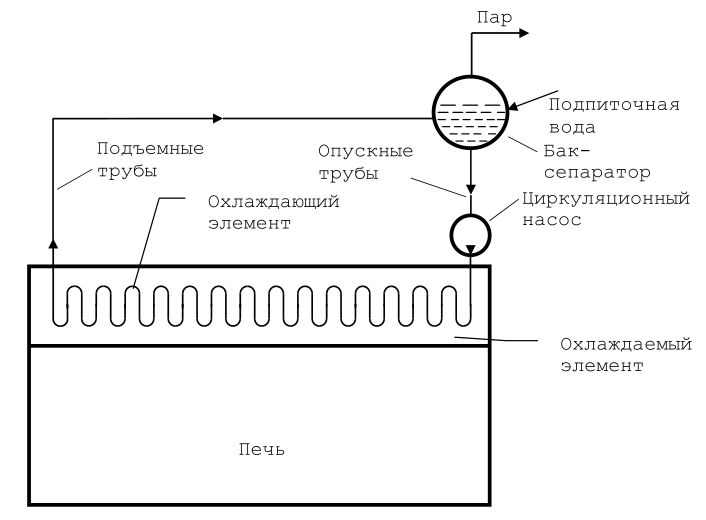
Таким образом, при испарительном охлаждении расход воды по сравнению с водяным сокращается в десятки раз. При этом замена технической воды химически очищенной приводит к увеличению срока службы охлаждаемых элементов в 5-10 раз. При испарительном охлаждении снижается расход электроэнергии на подачу воды, отпадает необходимость в сооружении громоздких и дорогостоящих водоводов, насосных станций, градирен, бассейнов, прудов.
Испарительное охлаждение применяют на доменных, мартеновских, нагревательных печах. Циркуляция воды в системе обычно естественная, но бывает и принудительная с использованием циркуляционного насоса, когда естественная циркуляция недостаточно эффективна.
Котлы-утилизаторы
Котлы-утилизаторы (бестопочные котлы) предназначены для получения пара за счёт использования теплоты уходящих газов технологических агрегатов. В чёрной металлургии температура уходящих газов в разных печах составляет 500-1800 °С. Поэтому различают котлы-утилизаторы радиационного, радиационно-конвективного и конвективного типов. Котлы первых двух типов применяют в конвертерном производстве, где температура газов выше 1000 °С.
Наибольшее распространение получили котлы-утилизаторы (КУ) конвективного типа. Их устанавливают за мартеновскими, нагревательными, обжиговыми и другими печами. Эти котлы предназначены для использования газов с температурой 600-850 °С. По компоновке поверхностей нагрева и газового тракта различают конвективные газотрубные и водотрубные КУ.
Газотрубные котлы-утилизаторы
Основная особенность газотрубных КУ заключается в движении горячих газов внутри труб, образующих поверхности нагрева котла, вода и пароводяная смесь находятся снаружи труб с газом. Газотрубные КУ работают с естественной циркуляцией, имеют горизонтальное расположение испарительных поверхностей, размещённых внутри барабана (рис. 13.3). В барабане размещено также сепарационное устройство для разделения воды и насыщенного пара. К барабану котла крепят входную и выходную камеры.

котла-утилизатора
По такой схеме выполняются котлы КУ-16 и КУ-40, рассчитанные на объём поступающих газов (с учётом подсосов воздуха перед ними) 16000 и 40000 м3/ч. Они вырабатывают перегретый пар давлением 0,9-1,4 МПа с температурой 250 °С в количестве 1,6-2,8 и 7,8 т/ч соответственно. Котлы оборудованы устройствами для очистки поверхностей нагрева и снабжены аппаратурой КИП и А.
