Примерно 25 % губчатого железа, производимого в мире, получают на установках прямого восстановления, работающих по способу ХиЛ.
В связи с относительно высоким удельным расходом энергии (17—19 ГДж/т) периодически действующие установки с ретортами начиная с 1980 г. стали заменять непрерывно действующими установками с шахтными печами, работающими по способу ХиЛ-III . При этом были сохранены проверенные принципы и компоненты процесса ХиЛ-I, например, способ получения газа-восстановителя, обогащение его водородом, а также ведение процесса восстановления в условиях повышенного давления и высокой температуры.
В настоящее время в Мексике по способу ХиЛ-III работают три установки с шахтными печами общей мощностью 3 млн т/год.
При способе ХиЛ-III в шахтной печи можно перерабатывать в качестве железосодержащего материала окатыши разного сорта и смеси окатышей с кусковой рудой.
Типичные пределы по химическому составу железорудных материалов, используемых на заводах в процессе HYL (ХиЛ), следующие:
Feобщ | 65 — 69 % |
Пустая порода | 1,4 — 7 % |
P | 0,01 — 0,1 % |
S | 0,001 — 0,05 % |
SiO2+Al2O3 | 1,1 — 4,0 % |
CaO + MgO | 0,1 — 3,0 % |
Na2O + K2O | 0,05 — 0,2 % |
CaO/SiO2 | 0,02 — 0,5 % |
Химический состав наиболее часто используемых железных руд и окатышей приведен в таблице ниже.
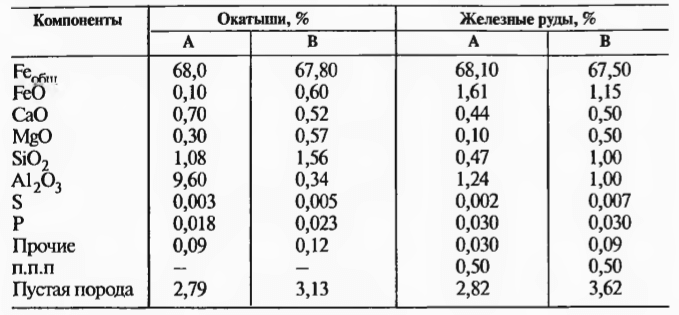
Особенность шахтной печи заключается в том, что давление газа на входе может достигать 5,5 · 105 Па (рис. 4.26). Поэтому требуется система шлюзов, через которые материалы подаются в загрузочный бункер, где давление равно давлению в печи. Материалы из загрузочного бункера с помощью четырех вертикальных труб распределяются по непрерывно опускающейся поверхности засыпи. Нагретый до 930 °С газ-восстановитель вдувается в зону восстановления через кольцевой огнеупорный канал. Восстановление осуществляется в противотоке. На выходе из печи колошниковый газ имеет температуру 400—450 °С.
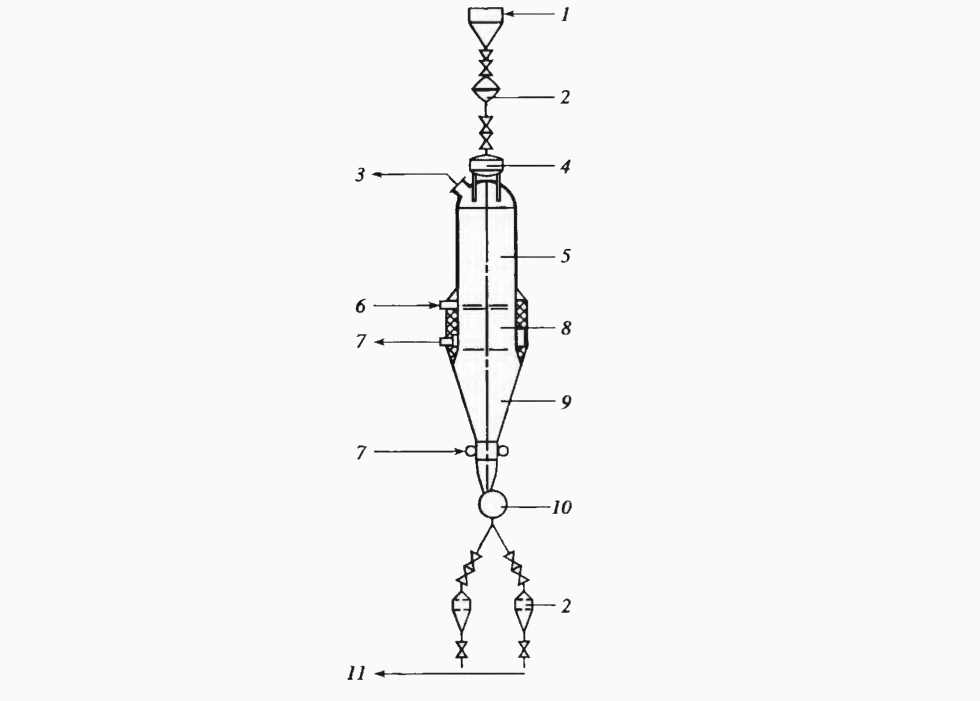
Высокая температура и высокое давление в зоне восстановления, а также высокое содержание водорода в газе-восстановителе обеспечивают достижение рекордных показателей удельной производительности по губчатому железу — почти 3,5 т/(ч·м2) по поперечному сечению шахты.