Водотрубные котлы-утилизаторы
Водотрубные котлы-утилизаторы отличаются от газотрубных тем, что по газоходам котла движутся уходящие газы печей, а испарительные трубные поверхности, выполненные из змеевиковых пакетов, размещаются в газоходах на пути газов. Пароводяная смесь циркулирует внутри труб. Котлы имеют башенную и П-образную (рис. 13.4) компоновку. Для установки за технологическими агрегатами котлы выбирают в зависимости от объёма уходящих газов, подлежащих утилизации (КУ-50, КУ-60, КУ-80, КУ-125, КУ-150). Цифры указывают на объем уходящих газов, тыс. м3/ч. Температура газов на входе 600-850 °С. Компоновка котлов горизонтальная (КУ-50), башенная (КУ-100Б), П-образная (остальные). Котлы однобарабанные, по ходу газов последовательно расположены одна секция испарительной поверхности, пароперегреватель, еще несколько секций испарительных поверхностей, водяной экономайзер. Все поверхности из труб Ø 32×3 мм. Применение труб малого диаметра вызвано необходимостью при конвективной теплоотдаче разместить большую поверхность нагрева в относительно небольшие габариты котла.
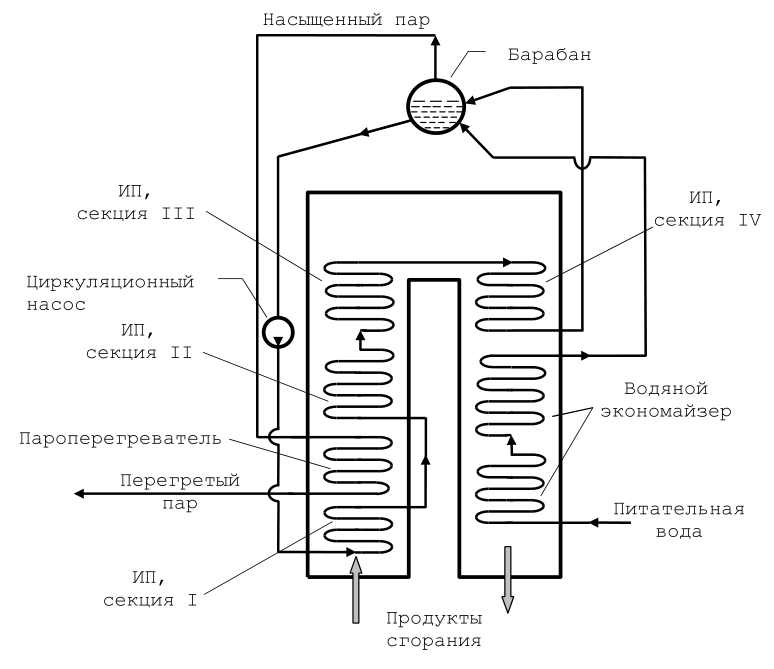
П-образной компоновки
ИП – испарительные поверхности
Циркуляция в КУ многократно принудительная, циркуляционный насос устанавливается на опускной трубе.
Тяга обеспечивается дымососом, рассчитанным на сопротивление системы «печь-котел-газоочистка». Газы охлаждаются в КУ до 200-230˚С, что достаточно для нормальной работы дымососа.
В конвективных КУ вырабатывается до 50 т пара в час (КУ-150), давление до 4,5 Мпа, температура 340-400 °С.
Пар используется для привода паровых турбин коксовых эксгаустеров (дутьевых средств, создающих разрежение), турбокомпрессоров, турбовоздуходувок, турбонасосов, турбогенераторов.
Энергетический аудит и энергетический менеджмент
Общие положения
За прошедшие после первого мирового энергетического кризиса более чем двадцать лет, в различных странах были разработаны и внедрены новые методы, средства и программы воздействия на потребление энергии. Ключевая концепция этих методов и программ — это управление с точки зрения обеспечения только необходимых потребностей, а также комплексное планирование ресурсов. Основным принципом этой концепции является то, что производители энергии и ее потребители имеют общие экономические интересы в отношении внедрения экономии энергии и повышения эффективности использования энергии.
Как правило, значительная экономия может быть достигнута без всяких затрат или при очень низком уровне затрат. В этом случае самое главное — информация.
Экономия другого рода может быть достигнута только путем инвестирования, и такие инвестиции выгодны. Период окупаемости таких инвестиций может составлять год-два.
Интенсивный рост цен на энергоносители явился причиной большинства проблем не только в энергетике, но и во всей экономике.
Отсутствие энергоресурсов в Украине явилось одной из важнейших причин того , что большая часть предприятий сократила производство своей продукции либо попросту простаивает из-за недостатка энергоресурсов. В то же время удельное потребление энергии на единицу произведенной продукции в Украине — одно из наивысших в Европе. На многих предприятиях только около 50% общей потребляемой энергии идет на производственные нужды. Все остальное попросту теряется.
Естественно, начать улучшать эффективность производства разумно там, где можно получить наиболее заметное улучшение при минимальных затратах. Прежде чем приступать к действиям по увеличению энергетической эффективности предприятий, необходимо провести энергетический аудит предприятия. Аудит — это обследование. Такую работу обычно целесообразно поручить независимым специалистам — энергетическим аудиторам, которые должны работать в тесном контакте с энергетическими и технологическими службами предприятия.
Процесс проведения энергетического аудита включает в себя следующие этапы:
- первоначальный обзор предприятия;
- создание карты потребления энергии на предприятии;
- сравнение потребления энергии как в целом по предприятию, так и по отдельным технологическим процессам и агрегатам, с данными из литературы, данными о подобных технологических процессах на других предприятиях;
- составление списка выявленных возможностей для экономии энергии на данном предприятии, ранжирование мероприятий по эффективности с учетом затрат, определение тех предложений, которые обеспечивают наибольший и быстро достижимый эффект при минимальных затратах, более детальная проработка проектов по таким предложениям.
Для наших предприятий прежде всего такими предложениями могут стать мероприятия, направленные на устранение всякого рода утечек и прямых потерь путем ремонта и
простейшей реконструкции.
Проведение на предприятии энергетического аудита — необходимая основа для внедрения системы энергетического менеджмента.
Энергетический менеджмент — это система управления, основанная на проведении набора типовых измерений и проверок, обеспечивающая такую работу предприятия, при которой потребляется только совершенно необходимое для производства количество энергии. Энергетический менеджмент — это инструмент управления предприятием, который обеспечивает постоянное знание распределения и уровня потребления энергоресурсов на предприятии, оптимального использования энергоресурсов как для производства, так и для потребностей отопления и иных непроизводственных нужд.
Занимаются энергетическим менеджментом сотрудники предприятия, ответственные за использование энергоресурсов.
Энергетический аудит, проведенный профессиональными энергетическими аудиторами, а затем энергетический менеджмент, которым занимаются специалисты самого предприятия — это мероприятия, с которых следует начинать повышать эффективность украинских предприятий. Применение такого подхода уменьшит импорт дорогостоящих энергоносителей и в долгосрочном плане уменьшит зависимость страны от стран — производителей энергоносителей.
Существует мнение, что основным рычагом проведения политики энергосбережения должен быть инспекторский контроль, нормирование, проверка соблюдения норм и наказание за неэффективное использование энергоресурсов. Мировая практика показала, что только таким методом нельзя решить проблему. Только с помощью длительной разъяснительной работы, обучения людей, применения экономических методов влияния на процессы потребления энергии можно решить эту проблему. В конце концов каждый и на каждом уровне должен понять — экономишь энергию — экономишь деньги.
Методика проведения энергетического аудита
Методика проведения энергетического аудита может быть условно разбита на 4 этапа.
Этап 1
После установления контакта с руководством предприятия необходимо выяснить мнение работников предприятия об энергосбережении и их подходы в этой области, выяснить, что было предпринято предприятием в отношении энергосбережения и имеются ли планы на будущее. Целесообразно, чтобы на этом этапе энергетический аудитор проинформировал руководство предприятия об основных направлениях энергетического аудита и ожидаемых результатах.
Затем собираются данные по энергопотреблению за прошедшие периоды времени (с использованием разработанных стандартных опросных листов). В ходе сбора данных накапливается информация по основным производствам и установкам. Очень важно, чтобы эти данные были объективно верны, не “лакированы”, для этого руководство предприятия и его работники должны проникнуться мыслью о том, что их сотрудничество с аудитором имеет важную для предприятия цель — улучшение положения предприятия на рынке продукции, его более стабильное положение.