Из зоны восстановления губчатое железо вначале попадает в так называемую зону равного давления, которая не только разделяет зоны восстановления и охлаждения, но и способствует равномерному сходу твердых материалов в зоне восстановления. В нижней конической части шахтной печи губчатое железо охлаждается в противотоке вдуваемым снизу охлаждающим газом. Губчатое железо, имеющее температуру около 50 °С, непрерывно выгружается через шлюз с ячейковым питателем и подается в один из двух выпускных патрубков. Здесь имеется та же система шлюзов, что и на участке загрузки.
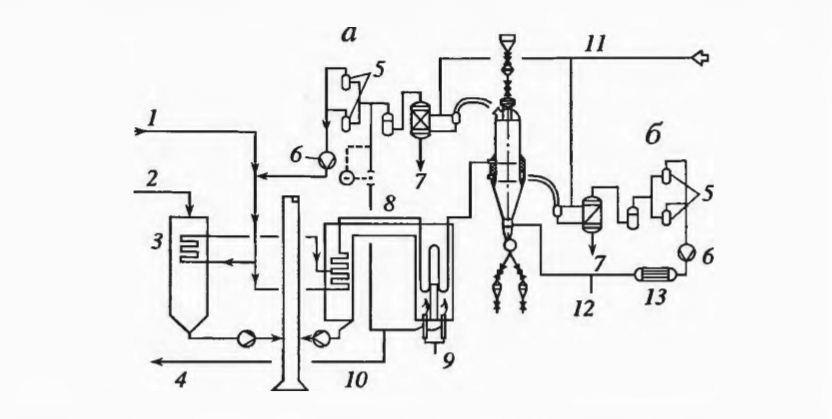
Схема процесса показана на рис. 4.27. Очистка выходящего из печи колошникового газа от пыли осуществляется в охладителе с брызгалами и промывочном охладителе. Вода, являющаяся продуктом реакции, удаляется, и затем газ охлаждается до температуры около 40 °С. Примерно две трети очищенного колошникового газа подается с помощью компрессора в систему рециркуляции, а одна треть в качестве остаточного газа должна быть выведена из цикла циркуляции газа-восстановителя для того, чтобы обеспечить удаление образующегося при восстановлении углекислого газа и азота, вносимого со свежим газом из реформера. Поскольку с остаточным газом удаляются не только СO2 и СО, но также водород, в контур циркуляции необходимо добавлять требуемое для восстановления количество свежего газа. Остаточный газ используется для обогрева газонагревателя и реформера. Смесь свежего газа из реформера и газа из системы рециркуляции и представляет собой газ-восстановитель, степень окисления которого η составляет 13—17%:
Газ-восстановитель проходит через установки предварительного подогрева и нагрева и достигает температуры 930 °С.
В конической части шахтной печи губчатое железо охлаждается и науглероживается движущимся в противотоке охлаждающим газом.
Охлаждающий газ, имеющий на выходе из зоны охлаждения температуру 500—550 °С, охлаждается, как и газ-восстановитель, путем непосредственного впрыскивания воды до 40 °С и очищается от пыли. После повторного сжатия с помощью компрессора для охлаждающего газа дополнительного охлаждения до 40 °С охлаждающий газ обогащается природным газом и вновь подается в зону охлаждения. Обогащение природным газом улучшает эффект охлаждения обеспечивает возможность регулирования содержания углерода в губчатом железе. Наряду с науглероживанием, добавки природного газа способствуют дополнительному получению водорода и окиси углерода, благодаря чему можно уменьшить добавку необходимого для восстановления свежего газа из реформера.