Этап 2
Общее энергопотребление различных энергоносителей, которое, как правило, известно из финансовой отчетности, разбивается по отдельным зданиям, группам технологических процессов, отдельным основным процессам и установкам. Эта работа является созданием карты потребления энергии. Карту обычно создают, проводя дополнительные измерения в узловых точках предприятия с помощью переносных или стационарных счетчиков. Некоторые данные основываются не на измерениях, а на расчетах.
В процессе ознакомления с предприятием, анализа данных на этапе 1 и в процессе составления карты потребления энергии собирается информация об энергопотреблении по отдельным технологическим процессам и установкам. На основе этого постепенно выявляются возможности экономии энергии. Для определения теоретических возможностей экономии энергии полезно произвести сравнение ключевых данных (например, расход энергии на 1 тонну продукции) с данными, известными из специальной литературы, информацией по аналогичным производствам.
Опытный аудитор может быстро определить множество типичных мест возможной экономии энергии (разогретые поверхности, утечки энергоносителей, плохая изоляция, непрерывно работающие двигатели, высокая температура отходящих газов и т.д.).
Все выявленные возможности экономии энергии должны быть внесены в перечень мест возможной экономии с указанием приоритетности (в зависимости от потенциала экономии в случае внедрения каждой из возможностей). Если на отдельном процессе или установке расходуется большое количество энергии и имеются реальные возможности экономии, то такая экономия должна иметь высокий приоритет в сравнении с экономией в системе, где расход энергии невелик.
Этап 3
Возможности экономии энергии из перечня “возможной экономии”, имеющие высокий приоритет (большой потенциал) оцениваются более детально с технической и экономической точки зрения. В ходе выполнения этой оценки могут потребоваться дополнительные измерения, консультации со специалистами для составления программы экономии энергии. В этой программе отдельным возможностям экономии энергии должны быть даны четкие приоритеты.
В конце этого этапа руководству предприятия представляется отчет по энергетическому аудиту. Предварительно крайне важно провести обсуждение этого отчета с соответствующими сотрудниками предприятия и, в случае, если какой либо из пунктов отчета вызывает критику персонала, этот пункт необходимо дополнительно проанализировать. Важно также выполнить эту работу в сжатые сроки — это повышает шансы принятия руководством предприятия положительного решения.
Этап 4
Этот этап включает в себя планирование и внедрение принятой программы экономии энергии. Энергетический аудитор может не принимать участия в этой работе, поскольку, зачастую, является независимым экспертом. Однако целесообразно привлечь его как автора программы к сотрудничеству на условиях выполнения функций контроля и консультирования в процессе внедрения программы.
Еще один вид деятельности аудитора может заключаться в совершенствовании системы энергетического менеджмента на предприятии. На основе карты распределения и расходования энергии можно оснастить счетчиками основные производства и установки и разработать схему анализа данных.
Энергетический аудитор должен быть специалистом широкого профиля с хорошей теоретической подготовкой и практическим опытом в области энергосбережения на промышленных предприятиях. При необходимости он должен выполнять функции руководителя проекта, привлекая к работе необходимых специалистов.
Методическое обеспечение энергетической экспертизы предприятий и организаций включает следующие документы:
- Характеристика энерго- и ресурсопотребления предприятия.
- Перечень наиболее характерных энергосберегающих мероприятий.
- Перечень вопросов по энергосбережению предприятий.
- Паспорт технологии.
Отчет по энергетическому аудиту, выполняемый после проведения всей работы, имеет такую структуру:
- титульный лист;
- содержание;
- аннотация;
- введение;
- описание предприятия;
- схемы потребления энергии;
- обзор возможностей экономии энергии;
- обзор возможных программ по энергосбережению;
- обзор вопросов, касающихся внедрения системы энергетического менеджмента на данном предприятии;
- приложение.