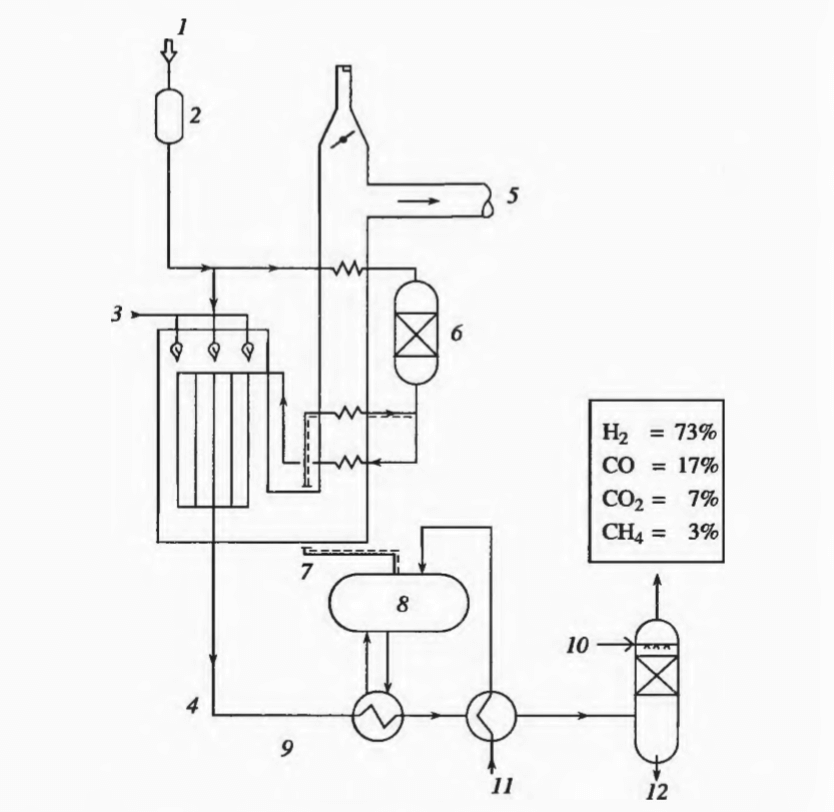
Для получения газа-восстановителя на установках ХиЛ-III также используется уже неоднократно проверенный на установках ХиЛ-I и химических установках обычный способ реформирования газа и пара (рис. 4.28). Очищенный и пропущенный через слой ZnO для удаления серы природный газ подается вместе с водяным паром при отношении пар/углерод около 2,4 в заполненную никелевым катализатором трубу. Здесь при температуре 800 °С и давлении 8 бар происходит реакция расщепления
СnН(2n+2) + nН2O → nСО + (2n + 1)Н2. (4.15)
Отношение водяной пар/углерод намного превышает стехиометрическое, в результате чего надежно подавляется образование вредных отложений углерода на катализаторе, особенно при повышенной концентрации углеводородов в природном газе.
Выходящий из труб реформера неочищенный газ подвергают, с использованием физического тепла (в теплообменниках получают насыщенный пар и подогревают питательную воду котлов), охлаждению в промывочных охладителях до температуры 40 °С, при этом вследствие конденсации удаляется содержащийся в нем водяной пар. Этот охлажденный газ подают в качестве свежего газа в контур циркуляции газа-восстановителя.
Тепло, необходимое для протекания эндотермической реакции расщепления, получают в результате сжигания природного газа в смеси с остаточным газом процесса восстановления. Тепло дымовых газов достаточно полно используется в теплообменниках (передача тепла конвекцией) и на установках для предварительного нагрева газа-восстановителя (см. рис. 4.27).
В процессе вносится следующее количество энергии, ГДж/т губчатого железа: 7,183 с природным газом для реакции расщепления, 1,231 с природным газом в контур циркуляции охлаждающего газа и 2,474 с горючим газом в реформер (рис. 4.29).
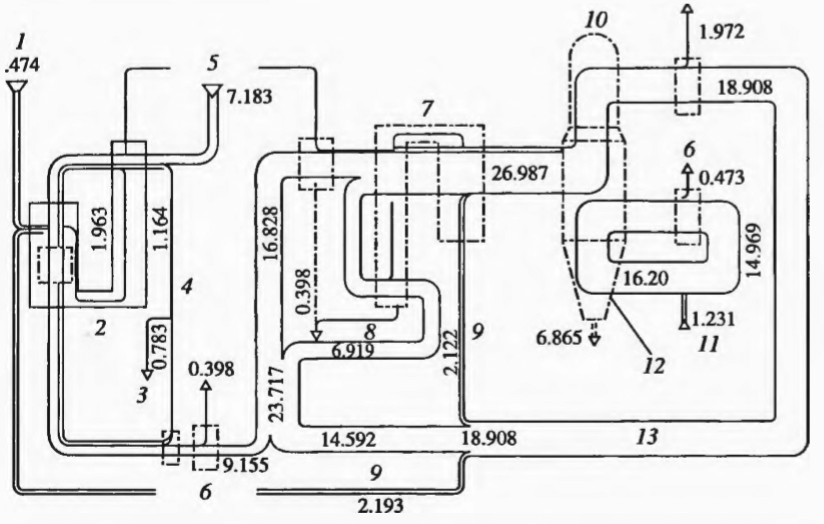
На основе описанных технических параметров процесса ХиЛ-III была сооружена установка прямого восстановления фирмы «Сикартса» в Лазаро Карденас, (Мексика). Установка рассчитана на производство губчатого железа в количестве 2 млн т/год. Она состоит из двух модулей с двумя шахтными печами, двумя установками для нагрева газа, одним газовым реформером и общими вспомогательными установками (данные для каждого модуля).
С целью дальнейшего повышения степени металлизации и удельной производительности в 1986 году две установки ХиЛ-III в Монтеррее были оборудованы системой отмывки от СO2. Система встроена в контур циркуляции газа-восстановителя между компрессором и участком подмешивания к газу-восстановителю свежего газа. Содержание CO2 в подаваемом на рециркуляцию колошниковом газе снижается с 10,5 до 1,5%.
Оборудование действующих установок в Монтеррее системой отмывки от СО2 обеспечило следующие преимущества: избирательное удаление CO2 из колошникового газа привело к сокращению до минимума количества остаточного газа, содержащего окись углерода и водород. Вследствие этого количество реформированного свежего газа, добавляемого к газу-восстановителю, увеличилось на 30%; соответственно возросла и производительность реформера; в результате более низкой степени окисления газа-восстановителя количество этого газа, подаваемого в шахту печи, при той же производительности уменьшилось. Вследствие этого при полном использовании имеющихся компонентов установки (реформера, установки для нагрева газа, шахтной печи, контура циркуляции газа-восстановителя и др.) производ ительность удалось повысить почти на 30%.
В настоящее время новые установки проектируются и сооружаются только с системами отмывки от CO2, так как при сравнимой производительности уменьшаются размеры компонентов установки и несколько сокращается потребление энергии и воды. Сравнение показателей работы установок ХиЛ-III, не оборудованных (А) и оборудованных (Б) системой отмывки от CO2, приведено ниже:
При наличии установки для отмывки от CO2 дымовые газы реформера используются уже не для предварительного нагрева газа-восстановителя, а для выработки пара. В результате этого система реформера и контур циркуляции газа-восстановителя рассоединяются. Пар, неиспользуемый для преобразования природного газа, применяется в турбинах, а отработавший пар — для нагрева на установке для отмывки от CO2. Установка дополнительных горелок в конвективной части реформера гарантирует наличие пара для запуска или в аварийных ситуациях при остановке процесса реформирования.
Благодаря соответствующей конструкции реформера и оснащению установки ХиЛ-III паровыми турбинами и турбогенераторами установка может работать в автономном режиме от источника электроэнергии.
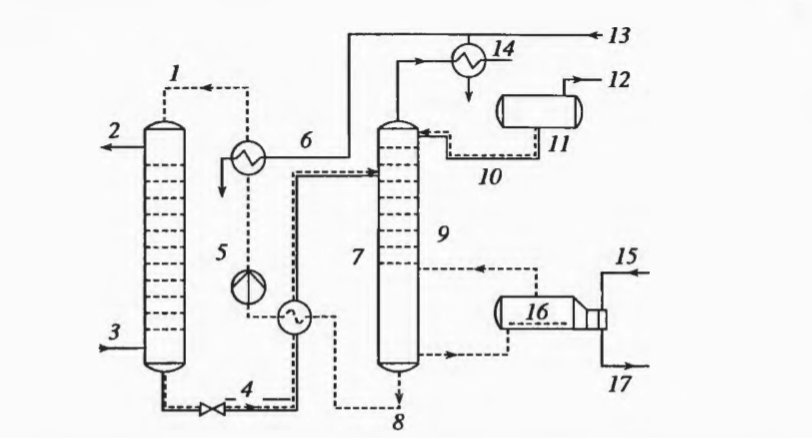
Что касается конструкции установки для отмывки от CO2, то принципиальная схема ее приведена на рис. 4.30. В абсорбере, представляющем собой тарельчатую ректификационную колонну, газ, содержащий CO2, движется навстречу промывочной жидкости, которая абсорбирует CO2. При этом CO2 реагирует с промывочным раствором согласно одному из приведенных выражений:
К2CO3 + Н2O + CO2 = 2КНCO3; (4.16)
H2O + CO2 + R2NCH3 = R2NHSH+4 + НСО—3. (4.17)
В уравнении (4.16) речь идет о растворе поташа (примерно 20—30%-ном), применяемом, например, при процессе Бенфилда, а в уравнении (4.17) — о метидциэтаноламиновом растворе — третичном амине (R2 — радикал). В принципе абсорбция CO2 при обоих способах ускоряется в условиях повышенного парциального давления и низкой температуры, а десорбция — в условиях низкого давления и высокой температуры. При подводе тепла в десорбер приведенные выше реакции протекают в обратном направлении.
Очищенный газ выходит через верхнюю часть абсорбера. Загрязненный промывочный раствор (обогащенный) выпускается через нижнюю часть абсорбера. Этот раствор используется для предварительного нагрева поступающего из десорбера «бедного» раствора в теплообменнике, затем нагретый раствор подается в верхнюю часть десорбера. Для нагрева бойлера десорбера используется отработавший пар паровых турбин, которыми оборудована установка прямого восстановления. Вьщеляющийся кислый газ, состоящий из CO2 и следов также абсорбированного Н2S, отсасывается из верхней части десорбера, охлаждается в конденсаторе и выпускается в атмосферу либо подается потребителям.
Потребление энергии на установке для отмывки от CO2 по способу Бенфилда составляет при начальном содержании CO2 в газе 10,5% и конечном его содержании 1,5% примерно 0,856 ГДж/т губчатого железа.
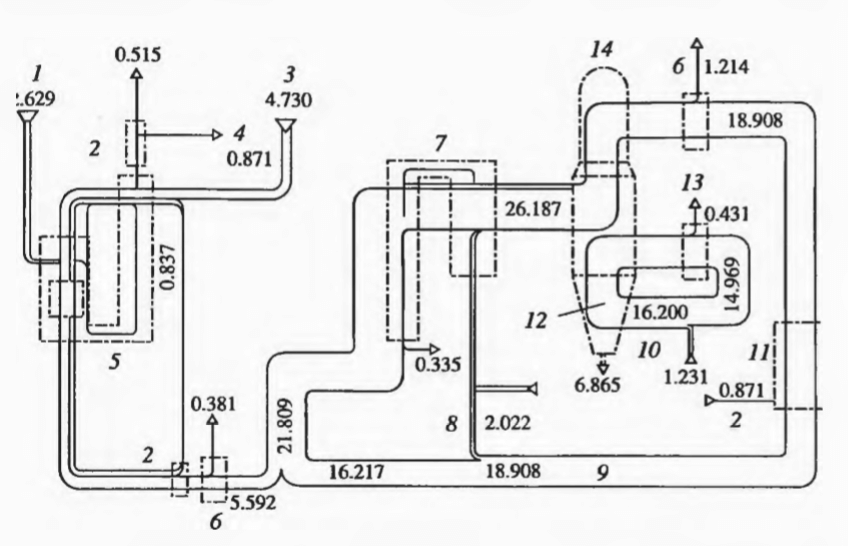
1 — горючий газ; 2 — выработка пара; 3 — технологический газ; 4 — пар ; 5 — реформер ; 6 — промывочный охладитель; 7 — нагрев газа-восстановителя ; 8 — остаточный газ; 9 — контур циркуляции газа-восстановителя ; 10 — природный газ; 11 — установка для отмывки от СO2; 12 — контур циркуляции охлаждающего газа; 13 — промывочный охладитель; 14 — реактор
При определении энергетического баланса (рис. 4.31) исходили из следующих теоретических расходных показателей, ГДж/т губчатого железа:
- Технологический газ (реформер): 4,730
- Горючий газ (реформер): 2,629
- Горючий газ (установка для нагрева газа-восстановителя): 2,022
- Природный газ, добавляемый в контур циркуляции охлаждающего газа: 1,231
- Общий расход: 10,612
Благодаря использованию тепла колошникового или охлаждающего газа для выработки пара для установки отмывки от CO2 можно достичь дополнительного снижения общего расхода энергии до 9,74 ГДж/т губчатого железа.
Возможности дальнейшего развития
Дальнейшими направлениями развития, которые могли бы способствовать улучшению гибкости и повышению экономичности процесса ХиЛ-III , являются горячее брикетирование, замена природного газа, самореформинг природного газа.
Что касается горячего брикетирования, то прессы для гсрячего брикетирования могут быть расположены у выпускных патрубков, через которые горячее губчатое железо выгружается из нижней части реактора (рис. 4.32). При применении горячего брикетирования контур циркуляции охлаждающего газа может оказаться вообще ненужным, кроме того, брикеты нечувствительны к вторичному окислению. Брикеты лучше поддаются хранению и транспортировке, чем небрикети- рованное губчатое железо. В связи с этим отпадают и проблемы с мелочью, образующейся при производстве и перегрузках губчатого железа.
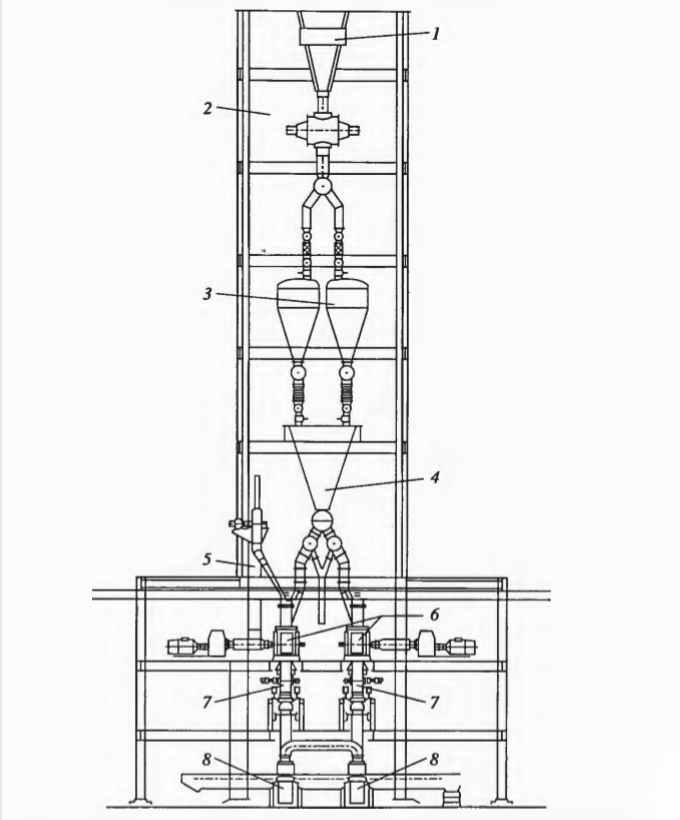
Благодаря высокой температуре восстановления облегчается поддержание температуры губчатого железа на уровне 700 °С, что необходимо для успешного протекания процесса брикетирования. Следующим вопросом является вопрос замены природного газа. Природный газ, используемый для получения газа-восстановителя в реформере, можно заменить синтез-газом, образующимся при других способах производства газа (рис. 4.33). Для обогрева реформера и установки для нагрева газа-восстановителя можно применять другие энергоносители (например, бедный газ). Это расширяет энергетическую базу процесса ХиЛ-III , а также служит стимулом для рассмотрения возможности применения этого процесса в «неклассических» областях восстановления газом.
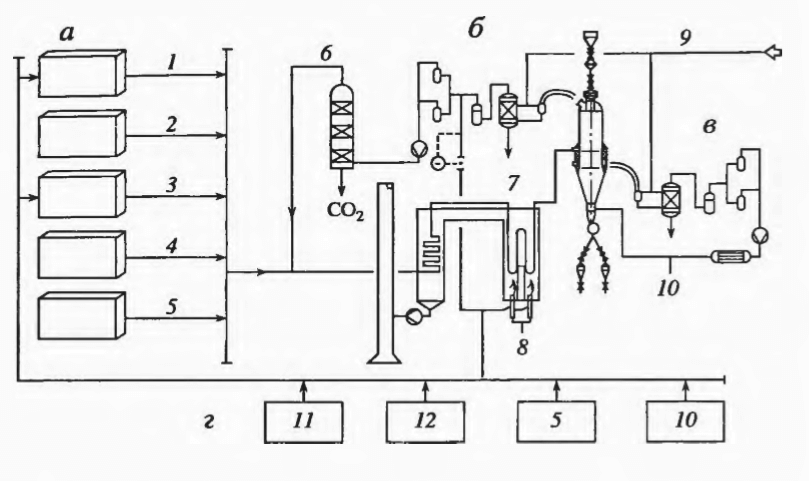
Значительное повышение экономической эффективности производства губчатого железа (ГЖ) в шахтных реакторах HYL достигается за счет новой технологии получения восстановительного газа, а именно — процесса самореформинга природного газа, разработанного фирмой «Нуl» при участии фирмы «Sidor/Danieli» (прежний процесс Агех). Первый промышленный агрегат HYL без реформера был пущен в апреле 1998 года в Монтеррее (Мексика) на заводе Hylsa 4М. Первоначальная годовая мощность реактора 675 000 т ГЖ в год может быть увеличена до 1,5 млн т/год. Кроме процесса самореформинга, на этом заводе реализована высокотемпературная пневматическая транспортная система (Hytemp Pneumatic Transport System) для подачи горячего науглероженного ГЖ непосредственно из реактора HYL в расположенную рядом электросталеплавильную печь.
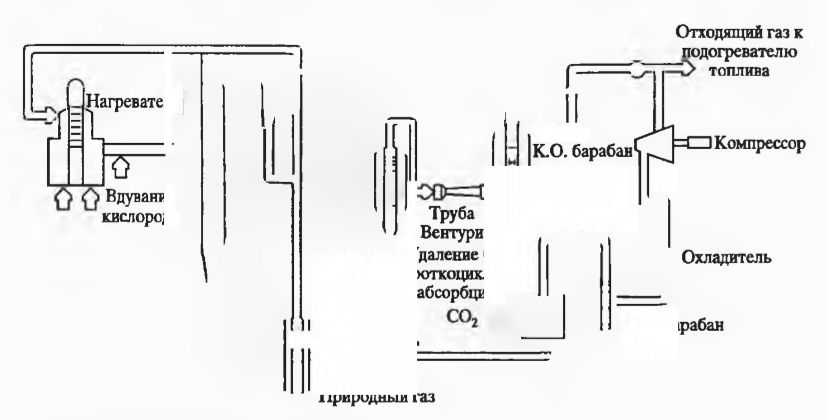
Модуль HYL на заводе Hylsa 4М включает восстановительный реактор и контур восстановления (рис. 4.34). Восстановительный реактор является типовым реактором HYL с разгрузкой горячего ГЖ и включает две зоны. Верхняя восстановительная зона имеет форму цилиндра. Здесь осуществляется процесс восстановления оксидов железа и идут реакции реформинга природного газа. Нижняя коническая зона снабжена роторным разгрузочным клапаном, регулирующим скорость потока твердых материалов внутри реактора. Контур восстановления включает все необходимое оборудование для обработки и кондиционирования технологического газа. Стартовой позицией в контуре восстановления является подача подпитывающего потока природного газа в поток рециркулирующего газа. Смесь этих газов увлажняется паром до необходимого уровня, который регулирует содержание углерода в ГЖ. Затем увлажненная смесь газов нагревается в рекуператоре, а в газонагревателе — до температуры более 900 °С. В газопровод, подающий нагретый газ в реактор, вдувается кислород для частичного окисления природного газа и нагрева газовой смеси до температуры 1020 °С, с которой он поступает в нижнюю часть восстановительного реактора. Газовая смесь, поступающая сюда, содержит около 30% СН4 и контролируемое содержание CO2 и Н2O. В этой части реактора идут процессы самореформинга природного газа, окончательного восстановления железорудных материалов до ГЖ и науглероживания ГЖ. Свежевосстановленное ГЖ в этой зоне играет роль катализатора для реакций реформирования природного газа. Образующиеся в процессе восстановления FeO до Fe окислители (CO2 и Н2O) используются в процессе реформинга природного газа, генерируя СО и Н2, которые снова используются в реакциях восстановления. Процесс науглероживания ГЖ не снижает его каталитических свойств. Регулируя содержание окислителей (CO2 и Н2O) в газах на входе в реактор, можно легко контролировать содержание углерода в ГЖ. Колошниковый газ из реактора охлаждается в рекуператоре, а затем очищается в скруббере, где одновременно из газа удаляется часть водяных паров. Часть газа после очистки удаляется из контура восстановления для контроля давления в реакторе. Оставшийся газ очищается от CO2 процессом короткоцикловой адсорбции и подается на смешивание с природным газом.
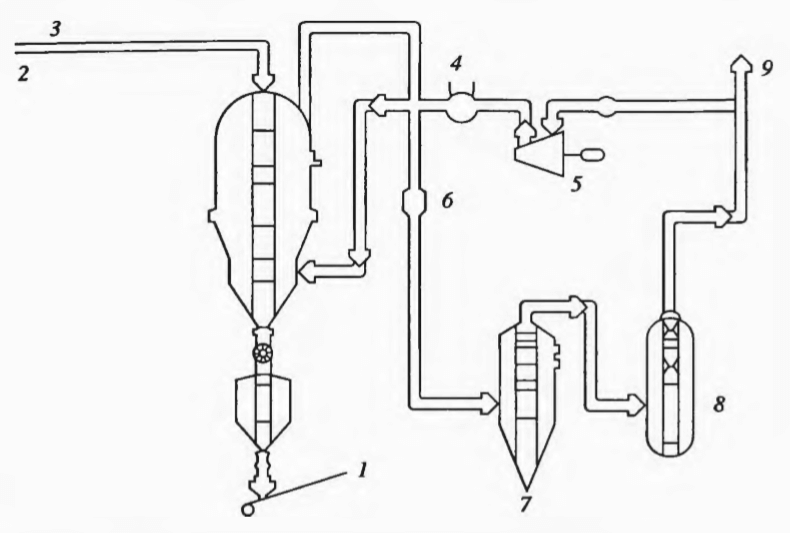
На выходе из восстановительного реактора через роторный разгрузочный клапан металлизованные окатыши самотеком за счет силы тяжести могут направляться по трем направлениям: в накопительный пробоотборный бункер, к устройству пневмотранспорта ГЖ до внешней системы охлаждения и к устройству пневмотранспорта ГЖ в электросталеплавильную печь. В шахтный охладительный агрегат системы охлаждения металлизованные окатыши подаются по трубопроводу (пневмотранспортом). Охлаждение окатышей производится газом в противотоке (рис. 4.35).
Для электросталеплавильной печи горячие металлизованные окатыши по трубопроводу транспортирующим газом подаются в загрузочный бункер, расположенный над электропечью. Транспортирующий газ очищается в скруббере и направляется в газонагреватель для нагрева до температуры 600 °С, после чего он снова используется для транспортировки горячих металлизованных окатышей к дуговой сталеплавильной печи (ДСП).
В течение первого года работы производительность завода Hylsa 4М составила более 400000 т. В 1999 году производительность составила 702600 т/год при средней степени металлизации ГЖ 94 % и среднем содержании углерода в нем 4,03 %. Процесс самореформинга позволяет легко контролировать содержание углерода в ГЖ в пределах от 2,2 до 5,5 %. По опыту работы заводов фирмы «Hylsa» 1 кг углерода в ГЖ экономит 2,5 кВт-ч электроэнергии в электроплавке. Это означает, что увеличение содержания углерода в ГЖ на 2% (абс.) приводит к экономии 50 кВт-ч электроэнергии. Величина экономии зависит от того, в каком виде присутствует углерод в ГЖ. Максимальная экономия достигается в случае, когда углерод находится в ГЖ в виде карбида (Fe3С), так как часть сажистого углерода в ГЖ в процессе плавления может окисляться. С ростом содержания углерода в ГЖ с 2 до 6,0 % доля углерода в виде карбида в ГЖ уменьшается с 96—98 % до 78—85 %. Повышение содержания углерода в ГЖ увеличивает его стоимость еще и в связи с тем, что углерод ГЖ является абсолютно чистым и не содержит ни летучих веществ, ни золы, содержание которых снижает цену углеродсодержащих материалов, используемых в электроплавке.
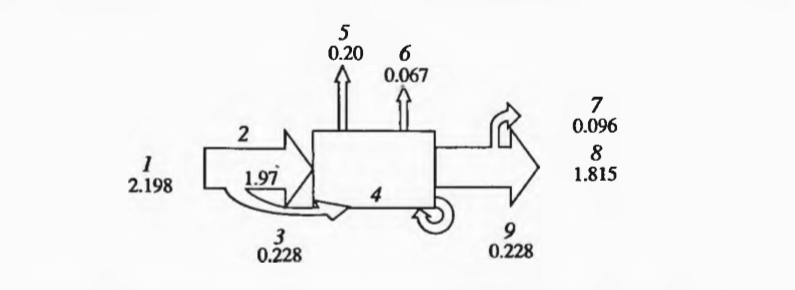
1 — общий расход природного газа; 2 — расход природного газа на процессы ; 3 — расход природного газа как топлива в газонагревателе; 4 — процесс получения ГЖ в реакторе; 5 — испарение; 6 — дымовые газы; 7 — теплосодержание ГЖ ; 8 — энергия, затраченная на получение ГЖ ; 9 — отходящие газы, используемые в качестве топлива в газонагревателе
Эффективность использования энергии на заводе Hylsa 4М иллюстрируется диаграммой на рис. 4.36. При общем расходе энергии 2,2 Гкал/т ГЖ полезно расходуется 1,91 Гкал/т, т. е. эффективность использования энергии в процессе составляет 87 %, что намного превышает эффективность использования энергии в большинстве процессов производства ГЖ, используемых в мире, где она составляет только около 70 %. Высокая эффективность использования энергии в процессе HYL на этом заводе достигается за счет минимизации расхода газа на сжигание (0,7 Гкал/т ГЖ при 1,2—1,5 Гкал/т в других процессах), за счет высокой химической энергии (высокое содержание углерода и высокая степень металлизации ГЖ), а также за счет высокого теплосодержания ГЖ.
Применение технологии самореформинга в процессе HYL приводит к увеличению расхода кислорода на 50 м3/т ГЖ, но сокращает расход природного газа на 5—10 %. Кроме того, капитальные затраты на строительство модуля сокращаются на 5—10 %.
Себестоимость получаемого ГЖ зависит, в основном, от стоимости приобретаемых окатышей или кусковой железной руды, что видно из данных таблицы, в которой приведены результаты расчета себестоимости ГЖ при различных вариантах используемой железорудной шихты.
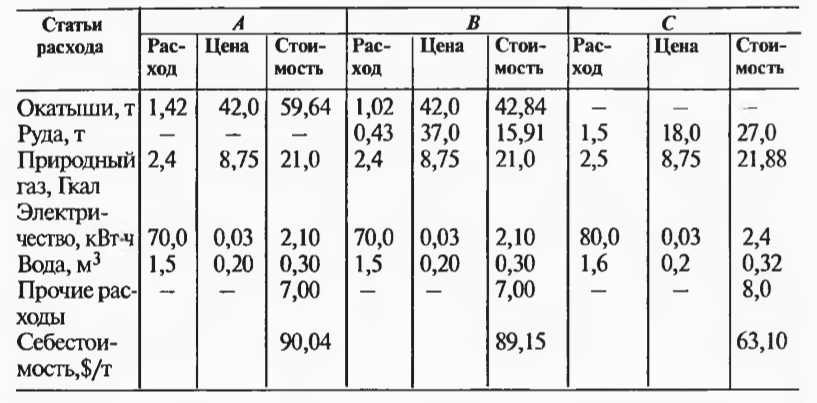
В варианте С используется дешевая железная руда, при восстановлении которой образуется много мелочи, что требует обязательного брикетирования получаемого продукта, следовательно, увеличивает эксплуатационные затраты. При производстве окатышей и ГЖ из них на одном и том же предприятии себестоимость ГЖ снижается до 71,58 дол. США/т.
Качественные характеристики ГЖ, %, процесса HYL варьируют в следующих пределах:
- Степень металлизации: 92,0—95,0
- Содержание углерода: 1,1—5,0
- Содержание Feобщ : 84,0—95,0
- Содержание Feмет: 80,0—90,0
- Пустая порода: 1,90—9,0
- P : 0,013-0,14
- S : 0,001-0,07
Процесс позволяет получать при необходимости содержание углерода в ГЖ до 5 %. В этом случае до 90 % его находится в продукте в виде карбида.
Для предотвращения спекания кусков руды в процессе их металлизации используют опрыскивание загружаемой руды цементно-водяной суспензией с расходом цемента (или альтернативного материала) 4—6 кг/т руды.
Один из самых мощных заводов HYL—IMEXSA HYL имеет 4 шахтных реактора и два реформера. При номинальной мощности 2 млн. т ГЖ в год завод производит 2,2—2,3 млн т/год.